《实用表面工程技术》
作者 | 谭昌瑶,王钧石主编 编者 |
---|---|
出版 | 北京:新时代出版社 |
参考页数 | 312 |
出版时间 | 1998(求助前请核对) 目录预览 |
ISBN号 | 7504203645 — 求助条款 |
PDF编号 | 87574928(仅供预览,未存储实际文件) |
求助格式 | 扫描PDF(若分多册发行,每次仅能受理1册) |
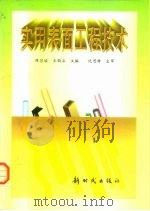
第一章绪论1
1.1 表面工程技术的内涵1
1.2 表面工程技术在国民经济及四化建设中的意义1
1.3 表面工程技术的分类2
第一篇基础理论4
第二章 金属表面的物理化学特征4
2.1 金属材料表面与内部的区别4
2.2 材料表面的功能5
2.3.2 钝化现象及作用6
2.3.1 金属材料表面膜的效应6
2.3 金属材料表面膜的形成及钝化作用6
第三章 金属的腐蚀与防腐8
3.1 金属腐蚀的分类及破坏形式8
3.1.1 金属腐蚀的分类8
3.1.2 金属腐蚀的破坏形式8
3.2 金属腐蚀的基本原理9
3.2.1 金属腐蚀的过程9
3.2.2 金属腐蚀的形式10
3.3 电极电势与极化作用13
3.3.1 金属的电极电势13
3.3.2 极化作用与腐蚀速度16
3.4 控制腐蚀的方法18
3.4.1 提高材料的热力学稳定性18
3.4.2 增强阳极极化19
3.4.3 增强阴极极化19
3.4.4 防腐涂层的利用20
第四章 金属的磨损22
4.1 磨损概述22
4.1.1 磨损的含义22
4.1.2 磨损的分类22
4.2 影响磨损的因素22
4.2.1 服役条件的影响23
4.2.2 材料本身性质的影响24
4.3 耐磨材料的选择28
第二篇电镀、化学镀、化学转化膜及表面着色技术30
第五章 电镀30
5.1 概述30
5.2 镀前处理30
5.2.1 表面整平30
5.2.2 脱脂32
5.2.3 酸洗32
5.2.4 活化(弱浸蚀)33
5.3.1 镀镍34
5.3 单金属电镀工艺34
5.3.2 镀铬39
5.3.3 镀锌43
5.3.4 镀铜48
5.3.5 镀锡52
5.4 镀层的后处理54
5.4.1 镀锌层的后处理54
5.4.2 其他后处理57
5.4.3 不良镀层的退除58
5.5.1 工艺槽61
5.5 施工设备与工装61
5.5.2 挂具62
5.5.3 电源设备63
5.5.4 过滤设备63
5.5.5 其他设备64
5.6 镀层质量的检验65
5.6.1 外观检验65
5.6.2 结合力检验65
5.6.3 厚度检验65
5.6.4 孔隙率检验66
5.7.1 分析故障的一般方法67
5.7 故障处理67
5.6.5 腐蚀性检验67
5.7.2 净化处理镀液的方法69
5.7.3 常见故障及处理方法69
5.8 电镀废液、废气的治理与环境保护70
5.8.1 电镀废液的治理71
5.8.2 电镀废气的治理71
第六章 电镀及其进展73
6.1 概述73
6.2 合金电镀73
6.2.1 合金镀层的特点和分类73
6.2.2 合金电镀工艺要领74
6.3 复合电镀82
6.3.1 复合电镀的特点82
6.3.2 复合镀层的沉积原理83
6.3.3 复合电镀的工艺要领84
6.4 非晶态电镀88
6.4.1 概述88
6.4.2 非晶态的构造88
6.4.3 电镀非晶态工艺要领及应用实例89
6.5 电刷镀90
6.5.1 电刷镀的兴起及应用前景90
6.5.2 电刷镀的原理及特点91
6.5.3 电刷镀电源93
6.5.4 电刷镀溶液95
6.5.5 电刷镀工艺要领98
6.5.6 电刷镀层的组织与性能101
6.6 低温镀铁102
6.6.1 镀铁原理102
6.6.2 镀铁工艺104
6.6.3 影响镀铁层性能的因素107
6.7 塑料及其他非金属上的电镀109
6.7.1 ABS塑料的电镀110
6.7.2 石膏与木材的电镀112
6.7.3 玻璃与陶瓷的电镀113
