《航空制造工程手册 特种铸造》
作者 | 《航空制造工程手册》总编委会主编 编者 |
---|---|
出版 | 北京:航空工业出版社 |
参考页数 | 1083 |
出版时间 | 1994(求助前请核对) 目录预览 |
ISBN号 | 7800468305 — 求助条款 |
PDF编号 | 81494738(仅供预览,未存储实际文件) |
求助格式 | 扫描PDF(若分多册发行,每次仅能受理1册) |
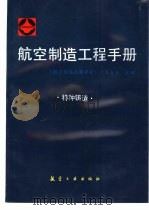
符号说明1
第1章 铸件结构设计1
1.1 概述1
1.2 铸件结构设计原则1
目录1
1.3 铸件结构要素2
1.3.1 铸件壁厚2
1.3.1.1 砂型铸件壁厚2
1.3.1.4 压铸件壁厚4
1.3.1.2 熔模铸件壁厚4
1.3.1.3 金属型铸件壁厚4
1.3.1.5 壳型铸件壁厚5
1.3.2 壁的连接5
1.3.2.1 壁的过渡形式和尺寸5
1.3.2.2 壁的连接形式和尺寸7
1.3.3 铸造圆角12
1.3.4.2 铸造斜度的选择13
1.3.4 铸造斜度13
1.3.4.1 铸造斜度的种类13
1.3.4.3 铸造斜度计算表14
1.3.5 铸造筋17
1.3.5.1 铸造筋的作用17
1.3.5.2 铸造筋的设计17
1.3.5.3 铸造筋的分布与尺寸的关系18
1.3.5.4 压铸件铸造筋的尺寸20
1.3.6 铸孔和铸槽20
1.3.6.1 砂型铸件的铸孔20
1.3.6.2 熔模铸件的铸孔和铸槽21
1.3.6.3 压铸件的铸孔和铸槽21
1.3.6.4 金属型铸件的铸孔22
1.3.6.5 壳型铸件的铸孔22
1.3.7 压铸齿轮和压铸螺纹22
1.3.8.1 砂型铸件的凸台与凸边23
1.3.8.2 熔模铸件的凸台与凸边23
1.3.8 铸造的凸台与凸边23
1.3.8.3 金属型铸件的凸台与凸边24
1.3.8.4 压铸件的凸台24
1.3.9 铸文字与铸图案24
1.3.10 镶嵌件24
1.4 铸件的尺寸精度与表面粗糙度25
1.4.1 铸件的尺寸精度25
1.4.1.1 影响铸件尺寸精度的因素25
1.5 国外航空铸件结构设计26
1.5.1 结构要素26
1.4.1.2 铸件尺寸精度的确定26
1.4.2 铸件的表面粗糙度26
1.5.1.1 内圆角半径28
1.5.1.2 壁和筋28
1.5.2 铸造斜度和分型面28
1.5.3 凸台和凸座28
1.5.4 凸缘28
1.5.6.2 腹板和壁的厚度29
1.5.6.1 长度和宽度29
1.5.5 型芯29
1.5.6 精度29
1.5.6.3 型面30
1.5.6.4 错箱和飞边30
1.5.6.5 平直度30
1.5.7 表面粗糙度30
1.5.8 工艺筋30
1.5.9 装夹平面30
1.5.10 铆接边距31
第2章 熔模铸造32
2.1 概述32
2.1.1 熔模铸造的特点32
2.1.2 熔模铸造的应用实例32
2.2 熔模铸件铸造工艺设计36
2.2.1 铸件在铸型中的位置设计36
2.2.2.1 铸孔39
2.2.2 铸件工艺性设计39
2.2.2.2 加工余量40
2.2.2.3 工艺筋41
2.2.2.4 工艺孔42
2.2.2.5 工艺凸台43
2.2.2.6 基准面的选择44
2.2.3 浇注系统的设计45
2.2.3.1 浇注系统的分类45
2.2.3.2 浇注系统的工艺要求及应用实例47
2.2.3.3 浇注系统各单元的尺寸设计52
2.2.4 补缩系统的设计57
2.2.4.1 冒口57
2.2.4.2 工艺补贴58
2.2.4.3 冷铁58
2.2.5 工艺图及铸件图的绘制59
2.3.1.2 压型组成61
2.3.1.1 压型分类61
2.3.1 压型分类及组成61
2.3 压型设计与制造61
2.3.2 压型设计62
2.3.2.1 压型结构类型62
2.3.2.2 压型分型面选择65
2.3.2.3 型体设计66
2.3.2.4 型芯设计及其安装定位形式76
2.3.2.5 活块设计82
2.3.2.6 压型定位83
2.3.2.7 锁紧机构85
2.3.2.8 抽芯机构89
2.3.2.9 出模机构90
2.3.2.10 压型尺寸精度和表面粗糙度93
2.3.2.11 常用压型材料96
2.3.2.12 总装技术要求96
2.3.3 压型制造97
2.3.3.1 易熔合金压型97
2.3.3.2 石膏压型98
2.3.3.3 环氧树脂压型99
2.3.4 压型实例100
2.3.5 浇注系统模具设计104
2.3.5.1 浇注系统模具设计要点104
2.3.5.2 常用浇注系统的类型105
2.3.5.3 浇注系统模具的典型结构106
2.3.6.3 校正模实例110
2.3.6.2 校正模设计要点110
2.3.6.1 校正模类型110
2.3.6 校正模设计110
2.4 熔模制造111
2.4.1 熔模材料111
2.4.1.1 熔模材料的要求111
2.4.1.2 熔模用原材料及模料种类113
2.4.2 模料成分及性能114
2.4.2.1 蜡基及松香基模料114
2.4.2.3 可溶性模料115
2.4.2.2 塑料模及填充模料115
2.4.2.4 萘基模料116
2.4.2.5 WM系列模料117
2.4.3 模料的回收117
2.4.3.1 石蜡硬脂酸模料的回收处理117
2.4.3.2 松香基模料的回收处理118
2.4.4 制模118
2.4.4.1 分型剂118
2.4.4.2 冷蜡块119
2.4.4.3 校正模119
2.4.4.4 制模工艺120
2.4.5 空心叶片熔模的制造120
2.4.5.1 空心叶片熔模制造的工艺流程120
2.4.5.2 型芯准备120
2.4.5.3 空心叶片熔模的透视检查和测厚121
2.4.5.4 型芯头自由端的制作121
2.4.5.5 金属芯撑121
2.4.6 熔模的缺陷及其防止方法122
2.4.5.6 空心叶片制模工艺参数122
2.4.7 制造熔模的常用设备123
2.4.8 模组组装用具129
2.4.9 模料性能的测试方法130
2.5 铸型的制造130
2.5.1 铸型分类及对型壳的要求130
2.5.2 制壳用耐火材料133
2.5.2.1 电熔刚玉133
2.5.2.2 锆英砂134
2.5.2.3 石英砂134
2.5.2.4 石英玻璃134
2.5.2.5 硅酸铝耐火材料134
