《航空制造工程手册 齿轮工艺》
作者 | 《航空制造工程手册》总编委会主编 编者 |
---|---|
出版 | 北京:航空工业出版社 |
参考页数 | 815 |
出版时间 | 1995(求助前请核对) 目录预览 |
ISBN号 | 7800466566 — 求助条款 |
PDF编号 | 82358248(仅供预览,未存储实际文件) |
求助格式 | 扫描PDF(若分多册发行,每次仅能受理1册) |
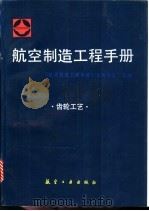
第1章航空齿轮结构及工艺特点1
1.1 齿轮制造技术的发展1
1.2 航空齿轮的分类6
1.2.1 航空齿轮的类型6
1.2.2 航空齿轮的精度等级6
1.2.3 航空齿轮材料概况7
1.3 航空齿轮的结构特点7
1.4 航空齿轮的工艺特点16
2.1.1 各国常用齿形标准17
2.1 外啮合圆柱齿轮传动17
第2章齿轮传动几何计算17
2.1.2 外啮合直齿圆柱齿轮传动的几何尺寸计算(中心距给定时)18
2.1.3 外啮合斜齿(人字齿)圆柱齿轮传动的几何尺寸计算20
2.1.4 外啮合齿轮变位系数的限制条件23
2.2 内啮合圆柱齿轮传动24
2.2.1 内啮合直齿圆柱齿轮传动的几何尺寸计算(中心距给定时)24
2.2.2 内啮合斜齿(人字齿)圆柱齿轮传动的几何尺寸计算26
2.2.3 内啮合齿轮变位系数的限制条件28
2.3.1 交错轴斜齿圆柱齿轮传动的啮合原理30
2.3.1.1 公共齿条与斜齿轮传动的啮合30
2.3 交错轴斜齿圆柱齿轮传动30
2.3.1.2 交错轴斜齿圆柱齿轮传动的特点31
2.3.1.3 正常啮合的条件31
2.3.2 交错轴斜齿圆柱齿轮传动的几何尺寸计算31
2.3.2.1 非变位交错轴斜齿圆柱齿轮传动的几何尺寸计算(中心距给定时)31
2.3.2.2 变位交错轴斜齿圆柱齿轮传动的几何尺寸计算32
2.3.3 交错轴斜齿圆柱齿轮传动的干涉35
2.4 齿轮与齿条传动35
2.4.1 齿轮与齿条传动的几何尺寸计算35
2.4.2 齿轮与齿条传动的限制条件36
2.5.1 直齿锥齿轮传动的几何尺寸计算38
2.5 直齿锥齿轮传动38
2.5.2 直齿锥齿轮的变位41
2.5.2.1 切向变位41
2.5.2.2 高变位43
2.5.2.3 角变位45
2.6 圆柱蜗杆传动45
2.6.1 圆柱蜗杆传动的类型45
2.6.2 蜗杆传动参数的选择46
2.6.2.1 模数46
2.6.2.3 蜗杆头数z1和蜗轮齿数z247
2.6.3 圆柱蜗杆传动的几何尺寸计算47
2.6.2.2 导程角47
2.7 齿轮传动几何计算的计算机程序49
2.7.1 外啮合直齿及斜齿(人字齿)圆柱齿轮几何尺寸计算的计算机程序49
2.7.1.1 数学模型49
2.7.1.2 程序使用范围49
2.7.1.3 程序框图49
2.7.1.4 源程序50
2.7.1.5 符号说明54
2.7.1.6 程序运行及结果55
2.7.2.2 程序使用范围57
2.7.2.3 程序框图57
2.7.2 直齿锥齿轮几何计算的计算机程序57
2.7.2.1 数学模型57
2.7.2.4 源程序58
2.7.2.5 符号说明61
2.7.2.6 程序运行及结果61
第3章航空齿轮常用材料及热处理64
3.1 常用航空齿轮材料64
3.1.1 国内常用航空齿轮钢64
3.1.2 国内常用航空齿轮有色金属68
3.1.3.1 美国(AISI SAE)70
3.1.3 国外常用齿轮钢70
3.1.3.2 前苏联(ГOCT)73
3.1.3.3 日本(ЛS)74
3.1.3.4 英国(BS)76
3.1.3.5 德国(DIN)76
3.1.3.6 法国(NF)78
3.1.4 国内外常用齿轮钢号对照78
3.2 航空齿轮的热处理要求79
3.2.1 钢的热处理方式代号表示方法79
3.2.2 渗碳齿轮的热处理要求80
3.2.5 航空仪表齿轮钢的热处理要求81
3.2.3 氮化齿轮的热处理要求81
3.2.4 氰化齿轮的热处理要求81
3.2.6 航空仪表齿轮用有色金属的热处理要求82
3.3 常用齿轮钢的预备热处理83
3.3.1 齿轮钢材与热处理的关系83
3.3.1.1 合金元素在钢中的作用83
3.3.1.2 齿轮钢材的热处理特性84
3.3.2 预备热处理的目的、方法及应用85
3.3.2.1 退火和正火的目的85
