《表面工程手册 第1篇 表面调整及净化》
作者 | 李国英 编者 |
---|---|
出版 | 北京:机械工业出版社 |
参考页数 | 36 |
出版时间 | 1998(求助前请核对) 目录预览 |
ISBN号 | 7111058690 — 求助条款 |
PDF编号 | 87026478(仅供预览,未存储实际文件) |
求助格式 | 扫描PDF(若分多册发行,每次仅能受理1册) |
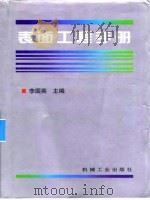
附录 国内现行的表面工程有关标准 附-1
1 除锈 4-3
1 镀层的主要特性及用途 6-3
第2章 渗碳与碳氮共渗3
3 发展趋势 5-3
2 种类与目的 5-3
1 作用与任务 5-3
1.2 锈蚀的鉴别 4-3
1.1 各种金属锈蚀的特征 4-3
1.1 热喷涂方法分类 3-3
1 热喷涂技术原理 3-3
1.3 涂料命名和型号 2-3
1.2 涂料分类 2-3
1.1 涂料组成及各组分的作用 2-3
1 涂料组成及分类 2-3
第2章 常用涂料3
2 涂料的作用 2-3
1 涂料与涂装的定义 2-3
2.2 按金属种类分类 7-3
1 摩擦学系统的基本结构 10-3
1.3 影响大气腐蚀主要因素 9-3
1.2 大气腐蚀的机制 9-3
1.1 概述 9-3
1 大气腐蚀及其主要影响因素 9-3
1 概述 8-3
2.3 按用途分类 7-3
1.1 防护性镀层 6-3
2.1 按转化膜分类 7-3
2 化学成膜处理法分类 7-3
1 定义 7-3
2.2 电化当量 6-3
2.1 法拉第定律 6-3
2 电化学计算 6-3
1.3 功能性镀层 6-3
1.2 防护装饰性镀层 6-3
1 表面工程的基本涵义、特点、分类及常用工艺方法 0-3
1 表面调整及净化的目的 1-3
3 表面调整及净化法选择 1-3
第2章 碱液清洗3
1 碱液清洗的目的 1-3
2 碱液清洗溶液 1-3
2.1 碱液清洗原理和主要材料 1-3
2 表面调整及净化分类 1-3
第2章 镀前处理4
1.2 各种热喷涂方法的技术特征 3-4
2.4 镀层厚度等计算 6-4
2 摩擦学系统的重要参数 10-4
2.2 碱液清洗液配方 1-4
2.3 电流效率 6-4
1.1 渗碳工艺参数 5-4
1 钢的渗碳 5-4
2.2 线材火焰喷涂 3-4
2.4 按施工方法分类 7-4
3 化学转化膜的防护性能 7-4
2.1 熔体金属注入喷涂 3-4
2.1 摩擦副的材料 10-4
2 热喷涂方法 3-4
2.3 大气腐蚀性分类 9-4
2.1 按表面湿润程度分类 9-4
2 大气腐蚀的分类 9-4
2.2 按大气环境分类 9-4
2.5 粉末火焰喷熔 3-5
3 表面工程技术发展趋势 0-5
4 化学转化膜的应用范围 7-5
第2章 电化学转化膜5
1 铝和铝合金的阳极氧化 7-5
1.1 概述 7-5
1.2 阳极氧化膜的生成机理及其性质 7-5
2.3 陶瓷棒火焰喷涂 3-5
3.常见的大气腐蚀类型 9-5
3.1 均匀腐蚀 9-5
3.2 缝隙腐蚀 9-5
3.3 应力腐蚀 9-5
2 表面工程技术在国民经济中的地位与作用 0-5
3.4 选择性腐蚀 9-5
3.5 电偶腐蚀 9-5
第1篇 表面调整及净化第1章 概 述5
1.4 磨光轮 6-5
1.3 除锈方法 4-5
2.4 粉末火焰喷涂 3-5
1.3 磨光机(抛光机) 6-5
2.6 爆炸喷涂 3-5
1.2 研磨 6-5
1.1 概述 6-5
1 研磨、抛光 6-5
3 碱液清洗工艺方法 1-5
3.1 工艺方法分类及主要特点 1-5
2.7 高速火焰喷涂 3-5
1.2 气体渗碳 5-5
1.6 粘接剂 6-6
2.8 电弧喷涂 3-6
2.9 等离子喷涂 3-6
1.5 磨料 6-6
1 溶剂清洗的目的和内容 1-6
第3章 溶剂清洗6
3.2 清洗工艺方法的选择 1-6
4 大气腐蚀数据表 9-6
1.7 磨光带磨光 6-6
2.2 负荷集 10-6
2 常用表面分析技术及相应仪器 8-6
2.1 X射线衍射谱(XRDS) 8-6
2.2 电子衍射谱(EDS)和透射电子显微镜(TEM) 8-6
2 涂料的性能 2-6
2.1 油脂漆 2-6
2.2 天然树脂漆 2-6
1.9 抛光轮 6-7
1.8 抛光 6-7
25 醇酸树脂涂料 2-7
2.4 沥青漆类 2-7
2 溶剂清洗材料 1-7
1.10 抛光膏 6-7
第4章 水剂清洗工艺方法7
2.3 酚醛树脂漆 2-7
4.2 检验分类和检验方法 4-117
2.11 线爆喷涂 3-7
2.10 反应等离子喷涂 3-7
1.11 成批光饰 6-7
3 溶剂清洗工艺方法 1-7
2.3 负荷持续时间 10-7
6.1 金色系列 6-147
2.4 扫描电镜(SEM)和电子探针(EPMA) 8-7
2.3 X射线荧光谱(XRFS) 8-7
2.6 氨基树脂漆 2-8
4.1 用化学热处理的方法改善喷涂涂层性能 3-8
3 涂层形成和裂纹产生过程 3-8
2.12 激光喷涂 3-8
1.1 水剂清洗的特点 1-8
1.1 水剂清洗材料 1-8
第2章 海洋环境的腐蚀与防护8
5.3 金属腐蚀的评价方法国家标准 9-8
2.5 俄歇电子能谱(AES) 8-8
2.1 概述 6-8
2 脱脂 6-8
2.2 有机溶剂脱脂 6-8
4 热喷涂技术和其他表面技术相互渗透的联合应用 3-8
5.2 加速腐蚀试验国家标准 9-8
5.1 大气腐蚀暴露试验 9-8
5 大气腐蚀试验与评价方法国家标准 9-8
2.6 X射线光电子谱(XPS) 8-9
4.2 用电镀和热喷涂工艺技术的结合来改善喷涂层的性能 3-9
4.3 用激光束重熔喷涂层提高涂层的耐磨性 3-9
5 热喷涂在工业中的应用 3-9
5.1 工艺控制 3-9
5.2 模拟与诊断 3-9
第2章 热喷涂涂层材料9
1 材料在海水中的腐蚀 9-9
2.7 硝基漆类 2-9
1.1 金属材料耐海水腐蚀性能 9-9
1.3 表面活性剂的分类及其特性指数 1-9
1.2 水剂清洗液的组分与表面活性剂 1-9
2.8 纤维素漆 2-9
2.3 化学脱脂 6-9
2.8 离子散射谱(ISS) 8-10
2.11 丙烯酸树脂漆 2-10
3.1 锌、铝、锌铝合金及低熔点合金丝 3-10
3 热喷涂线材 3-10
2 热喷涂涂层材料分类 3-10
1 热喷涂工艺对涂层材料的基本要求 3-10
2.10 烯树脂漆 2-10
2.9 过氯乙烯漆 2-10
2.4 接触条件 10-10
1.2 防海水腐蚀金属镀涂层的耐蚀性 9-10
2.7 二次离子质谱(SIMS) 8-10
第2章 涂(膜)层及界面的形貌表面分析11
2.10 激光拉曼谱(LRM) 8-11
2.9 电子能量损失谱(EE1S) 8-11
2.12 聚酯树脂漆 2-11
2.13 环氧树脂漆 2-11
3.2 镍及镍基合金丝 3-12
3.3 铁基合金丝 3-12
1 各种显微镜类型 8-12
2 光学显微镜(OM)分析 8-12
2.14 聚氨酯漆 2-12
3.2 酸洗常用酸 6-13
3.1 概述 6-13
3 酸洗 6-13
3 透射电子显微镜(TEM)分析 8-13
4 扫描电镜(SEM)分析 8-13
1.4 洗涤剂其他组分与洗涤剂 1-13
1.3 海洋环境有机涂装体系的耐蚀性 9-13
2.18 乳胶漆 2-13
2.17 其他漆 2-13
2.16 橡胶漆 2-13
2.15 元素有机漆 2-13
2.19 电泳漆类 2-14
3.3 常用酸洗液的配方和工艺条件 6-14
1.3 固体渗碳 5-14