2.5.2.6 耐火粘土136
2.5.3 表面活性剂136
2.5.4.1 水玻璃的性质137
2.5.4 水玻璃型壳137
2.5.4.2 水玻璃的处理138
2.5.4.3 水玻璃涂料制壳工艺140
2.5.5 硅酸乙酯型壳141
2.5.5.1 硅酸乙酯的性质142
2.5.5.2 硅酸乙酯水解液用材料143
2.5.5.3 硅酸乙酯水解配料计算144
2.5.5.4 硅酸乙酯的水解146
2.5.5.5 硅酸乙酯涂料制壳工艺147
2.5.6 硅溶胶型壳149
2.5.6.1 硅溶胶的性质149
2.5.6.2 硅溶胶的技术要求151
2.5.6.3 涂料配制152
2.5.6.4 硅溶胶涂料制壳工艺154
2.5.7 复合型壳154
2.5.8 晶粒细化用涂料156
2.5.9.2 造型157
2.5.9.3 铸型焙烧和型壳的后处理157
2.5.9.1 脱蜡157
2.5.9 脱蜡、造型和焙烧157
2.5.10 型壳缺陷及其防止方法160
2.5.11 制壳用的主要设备及装置161
2.5.12 粘结剂、涂料和型壳性能的检测165
2.6 陶瓷型芯166
2.6.1.3 石英玻璃167
2.6.1.2 型芯基体材料的处理167
2.6.1.1 对陶瓷型芯的要求167
2.6.1 陶瓷型芯材料167
2.6.1.4 矿化剂168
2.6.1.5 增塑剂及表面活性剂169
2.6.2 热压注陶瓷型芯169
2.6.2.1 陶瓷浆料的配制169
2.6.2.2 压制型芯171
2.6.2.3 型芯焙烧172
2.6.2.4 型芯强化173
2.6.3 传递模热固型芯174
2.6.2.5 热压注型芯缺陷分析174
2.6.4.1 陶瓷浆料的配比175
2.6.4.2 型芯制备175
2.6.4 灌浆陶瓷型芯175
2.6.5 型芯检测176
2.6.5.1 尺寸检查176
2.6.5.2 外观检查177
2.7 熔模铸件典型工艺177
2.8.1.1 重力浇注180
2.8.1.2 真空吸铸(CLA法)180
2.8.1 合金的浇注180
2.8 合金的浇注与陶瓷滤网净化180
2.8.1.3 离心浇注182
2.8.1.4 熔模铸型低压铸造183
2.8.2 陶瓷滤网净化技术184
2.8.2.1 净化原理184
2.8.2.2 陶瓷过滤网184
2.8.2.3 过滤效率185
2.8.2.4 应用186
2.9 熔模铸件常见缺陷及其防止188
方法188
2.10 熔模铸件控制凝固技术193
2.10.1 定向凝固和单晶技术193
2.10.1.1 定向凝固技术193
2.10.1.2 单晶技术195
2.10.1.3 定向和单晶合金的化学成分和持久强度196
2.10.1.4 定向凝固设备及操作197
2.10.1.5 应用199
2.10.2 细晶铸造技术201
2.10.2.1 工艺特点201
2.10.2.2 工艺方法201
2.10.2.3 应用202
第3章 金属型铸造204
3.1 概述204
3.2.2 分型面的选择205
3.2.1 铸件在金属型中的位置205
3.2 金属型铸件工艺设计205
3.2.3 铸件工艺性设计206
3.2.4 浇注系统设计207
3.2.4.1 浇注系统设计原则207
3.2.4.2 浇注系统的形式208
3.2.4.3 各种形式浇道的充型过程及热分布209
3.2.4.4 浇注系统组成部分211
3.2.4.5 浇注系统计算218
3.2.5.1 冒口的类型221
3.2.5 冒口的设计221
3.2.5.2 冒口尺寸计算222
3.2.5.3 减小冒口的措施223
3.2.6 铸件工艺图实例224
3.3 金属型铸造机227
3.3.1 金属型铸造机分类227
3.3.2 通用金属型铸造机结构形式228
3.3.2.1 可倾斜齿条传动铸造机228
3.3.2.2 可倾斜螺杆传动铸造机229
3.3.2.3 可倾斜气压传动铸造机230
3.3.2.4 可倾斜液压铸造机231
3.3.2.5 固定式液压铸造机231
3.3.2.6 四开型液压铸造机234
3.3.3 铸造机的选定236
3.3.3.1 金属型的外形尺寸236
3.4 金属型设计237
3.4.1 金属型分类及结构特点237
3.3.3.2 金属型开型力和抽芯力计算237
3.4.2 金属型结构设计239
3.4.2.1 型体设计239
3.4.2.2 型芯设计243
3.4.2.3 活块设计249
3.4.2.4 型腔尺寸计算250
3.4.2.5 金属型排气252
3.4.3 金属型操纵机构设计254
3.4.3.1 开(合)型机构254
3.4.3.2 锁紧机构256
3.4.3.3 抽芯机构260
3.4.3.4 顶出机构270
3.4.4 金属型加热与冷却装置275
3.4.4.1 金属型加热装置275
3.4.4.2 金属型冷却装置280
3.4.5.2 金属型零件常用材料282
3.4.5.3 金属型材料的物理性能282
3.4.5.1 对金属型材料的要求282
3.4.5 金属型用材料282
3.4.6 金属型的尺寸精度与表面粗糙度283
3.4.6.1 金属型的尺寸精度283
3.4.6.2 金属型表面粗糙度284
3.4.7 金属型结构实例284
3.5 金属型铸造工艺288
3.5.1 金属型的准备288
3.5.1.1 金属型的清理288
3.5.1.3 金属型涂料的涂敷工艺289
3.5.1.2 金属型预热289
3.5.2 金属型用涂料290
3.5.2.1 涂敷涂料的目的和对涂料的要求290
3.5.2.2 涂料的组成290
3.5.2.3 涂料成分在涂料中的作用291
3.5.2.4 各种铸造合金用金属型涂料292
3.5.2.5 涂料的配制294
3.5.3 金属型浇注工艺294
3.5.3.1 金属型的工作温度294
3.5.3.2 合金的浇注温度295
3.5.3.3 金属型铸件的浇注速度295
3.5.3.4 铸件在金属型中保持时间295
3.5.4 金属型的试铸296
3.5.4.1 尺寸定型296
3.5.4.2 冶金定型296
3.6 典型金属型铸件工艺297
方法298
3.7 金属型铸件常见缺陷及其防止298
第4章 压力铸造300
4.1 概述300
4.1.1 压力铸造的工艺过程300
4.1.2 压力铸造的工艺特点300
4.1.3 压力铸造的优缺点及应用范围300
4.2.1 压铸机种类及特点302