3.3.2.2 退火和正火的方法及应用85
3.4.1 淬火86
3.4 常用齿轮钢的最终热处理86
3.3.2.3 退火和正火的选择86
3.4.2 回火88
3.4.3 冷处理88
3.4.4 人工时效89
3.5 常用齿轮钢的化学热处理89
3.5.1 渗碳89
3.5.2 渗氮(氮化)90
3.5.3 碳氮共渗(氰化)91
3.5.4 非化学热处理表面的防护措施92
3.5.4.1 非渗碳表面的防护92
3.6 航空仪表齿轮的热处理94
3.5.4.2 非渗氮(氮化)表面的防护94
3.5.4.3 非碳氮共渗(氰化)表面的防护94
3.6.1 不锈钢的热处理95
3.6.1.1 奥氏体不锈钢的热处理95
3.6.1.2 马氏体不锈钢的热处理95
3.6.2 有色金属的热处理95
3.6.2.1 铝合金的热处理95
3.6.2.2 铜合金的热处理96
3.7 热处理工序在工艺规程中的位置97
3.8.1.1 热处理零件检验类别98
3.8.1 齿轮热处理的检验98
3.8 齿轮热处理的检验及质量控制98
3.8.1.2 硬度检验99
3.8.2 齿轮热处理常见缺陷及预防补救措施102
3.9 航空齿轮新材料及热处理105
3.9.1 新材料的特点及技术要求105
3.9.1.1 新材料的特点105
3.9.1.2 新材料的技术要求105
3.9.2 热处理新技术108
3.9.2.1 国外热处理新技术发展概况108
3.9.2.3 国外热处理近况109
3.9.2.2 我国齿轮热处理近况109
3.9.2.4 国外齿轮热处理工序在工艺规程中位置的安排110
3.9.2.5 近代热处理控制111
第4章圆柱齿轮加工工艺及设备113
4.1 滚齿113
4.1.1 滚齿工艺113
4.1.1.1 滚齿前的准备113
4.1.1.2 切削用量的选用118
4.1.1.3 切齿高度差Δh的确定119
4.1.1.4 短齿齿轮的滚切119
4.1.1.6 磨齿前滚齿120
4.1.1.5 精滚齿轮120
4.1.2 滚齿机床121
4.1.2.1 各类滚齿机的特点与适用范围121
4.1.2.2 国产中型滚齿机型号及技术规格121
4.1.2.3 几种国外滚齿机型号及技术规格123
4.1.3 滚齿缺陷产生原因及消除方法123
4.1.4 提高滚齿生产率的途径126
4.2 插齿129
4.2.1 插齿工艺129
4.2.1.1 插齿前的准备129
4.2.1.2 剃前插齿131
4.2.1.3 插制斜齿轮132
4.2.1.4 内齿轮插齿加工133
4.2.2 插齿机床133
4.2.2.1 国内外主要插齿机型号及部分性能数据134
4.2.2.2 德国LORENZ公司MCS40和MCS60型插齿机137
4.2.3 插齿缺陷产生的原因及消除方法138
4.2.4 提高插齿生产率的途径139
4.3 剃齿139
4.3.1 剃齿工艺140
4.3.1.1 剃齿的工作原理140
4.3.1.2 剃齿的分类142
4.3.1.3 剃齿工艺的加工精度与表面粗糙度的分析144
4.3.1.4 内齿轮的剃齿146
4.3.1.5 双联齿轮或带凸台齿轮的剃齿146
4.3.1.6 径向切入剃齿法148
4.3.1.7 鼓形齿齿轮的剃齿150
4.3.1.8 小锥度齿齿轮的剃齿151
4.3.1.9 剃齿机的调整152
4.3.1.10 剃齿的切削用量154
4.3.2 剃齿机床157
4.3.3 保证剃齿精度的措施159
4.4.1.1 珩齿的工作原理161
4.4 珩齿161
4.4.1 珩齿工艺161
4.4.1.2 珩齿方法的分类162
4.4.1.3 珩齿的切削用量及条件163
4.4.1.4 珩齿的精度分析165
4.4.1.5 珩磨轮的制造166
4.4.1.6 珩磨轮的修整170
4.4.2 珩齿机床170
4.4.3 珩齿误差的原因及克服误差的措施171
4.5.1.1 梳齿的工作原理与特点173
4.5.1 梳齿工艺173
4.5 梳齿173
4.5.1.2 梳齿机的调整(马格型梳齿机)175
4.5.1.3 梳齿的切削用量179
4.5.2 梳齿机床185
4.6 研齿186
4.7 磨齿187
4.7.1 磨齿工艺187
4.7.1.1 磨齿法的分类及特点187
4.7.1.2 磨齿砂轮的选择188
4.7.1.3 磨齿的切削用量198
4.7.1.4 磨齿机床的调整200
