《精密加工新技术全集 第2版》
作者 | 田中义信等著 编者 |
---|---|
出版 | 复汉出版社 |
参考页数 | 477 |
出版时间 | 1983(求助前请核对) 目录预览 |
ISBN号 | 无 — 求助条款 |
PDF编号 | 85319078(仅供预览,未存储实际文件) |
求助格式 | 扫描PDF(若分多册发行,每次仅能受理1册) |
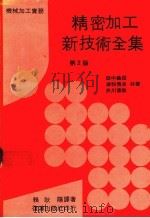
上册1
第1章精密加工的基础1
1.精密加工的意义1
2.精密加工法的分类1
3.精密加工的效果2
3.1增大接触面积2
3.2轴承的负荷能力增大5
3.3疲劳强度增大6
3.4耐摩耗性增大6
3.5耐蚀性增大6
3.6变质层厚度减少6
4.精密加工的原则7
4.1基准面8
4.2工作母机8
4.3工具13
4.4工作物14
4.5加工条件16
第2章切削理论18
1.序说18
1.1切削的定义18
1.2切削理论的意义18
1.3切削工具的角度19
1.4二次元切削与三次元切削20
2.切削的生成机构21
2.1切削的基本形态21
2.1.1切削的分类21
2.1.2流动形切削22
2.1.3剪断形切削22
2.1.4撕裂形切削23
2.1.5龟裂形切削23
2.2切削所受力的作用24
2.3切削内的应力与变形24
2.4切削条件所致切削形态的变化26
2.4.1工作物材质所致的变化26
2.4.2切削条件所致的变化26
2.5构成刃尖27
3.切削阻力28
3.1切削阻力28
3.2切削阻力的测定法29
3.2.1基本方法29
3.2.2工具动力计的条件30
3.3切削阻力的基础理论32
3.3.1流动形切削与剪断面32
3.3.2基本关系34
3.3.3切削阻力的理论式37
3.4切削条件与切削阻力的关系40
3.4.1切削阻力分力的关系40
3.4.2进刀深度及进给量的影响41
3.4.3工具角度的影响43
3.4.4切削速度的影响44
3.5工作物的机械性性质与切削阻力的关系44
4.切削温度45
4.1概说45
4.2切削温度的测定法46
4.3切削温度的理论48
4.3.1剪断面的平均温度?s48
4.3.2工具、切屑接触面(斜角面)的平均温度?t49
4.3.3切削条件与切削温度50
4.3.4切削场的温度分布50
4.4切削温度的实验式51
4.5切削温度与工具寿命52
5.切削加工面52
5.1概说52
5.2切削加工面的粗糙度53
5.2.1加工面粗糙度的构成53
5.2.2切削方向的粗糙度53
5.2.3进给方向的粗糙度56
5.2.4对理论粗糙度的外乱57
5.3加工变质层59
5.3.1加工变质层的组成59
5.3.2变质层深度的测定法59
5.3.3切削条件所致变质层厚度的变化63
5.3.4残留应力65
6.切削工具的摩耗与寿命66
6.1工具材料66
6.1.1高速钢工具66
6.1.2超硬合金工具67
6.1.3陶瓷工具67
6.1.4其他超硬工具材料67
6.2切削工具的损耗与其形态71
6.3工具损耗的机构72
6.3.1摩耗的机构72
6.3.2缺损机构73
6.4工具的寿命73
6.4.1工具寿命的基准73
6.4.2VT线图75
6.4.3最适切削速度76
7.被削性78
7.1被削性的定义78
7.2被削性的试验法79
7.2.1工具的寿命试验80
7.2.2利用切削阻力的方法80
7.2.3利用切削温度的方法80
7.2.4简易试验法81
7.3被削性方程式81
7.4主要材料的被削性82
7.4.1纯金属82
7.4.2碳钢82
7.4.3特殊钢82
7.4.4快削钢84
7.4.5铸铁86
7.4.6铜合金87
7.4.7轻合金89
8.切削系统的振动89
8.1振动的种类与原因89
8.1.1强制振动89
8.1.2自激振动90
8.2制振法91
8.2.1机械的防振91
8.2.2阻尼器92
8.2.3切削条件的选择92
8.2.4振动的适应控制92
9.加工液93
9.1概说93
9.2加工液的种类与性能94
9.2.1加工液的种类94
9.2.2非水溶性切削油94
9.2.3水溶性切削油96
9.2.4其他切削剂96
9.3加工液的注加方法96
10.特殊切削法97