第七章 化学镀116
7.1 概述 .116
7.2 化学镀镍116
7.2.1 次磷酸钠化学镀镍116
7.2.2 硼氢化物化学镀镍119
7.2.3 胺基硼烷和肼化学镀镍120
7.3 化学镀铜122
7.4 化学镀钴125
7.4.1 次磷酸钠化学镀钴125
7.5 化学镀银126
7.4.2 硼氢化物和肼化学镀钴126
7.6 化学镀金128
7.7 化学镀锡129
7.8 化学镀合金130
7.8.1 化学镀镍基合金130
7.8.2 化学镀钴基合金132
7.9 化学复合镀133
8.2 钢铁零件的氧化——发蓝135
8.2.1 氧化膜生成机理135
8.1 概述135
第八章 化学转化膜技术135
8.2.2 钢铁零件发蓝的工艺流程136
8.3 钢铁零件的磷化138
8.3.1 磷化膜生成机理138
8.3.2 钢铁零件磷化的工艺流程139
8.4 铝及其合金的氧化141
8.4.1 概述141
8.4.2 防护装饰性氧化142
8.4.3 硬质阳极氧化149
8.4.4 瓷质阳极氧化150
8.4.5 封闭处理152
9.1.1 化学染色原理155
9.1 金属表面着色原理155
第九章 金属表面着色技术155
9.1.2 电解着色原理156
9.2 铝及其合金氧化膜的着色156
9.2.1 化学染色156
9.2.2 电解着色159
9.3 铜及其合金的着色161
9.3.1 着色机理161
9.3.2 铜的着色162
9.3.3 黄铜的着色162
9.4 不锈钢的着色164
第三篇涂装新技术167
第十章 新型涂料167
10.1 涂料的新进展167
10.2 涂料的基本构成168
10.2.1 主要成膜物质168
10.2.2 次要成膜物质168
10.2.3 辅助成膜物质169
10.3 涂料的种类、性能与新型涂料170
11.2 有机涂料防护原理174
11.1.1 物理成膜机理174
11.1.2 化学成膜机理174
11.1 有机涂料成膜机理174
第十一章 涂装新工艺174
11.3 无机涂层175
11.4 新型涂装方法176
11.4.1 涂装前表面处理176
11.4.2 涂装新方法176
第四篇表面扩散渗入处理技术182
第十二章 表面扩散渗入处理原理182
12.1 表面扩散渗入处理工艺分类182
12.2 表面扩散渗入处理工艺的基本过程183
12.2.2 界面层中的外扩散184
12.2.1 介质中的化学反应184
12.2.3 表面吸附与界面反应185
12.2.4 内扩散185
第十三章 渗硼及新进展186
13.1 概述186
13.1.1 渗硼的简要原理186
13.1.2 渗硼层的组织与性能186
13.1.3 渗硼工艺分类188
13.2 渗硼工艺188
13.2.1 固体法渗硼188
13.2.2 影响渗硼工艺的因素191
13.3.1 渗硼层的检验192
13.3 渗硼层的检验及组织缺陷192
13.2.3 渗硼工艺的应用范围192
13.3.2 渗硼层的组织缺陷及预防措施193
13.4 以渗硼为主的复合渗194
13.4.1 硼铝共渗194
13.4.2 硼氮共渗194
13.4.3 硼锆共渗194
13.4.4 硼钒共渗195
14.1.2 渗碳工艺分类196
14.1.1 渗碳的原理196
14.1 概述196
第十四章 渗碳及新进展196
14.1.3 渗碳用钢197
14.2 渗碳工艺198
14.2.1 渗碳前的准备工作198
14.2.2 碳势的测量与控制199
14.2.3 气体渗碳工艺201
14.2.4 固体渗碳工艺202
14.2.5 渗碳后的热处理203
14.2.6 影响渗碳的因素204
14.3.2 渗碳件的组织缺陷及预防措施205
14.3.1 渗碳层的检验205
14.3 渗碳层的检验及组织缺陷205
第十五章 渗氮及其新进展206
15.1 概述206
15.1.1 渗氮的原理206
15.1.2 影响渗氮工艺过程的因素208