6 场离子显微镜(FIM)分析 8-14
5 扫描透射电镜(STEM)分析 8-14
2 水剂清洗工艺方法 1-15
2 清洗 4-15
1.4 液体渗碳与电解渗碳 5-15
2.2 清洗方法分类法 4-15
2.3 清洗材料分类法 4-15
3 乳剂清洗 1-15
2.20 粉末涂料 2-15
2.1 概述 4-15
第5章 化学除锈15
3.5 钼丝 3-15
3.4 铜及铜合金丝 3-15
8 试样的制备 8-15
7 各种显微镜的应用前景 8-15
3.6 镍铝复合喷涂丝 3-16
3.7 一步法耐磨涂层用复合丝 3-16
3.8 陶瓷棒 3-16
1.1 化学除锈的目的 1-16
1.2 化学除锈内容 1-16
1 表面微米级深度的元素分析 8-16
2.21 高固体分涂料 2-16
2.22 非水分散型涂料 2-16
2.23 紫外线固化(UVC)涂料 2-16
第3章 涂(膜)层及界面的成分与结构分析16
9 图像分析技术 8-16
2.1 化学除锈原理 1-16
2 化学除锈溶液 1-16
3.5 电化学抛光 6-16
第3章 电镀单金属16
1 化学除锈的目的和内容 1-16
3.4 电化学浸蚀 6-16
2.1 俄歇电子谱 8-17
1 镀铜 6-17
4 热喷涂粉末材料 3-17
4.1 热喷涂粉末主要特性 3-17
4.2 金属及合金粉末 3-17
2.4 化学除锈液配方 1-17
2.3 各种酸除锈性能比较 1-17
2 海洋环境腐蚀的防护 9-17
2.1 合理的选材与设计 9-17
3 摩擦副中磨损造成损伤的机理和现象 10-17
3.1 磨损造成损伤的基本类型 10-17
2.24 电子束固化(EEC)涂料 2-17
3.2 粘着磨损 10-17
1.5 离子渗碳与其他渗碳方法 5-17
1.1 铜镀层的性质和用途 6-17
2 几个原子表层的元素分析 8-17
2.2 缓蚀剂的作用与品种 1-17
1.2 氰化镀铜 6-18
2.2 俄歇线扫描曲线 8-18
2.3 俄歇像 8-18
2.4 原子浓度-深度剖面图 8-18
3.2 溶剂的通性及其作用 2-18
2.5 中和与水洗 1-18
3 常用涂料的稀释剂 2-18
3.1 概述 2-18
3 最外表面单原子层的元素分析 8-19
4 其他微区元素分析和比较 8-19
2.7 去油除锈综合处理 1-19
2.6 碱去锈及除氧化皮 1-19
3.3 磨料磨损 10-19
第6章 机械清理20
3 不同基材化学除锈方法 1-20
2.9 用除锈电极除锈 1-20
2.8 化学除锈膏除锈 1-20
3.4 疲劳磨损 10-20
3.3 各类溶剂及特性 2-20
3.6 油浴脱水 4-21
3.5 晾干或滴干 4-21
3.4 擦干 4-21
3.3 红外线干燥 4-21
3.1 压缩空气吹干 4-21
第2章 防锈水剂及防锈切削液21
1 水溶性缓蚀剂 4-21
3.2 干燥器烘干等加热干燥 4-21
1.1 中性介质缓蚀剂的作用机理 4-21
2.4 清洗应注意事项 4-21
1 机械清理的目的、内容 1-21
2 机械清理方法 1-21
第7章 表面精整21
3.4 常用涂料的稀释剂 2-21
3.5 摩擦化学磨损 10-21
1.3 硫酸盐镀铜 6-21
5 X射线光电子能谱(XPS)分析表面化学态 8-21
4.3 自熔性合金粉末 3-21
3 干燥 4-21
第3章 大型贮罐防护22
6 激光拉曼谱(LRM)分析表面分子态 8-22
7 表面微区晶体结构分析 8-22
3.5 溶剂的选择与使用 2-22
1.3 阳极氧化方法的分类 7-22
2.2 海洋环境防蚀涂覆保护层 9-22
4.1 磨损率 10-22
4 磨损特性与可靠性 10-22
1.2 常用的中性介质缓蚀剂 4-23
第4章 涂(膜)层及界面的电镜分析图谱23
4 涂料的选择 2-23
8 各种晶体结构分析技术的比较 8-23
1.6 渗碳用钢及渗碳后的热处理 5-24
第3章 表面工程技术的耐磨损作用24
5 涂料的施工条件 2-24
6 涂料选用的原则 2-24
第3章 涂装前处理工艺及设备24
4.3 可靠性 10-24
4.2 磨损表征 10-24
2 防锈水剂 4-25
2.1 防锈水剂的特性 4-25
2.2 防锈水剂的种类 4-25
1.4 焦磷酸盐镀铜 6-25
1 涂装前处理的目的 2-25
2 除油处理工艺 2-25
2.1 金属除油 2-25
1 电镀、刷镀和化学镀 8-25
1.7 渗碳层的组织和性能 5-25
2.2 木材表面除油及其他预处理工艺 2-26
2.3 塑料表面前处理 2-26
2.4 混凝土表面前处理工艺 2-26
2.3 防锈水的配制和使用 4-26
4.4 陶瓷粉末 3-26
1.1 精整目的 1-27
1.2 精整方法 1-27
3 除锈工艺 2-27
3.1 除锈方法的分类与应用 2-27
3.2 除油除锈综合处理及除锈等级 2-27
1 精整方法 1-27
3 防锈切削液 4-27
3.1 防锈切削液的作用和要求的性能 4-27
3.2 防锈切削液的分类 4-27
4 磷化工艺 2-28
4.1 磷化的作用与分类 2-28
1.5 铜镀层的镀后处理 6-29
1.6 不良铜镀层的退除 6-29
2 镀镍 6-29
2.1 镍镀层的性质和用途 6-29
4.5 塑料粉末 3-29
1 耐磨表面保护的基本模型 10-29
第8章 表面清洁度一般要求及检测方法29
2 精整工作介质 1-29
4.2 磷化膜形成的原理及特征 2-29
1.2 涂层选择 9-30
1.1 工艺方法 9-30
1.8 渗碳件质量检验、常见缺陷及防止措施 5-30
4.3 磷化液配方及工艺参数 2-30
2.3 镀镍溶液的种类 6-30
1 工艺方法及涂层选择 9-30
2 耐粘着磨损表面保护的基本要求 10-30
2.2 原理 6-30
4.4 磷化膜的质量检验 2-31
2.4 镀镍液各种组分的作用和影响 6-31
4.6 复合粉末 3-31
3 耐磨料磨损表面保护的基本要求 10-31
2.1 流程设计依据 9-32
2.6 镀镍光亮剂 6-32
2.5 工艺条件的影响 6-32
2 钢的碳氮共渗 5-32
2 流程设计及施工工艺 9-32
2.1 气体碳氮共渗 5-32
第9章 铸、锻、焊件毛坯表面净化32
4 耐疲劳磨损表面保护的基本要求 10-32
2 检测方法 1-32
1 一般要求 1-32
4.5 影响磷化膜质量的主要因素 1-32
2.2 涂装工艺流程 9-33
第4章 耐磨表面工程技术及其应用33
2.3 涂装工艺 9-33
附录 国内热喷涂材料生产厂家见附表 3-33
第4章 高温环境钢结构防护33
第3章 基体表面预处理33
5 主要耐磨表面保护技术类型 10-33
4.6 磷化过程中出现的病态及防治方法 2-33
4.7 金属钝化 2-34
2.7 镀镍液的杂质处理 6-34
4.8 去油、除锈、磷化或钝化“三合一”处理工艺 2-34
1 概述 3-34
2 基体表面预处理方法 3-34
第3章 防锈油脂34
3.3 防锈切削液的配制和使用时应注意事项 4-34
第2篇 有机涂装第1章 概 述35
2 表面净化方法 1-35
4.9 去油、除锈、磷化、钝化“四合一”处理工艺 2-35
1 铸、锻、焊件毛坯表面特点 1-35
1 油溶性缓蚀剂 4-35
1 热喷涂 10-35
1.1 油溶性缓蚀剂的作用机理 4-35
3 基体表面预处理设备与材料 3-35
1.1 概述 10-35
2 转化膜 8-36
5.2 设备的结构 2-36
1.2 油溶性缓蚀剂的分类 4-36