10.1高速、超高速切削97
10.1.1高速切削的意义97
10.1.2高速切削的作业98
10.1.3超高速切削99
10.2高温切削100
10.2.1高温切削的意义100
10.2.2高温切削的方法100
10.2.3高温切削的切削作用103
10.3低温切削103
10.4振动切削104
第3章利用切削的精密加工105
1.精密车削反精密搪孔105
1.1概说105
1.2工具105
1.2.1钻石刀具105
1.2.2超硬刀具107
1.3作业条件108
1.3.1切削速度108
1.3.2进刀深度及进给量108
1.3.3加工面粗糙度与精度109
1.4精密车床109
1.5精密搪床110
2.拉削111
2.1概说111
2.2拉刀111
2.2.1拉刀的种类111
2.2.2拉刀的构成113
2.2.3柄与导引部114
2.2.4齿距115
2.2.51齿的进刀深度116
2.2.6齿的形状117
2.2.7斜角与离隙角119
2.2.8齿的倾角119
2.2.9断屑沟119
2.2.10 擦光用拉刀119
2.2.11旋转拉刀120
2.2.12拉刀的制法121
2.2.13 拉刀例121
2.3拉床与其作业123
2.3.1拉床123
2.3.2拉床的作业126
第4章砂轮130
1.研磨与砂轮130
2.砂轮的形状131
3.砂轮的构成要素133
3.1磨料133
3.1.1A磨料134
3.1.2WA磨料134
3.1.3 C磨料135
3.1.4 G C磨料135
3.1.5其他A系磨料135
3.1.6氧化锆系135
3.1.7人造钻石磨料135
3.1.8立方晶氮化硼磨料136
3.2粒度136
3.3结合度(硬度)137
3.4结合度的机械性试验法137
3.4.1大越氏结合度试验法137
3.4.2球压入法139
3.4.3利用砂轮固有振动数的方法一sonic式试验方法139
3.4.4其他的方法139
3.5结合剂139
3.5.1瓷质烧结式结合剂139
3.5.2矽酸塩结合剂140
3.5.3虫胶结合剂140
3.5.4树脂结合剂140
3.5.5橡胶结合剂140
3.6组织141
4.砂轮的试验142
5.砂轮品质表示法145
第5章研磨理论146
1.引言146
2.砂轮的研磨作用146
2.1砂轮的切削作用147
2.2研磨的切削148
2.3研磨过程的4形态149
2.4磨料切入深度与接触弧150
2.5研磨的机率现象153
3.研磨阻力153
3.1研磨阻力与其意义153
3.2单粒的研磨阻力154
3.3研磨阻力的理论式155
3.4研磨阻力的测定法157
3.4.1在砂轮部测定157
3.4.2在工作物部测定157
3.5研磨阻力与研磨条件158
4.研磨热159
4.1研磨热159
4.2研磨温度160
4.3研磨温度的计算160
4.3.1磨料研磨点温度160
4.3.2砂轮研磨点温度161
4.3.3工作物的平均温升161
4.4研磨温度的测定法162
4.4.1磨料研磨点温度162
4.4.2砂轮研磨点温度163
4.4.3工作物的平均温度164
4.5实际的研磨温度164
4.6研磨温度的控制165
5.研磨面165
5.1研磨面的形成165
5.2加工面的粗糙度166
5.2.1加工面粗糙度的几何学166
5.2.2粗糙度的机率论168
5.2.3粗糙度的半机率论170
5.2.4研磨条件对研磨面粗糙度的影响171
5.3研磨面的损伤173
5.3.1加工变质层173
5.3.2残留应力174
5.3.3研磨烧焦与研磨破裂175
6.砂轮的损耗与寿命177
6.1砂轮的切刃177
6.1.2切刃的形状与分布177
6.1.2连续切刃间隔178
6.1.3研磨中的切刃变化179
6.1.4切刃面积率180
6.1.5切刃的自生作用182
6.2砂轮的寿命182
6.2.1砂轮的损耗183
6.2.2比损耗量与研磨比183
6.2.3研磨条件与砂轮损耗量的关系185
6.2.4砂轮的修整间寿命186
6.2.5研磨条件与砂轮寿命187
第6章研磨作业189
1.砂轮的选择189
1.1选择的基准189
1.2磨料的选择189
1.3结合剂的选择192
1.4粒度的选择193
1.5结合度的选择193
