《航空制造工程手册:特种加工》
作者 | 《航空制造工程手册》总编委会主编 编者 |
---|---|
出版 | 北京:航空工业出版社 |
参考页数 | 733 |
出版时间 | 1993(求助前请核对) 目录预览 |
ISBN号 | 7800466809 — 求助条款 |
PDF编号 | 83985468(仅供预览,未存储实际文件) |
求助格式 | 扫描PDF(若分多册发行,每次仅能受理1册) |
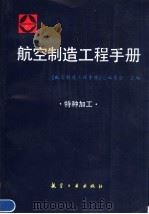
1.1 特种加工技术的发展1
1.2 特种加工技术的特点1
第1章 概述1
1.3 特种加工技术的分类2
1.4 特种加工技术应用范围3
1.5 特种加工技术在航空工业中的应用及其发展趋势7
1.6 本分册的内容12
2.1.1 分类及特征13
2.1 概论13
第2章 电解加工13
2.1.2 应用范围20
2.1.3 国内外应用现状及发展动态21
2.2.1 电解加工的电极反应24
2.2 电解加工基本原理24
2.2.2 电解加工与法拉第定律25
2.2.3.1 术语及常用电极的标准电极电位26
2.2.3 电解加工的极化效应26
2.2.3.4 极化与电流效率29
2.2.3.3 极化与分解电压29
2.2.3.2 极化的形成及影响因素29
2.2.4 阳极的活化、钝化和超钝化31
2.2.3.5 分解电压与电流效率的测定方法31
2.3.1.1 组成、分类和选型34
2.3.1 总体论述34
2.2.5 极化对电解加工的影响34
2.3 电解加工设备34
2.3.1.2 设备主要规格的选取36
2.3.1.3 电解加工设备的总体要求38
2.3.2.1 电解加工机床的组成、技术要求及主要部件结构的选取39
2.3.2 机床39
2.3.2.2 叶片电解加工机床44
2.3.2.4 立式单头电解加工机床50
2.3.2.3 大型卧式单头电解加工机床50
2.3.2.5 电解磨削机床51
2.3.3.1 基本要求54
2.3.3 电解加工电源及短路保护系统54
2.3.3.2 分类、特征及应用范围55
2.3.3.3 可控硅整流电源及斩波器56
2.3.3.4 快速短路保护系统58
2.3.4.1 组成59
2.3.4 电解液系统59
2.3.4.2 功能及基本要求60
2.3.4.3 电解液主泵61
2.3.4.5 恒温系统63
2.3.4.4 电解液槽63
2.3.4.6 电解液净化装置64
2.3.5.1 组成及功能65
2.3.5 自动控制系统65
2.3.5.2 加工间隙参数的采样和控制66
2.3.5.3 加工循环的自动控制67
2.3.5.4 电解加工控制系统类型69
2.4.1.2 电解液的分类70
2.4.1.1 电解液的作用及对电解液的基本要求70
2.4 电解加工工艺70
2.4.1 电解液70
2.4.1.4 常用电解加工材料的电解液配方72
2.4.1.3 几种常用的电解液72
2.4.2.2 间隙公式73
2.4.2.1 间隙的作用及其影响因素73
2.4.2 加工间隙73
2.4.2.3 间隙与电场、流场74
2.4.2.5 间隙的几何形状及概算78
2.4.2.4 间隙的分布与大小的选择78
2.4.3.1 概述81
2.4.3 流场81
2.4.3.2 三种基础流场的分析83
2.4.3.3 平面与孔加工流场84
2.4.3.4 叶片电解加工流场85
2.4.4.1 工具阴极的分类86
2.4.4.工具阴极及夹具86
2.4.4.2 工具阴极的设计88
2.4.4.3 工具阴极的制造104
2.4.4.4 电解加工夹具105
2.5.1.1 混气电解加工的特点107
2.5.1 混气电解加工107
2.5 提高电解加工精度的措施107
2.5.1.2 混气腔的设计109
2.5.2.2 脉冲电流加工的分类111
2.5.2.1 原理、特点、应用范围111
