《航空制造工程手册 非金属结构件工艺》
作者 | 《航空制造工程手册》总编委会主编 编者 |
---|---|
出版 | 北京:航空工业出版社 |
参考页数 | 467 |
出版时间 | 1996(求助前请核对) 目录预览 |
ISBN号 | 7800469565 — 求助条款 |
PDF编号 | 86777288(仅供预览,未存储实际文件) |
求助格式 | 扫描PDF(若分多册发行,每次仅能受理1册) |
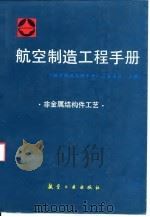
第1章 概论1
1.1 玻璃纤维增强塑料件的范围和特点1
目录1
第1篇 玻璃纤维增强塑料件1
1.2 玻璃纤维增强塑料件的类型3
1.3 玻璃纤维增强塑料件制造技术的内容4
1.4.2 各种成形方法的特点与适用范围5
1.4.1 成形工艺特点5
1.4 玻璃纤维增强塑料件的制造工艺特点5
1.4.3 成形方法的选用原则6
1.5 玻璃纤维增强塑料件制造发展技术现状7
2.1.2.2 基体材料9
2.1.2.1 增强材料9
第2章 材料9
2.1 概述9
2.1.1 材料的范围9
2.1.2 材料的种类9
2.1.2.3 预浸料和夹芯材料10
2.1.3 材料的选择原则11
2.1.2.4 工艺辅助材料11
2.2.1 玻璃纤维及其制品的种类12
2.2 玻璃纤维及其制品12
2.2.2.3 玻璃纤维的耐腐蚀性能14
2.2.2.2 玻璃纤维的介电性能14
2.2.2 玻璃纤维及其制品的特点14
2.2.2.1 玻璃纤维的力学特征14
2.2.3.1 表面处理的方法15
2.2.3 玻璃纤维及其制品的表面处理15
2.2.2.4 玻璃纤维的吸湿性15
2.2.3.3 常用的表面处理剂16
2.2.3.2 浸润剂的去除方法16
2.2.3.4 几种表面处理剂的配制及处理工艺17
2.2.4.1 玻璃纤维纱的规格及其性能18
2.2.4 可供选用的玻璃纤维制品18
2.2.4.2 玻璃纤维织物的规格及其性能19
2.3.1 概述26
2.3 树脂体系26
2.3.2.1 我国航空器上常用的树脂体系28
2.3.2 常用的树脂体系28
2.3.2.2 国外部分树脂体系34
2.3.3.3 环氧树脂的固化剂36
2.3.3.2 酚醛树脂的固化剂36
2.3.3 固化剂36
2.3.3.1 不饱和聚酯树脂的固化剂36
2.4.2 增韧剂39
2.4.1 稀释剂39
2.4 助剂39
2.4.3 阻燃剂40
2.4.4 填料41
2.5.1.2 混合溶液类脱模材料42
2.5.1.1 油膏、石蜡类脱模剂42
2.5 工艺辅助材料42
2.5.1 脱模材料42
2.5.1.3 薄膜类脱模材料43
2.5.2 真空袋材料44
2.5.3 导气材料45
2.5.4 吸胶材料46
2.5.5 隔离材料47
2.5.6 密封材料48
2.6.2 常用的预浸料及其主要性能49
2.6.1 预浸料的类型与特点49
2.6 预浸料49
2.7.1 类型与特点50
2.7 非金属蜂窝芯材50
2.7.3.1 Nomex蜂窝芯材的性能51
2.7.3 蜂窝芯材的性能51
2.7.2 蜂窝的尺寸形状表示法51
2.7.3.2 玻璃布蜂窝芯材的性能56
2.7.4.1 蜂窝骨架材料58
2.7.4 制造蜂窝用的主要材料58
2.8.2 典型的泡沫塑料配方和有关性能59
2.8.1 分类和特点59
2.7.4.2 蜂窝芯条胶59
2.7.4.3 蜂窝浸渍用树脂59
2.8 泡沫塑料59
3.1.1 分类62
3.1 类型与特点62
第3章 模具62
3.1.2.2 阴模64
3.1.2.1 阳模64
3.1.2 各类模具的特点64
3.1.2.3 对模65
3.2.1 常用金属材料67
3.2 模具材料67
3.3.2.1 成形工艺方法要求68
3.3.2 制件成形工艺要求68
3.2.2 常用非金属材料68
3.3 模具选用原则68
3.3.1 制件结构和外形要求68
3.3.1.1 制件外形要求68
3.3.1.2 制件结构要求68
3.3.3.1 模具材料成本69
3.3.3 经济性要求69
3.3.2.2 成形压力要求69
3.3.2.3 成形温度要求69
3.3.2.4 利于脱模69
3.4.1 成形型腔的制造70
3.4 制造与检验70
3.3.3.2 制造成本70
3.3.3.3 使用寿命70
3.4.2.1 模具定位件71
3.4.2 模具结构件制造71
3.4.1.1 标准样件法71
3.4.1.2 切面样板法71
3.4.1.3 数字化程序控制加工法71
3.4.2.2 顶件机构72
3.4.3.2 按模压制件检验73
3.4.3.1 按图纸检验73
3.4.3 检验73
3.5.2.1 定期检验74
3.5.2 模具定期检验与返修74
3.5 使用与维护74
3.5.1 模具的正确使用与维护74
3.5.1.1 脱模剂使用74
3.5.1.2 正常使用74
5.4.1 芯条涂印方法90
5.4 制造方法90
3.5.2.2 返修规定……………………………第4章 预浸料制造4.1 概述………………………………………?4.2 原理与特点………………………………?4.2.1 基本原理………………………………?4.2.2 预浸料的特点…………………………?4.3 预浸料的原材料要求…………90
5.4.1.3 工艺方法91
5.4.1.2 芯条胶的要求与选择91
5.4.1.1 分类、特点与适用范围91
5.4.2.1 芯条叠合95
5.4.2 芯条叠合、固化与分切法95
5.4.3 蜂窝芯拉伸与定形法97
5.4.2.3 蜂窝叠层板分切97
5.4.2.2 蜂窝叠层板固化97
5.4.4.1 浸渍树脂的要求与选择98