4.7.2 齿面修形齿的磨齿204
4.7.2.1 齿面修形齿的分类204
4.7.2.2 马格型磨齿机的修形机构205
4.7.2.3 雷斯豪尔型磨齿机的修形磨齿210
4.7.2.4 红环磨齿机的修形磨齿212
4.7.2.5 S10型和GG24型磨齿机的修形磨齿212
4.7.3 磨齿机床213
4.7.3.1 马格型磨齿机213
4.7.3.2 雷斯豪尔磨齿机216
4.7.3.3 红环磨齿机224
4.7.3.4 S10型磨齿机227
4.7.3.5 GG24型成形磨齿机228
4.7.4 砂轮修整器228
4.7.4.1 砂轮的修整228
4.7.4.2 砂轮修整方法的分类229
4.7.4.3 砂轮修整工具229
4.7.4.4 砂轮的修整用量232
4.7.4.5 马格磨齿机砂轮修整器233
4.7.4.6 雷斯豪尔磨齿机的砂轮修整器235
4.7.4.7 红环磨齿机的砂轮修整器244
4.7.4.8 S10成形磨齿机砂轮修整器258
4.7.4.9 GG24型磨齿机砂轮修整器262
4.7.5 磨削烧伤的检查与防止270
4.7.5.1 磨削烧伤的检验程序270
4.7.5.2 磨削烧伤的技术标准270
4.7.5.3 磨削烧伤的原因与防止271
4.7.6 磨齿余量272
4.7.6.1 磨齿余量的形式272
4.7.7 磨齿误差的原因及排除措施273
4.7.7.1 马格磨齿机的误差原因及排除措施273
4.7.6.2 磨齿余量的选择273
4.7.7.2 NZA型磨齿机的误差原因及排除措施276
4.7.7.3 红环SGK24型成形磨齿机的误差原因及排除措施277
4.8 圆柱蜗杆副加工278
4.8.1 圆柱蜗杆加工279
4.8.1.1 圆柱蜗杆分类及其齿形成形方法279
4.8.1.2 圆柱蜗杆轮齿的加工282
4.8.2 蜗轮加工283
4.8.2.1 蜗轮加工的特点283
4.8.2.3 蜗轮的滚齿284
4.8.2.2 蜗轮滚刀和蜗轮毛坯的安装284
4.8.2.4 飞刀加工蜗轮285
4.8.3 蜗杆副接触斑点分析285
4.9 轮齿的光整加工288
4.9.1 振动光饰288
4.9.2 毡轮抛光289
4.9.2.1 抛光的工作过程289
4.9.4.2 圆片铣刀去毛刺290
4.9.4 刀具去毛刺290
4.9.4.1 车刀去毛刺290
4.9.2.2 抛光剂290
4.9.3 机械刷去毛刺290
4.9.4.3 蜗杆形刀具去毛刺291
4.9.5 蜗杆形导电磨轮去毛刺291
4.9.6 砂轮磨削法去毛刺292
4.9.6.1 手工操作法292
4.9.6.2 齿轮倒角机去毛刺293
4.9.7 化学法去毛刺293
4.9.8 热能法去毛刺295
4.9.9 电解加工去毛刺295
4.9.10.1 工作原理与设备296
4.9.10 阿布哈勒(Abral)抛光296
4.9.10.2 零件的抛光工艺298
第5章锥齿轮加工工艺及设备300
5.1 锥齿轮加工原理及工艺特点300
5.1.1 加工原理300
5.1.1.1 平面产形轮原理300
5.1.1.2 平顶产形轮原理301
5.1.2 锥齿轮切齿工艺特点302
5.2 直齿锥齿轮加工工艺及设备302
5.2.1 直齿锥齿轮加工工艺302
5.3.1 弧齿锥齿轮铣齿加工工艺304
5.3.1.1 铣齿方法及其适用范围304
5.2.2 直齿锥齿轮切齿机床304
5.3 弧齿锥齿轮铣齿加工工艺及设备304
5.3.2 弧齿锥齿轮切齿加工设备305
5.3.2.1 常见弧齿锥齿轮铣齿机床规格范围305
5.3.2.2 铣齿机的基本结构和调整环节306
5.3.2.3 常见铣齿机的传动系统307
5.3.2.4 变性机构307
5.3.2.5 刀倾机构307
5.3.2.6 螺旋运动机构310
5.4.1 弧齿锥齿轮磨齿加工工艺313
5.3.2.7 铣齿机具有的特性机构一览表313
5.4 弧齿锥齿轮磨齿加工工艺及设备313
5.4.2 弧齿锥齿轮磨齿加工设备314
5.4.2.1 常见弧齿锥齿轮磨齿机床规格范围314
5.4.2.2 常见磨齿机的传动系统314
5.4.2.3 磨齿机上的展成凸轮315
5.4.2.4 砂轮修整器319
5.5 弧齿锥齿轮切齿计算320
5.5.1 已知条件320
5.5.1.1 轮齿参数及几何尺寸320
5.5.1.2 刀盘直径及刀号的选择324