2.5.2 脉冲电流加工111
2.5.2.3 脉冲电流加工工艺及实例112
2.6.1.1 分类、特证、应用范围115
2.6.1 叶片加工115
2.6 电解加工在航空工业中的应用115
2.6.1.2 典型加工实例117
2.6.1.3 叶片电解加工常见疵病、故障及排除119
2.6.2.1 二维不变截面整体叶轮、定子叶栅叶片型面加工120
2.6.2 整体叶轮加工120
2.6.2.2 变截面扭转整体叶轮型面加工122
2.6.2.3 疵病、故障及排除123
2.6.3.1 分类、特证及参数124
2.6.3 小孔加工124
2.6.3.2 典型加工零件125
2.6.4 机匣加工127
2.6.3.3 加工故障及排除127
2.6.4.1 加工方法概述128
2.6.4.2 电解液及工艺参数选用129
2.6.5.1 电解加工表面质量的特点130
2.6.5 电解加工的表面质量与疲劳强度130
2.6.4.3 加工尺寸范围及加工精度130
2.6.5.2 影响表面质量的因素及改善表面质量的措施131
2.6.5.3 电解加工对疲劳强度的影响及提高电解加工零件疲劳强度的方法134
2.7.1 电解去毛刺及尖边倒圆137
2.7 其他类型电解加工工艺137
2.7.1.1 原理及工艺138
2.7.1.2 应用实例139
2.7.2.2 基本工艺规律142
2.7.2.1 用途、特点142
2.7.2 电解抛光142
2.7.2.3 电抛光表面疵病、原因、质量措施144
2.7.2.4 应用举例146
2.7.3.1 概述149
2.7.3 电解磨削149
2.7.3.2 电解液151
2.7.3.3 主要工艺参数152
2.7.3.4 应用实例154
2.7.3.5 电解磨削导电磨轮158
2.8.1.1 电解液对环境的污染159
2.8.1 电解加工的环境污染及环境保护159
2.8 技术安全159
2.8.2 电解泥的提炼160
2.8.1.2 对大气的污染160
附表161
3.1.1.1 电火花成形穿孔加工167
3.1.1 分类167
第3章 电火花加工167
3.1 概述167
3.1.1.4 电火花展成加工168
3.1.1.3 电火花线电极加工168
3.1.1.2 电火花磨削加工168
3.1.3.1 电参数169
3.1.3.极间放电状态及检测169
3.1.2 机理169
3.1.3.4 极间放电状态的检测172
3.1.3.3 脉冲能量172
3.1.3.2 脉冲分类172
3.2.1 电火花成形加工机系列173
3.2 电火花成形加工设备173
3.2.2 主机结构特点、形式、性能175
3.2.2.1 主轴头176
3.2.2.2 工作台177
3.2.3.1 脉冲电源178
3.2.3 电源178
3.2.3.2 数控电源179
3.2.4.1 控制过程参数对工艺指标的影响180
3.2.4 控制系统180
3.2.4.4 控制功能182
3.2.4.3 控制方式分类182
3.2.4.2 控制系统的目标182
3.2.5.1 工作液的作用186
3.2.5 工作液及其循环过滤系统186
3.2.5.3 添加剂187
3.2.5.2 常用工作液187
3.2.5.5 工作液的过滤188
3.2.5.4 工作液循环系统188
3.2.6.2 平动头190
3.2.6.1 电极夹头190
3.2.6 辅助设备及附件190
3.2.7.1 主控制系统191
3.2.7 数控电火花成形机191
3.2.7.2 机械系统与运动控制192
3.2.7.3 电源194
3.3.1 工具电极形式196
3.3 工具电极196
3.2.7.4 辅助控制功能196
3.3.2.1 工具电极常用材料197
3.3.2 工具电极材料197
3.3.2.2 电极材料的选择199
3.3.3.1 电极损耗定义202
3.3.3 工具电极损耗202