5.4.4 蜂窝块浸渍与固化法98
5.5.1 玻璃布蜂窝芯的制造(漏胶法)99
5.5 非金属蜂窝芯制造实例99
5.4.4.2 浸渍方法与固化方法99
5.5.2 芳纶纸蜂窝芯制造(横向印胶法)100
5.6.2 蜂窝芯密度标准与检验方法101
5.6.1 蜂窝芯外观质量标准101
5.6 质量标准与检验方法101
5.7 影响蜂窝芯质量的因素及保证措施102
5.6.4 蜂窝芯强度标准与试验方法102
5.6.3 蜂窝芯块尺寸允差标准102
6.1.2.1 蜂窝夹层结构各种成形方法的特点和适用范围104
6.1.2 夹层结构制造工艺特点104
第6章 夹层结构工艺104
6.1 概述104
6.1.1 基本原理104
6.2 材料105
6.1.2.3 泡沫塑料夹层结构成形方法的特点与适用范围105
6.1.2.2 蜂窝夹层结构分次成形的特点105
6.2.2 夹层结构件常用的胶粘剂和发泡胶106
6.2.1 夹层结构面层和芯层材料的匹配关系106
6.4.1.1 蜂窝夹层结构件制造工艺流程107
6.4.1 蜂窝夹层结构件的成形工艺107
6.3 设备、模具与工装107
6.4 夹层结构件成形工艺107
6.4.1.2 工艺准备的程序和要点109
6.4.1.4 固化110
6.4.1.3 蜂窝夹层结构的组合110
6.4.2.1 预制粘结成形工艺111
6.4.2 泡沫塑料夹层结构件成形工艺111
6.4.1.5 脱模111
6.4.1.6 检验111
6.4.1.7 蜂窝夹层结构件常见的缺陷与解决办法111
6.5.1 结构特点与尺寸112
6.5 蜂窝夹层结构典型件制造实例112
6.4.2.2 整体浇注成形工艺112
6.5.3.1 材料113
6.5.3 材料、工装模具与设备113
6.5.2 成形工艺方法及成形装置113
6.5.4.2 成形前准备114
6.5.4.1 工艺流程与结构组合114
6.5.3.2 工装模具与设备114
6.5.4 制造工艺过程114
6.6.1 典型件简介118
6.6 泡沫塑料夹层结构典型件制造实例118
6.5.4.3 雷达天线整流罩成形……………11?6.5.4.4 制造工艺过程中的缺陷修补118
6.6.3.2 工装模具与设备119
6.6.3.1 材料119
6.6.2 成形工艺方法119
6.6.3 材料、工装模具与设备119
6.6.5 垂尾翼尖成形120
6.6.4 垂尾翼尖制造工艺流程120
7.2.1.1 对增强材料的工艺性要求122
7.2.1 增强材料的要求122
第7章 手糊成形法122
7.1 特点与适用范围122
7.1.1 原理122
7.1.2 工艺特点122
7.1.3 适用范围122
7.2 材料要求与选择122
7.2.2.2 对树脂体系的工艺性要求123
7.2.2.1 对树脂的要求123
7.2.1.2 适用的增强材料123
7.2.2 树脂体系的要求123
7.3.2 模具124
7.3.1.3 修整设备124
7.2.3 脱模材料的要求124
7.3 设备与模具124
7.3.1 设备124
7.3.1.1 配胶设备124
7.3.1.2 加热设备124
7.3.3 常用工具125
7.3.2.2 对模具的要求125
7.3.2.1 模具特点125
7.4.4.1 不饱和聚酯树脂体系126
7.4.4 树脂体系的配制方法126
7.4 制造工艺126
7.4.1 工艺流程126
7.4.2 工艺准备126
7.4.3 玻璃布剪裁方法126
7.4.6 固化工艺及参数127
7.4.5 糊制方法127
7.4.4.2 环氧树脂体系127
7.4.4.3 配制时应注意的问题127
7.5 质量标准与检验方法128
7.4.7.2 修整128
7.4.7 脱模与修整128
7.4.7.1 脱模128
7.7.1 典型件129
7.7 典型件制造实例129
7.6 常见的质量问题及预防措施129
7.7.7 制件检验130
7.7.6 脱模与修整130
7.7.2 对电缆罩性能的要求130
7.7.3 工艺准备130
7.7.3.1 增强材料的准备130
7.7.3.2 模具的准备130
7.7.3.3 树脂体系配制130
7.7.4 糊制130
7.7.5 固化130
8.1.2 工艺特点131
8.1.1 基本原理131
第8章 袋压成形法131
8.1 原理与特点131
8.1.4 适用范围132
8.1.3 分类132
8.2.2 常用树脂类型133
8.2.1 常用的增强材料133
8.2 材料要求与选择133
8.3.1.2 真空设备134
8.3.1.1 加热设备134
8.2.3 树脂体系的使用状态134
8.2.4 工艺材料134
8.3 设备与工具134
8.3.1 设备134
8.3.2.3 模具的类型135
8.3.2.2 模具材料135
8.3.1.3 加压设备135
8.3.2 模具135
8.3.2.1 技术要求135
8.4.1 工艺流程136
8.4 制造工艺136
8.3.2.4 模具结构136
8.3.3 工具136
8.4.4 装袋(工艺组合)137
8.4.3 铺贴坯件137
8.4.2 工艺准备137
8.4.5 固化138
8.6 常见的质量问题与解决措施139
8.5 质量标准与检验方法139
8.4.6 脱模139
8.7.3 主要设备140
8.7.2 技术要求140
8.7 典型件制造实例140
8.7.1 概述140
8.7.5 制造工艺141
8.7.4.2 工艺材料141
8.7.4 主要原材料及工艺辅助材料141
8.7.4.1 原材料141
8.7.6 检验143
9.2.1 预浸料144
9.2 材料要求和选择144