5.5.1.3 切齿方法及机床的选择330
5.5.2 弧齿锥齿轮切齿计算331
5.5.2.1 SB计算卡331
5.5.2.2 SGM计算卡339
5.5.2.3 LCD计算卡355
5.5.2.4 ZGDS计算卡357
5.5.3 小轮控制参数的选取361
5.5.4 齿面接触分析(TCA)362
5.5.4.1 已知条件362
5.5.4.2 TCA数学模型364
5.5.4.4 TCA结果的判断366
5.5.4.3 TCA的输出结果366
5.5.5 小轮齿面的根切检查(UC)369
5.5.6 常用的辅助计算369
5.5.6.1 机床变换369
5.5.6.2 螺旋角旋向变换369
5.5.6.3 刀倾刀转角的修正计算369
5.5.6.4 按铣齿卡计算磨齿卡371
5.5.7 格里森电算程序简介372
5.5.7.1 常用的程序情况372
5.5.8 格里森切齿计算卡项目名词解释373
5.5.8.1 刀具部分373
5.5.7.2 程序结构373
5.5.8.2 机床部分374
5.5.8.3 轮齿接触部分376
5.5.8.4 啮合理论计算部分377
5.5.8.5 切齿计算部分378
5.6 弧齿锥齿轮机床调整及夹具安装380
5.6.1 铣齿机调整380
5.6.1.1 机床调整数据380
5.6.1.2 床鞍的调整380
5.6.1.7 滚比挂轮调整381
5.6.1.10 变性机构的调整381
5.6.1.9 刀倾、刀转角调整381
5.6.1.8 分齿挂轮调整381
5.6.1.4 偏心角、摇台角的调整381
5.6.1.6 垂直轮位调整381
5.6.1.5 水平轮位调整381
5.6.1.3 机床安装角的调整381
5.6.1.11 螺旋运动机构的调整382
5.6.2 磨齿机床的调整382
5.6.2.1 展成凸轮的调整382
5.6.2.3 端面修正器的调整383
5.6.2.4 分齿挂轮的调整383
5.6.2.2 侧面修正器的调整383
5.6.3 切齿夹具及其安装388
5.7 弧齿锥齿轮的切齿刀具393
5.7.1 铣刀盘的规格和种类393
5.7.1.1 铣刀盘的规格393
5.7.1.2 铣刀盘的种类394
5.7.2 铣刀盘的结构394
5.7.2.1 小直径铣刀盘的结构394
5.7.2.2 双面铣刀盘的结构394
5.7.2.3 单面铣刀盘的结构396
5.7.2.4 新型结构铣刀盘396
5.7.2.5 铣刀盘的构成要素401
5.7.3 圆拉刀盘406
5.7.4 铣刀盘的刃磨及检验407
5.7.4.1 铣刀盘的刃磨407
5.7.4.2 铣刀盘的检验409
5.7.4.3 铣刀盘的技术条件409
5.8 弧齿锥齿轮轮齿加工精度及误差分析409
5.8.1 弧齿锥齿轮加工精度409
5.8.2 切齿时常见的误差分析409
5.8.2.1 齿圈跳动409
5.8.3.1 影响齿面粗糙度的因素410
5.8.3 磨齿可能产生的各种误差及消除方法410
5.8.2.4 接触硬棱410
5.8.2.3 齿面粗糙度410
5.8.2.2 齿距误差410
5.8.3.2 产生齿距误差的原因411
5.8.3.3 齿圈跳动412
5.8.3.4 轮齿尺寸不稳定412
5.8.3.5 磨齿产生的金相缺陷412
第6章特种齿轮刀具414
6.1 特种滚齿刀具414
6.1.1 摆线油泵齿轮滚刀414
6.1.1.1 摆线油泵转子齿形的形成及其数学模型414
6.1.1.2 摆线的等效形成关系415
6.1.1.3 转子滚刀的形面设计416
6.1.2 全切式小模数齿轮滚刀420
6.1.2.1 全切式小模数齿轮滚刀的类型和尺寸421
6.1.2.2 全切式小模数齿轮滚刀的材料422
6.1.2.3 全切式小模数齿轮滚刀的技术要求422
6.1.3 小模数直齿端面齿轮滚刀425
6.1.3.1 端面齿轮滚刀工作原理425
6.1.3.2 端面齿轮滚刀的设计425
6.1.4 小模数直齿锥齿轮滚刀425
6.1.4.2 锥齿轮滚刀的设计计算426
6.1.4.1 锥齿轮滚刀加工原理426
6.1.5 成形定装滚刀431
6.1.5.1 成形定装滚刀工作原理432
6.1.5.2 成形定装滚刀的设计计算432
6.2 特种剃齿刀435
6.2.1 内齿轮用剃齿刀435
6.2.2 径向剃齿刀437
6.2.2.1 径向剃齿刀齿面分析438