5 浸渍式涂装前处理设备 2-36
4.10 有色金属件的预处理 2-36
1.2 热喷涂层的摩擦学性能 10-36
2.2 液体碳氮共渗 5-36
5.1 设备的类型 2-36
1.2 耐热涂层设计 9-37
4.2 磨料粒度与类型选择 3-37
4.1 喷砂工艺参数选择指南 3-37
4 喷砂工艺参数的选择 3-37
2.3 离子碳氮共渗与真空碳氮共渗 5-37
2.4 碳氮共渗用钢与共渗后的热处理 5-37
2.5 碳氮共渗层组织和性能 5-37
1 工艺方法及涂层设计 9-37
1.1 工艺方法及涂料 9-37
2.1 防锈油脂应具备的性能 4-38
2 防锈油脂 4-38
2.2 防锈油脂的分类 4-38
6.1 设备类型 2-38
6 喷淋式涂装前处理设备 2-38
2 施工工艺流程设计 9-38
2.1 工艺流程设计 9-38
4.3 基体预热温度选择 3-38
2.3 耐温涂料涂装实例 9-39
1 概述 3-39
第4章 线材火焰喷涂39
5 基体表面的保护与遮蔽 3-39
2.2 涂装用主要工具和设备 9--39
6.2 设备结构 2-39
2.6 碳氮共渗件质量检验与常见缺陷及防止措施 5-40
2 线材火焰喷涂原理 3-40
3 线材火焰喷涂装置 3-40
3.1 喷枪 3-40
第3章 低温化学热处理40
第5章 长输管线的外防护41
3 成本估算 9-41
2.4 耐热涂料施工中可能出现的缺陷及防止方法 9-41
2.8 不良镍镀层的退除 6-41
3.1 性质和用途 6-42
3.2 氰化镀锌 6-42
1.2 涂层设计 9-42
3 镀锌 6-42
4.1 火焰形态和燃气流量的选择 3-42
4 线材火焰喷涂工艺 3-42
3.2 线材火焰喷涂装置供气系统 3-42
3 化学热处理及物理气相沉积 8-42
7 气相式除油清洗设备 2-42
2 其他有色金属的阳极氧化 7-42
2.1 镁合金的阳极氧化 7-42
1.1 工艺方法 9-42
1 工艺方法及涂层设计 9-42
2.1 工艺流程设计 9-43
第4章 涂装工艺和设备43
8.2 喷抛丸除锈清理设备的主要结构 2-43
1.3 热喷涂工艺参数对涂层摩擦学性能的影响 10-43
2 施工工艺流程设计 9-43
8 涂装前机械除锈喷抛丸设备 2-43
8.1 喷抛丸除锈清理设备的类型 2-43
4.2 喷涂时压缩空气的压力选择 3-43
1 低温化学热处理的特点和工艺方法 5-43
4.3 喷涂距离的选择 3-43
4.6 送丝速度与线材规格 3-44
3.3 锌酸盐镀锌 6-44
2.2 铜和铜合金的阳极氧化 7-44
4.5 喷涂角度的选择 3-44
4.4 基体的材质及规格 3-44
2.1 渗氮用钢及预备热处理 5-44
2 渗氮 5-44
2.3 管道防腐施工举例 9-44
2.2 施工主要工具和设备 9-44
5 线材火焰喷涂涂层 3-45
5.1 涂层特征 3-45
5.2 涂层的结合 3-45
6 线材火焰喷涂技术的应用 3-45
2.3 国外(美、英、日)防锈油脂的种类、质量和性能 4-45
6.1 轴及曲轴的修复 3-45
2.3 硅、锗、钽、锆、钛、锌和镉的阳极化 7-45
2.2 气体渗氮 5-45
1 概述 7-46
第3章 化学转化膜46
1.4 热喷涂(焊)层的摩擦学工业应用 10-46
6.5 材料表面改性 3-46
6.4 钢结构、储罐的长效保护 3-46
6.3 常用于机械零件表面强化和修复的耐蚀及耐磨材料 3-46
6.2 机械轴或辊表面修复及强化 3-46
2.4 钢的阳极氧化 7-46
3.4 氯化物镀锌 6-46
第5章 涂(膜)层厚度测量47
4 热喷涂(焊)涂层 8-47
2.1 钢铁的化学氧化(钢铁发蓝) 7-47
2 化学氧化法 7-47
第6章 复合管道48
2.4 选择防锈油的基本要点 4-48
2 堆焊 10-48
2.1 堆焊层的摩擦学特性 10-48
1.2 涂料的选用原则 2-48
1.1 涂层的分类 2-48
3 成本估算 9-48
1 涂装工艺设计原则 2-48
1.3 涂装方法的选用原则 2-48
1.4 涂装工艺设计原则 2-48
2喷涂(空气喷涂)工艺和喷漆室 2-49
2.1 空气喷枪的种类和选用 2-49
附录 常用线材的火焰喷涂工艺参数表 3-49
第5章 等离子喷涂49
1 等离子喷涂技术基础 3-49
1.1 等离子体基本概念 3-49
1.2 等离子的物理基础 3-49
2.2 钢铁化学发黑新工艺 7-50
2.2 堆焊层的摩擦学工业应用 10-50
1.3 等离子弧的形式和特征 3-50
2.3 离子渗氮 5-50
1.4 等离子喷涂的基本原理和特点 3-51
2.2 空气喷涂的工艺要点 2-51
3.5 镀锌层的钝化处理 6-51
3 化学热处理 10-52
1.5 等离子喷涂的分类 3-52
2 大气等离子喷涂 3-52
2.3 喷漆室 2-52
2.5 防锈油的使用方法和使用应注意事项 4-52
第4章 气相缓蚀剂和气相防锈材料52
2.1 特点 3-52
2.3 铝和铝合金的化学氧化 7-52
2.2 设备 3-52
3.1 概述 10-52
3.2 渗碳和碳氮共渗层 10-52
1 概述 8-53
1.1 涂(膜)层厚度测量方法的种类与特点 8-53
3.6 不良锌镀层的处理 6-53
4 镀锡 6-53
4.1 锡镀层的性质和用途 6-53
2 气相缓蚀剂的种类 4-53
1 气相缓蚀剂的特性 4-53
1.2 涂(膜)层厚度测量方法的选择 8-53
2.4 喷漆室辅助装置 2-53
2.4 其他渗氮方法 5-53
2.5 自动空气喷涂 2-54
3 静电喷涂工艺和静电喷涂设备 2-54
3.1 静电喷涂的特点 2-54
3 重要的气相缓蚀剂的成分和性能 4-54
4.2 碱性镀锡 6-54
3.1 气体氮碳共渗 5-55
3.3 渗硼层 10-55
1 衬橡胶管及管件 9-55
2 显微镜法测定涂(膜)层厚度 8-55
2.1 涂(膜)层横截面厚度显微镜测量 8-55
4.3 光亮硫酸盐镀锡 6-55
1.1 衬里用橡胶种类及牌号 9-55
3 氮碳共渗 5-55
3.2 静电喷枪的种类和选用 2-55
4 浸涂工艺和浸涂设备 2-56
4.1 浸涂的特点和用途 2-56
3.4 静电涂装的工艺条件 2-56
3.3 自动静电喷涂 2-56
1.2 衬里用橡胶的物理力学性能 9-56
4.2 浸涂设备 2-56
1.3 硫化橡胶的耐蚀性能 9-57
3 射线法涂(膜)层厚度测量 8-57
2.2 涂(膜)层横截面厚度扫描电子显微镜测量 8-57
1.4 衬里层选择及使用说明 9-57
5 电泳涂装工艺和设备 2-57
4.3 浸涂漆工艺条件 2-57
3.2 盐浴氮碳共渗的复合处理 5-57
3.1 X射线光谱测量方法 8-57
4 气相缓蚀剂的作用机理 4-57
5.1 电泳涂装的特点和用途 2-57
5.2 电泳涂装设备 2-57
1.5 管道、管件橡胶衬里的施工 9-58
4 涂(膜)层厚度的测厚仪测量 8-58
4.1 磁性法涂(膜)层厚度测量 8-58
4.2 涡流法涂(膜)层厚度测量 8-58
3.2 β反散射法 8-58
5 气相防锈材料的应用方式 4-58
5.1 气相防锈粉末、片剂、丸剂 4-58
3.4 渗金属层 10-58
4.4 氟硼酸盐镀锡 6-58
5.5 气相防锈油 4-58
5.4 气相防锈塑料薄膜 4-58
5.3 气相防锈纸 4-58
5.2 气相防锈水剂(溶液) 4-58
5.2 原理 6-59
5 镀铬 6-59