第9章 热压罐成形法144
9.1 原理和特点144
9.1.1 基本原理144
9.1.2 工艺特点144
9.1.3 适用范围144
9.2.3 夹芯层145
9.2.2 夹层结构用胶粘剂145
9.3.1.1 热压罐的构造146
9.3.1 热压罐146
9.2.4 辅助材料146
9.3 设备与工装146
9.3.1.3 先进热压罐的技术特点147
9.3.1.2 热压罐的技术要求147
9.3.1.4 热压罐应用现状148
9.3.2.2 结构形式149
9.3.2.1 模具材料149
9.3.2 成形模具149
9.3.2.3 技术要求150
9.4.1.1 层压板制件制造工艺151
9.4.1 工艺流程与制造工艺151
9.4 制造工艺151
9.4.1.2 夹层制件制造工艺152
9.4.2.1 垂尾前缘制造153
9.4.2 典型件制造实例153
9.4.2.2 玻璃布蜂窝夹层水箱制造154
9.4.3 常见技术故障及处理方法155
9.5 质量标准与检验方法156
10.1.2 工艺特点157
10.1.1 基本原理157
第10章 模压成形法157
10.1 原理与特点157
10.2.2 常用的模压材料158
10.2.1 材料的使用状态158
10.1.3 适用范围158
10.2 材料要求与选择158
10.3.1 加压设备159
10.3 设备与工装159
10.2.3 模压料工艺性能159
10.3.1.1 液压机160
10.3.2.1 模压成形对模具的要求161
10.3.2 模具与工具161
10.3.1.2 机械加压设备161
10.4.2.1 模具准备162
10.4.2 工艺准备162
10.3.2.2 工具162
10.4 模压工艺过程162
10.4.1 模压成形工艺流程162
10.4.3 装模163
10.4.2.3 成形用坯件的准备163
10.4.2.2 制件压制表压的计算163
10.4.5 压制工艺参数164
10.4.4 压制164
10.6 常见质量问题、产生原因及解决办法166
10.5 质量控制与检验166
10.4.6 脱模166
10.4.7 后固化166
11.1.2 工艺特点168
11.1.1 基本原理168
第11章 压注成形法168
11.1 原理与特点168
11.2.1 适用的增强材料169
11.2 材料要求169
11.1.3 适用范围169
11.2.2 适用的树脂基体170
11.3.1.2 真空系统171
11.3.1.1 压力源171
11.3 专用设备与模具171
11.3.1 专用设备171
11.3.1.6 测控系统172
11.3.1.5 加热系统172
11.3.1.3 树脂配制系统172
11.3.1.4 清洗系统172
11.4.5 合模173
11.4.4 树脂体系的配制173
11.3.2 模具173
11.4 制造工艺173
11.4.1 制造工艺流程173
11.4.2 模具的准备173
11.4.3 增强材料的准备与铺置173
11.4.6 压注174
11.4.9 常见质量问题与预防措施175
11.4.8 脱模175
11.4.7 固化与后固化175
11.6.2 原材料176
11.6.1 制件简介与工艺分析176
11.5 质量标准与检验方法176
11.6 典型件制造实例176
11.6.3.3 铺放编织套177
11.6.3.2 模具技术要求177
11.6.3 制造工艺177
11.6.3.1 工艺流程177
11.6.3.5 压注成形178
11.6.3.4 配制树脂体系178
11.6.4 质量检测179
12.1.1 基本原理180
12.1 原理与特点180
第12章 缠绕成形法180
12.1.3 分类与适用范围181
12.1.2 工艺特点181
12.2.2 树脂体系182
12.2.1 纤维182
12.2 材料要求与选择182
12.3.1.1 机械式183
12.3.1 缠绕机183
12.3 设备与工装183
12.3.1.3 国内外生产的一些缠绕机184
12.3.1.2 数控和微机控制184
12.3.2.2 分类185
12.3.2.1 技术要求185
12.3.2 固化设备185
12.3.4.2 分类186
12.3.4.1 技术要求186
12.3.3 模具186
12.3.3.1 技术要求186
12.3.3.2 模具的结构、材料与适用范围186
12.3.4 脱模装置186
12.4.1.2 参数计算187
12.4.1.1 参数定义187
12.4 缠绕工艺187
12.4.1 线型参数187
12.4.3 线型设计与线型工艺参数计算步骤190
12.4.2 线型工艺参数及计算190
12.4.4.3 纤维的线速度192
12.4.4.2 张力192
12.4.4 缠绕工艺参数192
12.4.4.1 树脂体系的粘度192
12.4.6.2 固化工艺参数193
12.4.6.1 工艺准备193
12.4.5 缠绕过程193
12.4.5.1 模具准备193
12.4.5.2 树脂体系配制193
12.4.5.3 缠绕193
12.4.6 固化工艺193
12.5.2 产品的质量标准与检验方法194
12.5.1 工艺过程中的质量控制与检验方法194
12.4.6.3 固化194
12.4.7 脱模194
12.5 质量标准与检验方法194
12.6.2.1 结构与主要指标195
12.6.2 运输机用40升氧气瓶195
12.6 缠绕航空部件及典型制造实例195
12.6.1 缠绕航空部件195
12.6.2.3 缠绕设备和主要参数196
12.6.2.2 主要原材料196
12.6.3 直升机旋翼毂夹板组件197