3.3.3.2 影响电极损耗的因素204
3.3.4.1 工具电极设计206
3.3.4 工具电极设计与制造206
3.3.4.2 工具电极的制造211
3.3.5.1 工具电极的工艺基准校正214
3.3.5 工具电极的安装214
3.3.5.2 工具电极的装夹215
3.3.5.3 工具电极对工件的找正217
3.4.1.1 电火花穿孔加工220
3.4.1 电火花加工工艺类型220
3.4 电火花加工工艺220
3.4.1.2 型腔电火花加工225
3.4.1.3 电火花加工规准231
3.4.1.4 精密、细微零件电火花加工235
3.4.2.1 金属材料的热物理性能239
3.4.2 不同材料电火花加工特点239
3.4.2.2 其他材料电火花加工特点240
3.4.3.1 加工精度概念241
3.4.3 电火花加工精度241
3.4.3.2 影响电火花加工精度的因素242
3.4.4.1 电火花加工表面粗糙度244
3.4.4 电火花加工表面完整性244
3.4.4.2 电火花加工表层247
3.4.4.3 电火花加工表层的物理性能250
3.4.4.4 电火花加工表面缺陷的避免254
3.4.4.5 电火花加工表面后置处理255
3.4.5 电火花加工速度和加工稳定性256
3.4.5.1 电火花加工速度的表示方法256
3.4.5.2 影响加工速度的因素257
3.4.5.3 加工稳定性260
3.5.1 电火花表面强化原理261
3.5 电火花强化261
3.5.3.3 强化层的显微硬度262
3.5.3.2 强化层表面形貌262
3.5.2 电极材料262
3.5.3 电火花表面强化层特性262
3.5.3.1 强化层厚度262
3.5.3.6 强化层的残余应力263
3.5.3.5 强化层的耐磨性及耐蚀性263
3.5.3.4 强化层的红硬性263
3.5.4 电火花强化工艺264
3.5.5 影响电火花强化层厚度的因素265
3.6 电火花磨削269
3.7.1.1 加工方案271
3.7.1 整体叶轮叶片电火花加工271
3.7 电火花加工实例271
3.7.1.2 电极设计272
3.7.2 栅网小孔的整体电火花加工273
3.7.1.3 加工工艺273
3.7.3.1 航空发动机喷油嘴的加工274
3.7.3 小孔电火花加工在航空发动机中的应用274
3.7.3.2 航空发动机叶片等零件小孔加工275
3.7.4.1 技术要求276
3.7.4 伞齿轮精锻模电火花加工276
3.7.5.1 技术要求277
3.7.5 叶轮注射模电火花加工277
3.7.4.2 加工要点277
3.7.6 工艺美术品凹模型腔电火花加工278
3.7.5.3 加工要点278
3.7.5.2 加工前准备278
3.7.8.3 电火花加工方案279
3.7.8.2 工艺性分析279
3.7.7 电火花磨削加工实例279
3.7.7.1 弹簧夹头磨削279
3.7.7.2 偏心钻套磨削279
3.7.8 外支承弹性环深窄槽电火花加工279
3.7.8.1 加工对象279
3.7.9.3 工艺装备280
3.7.9.2 工艺性分析280
3.7.8.4 工艺措施280
3.7.9 滑油导管深盲孔电火花加工280
3.7.9.1 加工对象280
3.8.1 电气安全281
3.8 生产技术安全281
3.7.9.4 加工工艺281
3.7.10 液压伺服阀节流孔电火花加工281
3.7.10.1 加工对象281
3.7.10.2 工艺性分析281
3.7.10.3 工艺措施281
3.8.2.2 电火花加工中火灾的预防282
3.8.2.1 电火花加工中火灾产生的条件282
3.8.2 火灾的防止282
3.8.3.1 电火花加工中有害气体的产生及组成284
3.8.3 有害气体及通风净化284
3.8.2.3 初期火灾的扑灭284
3.8.3.3 通风净化285
3.8.3.2 有害气体对人体的危害285