4.2.1.1 热压室压铸机302
4.2 压铸机302
4.2.1.2 冷压室压铸机303
4.2.2 压铸机的选用305
4.2.3 国产常用压铸机的型号和主要参数307
4.2.3.1 国产压铸机的基本参数307
4.2.3.2 国产常用压铸机主要参数及铸型安装尺寸307
4.2.4 国外压铸机的型号和主要参数320
4.3 压铸件铸造工艺设计330
4.3.1 分型面设计330
4.3.1.1 分型面的分类330
4.3.1.2 选择分型面的原则331
4.3.2.1 浇注系统的结构333
4.3.2.2 浇注系统的设计原则333
4.3.2 浇注系统设计333
4.3.2.3 浇注系统的组成335
4.3.2.4 浇注系统的种类及特点349
4.3.3 铸件工艺图实例351
4.4 压铸合金354
4.4.1 压铸合金的基本要求354
4.4.2.1 国内常用压铸合金355
4.4.2 常用压铸合金355
4.4.2.2 国外常用压铸合金359
4.5 压铸工艺参数366
4.5.1 压铸压力366
4.5.1.1 比压366
4.5.1.2 压力的变化及作用367
4.5.1.3 压力损失折算系数367
4.5.4.1 铸型预热温度368
4.5.4 铸型温度368
4.5.2 充填速度368
4.5.3 浇注温度368
4.5.4.2 铸型工作温度369
4.5.5 压铸用涂料369
4.5.5.1 涂料的作用369
4.5.5.2 对涂料的要求369
4.5.5.3 常用压铸涂料370
4.5.6 充填时间与持压时间371
4.5.6.1 充填时间371
4.5.6.2 持压时间371
4.6 压铸型设计371
4.6.1 压铸型的组成371
4.6.2 压铸型外形尺寸及动型、静型主要零件的设计372
4.6.2.1 压铸型外形尺寸372
4.6.2.2 动型、静型镶块结构设计377
4.6.2.3 型芯的结构设计379
4.6.2.4 导柱和导套设计381
4.6.3 压铸型成形部分的尺寸计算386
4.6.3.1 影响铸件尺寸精度的因素386
4.6.3.2 压铸型成形零件的尺寸计算387
4.6.3.3 压铸螺纹成形零件的尺寸计算388
4.6.4 溢流槽和排气槽设计389
4.6.4.1 溢流槽的设计389
4.6.4.2 排气槽的设计393
4.6.5.1 抽芯力的确定395
4.6.5 抽芯机构设计395
4.6.5.2 斜销抽芯机构397
4.6.5.3 弯销抽芯机构407
4.6.5.4 斜滑块抽芯机构412
4.6.5.5 齿轴齿条抽芯机构414
4.6.5.6 液压抽芯机构416
4.6.6 顶出机构设计422
4.6.6.1 顶出机构的组成423
4.6.6.2 常用顶出机构423
4.6.6.3 顶出机构的导向装置431
4.6.6.4 顶出机构的复位435
4.6.7 加热与冷却系统设计438
4.6.7.1 铸型预热方法438
4.6.7.2 铸型冷却方法438
4.6.8 压铸型材料选择和热处理440
4.6.8.1 成形部分零件材料的选择原则440
4.6.8.2 导滑、顶出元件等零件材料的选择原则440
4.6.8.3 压铸型主要零件材料选用及热处理要求440
4.6.9.1 压铸型零件的公差与配合441
4.6.9 压铸型的技术要求441
4.6.9.2 压铸型零件不同工作面的表面粗糙度443
4.6.9.3 对压铸型总装的要求443
4.6.9.4 对压铸型零件的要求444
4.7 典型压铸件工艺444
4.8 压铸件常见缺陷及其防止448
方法448
4.9.1 压铸机的改进449
4.9 特殊压铸技术449
4.9.2 浇注、喷涂料、取件自动化450
4.9.3 真空压铸452
4.9.4 充氧压铸454
4.9.5 精速密压铸455
4.9.6 半固态压铸456
4.9.7 热能去毛刺457
4.9.8 计算机在压铸生产中的应用458
4.9.8.1 压铸工艺计算机辅助设计458
(CAD)458
4.9.8.2 压铸型计算机辅助设计与制造(CAD/CAM)458
4.9.8.3 生产过程计算机控制458
第5章 石膏型铸造460
5.1 概述460
5.1.1 石膏型铸造的分类和工艺过程460
5.1.2 石膏型铸造的工艺特点和应用范围460
5.2.2 铸件的收缩率461
5.2.1 铸件铸造位置和分型面选择461
5.2 石膏型铸件工艺设计461
5.2.3 铸件的尺寸精度和表面粗糙度462
5.2.4 铸造斜度和加工余量462
5.2.5 铸件浇注系统设计462
5.2.6 冒口设计和冷铁应用463
5.3 石膏型铸造用材料和模具463
5.3.1 原材料及其基本性能463
5.3.1.1 石膏463
5.3.1.2 辅助材料464
5.3.2 石膏铸型材料的组成、性能及其测定方法465
5.3.2.1 石膏铸型材料的组成和性能要求465
5.3.2.2 各种因素对石膏铸型材料性能的影响465
5.3.2.3 石膏铸型材料性能的测定方法469
5.3.3 石膏型铸造用模具471
5.3.3.1 模具的分类和材料471
5.4.1.1 浆料的配制472
5.4.1 石膏浆料的配制和灌浆工艺472
5.3.3.2 模具的结构设计472
5.4 石膏型制造工艺和设备472
5.4.1.2 铸型的灌浆473
5.4.2 石膏型的蒸汽处理和脱蜡474
5.4.2.1 铸型蒸汽处理474
5.4.2.2 铸型脱蜡474
5.4.3 石膏型的干燥和焙烧474
5.4.3.1 石膏型干燥焙烧的工艺特点474
5.4.3.2 石膏型干燥焙烧的典型工艺476
5.4.3.3 石膏型干燥程度的检测方法476
5.4.3.4 石膏型的出炉和浇注前准备477
5.4.3.5 石膏型的干燥焙烧设备477
5.5 石膏型的浇注工艺及设备477
5.5.1 石膏型浇注工艺方法477
5.5.2 石膏型浇注设备478
5.5.3 石膏型铸件的组织和性能479
5.6.1 叶轮480
5.6 典型石膏型铸件工艺480
5.6.2 波导管481
5.6.3 复杂整体壳体铸件481
5.7 石膏型铸件的常见缺陷及防止方法482
第6章 壳型铸造484
6.1 概述484
6.1.1 壳型铸造的工艺过程484
6.1.2 壳型铸造的工艺特点及应用范围485
6.2 壳型铸件铸造工艺设计485
6.2.1 铸件在铸型中的位置485