12.6.2.5 检验197
12.6.2.4 固化工艺及主要参数197
13.2.1 概述…………………………………20?198
13.2 热膨胀模成形法………………………20?198
12.6.3.1 结构与主要指标…………………19?12.6.3.2 主要原材料………………………19?12.6.3.3 缠绕设备和主要参数……………19?12.6.3.4 固化工艺及主要参数198
12.6.3.5 检验………………………………19?第13章 其他成形法198
13.1 拉挤成形法……………………………20?13.1.1 概述…………………………………20?13.1.2 原理与特点…………………………20?13.1.2.1 原理………………………………20?13.1.2.2 工艺特点…………………………20?13.1.2.3 分类………………………………20?13198
13.1.3.2 常用树脂基体……………………20?13.1.4 拉挤成形设备与模具………………20?13.1.4.1 设备的组成和作用………………20?198
13.1.4.2 对模具的要求……………………20?198
13.1.5 拉挤工艺过程………………………20?13.1.5.1 增强纤维集束……………………20?198
13.1.5.2 浸渍树脂…………………………20?13.1.5.3 固化工艺…………………………20?13.1.5.4 后固化……………………………20?198
13.2.7 工艺设备与模具……………………21?208
13.2.6.1 热膨胀材料的基本性能…………20?13.2.6.2 常用热膨胀材料…………………21?208
13.2.2 基本原理……………………………20?13.2.3 工艺特点208
13.2.4 分类208
13.2.5 适用范围……………………………20?208
13.2.6 热膨胀材料…………………………20?208
13.2.8.1 制件坯料的成形212
13.2.8 制造工艺212
13.2.7.1 加热固化设备……………………21?1.3.2.7.2 模具212
13.2.8.4 脱模213
13.2.8.3 固化213
13.2.8.2 装模213
14.2.1 刀具材料与选择214
14.2 刀具材料与几何形状214
第14章 机械加工214
14.1 加工特点和种类214
14.1.1 加工特点214
14.1.2 加工种类214
14.2.2.2 铣刀215
14.2.2.1 车刀215
14.2.2 刀具的几何形状与参数选择215
14.2.2.3 孔加工刀具216
14.3.1.2 螺纹的车削217
14.3.1.1 薄板的车削217
14.3 车削217
14.3.1 车削工艺方法217
14.4.1 铣切方法及特点218
14.4 铣削218
14.3.2 车削工艺参数218
14.4.2.2 拉伸后铣切219
14.4.2.1 拉伸前的切割219
14.4.2 非金属蜂窝芯的铣切219
14.5.2.2 定心钻制孔221
14.5.2.1 钻头制孔221
14.5 钻削221
14.5.1 制孔类型与刀具221
14.5.1.1 制孔类型221
14.5.1.2 制孔用刀具221
14.5.2 层压板件制孔法及工艺参数221
14.5.2.3 套料刀制孔222
14.5.3 蜂窝夹层板件制孔223
14.5.2.4 特种形状刀具制孔223
14.5.5 制孔质量保证措施224
14.5.4 孔径尺寸变化量的计算与取值224
14.6.1.1 砂轮圆锯片225
14.6.1 锯切刀具225
14.6 锯切225
14.6.2 锯切工艺参数226
14.6.1.2 锯条226
14.7.1.3 工艺参数227
14.7.1.2 工艺过程227
14.6.3 锯切质量保证措施227
14.7 高压水射流加工227
14.7.1 加工工艺与参数227
14.7.1.1 原理和特点227
14.7.2 影响制件加工质量的因素228
15.1 产品试制的质量控制…………………22?15.1.1 技术负责人的确定…………………22?15.1.2 明确技术要求229
第15章 质量控制229
15.3.3 主要原材料的质量检验231
15.1.3 试制程序……………………………22?15.1.4 方案评审……………………………22?15.1.5 试制过程的质量控制………………22?15.1.6 鉴定…………………………………23?15.2 人员控制………………………………23?15.2.1 考核形式和内容……………………23?231
15.3.4 材料贮存要求232
15.4.3 量具和仪表的管理233
15.4.2 主要工艺设备的控制233
15.4 设备控制233
15.4.1 一般控制要求233
15.6.1 一般控制要求234
15.6 工艺过程控制234
15.4.4 模具控制234
15.5 工作间的环境条件控制234
15.6.2.4 预浸料铺贴工艺控制235
15.6.2.3 湿法手糊铺贴工艺控制235
15.6.2 主要工序控制235
15.6.2.1 树脂体系配制控制235
15.6.2.2 预浸料剪裁控制235
15.6.2.8 预浸料制造工艺制造236
15.6.2.7 蜂窝芯制造工艺控制236
15.6.2.5 工艺组合控制236
15.6.2.6 固化工艺控制236
15.7.3.1 内部缺陷237
15.7.3 内部缺陷及检测方法237
15.7 成品件的质量控制237
15.7.1 外观质量237
15.7.2 外形尺寸及公差237
15.7.4.2 随炉件的种类与性能检测238
15.7.4.1 随炉件的基本要求238