2.3 工艺 3-59
5.1 铬镀层的性质和用途 6-59
4.3 阳极溶解库仑法涂(膜)层厚度测量 8-59
1.6 衬胶对管道、管件的要求 9-59
5 化学溶解法涂(膜)层厚度测量 8-59
5.1 点滴法 8-59
5.2 液流法 8-59
5.3 称重法 8-59
4.1 渗硫 5-59
4 渗硫、硫氮共渗与硫氮碳共渗 5-59
5.3 镀铬液的种类 6-59
6 常用的气相缓蚀剂配方 4-59
6.1 常用的气相防锈纸及粉末和溶液的配方 4-59
6.2 气相防锈薄膜和气相防锈油的配方 4-59
5.7 气相防锈缓冲材料及其他气相防锈材料 4-59
5.6 气相防锈粘胶带 4-59
4.2 硫氮共渗及其与蒸气处理结合的复合处理 5-60
4.3 硫氮碳共渗 5-60
1 涂(膜)层表面粗糙度测定法的分类 8-60
第6章 涂(膜)层表面粗糙度的检验60
1.8 衬胶管、管件的安装和使用注意事项 9-60
1.7 橡胶衬里层质量检查 9-60
6.3 涂(膜)层厚度轮廓仪测量方法 8-60
6.2 微波法 8-60
6.1 电容法 8-60
6 涂(膜)层厚度其他测定方法 8-60
5.4 分析法 8-60
2.4 铜和铜合金的化学氧化 7-60
2 钢塑复合管道及管件 9-60
5.4 防护装饰性镀铬 6-60
3 低压等离子喷涂 3-60
3.1 特点 3-60
2.2 耐化学腐蚀性能 9-61
6.1 粉末涂装的特点和用途 2-61
5 低温化学热处理渗层组织与性能 5-61
5.1 渗层相组成 5-61
2 样板对照法 8-61
2.1 聚氯乙烯、聚丙烯力学物理性能 9-61
6 粉末静电喷涂工艺和设备 2-61
3.2 设备 3-61
5.3 电泳涂装管理 2-61
3.5 渗氮和氮碳共渗层 10-62
2.3 钢塑复合管道理化性能及耐蚀性 9-62
2.4 钢塑复合管成型工艺 9-62
5.2 力学性能 5-62
第5章 漆膜干燥工艺和设备62
6.2 静电粉末涂装设备 2-62
3 磷酸盐处理 7-62
7 国外气相缓蚀剂的种类、配方和有关技术规格 4-62
3.3 工艺 3-62
3.2 磷化膜形成的基本原理 7-62
3 显微镜调焦法和触针法 8-62
3.1 概述 7-62
3.4 低压等离子喷涂涂层性能 3-63
4 超音速等离子喷涂 3-63
4.1 特点 3-63
1 漆膜干燥方法 2-63
1.1 自然干燥 2-63
4.2 设备 3-63
2.5 钢塑复合管规格 9-63
1.2 人工干燥 2-63
3 玻璃内衬管道及管件 9-63
4 散斑法和扫描隧道显微镜(SIM)法 8-63
第7章 涂(膜)层的硬度检测63
2.7 钢塑复合管运输及安装要求 9-63
2.6 钢塑复合管质量检查 9-63
1 概述 8-64
2 直接硬度测量 8-64
2.1 温度 2-64
3.1 衬玻璃管及管件的性能 9-64
3.2 衬玻璃管及管件规格 9-64
2.2 干燥时间及升温梯度 2-64
2.3 空气湿度 2-64
4.3 工艺 3-64
2 影响漆膜干燥的因素 2-64
4.4 涂层特征 3-64
3.1 生产纲领和工件最大外形尺寸 2-65
3 间接硬度测量 8-65
2.4 空气流速 2-65
2.5 加热器与工件的距离 2-65
2.6 加热方式 2-65
3 漆膜人工干燥的设计原则 2-65
3.2 涂装工艺 2-65
3.3 涂料性质和涂层厚度 2-65
3.4 工件性质和形状 2-65
5 水稳等离子喷涂 3-65
5.1 特点 3-65
5.2 设备 3-65
5.5 功能性镀铬 6-65
3.3 衬制工艺 9-66
4 硬度测量技术的比较 8-66
5 应用 8-66
第8章 涂(膜)层结合强度的检测66
3.6 FeS减摩层 10-66
4.5 双行程或多行程烘干室 2-66
4.4 垂直升降式烘干室 2-66
4.3 桥式烘干室 2-66
4.2 直通式烘干室 2-66
4.1 固定式烘干室 2-66
4 干燥设备类别及其适应性 2-66
3.6 烘干室结构 2-66
3.5 能源状况和经济性 2-66
5.3 工艺 3-66
5.4 涂层特征 3-66
1 概述 8-67
6 等离子喷涂的应用 3-67
第6章 粉末等离子堆焊67
1 粉末等离子堆焊的技术基础 3-67
1.1 粉末等离子堆焊的基本原理 3-67
1.2 粉末等离子堆焊的特点 3-67
5 人工干燥设备能源选择 2-67
6 干燥设备加热器型式选择及其适应性 2-67
6.1 对流式加热器 2-67
6.2 辐射式加热器 2-67
2.1 堆焊电源 3-68
5.6 不良铬镀层的退除 6-68
2 结合力 8-68
3 理想的结合力检验要求 8-68
6.3 硫酸盐镀铁 6-69
3.3 磷化膜的性质 7-69
4 搪瓷管及管件 9-69
4.1 搪瓷管及管件的性能 9-69
2.2 电气控制系统 3-69
4 结合力测量 8-69
6.2 镀铁溶液的种类 6-69
6.1 铁镀层性质和用途 6-69
6 镀铁 6-69
8 使用气相防锈材料应注意事项 4-69
第5章 可剥性塑料69
3.4 衬玻璃管及管件质量检查 9-69
3.5 安装及使用注意事项 9-69
3.7 硫氮碳共渗层 10-70
1 热熔型可剥性塑料 4-70
1.1 热熔型可剥性塑料的特性 4-70
1.2 组分及其作用 4-70
6.4 氯化物镀铁 6-70
7 烘干设备结构 2-71
7.1 室体 2-71
4.2 搪瓷管及管件的规格 9-71
1.3 配方及配制方法 4-71
1.4 涂覆方法 4-71
5.3 耐腐蚀性能 5-71
2.3 等离子堆焊机床 3-72
第9章 涂(膜)层的内应力和应变的检测72
5 应用 8-72
3.8 钒氮硫共渗层 10-72
3.1 概述 6-172
7.2 加热系统 2-72
7.3 废气处理系统 2-73
5.4 抗腐蚀疲劳与腐蚀持久强度 5-73
7.1 镉镀层的性质和用途 6-73
7 镀镉 6-73
7.3 氰化镀镉 6-73
7.4 空气过滤器 2-73
7.2 常用镀镉溶液的种类 6-73
7.4 氨羧络合剂镀镉 6-74
1 概述 8-74
2 电镀层内应力的测定 8-74
2.1 挠度法 8-74
2.2 螺旋收缩仪法 8-74
第4章 电镀合金74
7.7 温度控制系统 2-74
7.6 风幕 2-74
7.5 热风循环系统 2-74
4 表面淬火 10-74
1 镀锌基合金 6-75
5 表面重熔和表面合金化层的摩擦磨损性能 10-75
8.1 固定式烘干室应用 2-75
2.4 喷枪气路系统 3-75
3 喷涂层内应力的测定 8-75
2.3 电阻应变法 8-75
1.1 镀锌镍合金 6-75
2.5 堆焊水路系统 3-75
3.4 各种金属的磷酸盐处理 7-75
8.2 直通式烘干室应用 2-75
第6章 涂装作业安全75
4.3 搪瓷管及管件的生产工艺 9-75
8 烘干室设备应用举例 2-75
4.5 搪瓷管和管件使用注意事项 9-76
2.2 组分及其作用 4-76
2.6 常用设备的技术参数及使用性能 3-76
4.4 搪瓷管及管件质量检验 9-76
2.3 配方及配制方法 4-76
5 聚四氟乙烯内衬管及管件 9-76
4 X射线衍射分析测定内应力的方法 8-76
2 溶剂型可剥性塑料 4-76
2.1 溶剂型可剥性塑料的特性 4-76
6 化学气相沉积(CVD)层的摩擦学性能 10-76
5.3 制造工艺 9-77
2.7 等离子堆焊枪 3-77
6 低温化学热处理工艺方法选择 5-77