6.2.2.2 径向剃齿刀设计计算的框图445
6.2.2.3 径向剃齿刀设计计算举例445
6.2.2.4 径向剃齿刀的容屑槽排列450
6.2.2.5 径向剃齿刀的齿面磨削451
6.2.3 平衡剃齿法剃齿刀451
6.2.3.1 平衡剃齿法的原理和条件451
6.2.3.2 平衡剃齿啮合角的计算452
6.2.3.3 平衡剃齿法剃齿刀设计453
6.3 摆线油泵齿轮插齿刀456
第7章齿轮夹具461
7.1 滚插齿夹具461
7.1.1 滚插齿夹具的类型461
7.1.2 滚插齿夹具中的弹性筒夹定位元件472
7.1.3 滚插齿夹具中的胀开式薄壁衬套473
7.2 剃齿夹具474
7.3 磨齿夹具476
7.4 以工件齿形定位精磨基准孔的夹具479
7.4.1 锁紧环式夹具479
7.4.1.1 夹具的结构479
7.4.1.2 夹具主要元件的设计479
7.4.2 以滚珠或滚柱定心的夹具481
8.1.1 齿轮综合误差的测量482
8.1.1.1 单面啮合综合测量482
8.1 圆柱齿轮的测量482
第8章齿轮测量482
8.1.1.2 双面啮合综合测量490
8.1.1.3 接触区检验494
8.1.2 单项测量496
8.1.2.1 齿距偏差(Δfpt)及齿距累积误差(ΔFp)的测量496
8.1.2.2 齿圈径向跳动(ΔFr)的测量500
8.1.2.3 齿形误差(Δff)的测量502
8.1.2.4 基节偏差(Δfpb)的测量508
8.1.2.5 齿向误差(ΔFβ)的测量510
8.1.2.6 齿厚测量512
8.2.1.1 齿坯精度要求517
8.2.1 齿坯检验517
8.2 锥齿轮检验517
8.2.1.2 齿坯尺寸和公差的表示方法518
8.2.1.3 齿坯检测方法519
8.2.2 单项轮齿要素的检验520
8.2.2.1 齿距偏差的测量520
8.2.2.2 齿圈跳动的测量520
8.2.2.3 齿厚与侧隙的测量521
8.2.3.2 数据处理522
8.2.4 接触区检验522
8.2.3.1 测量方法522
8.2.3 综合检验522
8.2.4.1 齿轮副对接触区的一般要求523
8.2.4.2 不理想的接触区524
8.2.4.3 接触区检验设备525
8.2.4.4 接触区检验方法526
8.2.5 V-H检验法528
8.2.6 测量齿轮529
8.2.6.1 测量齿轮的作用529
8.2.6.2 测量齿轮的种类与传递关系530
8.2.6.3 测量齿轮的设计与制造530
8.2.7 锥齿轮标印531
8.2.6.4 测量齿轮的标印与定检531
8.3 三坐标机用于齿轮检验532
8.3.1 三坐标测量机的工作原理532
8.3.2 用三坐标机测量齿轮533
8.3.2.1 柱形齿轮的测量534
8.3.2.2 锥齿轮的测量538
8.4 蜗杆副检验540
8.4.1 蜗杆的检验540
8.4.1.1 蜗杆螺旋线误差ΔfhL的检验540
8.4.1.3 蜗杆齿形误差Δfr1的检验541
8.4.1.2 蜗杆轴向齿距偏差Δfpx的检验541
8.4.1.4 蜗杆量柱测量距M的测量542
8.4.2 蜗轮的检验551
8.4.2.1 蜗轮切向综合误差的检验551
8.4.2.2 蜗轮径向综合误差的检验551
8.4.2.3 蜗轮齿距偏差、齿距累积误差、齿形误差和齿圈径向跳动的检验552
8.4.2.4 蜗轮齿厚偏差的测量552
8.5 花键检验552
8.5.1 渐开线直齿花键检验552
8.6 齿轮常见缺陷的分析与预防553
8.5.2 矩形花键553
8.5.1.2 综合检验553
8.5.1.1 单项检验553
8.7 齿轮的硬度检验559
8.7.1 时代里氏硬度测试仪HL-D559
8.7.1.1 里氏硬度测试原理与方法559
8.7.1.2 HL-D里氏硬度测试仪的主要参数和功能560
8.7.1.3 测试范围560
8.7.1.4 测试前的准备560
8.7.2 HRC-8型洛氏硬度计560
8.7.2.3 HRC-8型洛氏硬度计的结构与操作561
8.7.2.2 HRC-8型洛氏硬度计的主要技术参数561
8.7.2.1 齿面洛氏硬度测试原理与方法561
8.8 齿轮的表面粗糙度检验563
第9章航空主机齿轮典型零件加工565
9.1 航空主机齿轮工艺特点及工艺过程565
9.1.1 航空主机齿轮工艺特点565