1.6组织的选择194
1.7砂轮的选择表与选择剂194
1.8砂轮的安全性198
2.研磨作业的一般事项199
2.1砂轮的安装与平衡199
2.1.1砂轮的安装199
2.1.2砂轮的平衡200
2.2砂轮的修整与整形200
2.2.1Hantington修整器201
2.2.2用砂轮修整201
2.2.3钻石修整器202
2.2.4轧碎辊203
2.2.5旋转修整器204
2.3研磨液204
2.3.1研磨液的机能204
2.3.2研磨液的选择205
2.3.3研磨液的注加法206
2.4研磨条件207
2.4.1砂轮的周速207
2.4.2工作物的周速207
2.4.3进给速度208
2.4.4切入210
2.4.5研磨留量211
2.5研磨作业发生的缺陷211
3.各种研磨作业217
3.1圆筒研磨217
3.1.1基本形217
3.1.2圆筒磨床218
3.1.3自动定寸装置221
3.1.4圆筒研磨作业222
3.2内面研磨223
3.2.1内面的研磨的基本形223
3.2.2内面磨床224
3.2.3内面研磨作业228
3.3平面研磨229
3.3.1平面研磨的基本形229
3.3.2平面磨床231
3.3.3平面研磨作业233
3.4工具研磨235
3.4.1工具研磨的种类235
3.4.2车刀磨床与其作业235
3.4.3钻头磨床与其作业236
3.4.4工具磨床与其作业236
3.4.5其他的工具研磨240
3.5无心研磨240
3.5.1无心研磨的方法240
3.5.2无心磨床241
3.5.3研磨条件与作业方法242
3.6特殊的研磨作业247
3.6.1可搬式砂轮机247
3.6.2曲轴磨床248
3.6.3凸轮轴磨床249
3.6.4活塞磨床249
3.6.5座圈磨床250
3.6.6轧辊磨床250
3.6.7多砂轮磨床251
3.6.8栓槽轴磨床252
3.6.9滑移面磨床253
3.6.10轮廓磨床254
3.6.11切断磨床254
3.7利用钻石、氮化硼砂轮的研磨254
3.7.1钻石砂轮254
3.7.2超硬合金的研磨256
3.7.3氮化硼砂轮257
3.8超精密、镜面研磨258
第7章轧光与擦光261
1.轧光261
1.1轧光的方法261
1.2加工条件的影响262
1.2.1前加工的影响262
1.2.2滚子的直径及圆角半径263
1.2.3压力263
1.2.4滚子的进给263
1.2.5加工液264
1.3轧光的效果264
1.3.1轧光面的性质264
1.3.2轧光面的硬度265
1.3.3疲劳强度265
1.3.4摩擦性能266
1.3.5耐摩耗性266
1.4轧光的应用267
2.擦光268
2.1擦光的方法268
2.2擦光法的理论268
2.3擦光的效果270
2.3.1内径的尺寸精度270
2.3.2加工面粗糙度272
3.微细的擦光加工273
4.硬珠拉削法274
下册275
第8章精密磨料加工275
1.引言275
2.抹磨277
2.1概说277
2.2抹磨的机构279
2.2.1抹磨剂的切削作用279
2.2.2抹磨剂的粉碎280
2.2.3堵塞281
2.2.4压力与速度的影响282
2.2.5抹磨力283
2.3抹磨剂、抹磨具及加工液284
2.3.1抹磨剂284
2.3.2抹磨具285
2.3.3加工液286
2.4加工面286
2.4.1抹磨加工面的构成286
2.4.2抹磨面的粗糙度287
2.5抹磨机289
2.5.1立形抹磨机290
2.5.2其他抹磨机298
2.6手工抹磨299
2.6.1平面的抹磨299
2.6.2圆筒的抹磨303
3.搪磨305
3.1概说305
3.1.1搪磨的概念305
3.1.2搪磨的特色306
3.2加工条件与加工特性307
3.2.1前加工307
3.2.2磨石308
3.2.3速度与交差角311
3.2.4磨石压力与切入速度314
3.2.5加工液315
3.2.6搪磨的加工面316
3.3搪磨工具316
3.3.1基本构造与动作316
3.3.2三爪式(three finger type)搪磨工具318
3.3.3制动式(brake type)搪磨工具318
3.3.4油压式(hydr-aulic type)搪磨工具319
3.3.5其他内径用搪磨工具320