1.2 镀锌钴合金 6-77
2.1 涂料不安全的因素 2-77
2 安全涂料及选择 2-77
1 涂装作业安全的重要性 2-77
第10章 涂(膜)层的孔隙率的检测77
5.2 规格 9-77
4.2 微观内应力的测定方法 8-77
6.2 低温化学热处理综合技术对比 5-77
6.3 几类典型工件的适用工艺 5-77
6.1 选择工艺方法的原则 5-77
5.1 衬F4管及管件的性能 9-77
4.1 宏观内应力的测定方法 8-77
第6章 环境封存78
2.4 涂覆方法 4-78
3 防毒安全 2-78
3.1 毒源与危害 2-78
1 充氮封存 4-78
2.2 安全涂料的选择 2-78
5.4 衬聚四氟乙烯管及管件质量检查 9-78
1 概述 8-78
2 电镀层孔隙率的检验 8-79
2 干燥空气封存 4-79
2.1 茧式包装 4-79
2.1 贴滤纸法 8-79
2.3 刚性容器干燥空气封存 4-79
2.2 封套式包装 4-79
1.3 镀锌铁合金 6-79
7 物理气相沉积(PVD)层的摩擦学性能 10-79
3.2 防毒技术措施 2-79
4 防火防爆安全 2-80
4.1 涂装作业中的危险物及性能 2-80
7.2 常见缺陷及防止措施 5-80
3 除氧封存 4-80
1 轴承防锈 4-80
2.2 涂膏法 8-80
第7章 热交换设备的腐蚀与防护80
5.5 安装及使用注意事项 9-80
第4章 渗硼与渗金属80
第7章 典型机械制品的防锈工艺80
7 质量检验、常见缺陷及防止措施 5-80
7.1 质量检验 5-80
3.1 等离子堆焊的主要工艺指标 3-81
3.1 浮力法 8-81
4.2 成膜基本原理 7-81
3.2 直接称量法 8-81
3 等离子堆焊工艺 3-81
4.1 概述 7-81
4.2 爆炸危险性及火灾危险的分级 2-81
3.2 主要工艺参数及其预选 3-81
3 喷涂层孔隙率的检验 8-81
4 钢铁的草酸盐处理 7-81
3.3 工艺动作程序及控制方式 3-81
8 离子注入层的摩擦学性能 10-81
1.4 镀锌钛合金 6-81
2.3 孔隙率的其他测试方法 8-81
1 热交换器的涂层防腐 9-82
1.1 涂层对换热效率的影响 9-82
1.2 涂层换热器涂料的选用 9-82
4.3 防火、防爆措施 2-82
1.5 镀锌锰合金 6-82
1 渗硼 5-82
1.1 渗硼方法与工艺 5-82
3.4 工件堆焊面毛坯的设计 3-82
3.5 合金粉末材料的选用 3-82
3.6 几种典型产品工艺规范 3-82
3.3 渗透液体的秤量方法 8-82
3.4 根据透气性进行比较的方法 8-82
第9篇 腐蚀防护与防腐工程设计第1章 大气腐蚀与防护82
1.6 镀锌铬合金 6-83
1.7 镀锌镍铁合金 6-83
2 机床防锈 4-83
5.2 基本原理 7-83
5.1 概述 7-83
5 锌、镉、铜及其他有色金属的铬酸盐处理 7-83
5.3 膜的基本性质 7-84
5.1 粉尘的来源及危害 2-84
2.1 性质和用途 6-84
5 防尘安全 2-84
3 量具与刃具防锈 4-84
5.2 防尘安全措施 8-84
1.8 镀锌铁钴合金 6-84
2 镀铜锌合金 6-84
1.3 施工工艺选择 9-84
1.4 施工方法分析 9-84
2.3 镀液配方和工艺规范 6-85
2.4 镀液配制方法 6-85
2.5 镀液各种成分的作用 6-85
2.2 铜锌合金电沉积原理 6-85
6.2 防静电安全措施 2-85
6 防静电安全 2-85
6.1 涂装作业中静电产生及危害 2-85
9 电镀和化学镀层的摩擦学性能 10-85
9.1 硬铬镀层及其复合镀层 10-85
1.2 渗硼用钢与渗后热处理 5-85
4 堆焊层质量缺陷及解决措施 3-85
2.8 槽液维护和故障处理 6-86
2.7 工艺条件的影响 6-86
2.6 添加剂 6-86
1.3 渗硼层的组织与性能 5-86
5 堆焊层质量检测 3-86
5.1 宏观检查 3-86
5.2 微观检查 3-86
第7章 电弧喷涂86
1.5 工艺质量要求 9-86
1.6 实用举例 9-86
7.1 涂装作业的噪声源 2-86
7 防噪声安全 2-86
4 汽车防锈 4-86
7.2 噪声治理的一般原则 2-87
2 粉末等离子堆焊设备 3-87
1 电弧喷涂原理及特点 3-87
1.1 电弧喷涂原理 3-87
1.2 电弧喷涂的主要特点 3-87
7.3 涂装作业的噪声治理 2-87
2.9 无氰镀液电镀铜锌合金 6-87
5 大型机械防锈 4-87
2 电弧喷涂设备 3-88
2.11 不良镀层的退除 6-88
5.4 各种金属的铬酸盐处理工艺 7-88
2.10 电镀铜锌合金镀层的后处理 6-88
2.1 电源 3-88
8.1 涂装作业中的腐蚀因素及危害 2-89
2.2 送丝系统 3-89
2.3 电弧喷涂枪 3-89
8 防腐蚀安全 2-89
6 光学仪器防锈 4-89
9.2 电镀和化学镀镍及镍基复合层 10-89
3.2 氰化物镀液电镀铜锡合金 6-89
3.1 性质和用途 6-89
3 镀铜锡合金 6-89
2 渗铝钢制热交换器 9-90
1.7 换热器涂层的防腐 9-90
3.2 电弧喷涂层材料选择 3-90
3.1 表面预处理 3-90
3 电弧喷涂工艺 3-90
2.4 控制系统 3-90
7 船舶防锈 4-90
2.1 浸铝钢管的加工工艺 9-90
8.2 防腐蚀安全措施 2-90
2.2 设计与制造过程中应注意的问题 9-91
2.3 应用 9-91
9.1 涂装作业中危及个人的因素 2-91
9 个人安全技术措施 2-91
3.3 喷涂 3-91
3.2 喷铝或锌结合涂层防护 9-91
3 热交换器的金属喷涂及其与涂层联合防护 9-91
9.2 个人安全技术措施 2-91
第7章 涂装作业环境保护91
3.1 喷铝防护 9-91
第8章 建、构筑物的腐蚀防护92
4 其他防护技术 9-92
1 建筑物的腐蚀防护 9-92
1.1 建、构筑物的腐蚀特点及影响因素 9-92
4.1 长效防腐涂层的应用 3-92
1 涂装作业环境污染及其控制原则 2-92
1.1 涂装作业中环境污染的来源 2-92
1.2 控制三废的原则 2-92
9 通用设备防锈 4-92
3.3 焦磷酸锡酸盐镀液电镀铜锡合金 6-92
3.4 后处理 3-92
4 电弧喷涂应用 3-92
8 飞机防锈 4-92
3.5 不良镀层的退除方法 6-93
1.4 渗硼共晶化处理 5-93
1.5 渗硼工业应用 5-93
2 涂装前处理除油废水处理 2-93
2.1 除油废水的来源和组分 2-93
1.6 渗硼工件的质量检验常见缺陷及防止措施 5-93
10 农业机械防锈 4-93
3.4 焦磷酸一两价锡盐镀液电镀铜锡合金 6-93
4.3 工业锅炉受热管件耐高温腐蚀涂层的应用 3-93
11 机械配件防锈 4-93
12 建筑五金防锈 4-93
13 手工工具防锈 4-93
第8章 火焰粉末喷熔及重熔93
4.4 电弧喷涂快速制模技术 3-93
4.2 机械零件修复与预保护 3-93
9.3 镀铜层及其复合镀层 10-94
14 家用金属制品防锈 4-94
1.2 建、构筑物腐蚀防护方法 9-94
1.2 火焰粉末喷熔材料及要求 3-94
2.2 除油废水处理方法 2-94
3 酸废水的处理 2-94
4 镀镍铁合金 6-94
4.1 性质和用途 6-94
4.2 镀液配方及工艺规范 6-94
1 火焰粉末喷熔技术基础 3-94
1.1 火焰粉末喷熔原理 3-94