15.7.3.2 检验方法238
15.7.4 随炉件238
15.8.2 建立档案239
15.8.1 必备文件239
15.7.5 使用性能控制239
15.8 文件和资料控制239
16.2.1 可修补的缺陷类型240
16.2 范围与要求240
第16章 修补技术240
16.1 概述240
16.2.2 修补质量要求241
16.3 修补用材料242
16.4.2 修补工具244
16.4.1 修补设备244
16.4 修补用设备与工具244
16.5.2.2 树脂灌注和填充修补245
16.5.2.1 树脂注射修补245
16.5 修补方法与修补工艺245
16.5.1 修补方法245
16.5.2 修补工艺245
16.5.2.4 胶接贴补246
16.5.2.3 机械连接贴补246
16.5.2.5 胶接挖补247
16.6.2.2 无损检测248
16.6.2.1 外观检验248
16.6 修补质量与检验248
16.6.1 修补质量的影响因素248
16.6.2 质量检验248
16.7 典型修补事例249
16.6.3 质量跟踪249
16.6.2.3 功能试验检测249
17.1.2.3 通风251
17.1.2.2 相对湿度251
第17章 劳动保护251
17.1 作业环境251
17.1.1 一般要求251
17.1.2 具体要求251
17.1.2.1 温度251
17.2.2.1 车间空气中有害物质的最高允许浓度252
17.2.2 有关的安全卫生标准252
17.1.2.4 照明252
17.1.2.5 噪声252
17.1.2.6 工作地面252
17.2 安全卫生标准252
17.2.1 制定安全卫生标准的意义252
17.2.2.2 车间空气中粉尘的最高允许浓度253
17.2.2.4 常用树脂及助剂的毒性254
17.2.2.3 常用易燃溶剂蒸气的闪点及爆炸极限254
17.3.2.1 制定安全规程和加强宣传教育256
17.3.2.2 设备安全措施256
17.3 安全和保健措施256
17.3.1 影响操作者安全及健康的因素256
17.3.2 安全和劳动保护措施256
17.3.2.3 防火防爆措施257
17.3.2.4 劳动保护措施258
17.3.2.5 其它措施259
17.4.2 废弃物的处理方法260
17.4.1 废弃物的种类260
17.4 废弃物的处理260
18.2 航空透明件的特点和要求261
18.1 我国航空透明件工艺发展简况261
第2篇 透明件261
第18章 概论261
18.3 透明件的类型262
18.4 透明件制造技术的范围266
18.5 制造工艺对透明件质量与性能的影响267
18.6 透明件制造技术的发展趋势269
19.1.1 范围、分类及用途270
19.1 概述270
第19章 材料270
19.1.2.1 主要材料271
19.1.2 材料牌号和来源271
19.1.2.2 工艺辅助材料275
19.2.2.1 有机玻璃276
19.2.2 透明塑料板的特性与性能数据276
19.2 刚性透明材料276
19.2.1 种类和应用276
19.2.2.2 定向有机玻璃281
19.2.2.3 聚碳酸酯塑料板283
19.3.1 种类与特性284
19.3 柔性中间层材料284
19.2.3 玻璃的特性与性能数据284
19.3.2 国内中间层材料的性能数据285
19.4.2 边缘加强材料的性能数据286
19.4.1 类型和应用286
19.3.3 国外中间层材料的性能数据286
19.4 边缘连接件材料286
19.4.3 软固定带的性能数据287
19.4.4 胶粘剂的性能数据288
19.5.2 硫化型密封剂的性能数据290
19.5.1 类型和特性290
19.5 密封材料290
19.5.3 非硫化型密封腻子及垫片的性能数据292
20.1.2.2 性能比较与选材指南294
20.1.2.1 选材要求294
第20章 选材依据与工艺基础294
20.1 透明件材料的选择294
20.1.1 选材的基本原则294
20.1.2 刚性透明材料的选材294
20.1.3.1 选材要求296
20.1.3 柔性中间层材料的选材296
20.1.4.2 胶粘剂选材指南297
20.1.4.1 边缘连接件材料选材指南297
20.1.3.2 性能比较与选材指南297
20.1.4 边缘连接材料的选材297
20.1.5 密封材料的选材要求298
20.1.6 工艺辅助材料的选材要求299
20.2.2.1 成形工艺性300
20.2.2 浇铸有机玻璃的工艺特性300
20.2 透明塑料件的工艺基础300
20.2.1 制造质量的影响因素300
20.2.2.3 缺口敏感性301
20.2.2.2 加工工艺性301
20.2.3.1 热松弛特性302
20.2.3 定向有机玻璃的工艺特性302
20.2.2.4 表面开裂性(银纹)302
20.2.3.2 热松弛对材料性能的影响303
20.2.4 聚碳酸酯塑料板的工艺特性304
20.2.3.3 工艺特性304
20.2.5.1 透明件材料的热膨胀系数与热胀差305
20.2.5 连接安装工艺基础305
20.2.5.2 热胀差的分析与处理306
20.2.5.3 制造误差与装配应力307
21.1.1.1 成形模309
21.1.1 分类与特点309
第21章 成形工艺装备与设备309
21.1 有机玻璃成形工艺装备309
21.1.1.3 退火夹具310
21.1.1.2 检验模310
21.1.3.1 成形模的技术要求311
21.1.3 工艺装备的技术要求311
21.1.2 工艺装备的协调311