4.1.1 工作原理、分类及特征287
4.1 概述287
第4章 电火花线切割加工287
4.1.2.2 高速走丝机的“疏松接触式”放电过程288
4.1.2.1 低速走丝机的放电特点288
4.1.2 低速走丝机和高速走丝机的加工机理288
4.1.3 高速走丝和低速走丝线切割对比289
4.1.5 工艺指标及影响因素290
4.1.4.2 适用领域290
4.1.4 工艺特点和适用领域290
4.1.4.1 工艺特点290
4.2.2.1 机床的分类292
4.2.2 机床概况292
4.2 高速走丝电火花线切割加工292
4.2.1 工艺特点292
4.2.2.2 机床型号系列和参数表293
4.2.3.1 机床主机主要部件的结构294
4.2.3 机床主机294
4.2.2.3 机床的组成294
4.2.3.2 导轮组合件296
4.2.3.3 机床电器控制298
4.2.3.4 夹具类型、结构及特点300
4.2.3.5 附件301
4.2.4.1 脉冲电源的分类303
4.2.4 脉冲电源303
4.2.3.6 机床精度检验要求303
4.2.4.2 几种波形的参数范围及加工性能304
4.2.4.3 几种典型脉冲电源电路306
4.2.4.4 自适应控制脉冲电源307
4.2.5.1 数控系统的类型308
4.2.5 数控系统308
4.2.5.4 微型计算机数控系统(CNC)309
4.2.5.3 计算机群控系统309
4.2.5.2 程序控制系统309
4.2.6.1 机床的使用条件314
4.2.6 机床的使用条件及其安装要求314
4.2.7.1 工作液315
4.2.7 工作液和电极丝315
4.2.6.2 机床的安装315
4.2.7.2 电极丝316
4.2.8.1 工艺指标的评定318
4.2.8 基本工艺规律318
4.2.8.2 常用工件材料的种类及加工性319
4.2.8.3 影响工艺指标的因素320
4.2.9.1 对工件图纸进行审核与分析323
4.2.9 加工工艺323
4.2.9.2 工艺准备325
4.2.9.3 工件的加工329
4.2.10.1 编程细则331
4.2.10 程序编制331
4.2.10.3 手工编程332
4.2.10.2 编程前的准备工作332
4.2.10.4 自动编程333
4.2.11.3 模具及成形电极加工348
4.2.11.2 航空零件加工348
4.2.11 应用实例348
4.2.11.1 锥度零件的加工348
4.2.11.4 超厚零件线切割加工351
4.2.11.6 回转端面曲线型面的加工353
4.2.11.5 异形孔喷丝板的加工353
4.3.1 机床概况354
4.3 低速走丝电火花线切割加工354
4.3.2.1 机床主机主要部件355
4.3.2 机床主机355
4.3.2.2 高精度机床的结构特点357
4.3.3.1 电源特点358
4.3.3 脉冲电源358
4.3.2.3 机床精度检验要求358
4.3.2.4 主要技术规格358
4.3.3.2 常用电路形式360
4.3.3.3 实用电路举例362
4.3.4.1 系统组成363
4.3.4 数控系统363
4.3.4.2 几项通用标准364
4.3.4.3 计算机数控(CNC)装置366
4.3.4.4 伺服进给方式369
4.3.6.1 工作液372
4.3.6 工作液和电极丝372
4.3.5 机床的使用条件及其安装要求372
4.3.5.1 机床的使用条件372
4.3.5.2 机床的安装372
4.3.6.2 电极丝374
4.3.7.2 影响切割速度的因素376
4.3.7.1 机床的工作精度检验376
4.3.7 机床的工作精度检验及影响工艺指标的因素376
4.3.7.3 影响表面粗糙度和表面变质层的因素377
4.3.7.4 影响加工精度的因素378
4.3.8.1 加工过程381