15.1.3 渗氮工艺分类209
15.2 渗氮工艺210
15.2.1 渗氮前的准备工作210
15.2.2 气体渗氮工艺211
15.2.3 加速渗氮的途径212
15.3.1 渗氮层的检验214
15.3 渗氮层的检验及组织缺陷214
15.3.2 渗氮层的组织缺陷及预防措施215
第十六章 其余表面扩散渗入处理工艺217
16.1 软氮化217
16.1.1 软氮化的原理及特点217
16.1.2 软氮化工艺217
16.2 碳氮共渗219
16.2.1 碳氮共渗的原理219
16.2.2 气体碳氮共渗工艺219
16.3.1 渗硫的原理221
16.3.2 渗硫工艺221
16.3 渗硫221
16.4 渗铝222
16.4.1 渗铝的原理222
16.4.2 渗铝工艺223
第五篇热喷涂表面覆盖技术224
第十七章 热喷涂概论224
17.1 概述224
17.2 热喷涂技术的特点225
17.3 热喷涂的基本原理226
18.1.1 等离子喷涂设备229
18.1 热喷涂设备229
第十八章 热喷涂设备和材料229
18.1.2 氧-乙炔火焰喷涂设备231
18.1.3 线丝材喷涂设备234
18.2 热喷涂材料235
18.2.1 合金粉末材料236
18.2.2 陶瓷粉末材料239
18.2.3 热喷涂线材241
第十九章 热喷涂工艺243
19.1 等离子喷涂工艺245
19.1.1 等离子喷涂的基本原理和特点246
19.1.2 等离子喷涂工艺参数的选择248
19.2 氧-乙炔喷涂工艺250
19.2.1 氧-乙炔喷涂的基本原理和特点250
19.1.3 具体工艺实例250
19.2.2 氧-乙炔喷涂工艺参数选择252
19.3 涂层后处理255
19.3.1 封孔处理255
19.3.2 重熔处理256
19.3.3 强化处理257
19.3.4 扩散处理257
20.1.1 热喷涂层组织形态258
20.1.2 强化机理258
20.1 热喷涂层组织258
第二十章 热喷涂层组织与性能258
20.1.3 涂层组织控制259
20.2 涂层性能259
20.2.1 外观259
20.2.2 抗拉强度259
20.2.3 残余应力和涂层厚度260
20.2.4 硬度260
20.2.5 抗磨性260
20.2.6 耐蚀性和耐高温氧化性261
21.1.2 抗磨损的应用262
21.1.1 在机械零件尺寸恢复上的应用262
第二十一章 热喷涂的应用及新进展262
21.1 热喷涂的应用262
21.1.3 抗腐蚀的应用263
21.1.4 在电器上的应用263
21.1.5 装饰方面的应用263
21.2 热喷涂的新进展263
21.2.1 等离子喷涂技术263
21.2.2 线丝材火焰喷涂264
21.2.3 粉末火焰喷涂264
21.2.4 热喷涂新方法、新工艺264
22.1 物理气相沉积特点265
22.2 真空蒸发镀膜265
第六篇新型表面改性技术265
第二十二章 物理气相沉积265
22.2.1 蒸镀前的处理266
22.2.2 蒸发源266
22.2.3 合金、化合物的蒸镀方法268
22.3 溅射镀膜269
22.3.1 溅射镀膜的原理269
22.3.2 溅射镀膜方法269
22.4.1 离子镀膜原理及特点272
22.4 离子镀膜272
22.3.3 合金膜和化合物膜的镀制272
22.4.2 活性反应离子镀274
22.4.3 空心阴极离子镀274
第二十三章 化学气相沉积275
23.1 化学气相沉积的原理275
23.1.1 CVD几种典型化学反应275
23.1.2 CVD反应过程276
23.1.3 CVD的一般原理276
23.2 化学气相沉积的工艺方法277
23.2.1 CVD技术277
23.3.1 化学气相沉积的特点279
23.3.2 化学气相沉积的应用279
23.2.2 CVD主要工艺参数279
23.3 化学气相沉积的特点及应用279
23.4 化学气相沉积的新进展280