21.1.2.1 模线样板法311
21.1.2.2 标准样件法311
21.1.2.3 数控模型法311
21.2.1 吹塑成形工艺装备312
21.2 定向有机玻璃成形工艺装备312
21.1.3.2 检验模的技术要求312
21.1.3.3 退火夹具的技术要求312
21.2.1.3 液压系统314
21.2.1.2 加载系统314
21.2.1.1 结构特点与技术要求314
21.2.1.4 气压系统315
21.2.2.1 结构特点与要求316
21.2.2 接触成形工艺装备316
21.2.1.5 冷却系统316
21.3.1 模具材料的种类与选择317
21.3 模具材料与模垫317
21.2.2.2 加载系统317
21.4.1 木模的制造方法318
21.4 模具的制造与检验318
21.3.2 模垫材料的技术要求与种类318
21.4.1.2 木模加工程序319
21.4.1.1 木模机械加工设备319
21.4.1.3 木模制造精度要求321
21.5 加热设备322
21.4.2.3 试模鉴定322
21.4.2 检验方法322
21.4.2.1 检查依据322
21.4.2.2 尺寸检查322
21.6 使用与维护323
21.5.3 温控系统323
21.5.1 类型和选择323
21.5.2 技术要求323
22.1.2.3 成形零件的回弹与补偿324
22.1.2.2 收缩率与工艺余量324
第22章 透明塑料件成形工艺324
22.1 透明塑料件的种类与工艺性设计324
22.1.1 零件的种类324
22.1.2 工艺性设计中的几个问题324
22.1.2.1 零件的展开尺寸324
22.1.2.4 零件的拉伸与变薄量325
22.2.1.2 选择原则326
22.2.1.1 成形方法的种类326
22.2 浇铸有机玻璃成形326
22.2.1 成形方法的种类与选择326
22.2.4.1 凸模接触成形法329
22.2.4 成形方法329
22.2.2 成形工艺流程329
22.2.3 工艺参数与选择329
22.2.3.1 工艺参数329
22.2.3.2 选择依据329
22.2.4.2 凹模真空接触成形法330
22.2.4.4 真空成形装置及压力估算332
22.2.4.3 模框真空自由成形法332
22.2.4.5 模框自由吹塑成形法333
22.2.4.6 凹凸模接触成形法334
22.2.4.7 凹凸模模压成形法335
22.3.1.1 成形方法的种类337
22.3.1 成形方法的种类与选择337
22.2.4.8 凸模真空回缩成形法337
22.3 定向有机玻璃成形337
22.3.1.2 选择原则338
22.3.2 成形工艺流程339
22.3.4.1 模框自由吹塑成形法340
22.3.4 成形方法340
22.3.3 工艺参数与选择340
22.3.3.1 工艺参数340
22.3.3.2 选择依据340
22.3.4.2 凸模接触成形法342
22.3.4.4 刚性框架热成形法344
22.3.4.3 凹模真空接触成形法344
22.4.2.2 加温时间346
22.4.2.1 成形温度346
22.3.4.5 冷弯(热定形)成形法346
22.4 聚碳酸酯塑料板成形346
22.4.1 成形板材的干燥处理346
22.4.1.1 干燥处理的目的346
22.4.1.2 干燥处理的工艺条件346
22.4.2 成形工艺参数346
22.5 常见的成形质量问题、产生原因及排除措施347
22.4.3.2 热成形347
22.4.3 成形方法347
22.4.3.1 冷成形347
23.1.4 影响加工质量的主要因素349
23.1.3 机械加工的种类349
第23章 透明塑料件的机械加工349
23.1 加工特点、要求和种类349
23.1.1 透明塑料件的加工特点349
23.1.2 加工中的基本要求349
23.3.1.1 工具与参数350
23.3.1 锯切350
23.2 划线350
23.2.1 常用划线工具350
23.2.2 划线要求与方法350
23.3 切割350
23.3.1.3 锯切常见质量问题及其原因351
23.3.1.2 工艺参数351
23.4.1.2 设备、工具及参数352
23.4.1.1 特点与工艺要求352
23.3.2 刀割352
23.4 制孔352
23.4.1 钻孔352
23.4.1.3 工艺及参数354
23.4.1.5 质量标准及检验方法355
23.4.1.4 钻孔常见质量问题及预防措施355
23.4.3.1 铰刀356
23.4.3 铰孔356
23.4.2 扩孔356
23.4.2.1 常用扩孔刀具及其特点356
23.4.2.2 扩孔参数选择原则356
23.5.1.1 特点357
23.5.1 特点与刀具参数357
23.4.3.2 工艺要点357
23.5 铣削357
23.5.1.2 刀具参数358
23.5.2 工艺参数360
23.6.2.1 刮削工具361
23.6.2 刮削361
23.6 细加工361
23.6.1 锉削361
23.6.1.1 锉削刀具361
23.6.1.2 锉削方法361
23.6.2.2 刮削方法362
23.6.4.1 抛光特点363
23.6.4 抛光363
23.6.3 打磨363
23.6.3.1 打磨特点363
23.6.3.2 打磨材料的选择363
23.6.3.3 打磨方法及要求363
23.7.3 方法三:切削温度测量364
23.7.2 方法二:表面粗糙度检测364
23.6.4.2 抛光方法及要求364
23.7 机械加工质量的检验364
23.7.1 方法一:目视检查364
23.8.2 机械加工工艺及参数365