3.3.6外径用搪磨工具320
3.3.7磨石形状321
3.4自动定寸与控制装置321
3.5搪磨机与其作业324
3.5.1搪磨机的分类324
3.5.2立形搪磨机325
3.5.3横形搪磨机326
3.5.4搪磨机的作业例327
4.超细磨327
4.1概说327
4.1.1超细磨的历史327
4.1.2超细磨的特色329
4.1.3超细磨的应用333
4.2超细磨的机构333
4.2.1磨石的加工经过333
4.2.2超细磨的加工效率335
4.3超细磨的加工条件335
4.3.1磨石335
4.3.2压力338
4.3.3工作物的速度340
4.3.4磨石的振动数与振幅341
4.3.5加工液343
4.3.6超细磨的2段工程作业343
4.4超细磨面345
4.4.1超细磨面的构造345
4.4.2超细磨面的粗糙度346
4.4.3超细磨面的耐摩耗性与耐蚀性346
4.5超细磨机347
4.5.1超细磨头347
4.5.2圆筒超细磨机348
4.5.3内面超细磨机348
4.5.4平面超细磨机348
第9章磨光351
1.带式研磨351
1.1概说351
1.2研磨带(砂布,砂纸)351
1.3带式磨床353
1.4带磨作业354
1.4.1速度与压力354
1.4.2加工液354
1.4.3带磨机的作业例355
2.擦光加工356
2.1概说356
2.2擦光轮357
2.3磨料与擦光研磨剂359
2.3.1粗磨用磨料359
2.3.2中磨用磨料360
2.3.3光泽加工用磨料360
2.3.4擦光研磨剂361
2.4擦光机361
2.5加工特性362
2.5.1动力362
2.5.2擦光加工量363
2.5.3加工面粗糙度364
2.5.4研磨剂构成要素的作用364
2.6擦光的作业365
3.滚桶加工367
3.1概说367
3.2滚桶368
3.2.1旋转形滚桶368
3.2.2振动形滚桶370
3.2.3固定框371
3.3媒质(磨料)371
3.4研磨剂374
3.5加工特性375
3.6滚桶加工的作业条件376
3.6.1水的硬度376
3.6.2滚桶中的液面高度377
3.6.3工作物与媒质的混合比377
3.6.4滚桶速度377
3.6.5加工时间378
4.喷射加工378
4.1喷粒加工378
4.1.1概说378
4.1.2喷粒机379
4.1.3喷粒加工的作业379
4.1.4喷射磨料的精密加工382
4.2珠击法382
4.2.1概说382
4.2.2珠击法的施行法382
4.2.3珠383
4.2.4加工条件383
4.2.5珠击的效果与应用386
4.3液体搪磨388
4.3.1概说388
4.3.2液体搪磨法388
4.3.3磨料389
4.3.4加工条件391
4.3.5液体搪磨的应用392
5.粘弹性流动研磨393
5.1概说393
5.2媒质394
5.3加工机械394
5.4加工特性395
5.5应用例396
第10章特殊加工法397
1.前言397
2.放电加工397
2.1加工原理与特色398
2.2放电加工机398
2.2.1构成398
2.2.2电源与电极398
2.3加工特性400
2.4特殊放电加工401
2.4.1线切割放电加工工401
2.4.2放电切断401
2.4.3放电研削402
2.4.4非金属的放电加工402
3.电子束加工403
3.1加工原理与特色403
3.2电子束加工装置404
3.3加工特性404
3.4电子束的应用404
4.雷射加工405
4.1加工原理与特色405
4.2雷射加工机405
4.2.1雷射光源405
4.2.2雷射加工机的构成406
4.3加工特性与应用407
4.3.1点径与加工深度407
4.3.2开孔加工408
4.3.3切断408
4.3.4熔接409
4.3.5热处理409
5.电解应用加工409
5.1电解现象与加工409
5.2电解加工410
5.2.1方法与特色410
5.2.2加工机411
5.2.3加工特性412
5.3电解研削413
5.3.1方法与特色413
5.3.2电解研削机414
5.3.3加工特性414
5.4电解磨料加工415
5.4.1电解搪磨415
5.4.2电解抹磨415
5.4.3振动电解抹磨415
