《表3 分支空管挤出工艺中内流涎问题各个可能影响因素对比试验的试验条件与试验结果》
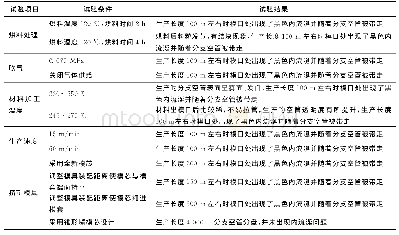
本系列图表出处文件名:随高清版一同展现
《Hytrel 7246材料分支空管内流涎问题的解决》
注:在进行各个可能影响因素(工艺参数)对比试验时,仅改变该因素设置,其余工艺参数均按照表2中给出的常规值设置。
为了确定分支空管挤出工艺中内流涎问题的真正影响因素,对烘料处理(温度和时间)、吹气、材料加工温度、生产速度、挤塑模具(模具类型及装配方式)各个可能影响因素进行了对比试验与结果分析。相关可能影响因素对比试验的试验条件与试验结果如表3所示。可见:a.烘料处理对比试验结果表明,提高烘料温度(常规100℃→120℃)和提高烘料时间(常规2h→4h)对解决内流涎问题并没有帮助,特别是经120℃、4h烘料处理后,Hytrel 7246料粒发黄,并有结块现象,更是表明烘料温度或烘料时间已达到极限,不宜再提高。因此,对于Hytrel 7246材料容易吸潮,拆封过的料必须进行烘料处理(其产品说明书中也提到使用时最好进行烘料处理),烘料处理时将烘料温度设定为100℃,烘料时间设定为2h已可满足生产要求,同时也确定了烘料处理并不是内流涎问题的影响因素。b.吹气对比试验(同一台设备,采用同一袋料)结果表明,吹气与否对解决内流涎问题(或减少出现频次)并没有帮助,即内流涎问题并非是由生产空管时采用的气源(来自空气压缩机,通过管路连接到挤塑机处)中可能含有少量的水分、油分、微小杂质等引起的。因此,可确定吹气并不是内流涎问题的影响因素。c.材料加工温度对比试验结果表明,适当降低或升高材料加工温度对解决内流涎问题没有帮助,反而会对分支空管的外观或成型造成影响,表2中给出的材料加工温度常规设置值(参考Hytrel 7246材料产品说明书中的推荐温度并结合实际情况制定)适宜性较可,确保了材料的加工性能。因此,可确定材料加工温度并不是内流涎问题的影响因素。d.生产速度对比试验结果表明,适当降低或升高生产速度对解决内流涎问题没有帮助,表2中给出的生产速度常规设置值适宜性较可。材料的加工温度一定时,生产速度的高低对材料的塑化有影响。由于材料塑化的热量来自于挤塑机螺膛外的加热块、材料与螺杆及料筒的摩擦剪切,而前者占主要因素,因此在加工温度及其他参数不变的情况下,若生产速度提高,单位时间内的出料量增加,相当于材料在螺膛内塑化的时间变短,降低了材料的塑化程度,反之若生产速度降低,则相当于提高了材料的塑化程度。因此,可确定生产速度并不是内流涎问题的影响因素。e.挤塑模具对比试验结果表明,无论是采用全新模芯、调整模具装配距离,还是采用锥形模芯嘴设计,均对解决内流涎问题有一定帮助。因此,可确定挤塑模具是内流涎问题的影响因素。相对于经过磨损的模芯(光缆构件通过模芯孔或清理模具时都会不可避免地碰触到模芯嘴,造成模芯磨损),采用全新模芯可有限改善(减少出现的频次,但无法真正解决和杜绝)内流涎问题,其原因在于熔融的材料通过全新模芯(同一规格且完好的、从未使用过)时不容易在模芯嘴前端处挂料,这就缓解了挂料长时间停留在模芯口,经过持续的高温作用,变黑形成内返料,当积累到一定程度时随着分支空管的前行被带走,形成内流涎的情况。相对于挤管式模具常规装配时模芯稍微伸出模套,调整模具装配距离使模芯与模套端面持平或稍微缩进模套同样可有限改善内流涎问题。相对于挤管式模具常规的管状模芯嘴(模芯嘴外形呈管状)设计,采用锥形模芯嘴(模芯嘴外形有一定倾斜角度)设计真正有效控制了内流涎出现的频次,解决了内流涎问题。
图表编号 | XD00221357800 严禁用于非法目的 |
---|---|
绘制时间 | 2020.10.25 |
作者 | 翟书宾 |
绘制单位 | 罗森伯格技术有限公司 |
更多格式 | 高清、无水印(增值服务) |