23.8.1 典型透明件及其机械加工365
23.7.4 方法四:溶剂银纹法365
23.8 典型透明件机械加工实例365
24.1.2 内应力对制件的影响367
24.1.1 透明塑料制件中的内应力367
第24章 制件的退火处理367
24.1 概述367
24.1.3 减少内应力的途径——退火处理368
24.1.4.2 定向有机玻璃的退火问题369
24.1.4.1 浇铸有机玻璃369
24.1.4 需要退火处理的工艺场合369
24.2.1.1 工艺参数与选择370
24.2.1 浇铸有机玻璃的退火工艺370
24.2 退火工艺370
24.2.1.3 注意事项372
24.2.1.2 工艺程序372
24.2.2.2 退火工艺及应用实例373
24.2.2.1 工艺参数与选择原则373
24.2.2 定向有机玻璃的退火工艺373
25.2.1 胶接接头的受力状态374
25.2 胶接接头设计374
第25章 透明塑料件的胶接374
25.1 范围与种类374
25.1.1 范围374
25.1.2 种类374
25.3 国内常用胶粘剂的配制方法375
25.2.3 胶接接头的基本形式375
25.2.2 胶接接头的基本要求375
25.3.2.2 SYT—1胶的配制376
25.3.2.1 丙烯酸酯胶的配制376
25.3.1 溶剂(溶液)型胶粘剂的配制376
25.3.2 丙烯酸酯类胶粘剂的配制376
25.4 胶接夹具与加热设备377
25.3.3 其它胶粘剂的配制377
25.3.2.3 SYT—2胶的配制377
25.3.2.4 胶粘剂粘度测定法377
25.5 透明塑料的胶接378
25.4.2 夹具形式378
25.4.1 夹具的要求378
25.6.1 胶接结构形式379
25.6 透明塑料件与边缘加强件的胶接379
25.5.1 有机玻璃的胶接379
25.5.2 聚碳酸酯板的胶接379
25.6.2 胶接工艺与应用实例380
25.6.3.2 检验方法381
25.6.3.1 质量标准381
25.6.3 胶接质量标准与检验方法381
25.7.2 胶接工艺与应用实例382
25.7.1 胶接结构形式382
25.6.4 常见质量问题及排除方法382
25.7 有机玻璃件与软固定带的胶接382
25.7.3.2 检验方法383
25.7.3.1 质量标准383
25.7.3 质量标准与检验方法383
26.1.1.2 范围384
26.1.1.1 定义384
第26章 连接安装与密封384
26.1 透明件的连接安装384
26.1.1 定义与范围384
26.1.3 连接安装的基本要求385
26.1.2 安装形式的种类与特点385
26.1.4.2 工艺方法与注意事项386
26.1.4.1 种类386
26.1.4 螺栓连接安装386
26.1.4.3 质量要求和检验方法387
26.1.5.1 安装的结构形式388
26.1.5 镶嵌连接安装388
26.1.4.4 常见故障及预防措施388
26.1.5.2 工艺方法389
26.1.6.1 安装的结构形式390
26.1.6 柔性连接安装390
26.1.6.2 工艺方法391
26.1.6.4 常见故障及预防措施392
26.1.6.3 质量要求与检验392
26.1.7.2 工艺方法393
26.1.7.1 定义393
26.1.7 复合连接安装393
26.2.2.2 嵌缝密封及应用实例394
26.2.2.1 填角密封及应用实例394
26.2 密封装配394
26.2.1 密封剂的要求394
26.2.1.1 工艺性要求394
26.2.1.2 施工环境要求394
26.2.2 透明件与骨架连接结构的密封形式394
26.2.2.4 连接件密封及应用实例395
26.2.2.3 贴合面密封及应用实例395
26.2.3.2 密封用工具396
26.2.3.1 密封前准备396
26.2.3 密封工艺396
26.2.4.2 检验397
26.2.4.1 质量要求397
26.2.3.3 刮涂密封法397
26.2.3.4 刷涂密封法397
25.2.3.5 垫片铺贴与腻子填充密封397
26.2.4 质量要求与检验397
27.1 概述398
第27章 玻璃层合透明件工艺398
27.1.1 玻璃层合透明件的结构特点399
27.2.1 玻璃原片的种类400
27.2 玻璃板的加工与增强400
27.1.2 玻璃层合透明件的工艺特点400
27.2.2.2 磨边401
27.2.2.1 切裁401
27.2.2 玻璃板的冷加工401
27.2.2.3 研磨和抛光402
27.2.3.2 玻璃板的物理钢化403
27.2.3.1 方法、特点与适用范围403
27.2.3 玻璃板的增强403
27.2.3.4 玻璃板增强的质量控制406
27.2.3.3 玻璃板的化学钢化406
27.3.1 类型、特点和应用407
27.3 透明导电元件工艺407
27.3.2 导电网电热元件工艺及应用实例408
27.3.3 热喷涂SnO2透明导电膜工艺及应用实例409
27.3.4 阴极溅射制备ITO膜及应用实例411
27.3.5 阴极溅射制备透明金膜导电元件412
27.4.1 方法类型与特点413
27.4 玻璃层合结构工艺413
27.4.2.1 工艺流程及主要设备414
27.4.2 热压法414
27.4.2.2 配片415
27.4.2.3 热压工艺制度416
27.4.2.5 典型件制造实例417
27.4.2.4 热压夹层法的工艺要点417
27.4.3.2 主要设备及夹具418
27.4.3.1 工艺流程418
27.4.3 叠片聚合法418
27.4.3.4 典型件制造实例419