6 常用化学转化膜典型工艺特征 7-95
2.2 火焰粉末喷焊枪 3-95
2.1 火焰粉末喷熔设备组成 3-95
2 火焰粉末喷熔及重熔设备 3-95
1.3 火焰粉末喷熔分类及特点 3-95
第4章 金属着色技术95
9.5 钴基复合镀层 10-95
9.4 镀铅层、镀锡层及其合金镀层 10-95
第8章 防锈包装95
16 库存产品防锈 4-95
15 露天材料防锈 4-95
4.3 镀液配制方法 6-95
4.4 镀液各成分的作用 6-95
1 概述 4-96
10.1 阳极氧化膜 10-96
4.5 工艺条件的影响 6-96
4.6 槽液维护和故障处理 6-96
4.7 不良镀层的退除方法 6-96
2.3 重熔枪 3-96
10 转化膜 10-96
2 防锈包装方法的选择 4-97
2.4 辅助设备 3-97
3.1 火焰粉末喷熔工艺流程 3-97
3.2 喷熔前准备 3-97
5.3 镀液的配制方法 6-97
5.2 镀液配方及工艺规范 6-97
5.1 镀层的性质和用途 6-97
5 镀铅锡合金及铅锡铜合金 6-97
4 电泳涂漆废水处理 2-97
3 火焰粉末喷熔及重熔工艺 3-97
2.1 防锈包装方法的分类 4-97
2.2 渗硅层的组织和性能 5-98
10.2 磷化膜 10-98
3.4 二步法喷熔及重熔工艺 3-98
2 建筑钢结构(包括桥梁)的腐蚀防护 9-98
第5章 耐磨表面工程技术的选用98
5.4 镀液各成分的作用 6-98
5.5 工艺条件的影响 6-98
5.6 常见故障及处理方法 6-98
2.1 渗硅方法与工艺 5-98
1 概述 7-98
2 渗硅 5-98
3.3 一步法喷熔工艺 3-98
6.1 性质和用途 6-99
2 摩擦学系统分析 10-99
1 选用的基本原则 10-99
5.7 铅锡合金镀层的钝化处理 6-99
6 镀铜锡锌合金 6-99
5.9 镀铅锡铜三元合金 6-99
5.8 不良铅锡合金镀层的退除 6-99
3 表面保护覆层类型的确定 10-99
2 铝和铝合金的阳极氧化的着色处理 7-99
3.5 火焰粉末喷熔后工件的冷却措施 3-99
2.1 自然发色法 7-99
3.1 表面保护覆层类型选择专家系统的结构 10-99
3.6 铸铁件的喷熔修补 3-100
37 喷熔层产生缺陷的原因和防止措施 3-100
5 喷漆室废水处理 2-100
6.3 电镀仿金三元合金工艺 6-100
6.2 电镀银白色铜锡锌三元合金 6-100
2.2 封存包装级别 4-100
3.1 基础与设备基础的防护 9-100
5.1 喷漆室废水的特点 2-100
2.2 电解着色法 7-100
5.2 处理方法 2-100
6 涂装溶剂废气处理 2-100
6.1 溶剂废气的来源及特点 2-100
6.2 废气处理方法 2-100
3 建筑物厂房的防护 9-100
6.5 镀后处理 6-101
2.3 防锈包装一般技术要求及方法实施要点 4-101
2.3 渗硅工业应用 5-101
2.4 渗硅层常见缺陷及防止措施 5-101
3 渗铝 5-101
6.4 镀液的维护与控制 6-101
4 火焰粉末喷熔工艺的应用 3-101
1 火焰粉末喷涂技术基础 3-101
第9章 火焰粉末喷涂101
1.1 气体燃烧火焰基础 3-101
6.6 仿金镀液的常见故障及处理方法 6-102
3.1 渗铝方法与工艺 5-102
1.3 火焰的形貌、构成和性质 3-102
1.2 回火预防措施 3-102
3.2 楼面与地面的防护 9-102
7.1 镀金钴合金 6-102
7 镀金合金 6-102
1.4 (焰温度 3-103
7.2 镀金银合金 6-103
3 防锈包装材料的选择 4-103
2 火焰粉末喷涂的原理及分类 3-104
2.1 火焰粉末喷涂的原理 3-104
2.3 吸附染色法(化学染色法) 7-104
2.2 火焰粉末喷涂方法分类 3-104
3 普通火焰粉末喷涂 3-104
7.3 镀金镍合金 6-104
7.4 镀金铜合金 6-104
3.1 包装纸 4-104
3.2 塑料薄膜及复合包装材料 4-104
3.3 包装容器 4-104
3.2 热浸渗铝 5-105
3.3 地沟、地坑及贮槽的防护 9-106
3.2 类型选择算法的说明 10-106
1 涂装生产线的类别 2-106
4.1 原理 3-106
8.1 电镀镍磷合金 6-106
8 非晶态合金电镀 6-106
7.5 镀金铜镍、金铜镉合金 6-106
7 涂装前处理含酸废气治理 2-106
第8章 涂装生产线106
4 塑料粉末火焰喷涂 3-106
8 涂装废渣处理 2-106
1.3 往复移动式涂装生产线 2-107
2.3 工艺时间对生产线的影响 2-107
1.1 连续式涂装生产线 2-107
3.4 衬垫、缓冲材料 4-107
1.2 间歇式涂装生产线 2-107
2.1 年生产纲领的挂具数 2-107
3.1 涂装生产线的组成 2-107
2 连续式涂装生产线生产能力的确定 2-107
2.2 挂具间距(T) 2-107
3 涂装生产线的区划与设备布置 2-107
4.3 火焰喷塑工艺 3-107
4.2 火焰喷塑设备 -107
第9章 防腐工程预算107
3.4 厂房墙、柱、梁板等的防护 9-107
3.1 概述 7-108
3 铜和黄铜层的着色 7-108
8.2 电镀镍硫合金 6-108
3.3 着色工艺举例 7-108
8.3 电镀铁钼合金 6-108
3.2 着色前处理 7-108
4.4 涂层后处理 3-108
4 涂装机器人的应用 2-109
3.3 渗铝层的组织与性能 5-109
4.3 涂装机器人的结构 2-109
4.2 涂装机器人的分类 2-109
4.1 涂装机器人的使用概况 2-109
5.1 高速火焰粉末喷涂工作原理 3-109
3.2 涂装生产线上设备的布置 2-109
4.5 涂层质量检验 3-109
4.6 火焰喷塑涂层应用 3-109
9.1 镀锡锌合金 6-109
9 镀其他合金 6-109
5 高速火焰粉末喷涂 3-109
4 镍层的着色和染色 7-110
4.1 镍层的着色 7-110
4.2 镍层的染色 7-110
5 锌层的着色和染色 7-110
5.1 锌层着色 7-110
4.5 涂装机器人与生产线的组合 2-110
4.4 涂装机器人的性能及规格 2-110
1.1 直接费 9-110
3.5 干燥剂的种类及性能 4-110
1 建筑安装工程费的组成 9-110
5.3 高速火焰喷涂涂层特征 3-110
5.2 高速火焰粉末喷涂设备组成 3-110
5.2 锌层染色 7-111
第11章 涂层的后处理与加工111
1 涂层的后处理 3--111
1 热喷涂金属表面预处理方面标准 3-111
第10章 热喷涂技术检验和试验方法标准111
6 火焰粉末喷涂技术应用 3-111
9.2 镀锡镍合金 6-111
2 热喷涂涂层材料方面标准 3-111
3 热喷涂涂层及性能检测方面标准 3-111
1.2 间接费 9-111
2 建筑安装工程预算定额 9-112
1.3 计划利润 9-112
1.4 税金 9-112
1.5 其他直接费 9-112
9.3 镀锡钴合金 6-112
9.4 镀镍钴合金 6-112
2.1 建筑安装工程定额及其计算 9-112
6.3 不锈钢着色举例 7-112
6.2 不锈钢氧化着色法原理 7-112
6.1 概述 7-112
6 不锈钢着色 7-112
2.2 热喷涂涂层的切削加工 3-113
3.4 渗铝工业应用 5-113
5 涂装生产线实例 2-113