第二十四章 辉光离子渗氮及发展283
24.1 辉光离子渗氮原理283
24.2 辉光离子渗氮设备284
24.3 辉光离子渗氮工艺285
24.3.1 辉光离子渗氮处理过程285
24.3.2 辉光离子渗氮的几个工艺问题286
24.3.3 渗氮温度和保温时间对渗氮层硬度和深度的影响287
24.4 辉光离子渗氮用材料288
24.5.1 离子渗碳及氮碳共渗(离子软氮化)289
24.5.2 离子硫氮共渗289
24.5 辉光离子渗碳、氮碳共渗及渗其他元素289
24.5.3 离子渗其他元素290
第二十五章 金属材料的涂层熔融凝结强化291
25.1 涂层熔融凝结强化的设备291
25.2 涂层熔融凝结工艺及涂层性能291
25.2.1 涂层熔融凝结工艺291
25.2.2 涂层性能292
25.3 涂层熔融凝结强化的工业应用292
26.1.1 激光束的产生293
第二十六章 激光表面强化293
26.1 激光表面强化的工艺原理293
26.1.2 激光束对金属的加热过程294
26.1.3 提高金属对激光吸收率的措施294
26.2 激光表面强化对性能的影响295
26.2.1 机械性能295
26.2.2 残余应力297
26.3 激光表面强化的工业应用297
26.3.1 轴类零件297
26.3.6 模具298
26.3.5 工具298
26.3.3 各种尺寸的活塞环298
26.3.2 齿轮、凸轮298
26.3.4 各种小型汽缸套298
第二十七章 离子注入技术299
27.1 离子注入的基本原理299
27.2 离子注入的设备300
27.3 离子注入技术的功能300
27.3.1 改善材料的摩擦磨损性能300
27.3.2 改善材料的抗腐蚀性能301
28.1 金刚石涂层的表面改性技术及应用303
28.1.1 金刚石薄膜的沉积方法303
第二十八章 金属材料的其他表面改性技术303
28.1.2 金刚石薄膜的应用304
28.2 金属材料表面的电火花强化技术305
28.2.1 电火花强化的原理305
28.2.2 电火花强化的操作方法306
28.2.3 电火花强化工艺的优点和应用306
28.3 电子束表面改性技术307
28.3.1 电子束技术概述307
28.3.2 电子束表面改性技术308
28.3.3 电子束表面改性技术的特点及应用308
参考文献309
1998《实用表面工程技术》由于是年代较久的资料都绝版了,几乎不可能购买到实物。如果大家为了学习确实需要,可向博主求助其电子版PDF文件(由谭昌瑶,王钧石主编 1998 北京:新时代出版社 出版的版本) 。对合法合规的求助,我会当即受理并将下载地址发送给你。
高度相关资料
-
- 表面改性技术工程师指南
- 1992 北京:清华大学出版社
-
- 软工程实用技术与方法
- 1994年5月第1版 云南科技出版社
-
- 金属表面技术用语集
- 1980
-
- 工程爆破实用技术
- 1998 北京:煤炭工业出版社
-
- 高等学校试用教材 金属表面强化技术-金属表面工程学
- 1989 北京:机械工业出版社
-
- 工程实用优化技术
- 1989 北京:兵器工业出版社
-
- 金属表面强化技术 金属表面工程学
- 1989 北京:机械工业出版社
-
- 表面工程
- 1989 上海:上海交通大学出版社
-
- 表面沉积技术
- 1989 北京:机械工业出版社
-
- 石油、化工实用防腐蚀技术 第6册 表面处理技术
- 1974 燃料化学工业出版社
-
- 表面处理技术
- 1974 燃料化学工业出版社
-
- 现代表面技术
- 1999 北京:机械工业出版社
-
- 表面涂层技术
- 1994 北京:机械工业出版社
-
- 表面组装技术
- 1994 北京:电子工业出版社
-
- 实用热工仪表检修技术
- 1992 北京:中国计量出版社
提示:百度云已更名为百度网盘(百度盘),天翼云盘、微盘下载地址……暂未提供。➥ PDF文字可复制化或转WORD