4.3.8 加工工艺381
4.3.8.2 减少工件材料变形的措施382
4.3.8.3 多次切割383
4.3.8.4 加工条件的选择385
4.3.8.5 锥度切割391
4.3.8.6 断丝故障和加工缺陷及其解决办法393
4.3.8.8 断芯的自动处理395
4.3.8.7 改善表面层质量的其他措施395
4.3.9.1 ISO代码编程396
4.3.9 程序编制396
4.3.9.2 命令词和命令程序406
4.3.9.3 自动编程409
4.3.10.1 集成电路引线框架冷冲模423
4.3.10 应用实例423
4.3.10.2 高精度粉末冶金模和挤压模425
4.3.10.3 成形刀具和电火花成形加工用电极427
4.3.10.4 零件加工428
4.3.10.5 超行程工件的加工429
5.1.1 概述431
5.1 激光加工431
第5章 高能束加工431
5.1.1.1 激光的产生434
5.1.1.2 激光特性435
5.1.1.3 激光加工原理437
5.1.1.6 激光加工的应用441
5.1.1.5 激光加工的分类441
5.1.1.4 激光加工的特点441
5.1.2.1 加工设备的组成及功用443
5.1.2 激光加工设备443
5.1.2.2 激光器444
5.1.2.3 主光路447
5.1.2.4 机床本体450
5.1.2.5 辅助系统453
5.1.2.6 国内外激光加工设备举例456
5.1.3 激光加工工艺459
5.1.3.1 激光打孔工艺460
5.1.3.2 激光切割工艺476
5.1.3.3 激光表面改性工艺495
5.1.4.1 激光打孔应用实例502
5.1.4 激光加工应用实例502
5.1.4.2 激光切割应用实例508
5.1.5 安全与防护512
5.1.5.1 激光的危害512
5.1.5.2 安全防护514
5.2.1.1 电子束加工的基本原理517
5.2.1 概述517
5.2 电子束加工517
5.2.2 电子束加工设备518
5.2.1.3 电子束加工的特点和应用518
5.2.1.2 电子束加工的分类518
5.2.2.2 电子束打孔机520
5.2.2.1 电子束焊机520
5.2.2.3 电子束曝光机524
5.2.2.6 电子束加工设备的维护和保养527
5.2.2.5 电子束加工设备常用故障及产生原因527
5.2.2.4 电子束铣切机527
5.2.3.2 电子束打孔530
5.2.3.1 电子束焊接(参见《焊接》分册)530
5.2.3 各种电子束加工方法及工艺特点530
5.2.3.3 电子束表面改性处理535
5.2.3.4 电子束熔炼538
5.2.3.5 电子束曝光539
5.2.3.6 电子束铣切548
5.2.3.7 电子束镀膜549
5.2.3.8 电子束加工中的缺陷及产生的原因550
5.2.4.2 化纤喷丝头打孔551
5.2.4.1 喷气发动机燃烧室罩打孔551
5.2.4 电子束加工应用实例551
5.2.4.4 电子束表面熔化处理应用实例552
5.2.4.3 人造革打透气孔552
5.2.5 电子束安全防护553
5.2.4.5 带材的电子束退火553
5.3.1 等离子喷涂原理、分类及特点554
5.3 等离子喷涂技术554
5.3.2.2 喷枪555
5.3.2.1 等离子喷涂设备的组成555
5.3.2 等离子喷涂设备555
5.3.2.3 送粉器556
5.3.2.4 直流电源557
5.3.2.5 控制系统(控制柜)558
5.3.3.1 等离子喷涂粉末材料的要求559
5.3.3 粉末材料559
5.3.2.6 热交换器559
5.3.3.2 粉末材料的发展560
5.3.3.4 几类粉末材料的熔点、密度和显微硬度561
5.3.3.3 MMoCrSi和MCrAIY粉末的化学成分561
5.3.3.5 粉末材料的质量保证562