6.2.2 铸件分型面的选择485
6.2.3 壳芯设计486
6.2.3.1 壳芯的结构设计486
6.2.3.2 壳芯头设计487
6.2.3.3 壳型芯头与壳型芯座的配合间隙491
6.2.4.1 浇注系统设计原则492
6.2.4.2 浇注系统形式492
6.2.4 浇注系统设计492
6.2.5 补缩系统设计494
6.2.6 冷铁的应用494
6.2.7 铸件工艺图实例494
6.3 壳型铸造铸型的设计495
6.3.1 壳型铸造铸型的分类495
6.3.2 壳型铸造铸型的组成单元496
6.3.3 壳型型板设计496
6.3.3.1 型板的结构形式496
6.3.3.2 型板的结构设计496
6.3.4 壳芯盒及热芯盒设计499
6.3.4.1 芯盒的结构形式499
6.3.4.2 分型面的选择500
6.3.4.3 盒体的设计501
6.3.4.4 型芯及活块的设计504
6.3.4.5 型腔尺寸计算506
6.3.4.6 嵌件的定位507
6.3.4.7 型腔的排气508
6.3.4.8 吹嘴、射砂头、吹砂板、射砂板及射砂口512
6.3.4.9 芯盒的定位516
6.3.4.10 取芯机构517
6.3.5 壳型型板、壳芯盒及热芯盒的加热装置524
6.3.6 壳型型板、壳芯盒及热芯盒的技术要求526
6.3.6.1 壳型型板、壳芯盒及热芯盒常用材料及热处理526
6.3.6.3 总装技术要求527
6.3.6.2 壳型型板、壳芯盒及热芯盒零件的尺寸精度和表面粗糙度527
6.4 壳型铸造铸型实例528
6.5 制壳型(芯)材料533
6.5.1 原材料及其基本性能533
6.5.1.1 原砂533
6.5.1.2 树脂、硬化剂及附加物534
6.5.2 树脂砂的配制541
6.5.2.1 原材料的准备541
6.5.2.2 壳型铸造用树脂砂的成分、性能及应用范围541
6.5.2.3 树脂砂的配制工艺和特点547
6.5.2.4 树脂砂性能的测定548
6.6 壳型铸造工艺549
6.6.1 壳型铸造工艺分类549
6.6.2 壳型(芯)制造原理549
6.6.3 分型剂550
6.6.4 壳型(芯)制造工艺551
6.6.4.1 壳型(芯)制造工艺过程551
6.6.4.2 壳型(芯)制造工艺参数553
6.6.4.3 热芯盒法制芯典型操作工艺554
6.6.5 工艺因素对壳型(芯)制造质量的影响及其控制556
6.6.6 壳型及壳芯的缺陷分析557
6.6.7 壳型的合型与装配557
6.6.7.1 壳型的合型与装配工艺及应用范围557
6.6.8.2 各类合金的典型浇注温度559
6.6.8.1 铸件的浇注和清理工艺559
6.6.7.2 壳型装配用化学粘合剂的成分、特性及工艺要求559
6.6.8 铸件的浇注和清理559
6.7 壳型铸造设备560
6.7.1 混砂设备560
6.7.1.1 ZS7215型热法树脂砂混砂560
装置560
6.7.1.2 S116型混砂机的热法覆膜砂混砂系统561
6.7.2 壳型机562
6.7.3.1 上吹式壳芯机564
6.7.3 壳芯机564
6.7.3.2 下吹式壳芯机566
6.7.3.3 上吹翻斗式壳芯机566
6.7.4 射芯机569
6.8 典型壳型铸件工艺574
6.9 壳型铸件常见缺陷及其防止576
方法576
7.1 概述577
7.1.1 低压铸造的基本原理577
第7章 低压铸造577
7.1.2 低压铸造的工艺过程578
7.1.3 低压铸造的工艺特点及其应用范围578
7.2 低压铸件铸造工艺设计579
7.2.1 铸件在铸型中的位置579
7.2.2 铸件分型面的选择580
7.2.3 浇注系统设计581
7.2.3.1 选择原则581
7.2.3.2 浇冒口的数量和大小581
7.2.3.3 浇注系统的形式581
7.2.4 补缩系统设计581
7.2.5 铸件工艺图实例584
7.3 低压铸造的铸型设计585
7.3.1 低压铸造的铸型分类及组成585
7.3.2 铸型的型腔及结构设计587
7.4.1 设备总体592
7.4.2 设备形式592
7.4 低压铸造设备592
7.4.3 设备结构597
7.4.3.1 铸型开(合)型机构597
7.4.3.2 保温炉及密封系统598
7.4.3.3 液面加压控制系统606
7.5 低压铸造工艺615
7.5.1 低压铸造工艺操作过程615
7.5.3.1 加压过程616
7.5.3 工艺参数的选择控制616
7.5.2 浇注前的准备616
7.5.3.2 升液速度617
7.5.3.3 充型压力617
7.5.3.4 充型速度617
7.5.3.5 结晶压力621
7.5.3.6 保压时间621
7.5.3.7 液面加压规范622
7.5.3.8 铸型温度和浇注温度623
7.6 典型低压铸件工艺623
方法624
7.7 低压铸件常见的缺陷及其防止624
7.8 特殊低压铸造技术626
7.8.1 差压铸造626
7.8.1.1 差压铸造的工作原理626
7.8.1.2 差压铸造的工艺特点及其应用范围626
7.8.1.3 差压铸造分类626
7.8.1.4 差压铸造设备626
7.8.1.5 差压铸造浇注工艺627
7.8.1.6 铸件冶金质量及合金力学性能的评估628
7.8.2 调压铸造629
7.8.2.1 调压铸造的工作原理629
7.8.2.2 调压铸造的工艺特点及应用范围630
7.8.2.3 调压铸造的浇注工艺630
7.8.4.2 电磁低压铸造设备631
7.8.4.3 电磁低压铸造的工作过程631
7.8.4 电磁低压铸造631
7.8.4.1 电磁低压铸造的工作原理631
7.8.3 引气负压低压铸造631
7.8.4.4 电磁低压铸造的工艺特点及应用范围632
第8章 其他特种铸造633
8.1 陶瓷型铸造633
8.1.1 陶瓷型铸造的工艺过程633
8.1.2 陶瓷型铸造的工艺特点及应用范围633
8.1.3 陶瓷型铸件铸造工艺设计634
8.1.3.1 母模材料634
8.1.3.2 工艺设计技术规范634
8.1.4 陶瓷铸型用原材料635
8.1.5 陶瓷型铸造工艺636
8.1.5.1 陶瓷型工艺分类、特点及应用范围636
8.1.5.4 陶瓷型制作工艺637
8.1.5.5 合箱、浇注和清理637
8.1.5.3 陶瓷型浆料的配制637
8.1.5.2 预制型(砂套)制作637