第9章 涂装车间工艺设计113
7.1 银层着色 7-113
7 其他镀层的着色与染色 7-113
2 热喷涂涂层的机械加工 3-113
2.1 涂层机械加工特点 3-113
7.2 锡层着色 7-114
7.3 镉层的着色和染色 7-114
第5章 特种电镀114
9.5 镀银基合金 6-114
2.2 单位估价表 9-114
第5章 转化膜工艺质量控制114
2.3 刷油、绝热、防腐蚀工程预算定额 9-115
1 复合镀 6-115
1.1 概述 6-115
3.5 渗铝件的质量检验、常见缺陷及防止措施 5-115
4 渗铬 5-115
4.1 渗铬方法与工艺 5-115
1 转化膜的检验 7-115
1.1 铝和铝合金的阳极氧化膜的检验 7-115
2 涂装车间工艺设计的阶段、程序与设计文件 2-116
3.1 概述 9-116
3 防腐保温施工图预算的编制 9-116
2.4 工业建筑防腐蚀工程预算定额 9-116
1 概述 2-116
2.3 涂层的机加工工艺 3-116
2.1 设计阶段与程序 2-116
2.2 各设计阶段中工作的主要内容 2-116
4.1 检验管理 4-116
4 封存包装的质量控制和有关标记 4-116
3.6 湿度指示剂 4-116
2.4 喷涂层的磨削加工及工艺 3-116
4.3 包装标记 4-117
3.2 除锈、刷油施工图预算的编制 9-117
5.2 涂装 4-118
5.1 涂装前表面预处理 4-118
4 表面保护覆层类型的评价 10-118
5 应用实例:大型出口锅炉、电站成套设备防锈包装 4-118
1.2 复合电镀基本原理 6-118
4.1 技术性评价 10-118
2.3 涂装车间初步设计文件(工艺部分)目录 2-118
5.3 防锈的要求与方法 4-119
3.3 工作制度与年时基数 2-119
3.2 项目投资和建筑面积 2-119
3.1 生产纲领 2-119
第12章 热喷涂安全与防护119
2.6 涂层其他加工方法 3-119
2.5 自熔合金焊层磨削工艺的选择 3-119
3 涂装车间工艺设计的基本限制条件 2-119
2.4 涂装车间施工图设计文件(工艺部分)目录 2-119
4 涂装车间工艺设计中需解决的重点问题 2-120
4.1 涂装车间在全厂中位置的确定 2-120
3.6 国家有关法律、法令、政策 2-120
4.2 涂料品种的选择 2-120
第9章 防锈封存与包装材料的检验方法与分析方法120
1 概述 3-120
2 热喷涂设备的安全使用与防护 3-120
2.1 热喷涂用气体 3-120
2 防锈油脂的检验方法 4-120
1 防锈与包装材料的取样规定 4-120
5.4 包装 4-120
3.4 涂漆标准 2-120
3.3 防腐蚀施工图预算的编制 9-120
4.2 经济性评价 10-120
第10篇 表面工程技术的摩擦学工业应用第1章 概 述第2章 摩擦、磨损的产生120
3.5 项目工厂自身的限制条件 2-120
2.2 喷枪 3-121
4.2 渗铬层的组织与性能 5-121
1.2 磷酸盐膜的检验 7-121
4.4 涂装工艺流程及设备的确定 2-121
4.3 表面保护覆层的磨损特征值汇集 10-121
4.1 工件表面预处理安全防护 3-121
4 热喷涂的操作安全 3-121
2.3 喷砂机 3-121
3 热喷涂材料的安全使用与防护 3-121
1.3 复合电镀工艺 6-121
4.5 涂装车间工艺平面布置 2-121
4.3 涂装作业的组织形式 2-121
4.6 公用动力耗量的计算与确定 2-122
4.2 操作场地的安全性 3-122
4.3 热喷涂操作者的安全与防护 3-122
附录 3-122
第4篇 防锈封存与包装第1章 金属表面的预处理122
1.4 复合电镀应用 6-123
1.3 铬酸盐膜的检验 7-124
11 苏打水的分析 4-124
参考文献 2-124
第3篇 热喷涂第1章 热喷涂的原理和方法124
3 气相缓蚀剂主要试验方法 4-124
4.7 涂装车间对土建的要求 2-124
2 转化膜处理液的检测 7-126
2.1 铝和铝合金阳极氧化电解液的分析 7-126
4 气相防锈纸试验方法 4-128
5 应用实例 10-128
2.2 磷酸盐处理液的检验及试验方法 7-128
5 通用水基金属净洗剂试验方法 4-129
4.3 渗铬用钢与合金及渗后热处理 5-130
6 乳化液试验方法 4-130
1.5 复合化学镀 6-130
4.4 渗铬工业应用 5-131
4.5 渗铬工件的质量检验、常见缺陷及防止措施 5-131
7 包装材料试验方法 4-131
9 压敏胶粘带性能测试方法 4-132
8 可剥性塑料性能测试方法 4-132
5 渗锌 5-132
5.1 渗锌方法与工艺 5-132
2.3 草酸处理液的分析 7-132
3 转化膜标准规范 7-132
2.4 铬酸处理液的分析 7-132
10 纸张的试验方法及其标准号 4-133
3.1 关于铝上氧化膜的标准 7-133
2 刷镀 6-134
2.1 概述 6-134
2.2 刷镀原理 6-134
12 乳化液的分析 4-134
第8篇 表面涂(膜)层质量检测技术第1章 涂(膜)层及界面特性的表面分析方法134
3.2 关于磷酸盐膜的标准 7-134
3.3 关于铬酸盐膜的标准 7-134
5.2 热浸锌 5-134
13 碳酸钠-亚硝酸钠防锈液的分析 4-135
16 15号气相剂的分析 4-135
15 三乙醇胺-苯甲酸钠防锈液的分析 4-135
14 三乙醇胺-亚硝酸钠防锈液的分析 4-135
2.3 刷镀设备 6-135
5.3 渗锌层的组织与性能 5-135
17 酸洗溶液的分析 4-136
5.4 渗锌工艺应用 5-137
2.4 镀件的表面准备 6-137
6 渗钒、渗钛、渗铌与渗钽 5-138
2.6 刷镀镀层的设计要求 6-138
附录 4-138
附录A 防锈技术有关的一些产品及试验方法的国内外标准 4-138
6.1 碳化物型覆层的形成模式 5-138
6.2 碳化物型覆层方法与工艺 5-138
2.5 刷镀液 6-138
6.4 渗钛 5-139
6.3 渗钒 5-139
3.1 概述 6-139
3 电铸 6-139
2.7 刷镀工艺条件 6-139
6.5 碳化物型覆层的组织与性能 5-140
3.3 芯模 6-140
3.2 电铸的应用 6-140
3.4 电铸溶液 6-141
4.2 热机械镀锌(干法) 6-143
4 机械镀 6-143
3.5 电铸后处理 6-143
4.3 冷机械镀锌 6-143
4.1 概述 6-143
附录B油溶性缓蚀剂一览表 4-143
6.6 碳化物覆层工业应用 5-144
5.2 适用电镀层罩光的有机涂料种类和特点 6-145
5.1 概述 6-145
5 电镀-有机涂层 6-145
7.1 硼和其他元素共渗与复合渗 5-146
5.3 涂层施工方法 6-146
7 共渗、复合渗与镀渗复合 5-146
6 彩色电镀 6-147
6.2 仿古系列 6-150
7.2 铝和其他元素共渗与复合渗 5-150
6.3 黑色系列 6-151
7.3 铬和其他元素共渗与复合渗 5-151
7.1 概述 6-153
附录C防锈油脂配方一览表 4-153
7 脉冲电镀 6-153
7.2 脉冲镀银 6-154
7.3 脉冲镀金 6-154
8 高速电镀 6-155
8.1 概述 6-155
7.4 脉冲镀镍 6-155
8.2 铜带、铜引线电镀光亮锡 6-156
8.3 铜引线电镀铅锡合金 6-156
8.4 钢带、钢线电镀锌 6-156