27.4.3.3 工艺要点及聚合工艺曲线419
27.4.4.4 灌浆工艺及固化参数420
27.4.4.3 灌浆夹具420
27.4.4 灌浆法420
27.4.4.1 GN—581透明有机硅橡胶的特点及应用420
27.4.4.2 工艺流程420
27.4.5 胶合层缺陷产生原因及预防措施421
27.5.1 包边材料工艺特性及边缘结构形式422
27.5 包边装框422
27.4.6 玻璃层合结构工艺的质量控制422
27.6 产品质量要求与检验423
27.5.2 包边装框的质量控制423
28.1.4 清洗方法425
28.1.3 清洗剂种类425
第28章 表面清洗、保护和修整425
28.1 清洗425
28.1.1 清洗目的和要求425
28.1.2 清洗工作间425
28.2.2 表面保护材料426
28.2.1 表面保护的目的426
28.1.5 清洗后质量检查426
28.2 表面保护426
28.2.3 保护材料的使用方法427
28.3.2.1 打磨用材料428
28.3.2 打磨428
28.3 表面修整428
28.3.1 表面修整的目的428
28.3.3.3 擦亮和打蜡429
28.3.3.2 抛光方法429
28.3.2.2 打磨方法429
28.3.3 抛光429
28.3.3.1 抛光用材料429
28.4 特种表面涂饰430
28.3.5 打磨抛光的质量控制430
28.3.4 打磨抛光对有机玻璃性能影响430
29.2 从事透明件制造人员素质要求432
29.1 概述432
第29章 质量控制432
29.3.2.2 有机玻璃性能检测433
29.3.2.1 材料入厂检验433
29.3 材料控制433
29.3.1 材料采购控制433
29.3.2 材料性能控制433
29.3.2.3 单片硅酸盐玻璃性能检测440
29.3.2.5 边缘连接材料性能检测441
29.3.2.4 中间层材料性能检测441
29.3.2.7 密封材料性能检测442
29.3.2.6 边缘连接用胶粘剂性能检测442
29.3.3.3 胶粘剂贮存要求444
29.3.3.2 透明材料和边缘连接材料贮存要求444
29.3.3 贮存控制444
29.3.3.1 材料贮存控制要求444
29.4.2 专用工装的控制要求445
29.4.1 设备控制要求445
29.3.3.4 密封材料贮存要求445
29.3.3.5 透明制件的贮存要求445
29.4 设备工装控制445
29.6 工艺过程控制446
29.5 厂房环境条件控制446
29.6.1.4 成形件的内应力447
29.6.1.3 成形件外形尺寸447
29.6.1 成形工艺控制447
29.6.1.1 成形板材质量447
29.6.1.2 工艺参数447
29.6.4 连接装配质量控制448
29.6.3 胶接质量控制448
29.6.2 机械加工质量控制448
29.7.2 制件厚度控制与检测449
29.7.1 制件外形尺寸标准与检验449
29.7 成品件质量控制449
29.7.4.1 光学质量标准450
29.7.4 制件光学质量标准与检验方法450
29.7.3 制件外观质量际准450
29.7.4.2 检验方法451
29.7.5.1 气密试验基本要求453
29.7.5 制件气密试验453
29.7.5.2 气密试验技术要求454
30.1.6 噪声455
30.1.5 照明455
第30章 安全卫生455
30.1 作业环境455
30.1.1 环境条件455
30.1.2 厂房温度455
30.1.3 厂房湿度455
30.1.4 通风455
30.3.1 化学品毒性大小的表示法456
30.3 劳动卫生456
30.1.7 工作场地456
30.2 劳动安全456
30.3.3 劳动保护措施457
30.3.2 车间空气中有害物质的最高允许浓度457
30.4 废弃物处理458
附录 基础术语浅释459
参考文献465
1996《航空制造工程手册 非金属结构件工艺》由于是年代较久的资料都绝版了,几乎不可能购买到实物。如果大家为了学习确实需要,可向博主求助其电子版PDF文件(由《航空制造工程手册》总编委会主编 1996 北京:航空工业出版社 出版的版本) 。对合法合规的求助,我会当即受理并将下载地址发送给你。
高度相关资料
-
- 航空模型制造工艺学
- 1957 北京:人民体育出版社
-
- 航空蜂窝结构制造工艺
- 1980
-
- 金属结构制造工艺
- 1992 中国劳动出版社
-
- 航空制造工程手册 通用基础
- 1993 北京:航空工业出版社
-
- 航空非金属件失效分析
- 1993 北京:科学出版社
-
- 航空制造工程手册 电连接器工艺
- 1996 北京:航空工业出版社
-
- 航空制造工程手册 发动机叶片工艺
- 1998 北京:航空工业出版社
-
- 航空制造工程手册 框架壳体工艺
- 1997 北京:航空工业出版社
-
- 航空制造工程手册 飞机结构工艺性指南
- 1998 北京:航空工业出版社
-
- 航空制造工程手册:特种加工
- 1993 北京:航空工业出版社
-
- 航空制造工程手册:飞机机械加工
- 1995 北京:航空工业出版社
-
- 航空制造工程手册 救生装备工艺
- 1995 北京:航空工业出版社
-
- 航空制造工程手册 飞机装配
- 1993 北京:航空工业出版社
-
- 航空制造工程手册 飞机工艺装备
- 1994 北京:航空工业出版社
-
- 航空制造工程手册 飞机钣金工艺
- 1992 北京:航空工业出版社
提示:百度云已更名为百度网盘(百度盘),天翼云盘、微盘下载地址……暂未提供。➥ PDF文字可复制化或转WORD