8.1.6 典型陶瓷型铸件工艺639
8.1.7 陶瓷型铸件常见缺陷及其防止方法640
8.2 挤压铸造641
8.2.1 挤压铸造的工艺过程641
8.2.2 挤压铸造的工艺特点及其应用范围641
8.2.3.2 挤压铸造机的结构642
8.2.3.1 设备总体642
8.2.3 挤压铸造设备642
8.2.3.3 挤压铸造机的技术规格643
8.2.4 挤压铸造工艺643
8.2.4.1 型芯制造643
8.2.4.2 挤压铸造机的准备645
8.2.4.3 型芯的安装及挤铸647
8.2.4.4 铸件的出型及清理647
8.2.5 挤压铸件的热处理及矫正648
8.2.6 典型挤压铸件工艺649
8.2.7 挤压铸件常见缺陷及其防止方法650
8.3 细孔铸造651
8.3.1 细孔铸造的工艺过程、特点及应用651
8.3.1.1 细孔铸造工艺过程651
8.3.1.2 细孔铸造工艺特点及应用651
8.3.2 铜管型芯设计652
8.3.2.1 铜管型芯设计原则652
8.3.2.2 铜管型芯的结构和有关尺寸652
8.3.3.2 灌低熔点合金655
8.3.3 铜管型芯制造655
8.3.3.1 下料655
8.3.3.3 铜管型芯弯制656
8.3.3.4 加工排气孔658
8.3.3.5 去除低熔点合金659
8.3.4 铜管型芯组合659
8.3.4.1 铜管型芯组合形式659
8.3.4.4 细孔通道型芯组合661
8.3.4.5 细孔通道型芯在铸型中的定位661
8.3.4.2 铜管型芯焊前准备661
8.3.4.3 铜管型芯焊接夹具661
8.3.5 型芯表面涂料662
8.3.6 铜管型芯的去除662
8.3.6.1 直通式腐蚀法663
8.3.6.2 浸入式腐蚀法663
8.3.6.3 型芯腐蚀、铸件清洗用槽液技术要求663
8.3.7 细孔通道的检查663
8.3.8 典型细孔铸件工艺664
8.3.9 细孔铸件常见缺陷及其防止方法665
8.4 真空吸铸667
8.4.1.2 真空吸铸的工艺特点及应用668
8.4.2 真空吸铸设备668
8.4.2.1 熔化炉669
8.4.2.2 结晶器669
8.4.2.3 结晶器升降机670
8.4.2.4 真空系统671
8.4.2.5 冷却系统673
8.4.3 真空吸铸工艺673
8.4.3.1 吸铸温度的选择673
8.4.3.2 真空压强的选择674
8.4.3.3 结晶器在液体金属中的浸入深度674
8.4.3.4 出模时间的确定674
8.4.3.5 铸件加工余量675
8.4.3.6 涂料675
8.4.4 典型真空吸铸件工艺676
8.4.5 真空吸铸件常见缺陷及其防止方法676
8.4.1.1 真空吸铸工艺过程677
8.4.1 真空吸铸的工艺特点及其应用677
第9章 钛合金铸造679
9.1 概述679
9.1.1 钛合金铸造技术的发展679
9.1.2 铸造钛合金的牌号及化学成分679
9.1.3 钛合金铸件的应用680
9.2.2.2 工业钛合金的热导率682
9.2.2.1 工业钛合金的密度和熔化温度682
9.2.1 纯钛的物理性能682
9.2.2 工业钛合金的物理性能682
9.2 钛合金特性及铸造工艺设计682
9.2.2.3 工业钛合金的线膨胀系数683
9.2.2.4 工业钛合金的比热容683
9.2.2.5 工业钛合金的电阻率683
9.2.3 钛及其合金的化学性能684
9.2.3.1 钛的抗氧化性能684
9.2.3.2 钛的耐腐蚀性能684
9.2.3.3 氢脆685
9.2.4 钛合金的铸造性能685
9.2.4.1 流动性685
9.2.4.2 收缩与缩孔685
9.2.4.3 形成气孔的倾向性686
9.2.4.4 抗裂性686
9.2.5 钛合金铸件的结构设计与工艺设计686
9.2.5.1 铸件结构设计686
9.2.5.2 铸件工艺设计687
9.2.6 钛合金铸件的尺寸精度与表面粗糙度688
9.2.7 钛合金铸件浇注系统及补缩系统设计原则688
9.2.7.1 设计原则688
9.2.7.2 改善铸件补缩的主要方法688
9.3 钛合金铸造用铸型及造型690
方法690
9.3.1 造型材料的性能及要求690
9.3.1.1 耐火材料690
9.3.1.2 粘结剂691
9.3.2 石墨铸型692
9.3.2.1 石墨加工型692
9.3.2.2 石墨捣实型692
9.3.3 熔模铸型693
9.3.3.1 石墨熔模铸型694
9.3.3.2 钨面层陶瓷熔模铸型695
9.3.3.3 惰性氧化物面层陶瓷熔模铸型695
9.4 钛合金的熔炼与浇注696
9.3.4.4 石墨气相沉积铸型696
9.4.1 钛合金铸造用母合金696
9.3.4.1 金属铸型696
9.3.4.2 氧化物陶瓷铸型696
9.3.4 其他铸型工艺696
9.3.4.3 石墨壳型696
9.4.2 真空自耗电弧凝壳炉结构697
9.4.2.1 类型697
9.4.2.2 结构697
9.4.2.3 技术特性699
9.4.3 钛合金真空自耗电弧凝壳熔炼浇注工艺699
9.4.3.1 工艺参数699
9.4.3.2 熔炼浇注工艺700
9.4.3.3 凝壳熔炼操作的技术安全701
9.4.4 钛合金其他熔炼方法702
9.5.1 力学性能703
9.5.1.1 技术标准规定的力学性能703
热处理703
9.5 铸造钛合金的性能、组织及其703
9.5.1.2 在不同温度下的拉伸性能704
9.5.1.3 热稳定性能704
9.5.1.4 扭转性能705
9.5.1.5 缺口拉伸性能705
9.5.1.6 持久和蠕变性能706
9.5.1.7 疲劳性能706
9.5.1.8 断裂韧性707
9.5.1.9 弹性性能708
9.5.2 相变与金相组织708
9.5.2.1 相转变温度708
9.5.2.2 宏观金相组织708
9.5.2.3 显微金相组织709
9.5.2.4 铸件表面层金相组织710
9.5.3 钛合金铸件的热处理710
9.6.2 修补711
9.6.1 清理711
9.6.2.1 补焊711
9.6 钛合金铸件的清理、修补与711
检验711
9.6.2.2 热等静压处理713
9.6.2.3 校正713
9.6.3 钛合金铸件出厂检验713
9.6.4 钛合金铸件的常见缺陷714
第10章 铝、镁合金砂型铸造715
10.1 概述715
10.2.1.1 原砂716