8.5 钢带、黄铜带镀镍 6-156
8.6 铜带、铜引线快速镀银 6-157
8.7 喷流法高速局部镀金 6-157
第6章 特殊基材上的电镀157
1 锌合金压铸件的电镀 6-157
1.1 概述 6-157
1.2 前处理 6-158
第5章 气相沉积158
7.4 镀渗复合 5-158
1 概述 5-159
2.2 真空蒸镀 5-161
2.1 物理气相沉积种类与特点 5-161
2 物理气相沉积 5-161
1.3 预镀 6-161
1.4 锌合金压铸件上的电镀 6-163
1.5 不合格镀层的退除方法 6-163
2.3 离子镀 5-163
2 铝件电镀 6-164
2.1 概述 6-164
2.2 镀前预处理 6-165
2.4 溅射镀 5-166
2.3 钎焊铝零件镀前预处理 6-166
2.4 中间处理 6-167
2.5 预镀 6-171
2.6 直接镀 6-171
2.7 退镀 6-171
3.1 化学气相沉积的原理及特点 5-171
3 化学气相沉积 5-171
3 铁基粉末冶金件电镀 6-172
3.2 封孔法 6-172
3.2 化学气相沉积的装置 5-172
3.3 化学气相沉积工艺及影响覆层的因素 5-172
第7章 电镀工程与基础实践173
3.3 喷砂与滚光 6-173
1.2 挂具常用的金属材料 6-174
1.1 挂具设计原则 6-174
1 电镀挂具 6-174
4.1 等离子体化学气相沉积的原理及持点 5-175
4.3 等离子体化学气相沉积的装置与工艺参数 5-175
4 等离子体化学气相沉积 5-175
第5篇 化学热处理及新型表面改性技术第1章概 论175
附录D液体手套 4-175
1.3 挂具材料截面的计算 6-175
4.2 等离子体化学气相沉积的种类及其特点比较 5-175
1.6 零件形状对电流分布的影响 6-175
1.4 挂具的导电接触 6-175
1.5 设计挂具考虑电流分布影响 6-175
1.7 阴阳极之间电流分布影响 6-175
1.8 通用挂具形式和结构 6-176
1.9 挂具制造和使用时应注意的事项 6-176
5.1 沉积层的组织结构与特性 5-177
1.10 专用挂具形式和结构 6-177
5 气相沉积层的组织与性能 5-177
1.12 绝缘处理方法 6-178
5.2 沉积层的摩擦磨损性能 5-178
1.11 挂具的绝缘处理 6-178
2 镀槽设计与安装 6-179
2.1 镀槽设计 6-179
2.2 钢槽 6-181
2.3 硬聚氯乙烯塑料槽 6-182
5.3 沉积层的切削性能、应力与疲劳性能 5-184
5.4 沉积层的耐腐蚀性能与抗高温氧化性能 5-185
2.4 钢槽的衬里 6-186
5.5 沉积层的装饰性 5-186
2.5 非金属材料的耐腐蚀性能 6-188
5.6 沉积层的其他性能 5-188
6 气相沉积的工业应用 5-188
第6章 高能束表面改性188
2.6 镀槽的材料选用 6-190
1.2 激光表面改性的原理与装置 5-190
1.1 激光表面改性分类与特点 5-190
1 激光表面改性 5-190
2.7 碳钢的耐腐蚀性能 6-191
2.8 不锈钢的耐腐蚀性能 6-192
1.3 激光表面淬火 5-193
2.9 铅及铅合金的耐腐蚀性能 6-193
2.10 钛的耐腐蚀及其他性能 6-194
2.12 耐酸陶瓷 6-195
2.11 常用耐腐蚀材料的耐腐蚀性能 6-195
1.4 激光表面合金化及其他激光表面改性 5-196
2.13 耐酸搪瓷 6-196
2.14 有机玻璃 6-197
3.1 蒸汽加热装置 6-198
3 加热及冷却设备 6-198
2.15 铸石与铸石粉耐酸混凝土、花岗石 6-198
3.3 热交换器加热 6-200
3.2 槽液温度自动控制 6-200
3.5 溶液冷却装置 6-201
3.4 燃油、燃气加热设备 6-201
3.6 制冷剂与冷媒 6-202
4.1 干燥设备 6-203
4 干燥设备及其他辅助设备 6-203
1.5 激光表面改性工业应用 5-205
4.2 其他辅助设备 6-206
2.1 电子束加热的原理与设备 5-207
2 电子束表面改性 5-207
2.2 电子束表面改性的特点与工艺控制 5-207
2.3 电子束改性层的性能及应用 5-208
4.3 无油吹吸两用气泵 6-209
4.4 微电脑自动药液添加机 6-210
3 离子注入 5-211
3.1 离子注入的原理与特点 5-211
3.2 离子注入装置 5-211
4.5 pH自动测量控制仪 6-211
4.6 电镀用电热元件 6-211
4.7 各种整流器 6-211
4.9 各种镀层测厚仪 6-213
4.8 制造纯水设备 6-213
5 线材电镀设备 6-213
6 半自动及自动生产线 6-213
3.3 离子注入工艺及注入层的性能 5-213
6.1 半自动生产线 6-214
6.3 直线式电镀自动线 6-214
6.2 自动生产线 6-214
6.4 环形电镀自动线 6-215
6.5 滚镀设备 6-217
第8章 电镀车间工艺设计217
3.4 离子注入技术的工业应用 5-223
1 总则 6-224
2 工艺资料的收集 6-224
3 车间设置位置 6-224
第6篇 电 镀第1章 概 论224
3.5 离子束沉积注入新技术 5-224
6 设备的选用及设计要求 6-225
5.3 设备尺寸规格的确定 6-225
5.2 设备的确定 6-225
5.1 工艺方法的确定 6-225
5 工艺方法及设备的确定 6-225
4.3 工人年时基数 6-225
4.2 设备年时基数 6-225
4.1 工作制度 6-225
4 工作制度及年时基数 6-225
7 车间区划及设备布置 6-226
8 厂房形式、跨度及高度 6-227
9 人员计算 6-227
10 车间面积及人员分类 6-227
11 动力消耗量的计算 6-228
12 其他要求 6-228
第7篇 转化膜技术第1章 概述228
1998《表面工程手册 第1篇 表面调整及净化》由于是年代较久的资料都绝版了,几乎不可能购买到实物。如果大家为了学习确实需要,可向博主求助其电子版PDF文件(由李国英 1998 北京:机械工业出版社 出版的版本) 。对合法合规的求助,我会当即受理并将下载地址发送给你。
高度相关资料
-
- 表面化学
- 1991 厦门:厦门大学出版社
-
- 表面工学讲座1 表面の构造
- 昭和46年7月第1版 朝仓书店
-
- 表面和胶体化学手册
- 1999 世界图书出版社
-
- 简明表面处理工手册
- 1995 北京:机械工业出版社
-
- 表面工程论文集
- 1987 大连:大连工学院出版社
-
- 化工产品手册 10 工业表面活性剂
- 1999 北京:化学工业出版社
-
- 金属表面强化技术 金属表面工程学
- 1989 北京:机械工业出版社
-
- 表面工程
- 1989 上海:上海交通大学出版社
-
- 表面工学
- 1976 养贤堂株式会社
-
- 表面处理工艺手册
- 1991 上海:上海科学技术出版社
-
- 表面工程与维修
- 1996 北京:机械工业出版社
-
- 铝表面处理手册
- 1988 长沙:中南工业大学出版社
-
- 金属表面工程学
- 1995 北京:兵器工业出版社
-
- 等离子体表面工程
- 1991 北京:中国科学技术出版社
-
- 实用表面工程技术
- 1998 北京:新时代出版社
提示:百度云已更名为百度网盘(百度盘),天翼云盘、微盘下载地址……暂未提供。➥ PDF文字可复制化或转WORD