9.1.2 航空主机齿轮加工工艺过程566
9.2 行星齿轮567
9.2.1 行星齿轮典型零件图样及技术要求567
9.2.2 行星齿轮典型零件的工艺路线567
9.3 主动齿轮570
9.3.1 主动齿轮典型零件图样及技术要求570
9.2.3 行星齿轮典型零件的工艺分析570
9.3.2 主动齿轮典型零件的工艺路线572
9.3.3 主动齿轮典型零件的工艺分析574
9.4 内齿圈575
9.4.1 内齿圈典型零件图样及技术要求575
9.4.2 内齿圈典型零件的工艺路线575
9.4.3 内齿圈典型零件的工艺分析577
9.5 带轴齿轮577
9.5.1 带轴齿轮典型零件图样及技术要求580
9.5.2 带轴齿轮典型零件的工艺路线580
9.6.1 整体式双联齿轮583
9.6.1.1 整体式双联齿轮典型零件图样及技术要求(例一)583
9.5.3 带轴齿轮典型零件的工艺分析583
9.6 双联齿轮(整体式和焊接式)583
9.6.1.2 整体式双联齿轮典型零件的工艺路线585
9.6.1.3 整体式双联齿轮典型零件的工艺分析587
9.6.2 焊接式双联齿轮587
9.6.2.1 对接焊双联齿轮典型零件图样及技术要求(例二)587
9.6.2.2 对接焊双联齿轮典型零件的工艺路线587
9.6.2.3 对接焊双联齿轮典型零件的工艺分析594
9.6.2.4 轴向套焊式双联齿轮典型零件图样及技术要求(例三)594
9.6.2.5 轴向套焊式双联齿轮典型零件的工艺路线595
9.6.2.6 轴向套焊式双联齿轮典型零件的工艺分析596
9.7 弧齿锥齿轮596
9.7.1 结构与工艺特点596
9.7.1.1 结构功能特点596
9.7.1.2 零件精度特点596
9.7.1.3 工艺流程概述596
9.7.2 盘类齿轮598
9.7.2.1 盘类齿轮典型零件图样及技术要求598
9.7.2.2 主要工艺路线及工艺分析598
9.7.3.2 主要工艺路线及工艺分析601
9.7.3.1 轴类锥齿轮典型零件图样及技术要求601
9.7.3 轴类锥齿轮601
9.7.4 双联锥齿轮603
9.7.4.1 双联锥齿轮典型零件图样及技术要求603
9.7.4.2 主要工艺路线及分析603
9.8 圆弧端齿联轴器605
9.8.1 圆弧端齿联轴器的结构特点605
9.8.2 圆弧端齿联轴器加工工艺和工艺分析606
9.8.2.1 加工机床和加工过程606
9.8.2.2 夹具设计的特点607
9.8.2.3 加工圆弧端齿的砂轮607
9.8.2.4 砂轮修形用的金刚石笔608
9.8.2.5 齿形设计和机床调整卡的编制609
9.8.2.6 编制机床调整卡实例616
9.8.3 圆弧端齿联轴器的检验620
9.8.3.1 工作面的着色检验620
9.8.3.2 圆弧端齿中心对某个基准面的同轴度检验620
9.8.3.5 端面弧齿对某个基准孔的角向位置621
9.8.4 检验用标准件的制造621
9.8.4.1 制造标准件的质量控制621
9.8.3.4 尺寸检验621
9.8.3.3 圆弧端齿的节径平面对某个基准端面的平行度检验621
9.8.4.2 标准件的材料623
9.8.4.3 标准件制造的工艺路线与技术要求623
9.8.4.4 标准件的数量和使用规定623
9.9 粉末冶金齿轮623
9.9.1 粉末冶金工艺623
9.9.1.1 粉末的准备623
9.9.1.2 成形624
9.9.1.3 烧结624
9.9.2 粉末冶金齿轮的后处理624
9.9.4 典型零件示例625
9.9.3 质量检验625
9.10 花键联结偶件626
9.10.1 花键轴的加工626
9.10.2 内花键加工626
第10章航空辅机齿轮典型零件加工631
10.1 航空辅机齿轮工艺特点631
10.2 带轴齿轮631
10.2.1 带轴齿轮概述631
10.2.2 带轴齿轮典型零件图样及技术要求632
10.2.3 带轴齿轮主要工艺路线及工艺分析632
10.3.2 带孔齿轮典型零件图样及技术要求635
10.3.3 带孔齿轮主要工艺路线及工艺分析635
10.3 带孔齿轮635
10.3.1 带孔齿轮概述635
10.4 行星齿轮637
10.4.1 行星齿轮概述637
10.4.2 行星齿轮典型零件图样及技术要求637
10.4.3 行星齿轮主要工艺路线及工艺分析638