5.5电解研磨415
5.5.1加工原理与特色416
5.5.2加工条件与特性416
5.5.3电解液417
6.化学加工417
6.1加工原理与特色417
6.2化学压穿417
6.2.1加工法与特色417
6.2.2工程418
6.2.3加工特性419
6.3化学切削——化学铣削——420
6.3.1方法与特色420
6.3.2工程420
6.3.3加工特性421
6.4化学研磨421
6.4.1方法与特色421
6.4.2化学研磨液421
7.超音波加工421
7.1加工原理与特色421
7.2加工机423
7.3加工特性423
7.4超音波振动加工的应用424
7.4.1利用超音波振动砂轮的精密加工424
7.4.2超音波研磨424
8.高速液体喷射加工法424
8.1原理与特色424
8.2加工特性425
第11章机械要素的精密加工427
1.螺纹的精密加工法427
1.1前言427
1.2螺纹的研磨427
1.2.1概说427
1.2.2螺纹研磨法428
1.2.3螺纹磨床431
1.2.4螺纹研磨用砂轮432
1.2.5研磨条件435
1.2.6螺纹研磨的精度437
1.2.7螺纹研磨作业的注意事项437
1.3螺纹的抹磨439
2.齿轮的精密加工法441
2.1前言441
2.2齿轮的研磨441
2.3齿轮的抹磨447
2.4齿轮的刮削447
2.5齿轮的搪磨455
第12章超精密加工456
1.引言456
1.1超精密加工456
1.2背景与意义456
2.超精密加工的实例457
3.超精密加工的原则457
3.1工作母机457
3.1.1热变形457
3.1.2刚性458
3.1.3计测控制技术458
3.1.4机械运动的控制界限458
3.1.5构造的简洁性459
3.2工作物459
3.2.1弹性变形459
3.2.2热变形460
3.2.3材料要因460
3.3工具460
3.3.1加工厚度的分解与最小加工厚度461
3.3.2表面加工能力461
3.3.3耐久性462
3.4加工现象462
3.4.12次元模型462
3.4.2从工具把轮廓复现到工作物463
3.4.3理想的工具464
4.超精密加工各论465
4.1用单刃钻石工具切削466
4.1.1工作母机466
4.1.2超精密车削的材料466
4.1.3加工条件467
4.1.4面粗糙度与精度468
4.1.5工具寿命468
4.2超精密精密研磨468
4.3利用磨料或粉末的超精密加工469
4.3.1EEM(elastic emission machin-ing)470
4.3.2液中镜面抛光471
4.3.3浮动抛光法472
4.3.4利用软质粒子的机械化学抛光473
4.4离子束加工473
4.4.1概说473
4.4.2原理与特征474
4.4.3加工机的构成474
4.4.4加工特性475
4.4.5应用476
1983《精密加工新技术全集 第2版》由于是年代较久的资料都绝版了,几乎不可能购买到实物。如果大家为了学习确实需要,可向博主求助其电子版PDF文件(由田中义信等著 1983 复汉出版社 出版的版本) 。对合法合规的求助,我会当即受理并将下载地址发送给你。
高度相关资料
-
- 机械加工新技术
- 1985 北京:科学技术文献出版社
-
- 新版 纤维加工技术
- 昭和51年12月第1版 株式会社 地人书馆
-
- 超精密加工技术
- 工业调查会
-
- 农村新技术大全 加工业
- 1997 昆明:云南科学技术出版社
-
- セラミックスの超精密加工
- 1983 日刊工業新聞社
-
- 超精密加工技術
- 1984 工業調査会
-
- 机械加工工艺手册 第2卷 第14章 精密加工及超精密加工
- 1991 北京:机械工业出版社
-
- 农药剂型加工技术 第2版
- 1998 北京:化学工业出版社
-
- 软盘加密与解密新技术
- 1994 北京:清华大学出版社
-
- 精密加工工艺学
- 1990 北京:国防工业出版社
-
- 实用食品加工新技术精选 2
- 1999 北京:中国轻工业出版社
-
- 信息加密技术
- 1989 成都:四川科学技术出版社
提示:百度云已更名为百度网盘(百度盘),天翼云盘、微盘下载地址……暂未提供。➥ PDF文字可复制化或转WORD