10.2 造型(芯)用材料716
10.2.1 造型(芯)用材料及其性能716
10.2.1.2 粘结剂718
10.2.1.3 附加物722
10.2.2 型砂和芯砂722
10.2.2.1 铝、镁合金用型砂和芯砂的工艺特性及技术要求722
10.2.2.2 铝、镁合金用粘土型(芯)砂的典型配方及配制722
10.2.4.1 冷硬呋喃树脂砂铸造特点725
10.2.4 铝、镁合金铸造用冷硬呋喃树脂砂725
10.2.3 激冷用特殊砂725
10.2.4.2 冷硬呋喃树脂砂的主要组成及其性能要求726
10.2.4.3 铝、镁合金用冷硬呋喃树脂砂的配制730
10.3 砂型铸造工艺设计731
10.3.1 铸件在砂型中的位置731
10.3.2 铸件分型面选择732
10.3.3 浇注系统设计734
10.3.3.1 浇注系统的类型734
确定735
10.3.3.2 浇注系统结构及尺寸的735
10.3.4 补缩系统设计745
10.3.4.1 冒口设计745
10.3.4.2 冷铁的设计和应用749
10.3.5 砂芯设计750
10.3.5.1 确定砂芯形状的基本原则751
10.3.5.2 芯头结构751
10.3.6.2 机械加工余量753
10.3.6.1 铸造收缩率753
10.3.6 铸造工艺参数选择753
10.3.5.3 砂型铸件型芯最大长度与直径的关系753
10.3.6.3 铸造斜度754
10.3.6.4 最小铸孔(槽)尺寸754
10.3.6.5 工艺补正量754
10.4 造型(芯)工艺及装备755
10.4.1 造型755
10.4.1.1 常用的造型方法、种类及使用范围755
10.4.1.2 铝、镁合金砂型造型的工艺要点755
10.4.2 制芯756
10.4.2.1 砂芯的通气孔(道)形成方法756
10.4.2.2 砂芯的涂膏和粘胶的成分及其配制756
10.4.3 冷硬呋喃树脂砂造型及制芯工艺757
10.4.3.1 冷硬呋喃树脂砂的硬化特性757
10.4.3.2 冷硬呋喃树脂砂造型和制芯工艺759
10.4.4.2 模板760
10.4.4.1 模样760
10.4.4 铝、镁合金砂型铸造用工艺装备760
10.4.4.3 砂箱761
10.4.4.4 砂芯盒764
10.4.4.5 烘芯板765
10.5 典型砂型铸造工艺766
10.5.1 典型铸件的铸造工艺实例766
10.5.1.1 机翼前缘襟翼壁板766
10.5.1.2 直升机发动机减速器机匣767
10.5.1.3 歼击机吹气襟翼前缘768
10.5.1.4 发动机附件传动机匣769
10.5.1.5 大型吊挂梁770
10.5.1.6 其他典型铝、镁合金铸件铸造工艺实例772
10.5.1.7 几类典型镁合金铸件工艺参数774
10.6 铝、镁合金砂型铸件的常见775
缺陷及其防止方法775
11.1 铸造铝合金熔炼和浇注779
11.1.1 铸造铝合金的牌号与化学成分779
第11章 有色合金熔炼与浇注779
11.1.2 熔炼用材料780
11.1.2.1 金属材料780
11.1.2.2 辅助材料781
11.1.3 熔炼设备与工具782
11.1.3.1 熔炼用炉782
11.1.3.2 坩埚与工具784
11.1.4 熔炼前的准备785
11.1.4.1 铝合金配料785
11.1.4.2 炉料和辅助材料的准备787
11.1.4.3 坩埚和工具的准备788
11.1.5 铸造铝合金的精炼和变质处理789
11.1.5.1 精炼789
11.1.5.2 变质和孕育处理792
11.1.6 铸造铝合金熔炼工艺795
11.1.6.1 中间合金熔炼工艺要点795
11.1.6.2 典型铸造铝合金的熔炼工艺要点796
11.1.7 铸造铝合金的浇注工艺797
11.1.8 铸造铝合金熔炼质量的控制797
11.1.8.1 合金化学成分的控制797
11.1.8.2 氢含量的控制和测定798
11.1.8.3 变质效果的控制和检验799
11.2 铸造镁合金熔炼和浇注800
11.2.1 铸造镁合金的牌号与化学成分800
11.2.2.1 金属材料801
11.2.2 熔炼用材料801
11.2.2.2 辅助材料802
11.2.3 熔炼设备与工具805
11.2.3.1 熔炼用炉805
11.2.3.2 坩埚与工具805
11.2.4 熔炼前的准备807
11.2.4.1 铸造镁合金配料807
11.2.4.2 炉料及熔炼用辅助材料的准备808
11.2.4.3 设备、坩埚与工具的准备808
11.2.5.1 铸造镁合金的变质处理809
11.2.5 铸造镁合金的变质和精炼处理809
11.2.5.2 铸造镁合金的精炼处理810
11.2.6 铸造镁合金的熔炼811
11.2.6.1 含锆镁合金的熔炼工艺811
11.2.6.2 含铝镁合金的熔炼工艺811
11.2.7 铸造镁合金的浇注工艺812
11.2.7.1 用浇包舀取金属液的浇注工艺812
11.2.7.2 带挡板坩埚的浇注工艺812
11.2.8.1 含锆镁合金813
11.2.8 镁合金熔炼质量的控制813
11.2.8.2 含铝镁合金814
11.2.8.3 镁合金精炼质量的控制815
11.2.9 铸造镁合金熔炼技术的新发展815
11.2.10 镁合金熔炼浇注安全技术815
11.3 铸造铜合金的熔炼和浇注816
11.3.1 铸造铜合金的类别、牌号和化学成分817
11.3.2.1 金属材料818
11.3.2 熔炼用材料818
11.3.2.2 主要辅助材料819
11.3.3 熔炼设备与工具819
11.3.3.1 坩埚炉820
11.3.3.2 感应电炉820
11.3.3.3 熔炼铜合金用的主要工具821
11.3.4 熔炼前的准备823
11.3.4.1 熔炼前准备工作要点823
11.3.4.2 配料计算826
11.3.5 铸造铜合金熔炼工艺827
11.3.5.1 铜合金熔炼的一般原则827
11.3.5.2 典型铸造铜合金熔炼工艺827
11.3.6 铸造铜合金的脱氧与除气828
11.3.6.1 常用的脱氧方法828
11.3.6.2 磷铜脱氧工艺要点828
11.3.7.1 合金成分的控制829
11.3.7 合金熔炼质量控制829
11.3.6.3 常用的几种除气方法829
11.3.7.2 含气量检查830
11.3.7.3 弯曲及断口检查830