10.5 内齿轮640
10.5.1 内齿轮概述640
10.5.2 内齿轮典型零件(之一)图样及技术要求641
10.5.3 本内齿轮主要工艺路线及工艺分析642
10.5.4 内齿圈典型零件(之二)图样及技术要求645
10.5.5 炮塔内齿圈主要工艺路线及工艺分析646
10.6 双联齿轮650
10.6.1 双联齿轮概述650
10.6.2 双联齿轮典型零件图样及技术要求650
10.6.3 双联齿轮主要工艺路线及工艺分析651
10.7 花键联结偶件652
10.7.1 花键联结偶件概述652
10.7.2 花键联结偶件典型零件图样及技术要求653
10.7.3 花键联结偶件主要工艺路线及工艺分析653
10.8.1 行星架齿轮概述654
10.8 行星架齿轮654
10.8.2 三轴行星架齿轮典型零件图样及技术要求655
10.8.3 三轴行星架齿轮主要工艺路线及工艺分析655
10.8.4 三孔行星架齿轮典型零件图样及技术要求659
10.8.5 三孔行星架齿轮主要工艺路线及工艺分析659
10.9 圆柱蜗杆副662
10.9.1 圆柱蜗杆概述662
10.9.2 圆柱蜗杆典型零件图样及技术要求662
10.9.3 圆柱蜗杆主要工艺路线及工艺分析663
10.9.6 蜗轮主要工艺路线及工艺分析664
10.9.4 蜗轮概述664
10.9.5 蜗轮典型零件图样及技术要求664
10.10 渐开线油泵齿轮副665
10.10.1 渐开线油泵齿轮副概述665
10.10.2 渐开线油泵齿轮典型零件图样及技术要求666
10.10.3 渐开线油泵齿轮主要工艺路线及工艺分析666
10.11 摆线油泵齿轮副668
10.11.1 摆线油泵齿轮副概述668
10.11.2 摆线油泵齿轮副(转子)典型零件图样及技术要求668
10.11.3 摆线油泵齿轮副(转子)主要工艺路线及工艺分析669
10.12.2 棘轮典型零件图样及技术要求671
10.12 棘轮齿加工671
10.12.1 棘轮概述671
10.12.3 棘轮主要工艺路线及工艺分析672
第11章航空仪表齿轮典型零件加工675
11.1 航空仪表齿轮的工艺特点及加工方法675
11.1.1 航空仪表齿轮的种类、结构特点及精度要求675
11.1.2 航空仪表齿轮轮齿加工方法675
11.1.2.1 全切式滚齿675
11.1.2.2 成形滚齿677
11.1.2.3 抛齿678
11.2.1 带轴小齿轮概述681
11.2 带轴小齿轮加工工艺681
11.2.2 带轴小齿轮典型零件图样及技术要求682
11.2.3 带轴小齿轮主要工艺路线及工艺分析683
11.3 片齿轮加工工艺684
11.3.1 片齿轮概述684
11.3.2 片齿轮典型零件图样及技术要求684
11.3.3 片齿轮主要工艺路线及工艺分析684
11.4 小模数直齿锥齿轮加工工艺685
11.4.1 小模数直齿锥齿轮概述685
11.4.3 小模数直齿锥齿轮主要工艺路线及工艺分析686
11.4.2 小模数直齿锥齿轮典型零件图样及技术要求686
11.5 小模数直齿端面齿轮加工工艺687
11.5.1 小模数直齿端面齿轮概述687
11.5.2 小模数直齿端面齿轮典型零件图样及技术要求687
11.5.3 小模数直齿端面齿轮主要工艺路线及工艺分析687
第12章齿轮制造新技术689
12.1 计算机技术在齿轮制造中的应用689
12.1.1 计算机辅助设计齿轮机械加工工艺规程689
12.1.1.1 CAPP基本原理与方法689
12.1.1.2 齿轮机械加工CAPP系统结构690
12.1.1.3 专家系统技术在CAPP系统中的应用691
12.1.1.5 开发齿轮加工CAPP系统应做的技术准备工作692
12.1.1.4 成组技术在CAPP系统中的应用692
12.1.1.6 计算机辅助编制工艺规程实例694
12.1.2 计算机辅助设计齿轮刀具695
12.1.2.1 计算机辅助设计技术概述695
12.1.2.2 内外直齿插齿刀CAD系统简介696
12.1.2.3 插齿刀CAD计算实例698
12.1.2.4 图形代真699
12.1.3 国外柔性制造系统(FMS)在齿轮加工中的应用701
12.2.1.1 用硬质合金滚刀加工淬硬齿轮702
12.2 硬齿面的加工702
12.2.1 硬齿面的滚切702
12.2.1.2 用超硬刀具加工淬硬齿轮705