5.3.4.2 除油工序563
5.3.4.1 凹切工序563
5.3.4 等离子喷涂工艺流程563
5.3.4.5 等离子喷涂工序564
5.3.4.4 预热工序564
5.3.4.3 表面粗化(喷砂)工序564
5.3.5.2 等离子喷涂的工艺参数选择565
5.3.5.1 等离子喷涂过程的重要参数565
5.3.4.6 涂层加工工序565
5.3.5 等离子喷涂工艺参数565
5.3.6.2 涂层性能及测试567
5.3.6.1 涂层性能分类567
5.3.5.3 等离子喷涂常用材料的工艺参数表567
5.3.6 等离子喷涂涂层性能与质量控制567
5.3.6.3 涂层质量的控制575
5.3.7.1 真空等离子喷涂(VPS)技术576
5.3.7 等离子喷涂新技术576
5.3.7.3 水等离子喷涂578
5.3.7.2 惰性气氛等离子喷涂578
5.3.8.1 涂层应用范围及经济技术效益579
5.3.8 等离子喷涂涂层应用579
5.3.8.2 等离子喷涂涂层分类及其典型应用580
5.3.8.3 涂层的去除585
5.3.9 等离子喷涂常见故障及排除方法586
5.4.1.1 等离子弧焊接的原理、分类和特点587
5.4.1 等离子弧焊接587
5.4 等离子弧焊接与切割587
5.4.1.2 等离子弧焊接设备588
5.4.1.3 等离子弧焊接工艺592
5.4.2.1 等离子弧切割的原理及特点594
5.4.2 等离子弧切割594
5.4.2.2 等离子弧切割设备595
5.4.2.3 等离子弧切割工艺597
6.1.3.1 化学铣切加工的特点600
6.1.3 化学铣切加工的基本特征600
第6章 化学铣切加工600
6.1 概述600
6.1.1 化学铣切加工的基本原理600
6.1.2 化学铣切加工的分类600
6.1.4 化学铣切加工的常用术语601
6.1.3.2 化学铣切加工的优点及局限性601
6.2.1.4 测试设备602
6.2.1.3 刻型设备602
6.2 化学铣切加工设备及工装602
6.2.1 化学铣切加工设备602
6.2.1.1 溶液槽602
6.2.1.2 涂敷保护涂料的设备和固化设备602
6.2.2.2 化铣样板的设计和制造标准605
6.2.2.1 化学铣切样板605
6.2.2 化学铣切加工工装605
6.2.2.3 样板侧向腐蚀量的计算606
6.3.2 铝及铝合金化学铣切加工的一般要求609
6.3.1 铝及铝合金化学铣切加工的分类609
6.3 铝及铝合金的化学铣切609
6.3.3.1 清洁处理610
6.3.3 铝合金化学铣切加工工艺610
6.3.3.2 涂敷保护涂料并固化613
6.3.3.3 刻型614
6.3.3.4 化学铣切加工615
6.3.3.6 去除保护涂层619
6.3.3.5 去污处理619
6.3.4 铝合金化学铣切缺陷及排除方法620
6.3.5 提高铝合金化学铣切加工表面质量的途径622
6.3.6 影响铝合金化学铣切加工的主要因素和加工疵病产生的原因及其预防措施623
6.3.7 化学铣切加工对铝合金机械性能的影响626
6.4.1 不锈钢和镍基合金化学铣切加工工艺629
6.4 其他金属材料的化学铣切加工工艺629
6.4.2 钛合金化学铣切加工工艺631
6.4.3 其他合金的化学铣切腐蚀加工工艺规范633
6.5 化学铣切保护涂料634
6.6.1 去除结构中的废重635
6.6 化学铣切加工在航空航天工业中的应用635
6.6.2 化学铣切加工在整体结构中的应用637
6.6.4 用于铣切难于机械加工的材料639
6.6.3 加工锥度工件639
6.7.1 人身技术安全640
6.7 技术安全640
6.6.5 化学铣切加工在挤压型材上的应用640
6.7.3 腐蚀溶液再生技术的应用642
6.7.2 烟雾的处理642
6.7.4 腐蚀溶液的中和处理644
7.1.1.2 工艺特点及应用646