11.3.8 铸造铜合金浇注工艺特点831
第12章 铸钢和铸造高温合金的熔炼833
与浇注833
12.1 铸钢的熔炼与浇注833
12.1.1 铸钢熔炼用原材料及工艺材料835
12.1.1.1 原材料835
12.1.1.2 工艺材料836
12.1.2 感应炉熔炼与浇注838
12.1.2.1 感应炉技术特性838
12.1.2.2 筑炉工艺839
12.1.2.3 熔剂和脱氧剂841
12.1.2.4 中频感应炉熔炼842
12.1.2.5 高频翻转炉熔炼847
12.1.2.6 铸钢的浇注848
12.1.3.1 电渣炉技术特性850
12.1.3 有衬电渣炉熔炼与浇注850
12.1.3.2 筑炉工艺851
12.1.3.3 电渣的配制852
12.1.3.4 电渣重熔对钢中夹杂物和气体的影响853
12.1.3.5 电渣重熔测温装置853
12.1.3.6 电渣重熔和浇注854
12.1.4.2 电弧炉技术特性855
12.1.4.3 筑炉工艺855
12.1.4.1 碱性电弧炉炼钢方法与特点855
12.1.4 电弧炉熔炼与浇注855
12.1.4.4 铸钢配料计算856
12.1.4.5 碱性电弧炉炼钢858
12.1.4.6 铸钢的浇注861
12.1.4.7 电弧炉熔炼过程中的故障863
排除863
12.2 铸造高温合金的熔炼与浇注863
12.2.1.1 合金中元素的蒸发864
12.2.1 铸造高温合金的熔炼特点864
12.2.1.2 合金中气体的逸出867
12.2.1.3 合金中氮化物的分解868
12.2.1.4 合金的脱氧和氧化物的还原869
12.2.1.5 坩埚反应871
12.2.2 真空感应熔炼炉及装置873
12.2.2.1 真空感应熔炼炉873
12.2.2.2 真空感应熔炼炉测量装置879
12.2.3 筑炉、熔炼及浇注用材料882
12.2.3.1 筑炉用材料882
12.2.3.2 熔炼用材料884
12.2.3.3 浇注用材料887
12.2.4 铸造高温合金母合金的熔炼与浇注888
12.2.4.1 筑炉工艺888
12.2.4.2 炉料准备及配料计算890
12.2.4.3 铸造高温合金母合金的熔炼892
12.2.4.4 铸造高温合金母合金的浇注895
12.2.5.1 坩埚准备896
12.2.5 铸造高温合金母合金重熔和浇注铸件896
12.2.5.2 重熔母合金和浇注铸件898
12.2.6 真空感应熔炼过程中的故障及其排除900
第13章 铸件热处理901
13.1 概述901
13.2 热处理设备选择901
13.2.1 热处理炉类型及适应范围901
13.2.2.1 常用温度检测仪表902
13.2.2 测温仪表类型及适用范围902
13.2.2.2 常用测温二次仪表904
13.3 有色合金铸件热处理905
13.3.1 铝合金铸件热处理905
13.3.1.1 铸造铝合金的牌号905
13.3.1.2 铝合金铸件热处理规范905
13.3.1.3 铸造铝合金的力学性能907
13.3.2.2 镁合金铸件热处理规范908
13.3.2.1 铸造镁合金的牌号908
13.3.2 镁合金铸件热处理908
13.3.2.3 铸造镁合金的力学性能909
13.3.3 铜合金铸件热处理909
13.3.3.1 铸造铜合金的类别909
13.3.3.2 铜合金铸件热处理规范910
13.4 钢铸件热处理910
13.4.1 结构钢铸件热处理910
13.4.1.1 碳钢铸件热处理910
13.4.1.2 低合金钢铸件热处理911
13.4.2 不锈钢与耐热钢铸件热处理912
13.4.2.1 不锈耐酸钢铸件热处理912
13.4.2.2 热强不锈钢铸件热处理913
13.4.2.3 耐热钢铸件热处理913
13.5 高温合金铸件热处理914
14.2 铸件清理916
14.2.1.1 脱型916
14.2.1 脱型与脱芯916
14.1 概述916
第14章 铸件的清理、修补与精整916
14.2.1.2 陶瓷型芯脱除920
14.2.2 喷丸与抛丸清理920
14.2.2.1 喷丸与喷砂920
14.2.2.2 抛丸清理925
14.2.3 切割浇冒口926
14.2.3.1 切割方法926
14.2.3.2 常用切割机械927
14.2.4 清刺与粗加工929
14.2.4.1 铸件清刺工艺方法929
14.2.4.2 铸件清刺常用工具929
14.3 铸件修补932
14.3.1 铸件补焊932
14.3.1.1 铸件上允许补焊缺陷的确定932
14.3.1.2 铸件补焊用设备933
14.3.1.3 铸件补焊用填充材料933
14.3.1.4 焊区处理935
14.3.1.5 铸件补焊工艺要点936
14.3.1.6 铸件补焊后的清理及热处理938
14.3.1.7 铸件补焊后的检验939
14.3.2 铸件的浸渗处理939
14.3.2.1 浸渗剂940
14.3.2.2 浸渗方法与设备940
14.3.2.3 浸渗工艺941
14.4 铸件精整942
14.4.1 铸件整形与修饰942
14.4.1.1 铸件修整942
14.4.1.2 铸件光饰处理943
14.4.1.3 铸件修整工艺举例944
14.4.2.2 矫正后检验947
14.4.3 液体喷砂947
14.4.3.1 工作原理与工艺特点947
14.4.2 铸件矫正947
14.4.2.1 矫正工艺方法947
14.4.3.2 液体喷砂机948
14.4.3.3 液体喷砂工艺949
14.4.4 铸件喷丸处理949
14.4.4.1 喷丸设备949
14.4.4.2 弹丸950
14.4.4.3 喷丸处理950
14.5.1 热等静压处理的意义和效果951
14.5 铸件热等静压(HIP)处理951
14.5.2 热等静压设备953
14.5.3 铸件热等静压处理工艺955
14.5.4 热等静压铸件的后处理和检验957
14.6 镁合金铸件化学氧化处理957
14.6.1 镁合金铸件化学氧化处理工艺957
14.6.1.1 氧化处理的工艺流程957
14.6.1.2 氧化处理溶液及处理规范958
14.6.2.1 检验与质量要求959
14.6.2.2 质量控制要点959
14.6.1.3 化学氧化溶液的配制959
14.6.2 氧化处理后的检验与质量控制959
14.6.3 常见缺陷的排除和膜层返修960