12.2.2 硬齿面的插齿加工706
12.2.2.1 硬质合金插齿刀的设计特点706
12.2.2.2 硬齿面插齿加工的条件与加工实例707
12.3 齿轮刀具的表面强化708
12.3.1 氮化钛(TiN)镀膜齿轮刀具708
12.3.2 齿轮刀具的多元共渗709
12.3.3.2 激光强化后的表面质量710
12.3.3.3 齿轮滚刀采用激光强化的优点710
12.3.3.1 激光强化的工艺参数710
12.3.3 齿轮滚刀的激光强化710
12.4 新型齿轮刀具711
12.4.1 新型齿轮滚刀711
12.4.1.1 加工硬齿面硬质合金滚刀711
12.4.1.2 金属陶瓷(Cermet)滚刀711
12.4.2 新型插齿刀713
12.4.2.1 组合式硬质合金插齿刀713
12.4.2.2 组合式薄片插齿刀713
12.5.1 CBN技术特性714
12.5 立方氮化硼(CBN)磨轮用于齿面精加工714
12.5.2 CBN用于珩齿概况715
12.5.3 CBN用于磨齿概况716
12.5.4 发展趋势与努力方向717
12.5.4.1 开发高质量的CBN磨料717
12.5.4.2 改进磨具制造技术,提高磨轮质量717
12.5.4.3 开发CBN磨齿机和珩齿机718
12.6 轮齿的无切削加工718
12.6.1 齿轮和花键轴的冷轧718
12.6.1.1 自由分度式冷轧法718
12.6.1.2 强制分度式冷轧法721
12.6.2 圆柱齿轮的精挤齿723
12.6.3 小型密齿内花键的电解加工724
12.7 齿轮的喷丸处理725
12.7.1 喷丸的已知条件726
12.7.2 喷丸的工艺过程726
12.7.3 喷丸的质量控制727
12.7.4 喷丸的实例728
12.8 齿轮检测技术730
12.8.1 检测技术之发展730
12.8.2 检测量仪730
12.9 新型齿轮加工机床731
12.9.1 圆柱齿轮加工机床的发展731
12.9.2 锥齿轮加工机床的发展736
附录齿轮工艺技术标准739
1 国内齿轮标准739
1.1 圆柱齿轮标准目录汇编739
1.2 锥齿轮标准目录汇编740
1.3 蜗杆副、齿条、花键及链轮标准741
2 国外圆柱齿轮标准摘录741
2.1 美国圆柱齿轮标准ANSI/AGMA2000-A88741
2.2 德国圆柱齿轮标准DIN3962T1-T38.1978754
2.3 日本圆柱齿轮标准JIS B1702-1976(85)773
2.4 法国圆柱齿轮标准NF E23-006792
2.5 前苏联圆柱齿轮传动公差ГOCT1643-81797
1995《航空制造工程手册 齿轮工艺》由于是年代较久的资料都绝版了,几乎不可能购买到实物。如果大家为了学习确实需要,可向博主求助其电子版PDF文件(由《航空制造工程手册》总编委会主编 1995 北京:航空工业出版社 出版的版本) 。对合法合规的求助,我会当即受理并将下载地址发送给你。
高度相关资料
-
- 航空制造工程手册 飞机工艺装备
- 1994 北京:航空工业出版社
-
- 近代齿轮制造工艺
- 1994 北京:航空工业出版社
-
- 齿轮制造手册
- 1998 北京:机械工业出版社
-
- 齿轮工手册
- 1976 天津:天津人民出版社
-
- 航空制造工程手册 非金属结构件工艺
- 1996 北京:航空工业出版社
-
- 航空制造工程手册 通用基础
- 1993 北京:航空工业出版社
-
- 航空制造工程手册 电连接器工艺
- 1996 北京:航空工业出版社
-
- 航空制造工程手册 发动机叶片工艺
- 1998 北京:航空工业出版社
-
- 航空制造工程手册 框架壳体工艺
- 1997 北京:航空工业出版社
-
- 航空制造工程手册 飞机结构工艺性指南
- 1998 北京:航空工业出版社
-
- 齿轮滚刀的制造工艺
- 1962 北京:中国工业出版社
-
- 航空制造工程手册:特种加工
- 1993 北京:航空工业出版社
-
- 航空制造工程手册:飞机机械加工
- 1995 北京:航空工业出版社
-
- 航空制造工程手册 救生装备工艺
- 1995 北京:航空工业出版社
-
- 航空制造工程手册 飞机装配
- 1993 北京:航空工业出版社
提示:百度云已更名为百度网盘(百度盘),天翼云盘、微盘下载地址……暂未提供。➥ PDF文字可复制化或转WORD