7.1.1.1 加工原理646
第7章 其他特种加工646
7.1 磨粒流加工工艺及设备646
7.1.1 概述646
7.1.2.1 加工设备648
7.1.2 加工设备、磨流介质和夹具(限制器)648
7.1.2.2 磨流介质651
7.1.2.3 夹具(限制器)652
7.1.3.1 磨流介质参数的选择656
7.1.3 工艺参数选择指南656
7.1.3.2 挤压力的合理选择659
7.1.3.4 加工参数选择实例662
7.1.3.3 其他影响因素662
7.1.3.5 机床故障与加工缺陷分析663
7.1.4 磨粒流加工后的表面质量665
7.1.5 磨粒流工艺应用实例666
7.2.1.1 纯水射流切割原理672
7.2.1 纯水射流切割原理、工艺特点及应用672
7.2 高压水射流切割技术672
7.2.1.2 纯水射流切割工艺特性674
7.2.1.3 纯水射流切割的应用676
7.2.2.1 磨料水射流切割原理678
7.2.2 磨料水射流切割原理、切割参数及应用678
7.2.2.2 影响水射流切割质量的因素681
7.2.2.3 磨料水射流切割的应用685
7.2.3.1 纯水射流切割系统的组成689
7.2.3 高压水射流切割系统689
7.2.3.2 磨料水射流切割系统691
7.2.3.3 高压水射流切割机692
7.2.4.1 高压水射流的发展概况696
流696
7.2.4 高压水射流技术的发展和新型射696
7.2.4.2 新型射流697
7.2.4.3 高压水射流技术的应用前景699
7.3.1.1 加工原理700
7.3.1 概述700
7.3 光化学加工700
7.3.1.3 分类及应用范围701
7.3.1.2 工艺特点701
7.3.2 光化学加工主要工艺过程及要点702
7.3.2.1 掩膜版制作703
7.3.2.3 抗蚀层制作方法707
7.3.2.2 零件表面预处理707
7.3.2.4 化学腐蚀与电成形716
7.3.3 光化学加工应用实例724
7.3.2.5 除胶724
参考文献731
1993《航空制造工程手册:特种加工》由于是年代较久的资料都绝版了,几乎不可能购买到实物。如果大家为了学习确实需要,可向博主求助其电子版PDF文件(由《航空制造工程手册》总编委会主编 1993 北京:航空工业出版社 出版的版本) 。对合法合规的求助,我会当即受理并将下载地址发送给你。
高度相关资料
-
- 航空制造工程手册 飞机工艺装备
- 1994 北京:航空工业出版社
-
- 特种加工
- 1991 重庆:重庆大学出版社
-
- 航空制造工程手册 发动机装配与试车
- 1996 北京:航空工业出版社
-
- 航空制造工程手册 非金属结构件工艺
- 1996 北京:航空工业出版社
-
- 航空制造工程手册 通用基础
- 1993 北京:航空工业出版社
-
- 航空制造工程手册 电连接器工艺
- 1996 北京:航空工业出版社
-
- 航空制造工程手册 发动机叶片工艺
- 1998 北京:航空工业出版社
-
- 航空制造工程手册 框架壳体工艺
- 1997 北京:航空工业出版社
-
- 航空制造工程手册 飞机结构工艺性指南
- 1998 北京:航空工业出版社
-
- 航空制造工程手册:机载设备环境试验
- 1995 北京:航空工业出版社
-
- 航空制造工程手册:飞机机械加工
- 1995 北京:航空工业出版社
-
- 航空制造工程手册:电子设备装配
- 1995 北京:航空工业出版社
-
- 航空制造工程手册 救生装备工艺
- 1995 北京:航空工业出版社
-
- 航空制造工程手册 飞机模线样板
- 1993 北京:航空工业出版社
-
- 航空制造工程手册 飞机装配
- 1993 北京:航空工业出版社
提示:百度云已更名为百度网盘(百度盘),天翼云盘、微盘下载地址……暂未提供。➥ PDF文字可复制化或转WORD