14.6.3.1 化学氧化处理常见缺陷及其防止方法960
14.6.3.2 膜层返修960
14.7 铸件防锈960
第15章 铸件质量检验963
15.1 概述963
15.1.1 铸件质量检验的意义963
15.1.2 铸件质量检验项目963
15.2 铸件化学成分分析966
15.2.1 航空铸件化学成分分析的特点966
15.2.2 化学分析方法966
15.2.2.1 化学分析方法的特点966
15.2.3 光谱分析法967
15.2.3.1 光谱分析法的特点967
15.2.3.2 光谱分析试样的取样967
15.2.2.2 化学分析试样的取样967
15.2.2.3 航空铸件常用的化学分析方法967
15.2.3.3 摄谱法和光电光谱法968
15.2.4 其他分析法968
15.2.4.1 原子吸收光谱分析968
15.3 铸件力学性能检验969
15.3.2.1 铸造铝合金试样969
15.3.2 各种铸造合金的力学性能试样969
15.3.1 力学性能检验项目969
15.2.4.4 X射线光谱分析969
15.2.4.3 气相色谱分析969
15.2.4.2 高速分析969
15.3.2.2 铸造镁合金试样971
15.3.2.3 铸造铜合金试样972
15.3.2.4 铸造不锈钢及耐热钢试样973
15.3.2.5 铸造结构钢试样974
15.3.2.6 铸造高温合金试样975
15.3.3 拉伸试验976
15.3.4 硬度试验976
15.3.5 冲击试验977
15.3.4.1 布氏硬度试验规范977
15.3.4.2 洛氏硬度试验规范977
15.3.6 蠕变及持久性能试验978
15.3.7 疲劳试验978
15.4 合金的物理化学性能检测979
15.4.1 合金的物理性能检测979
15.4.2 合金的化学性能检测979
15.4.2.1 钢及高温合金抗氧化性的检测979
15.4.2.2 不锈钢晶间腐蚀倾向的检测979
15.5.1 铸件金相检查的分类980
15.4.2.3 金属及其合金腐蚀的鉴别980
15.5 铸件的金相检查980
15.5.2 铸件低倍组织的检查981
15.5.2.1 高温合金铸件晶粒度的检查与评级981
15.5.2.2 铝合金铸件针孔的检查981
15.5.3 高温合金铸件显微疏松的检查983
15.5.4 铸件的表面组织检查985
15.5.4.1 铸件脱碳层的测定985
15.5.5 铸件非金属夹杂物的鉴别986
15.5.4.2 铸件渗碳层深度的测定986
15.5.4.3 铸件合金贫化层的测定986
15.6 铸件几何尺寸检测987
15.6.1 铸件尺寸精度检验987
15.6.1.1 铸件尺寸公差987
15.6.1.2 批生产铸件的尺寸公差等级989
15.6.1.3 单件生产铸件的尺寸公差等级989
15.6.1.4 铸件的铸造斜度990
15.6.1.5 铸件的加工余量990
15.6.1.6 通用量具选择原则990
15.6.1.7 通用量具的选择990
15.6.2 形状和位置公差及检测992
15.6.3 铸件多尺寸的测量992
15.6.4 叶片型面的检测993
15.6.4.1 叶片叶型检测的基本参数993
15.6.4.2 叶片型面的检测994
15.6.6.1 铸件表面粗糙度的评定参数及其数值系列996
15.6.5 叶片壁厚的检测996
15.6.6 铸件表面粗糙度检测996
15.6.6.2 评定原则及检验方法997
15.7 铸件的无损检测1001
15.7.1 航空铸件常用的无损检测方法1001
15.7.2 X射线检验1002
15.7.2.1 检验程序及其要求1002
15.7.2.2 铸件缺陷的判断1004
15.7.3 渗透检验1004
15.7.3.1 荧光渗透检验1004
15.7.3.2 着色渗透检验1007
15.7.4 磁粉检验1008
15.7.4.1 磁粉检验的应用和特点1008
15.7.4.2 磁化方法的分类及选择1008
15.7.4.3 磁粉检验工艺1008
15.7.5.1 密封性检验分类和级别1010
15.7.5.2 密封性检验的参数及要求1010
15.7.5 密封性检验1010
15.7.5.3 密封性检验工艺1011
15.8 铸件试制定型1011
15.8.1 试制准备1011
15.8.2 铸件试制1012
15.8.2.1 铸件尺寸定型1012
15.8.2.2 铸件冶金定型1012
15.8.3 铸件定型1014
对照1015
附录1015
附录A 中外铸造合金牌号和标准1015
附录B 常用国际单位及其换算1023
系数1023
附录C 常用铸造标准目录1025
附录D 铸造合金原材料标准1027
附录E 铸造常用工艺原材料1043
标准1043
1994《航空制造工程手册 特种铸造》由于是年代较久的资料都绝版了,几乎不可能购买到实物。如果大家为了学习确实需要,可向博主求助其电子版PDF文件(由《航空制造工程手册》总编委会主编 1994 北京:航空工业出版社 出版的版本) 。对合法合规的求助,我会当即受理并将下载地址发送给你。
高度相关资料
-
- 航空制造工程手册 飞机钣金工艺
- 1992 北京:航空工业出版社
-
- 特种铸造手册 (下册)
- 1978
-
- 铸造工程师手册
- 1997 北京:机械工业出版社
-
- 特种铸造手册 上
- 1976 北京:机械工业出版社
-
- 特种铸造手册 下
- 1978 北京:机械工业出版社
-
- 特种铸造工艺
- 1984 北京:国防工业出版社
-
- 铸造手册 第6卷 特种铸造
- 1994 北京:机械工业出版社
-
- 特种塑性成形
- 1995 北京:机械工业出版社
-
- 航空制造工程手册 通用基础
- 1993 北京:航空工业出版社
-
- 航空制造工程手册 电连接器工艺
- 1996 北京:航空工业出版社
-
- 航空制造工程手册 框架壳体工艺
- 1997 北京:航空工业出版社
-
- 航空制造工程手册:特种加工
- 1993 北京:航空工业出版社
-
- 航空制造工程手册:飞机机械加工
- 1995 北京:航空工业出版社
-
- 航空制造工程手册 救生装备工艺
- 1995 北京:航空工业出版社
-
- 航空制造工程手册 飞机装配
- 1993 北京:航空工业出版社
提示:百度云已更名为百度网盘(百度盘),天翼云盘、微盘下载地址……暂未提供。➥ PDF文字可复制化或转WORD