《实用机械加工工艺手册》
作者 | 陈宏钧主编 编者 |
---|---|
出版 | 北京:机械工业出版社 |
参考页数 | 1393 |
出版时间 | 1997(求助前请核对) 目录预览 |
ISBN号 | 7111052625 — 求助条款 |
PDF编号 | 810671668(仅供预览,未存储实际文件) |
求助格式 | 扫描PDF(若分多册发行,每次仅能受理1册) |
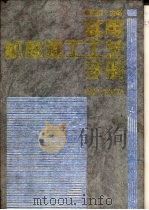
前言1
第1章 机械加工工艺规程的制订1
第1节 机械制造工艺基本术语1
第2节 机械加工工艺规程的编制3
l 机械加工工艺规程的作用3
2 机械加工工艺规程的制订程序4
3 零件图样的工艺审查4
3.l 各种加工类型对零件结构工艺性的要求4
3.2 零件结构的切削加工工艺性5
4 工艺过程设计18
4.1 定位基准的选择与定位夹紧符号18
4.2 零件表面加工方法的选择27
4.3 加工顺序的安排27
5 工序设计28
5.1 机床的选择28
5.2 工艺装备的选择28
6.1 工艺工作程序29
6 工艺工作程序及工艺文件29
5.3 时间定额的确定29
6.2 工艺文件30
第3节 工艺尺寸链35
1 尺寸链的计算参数与计算公式35
1.1 计算参数35
1.2 计算公式35
2 工艺尺寸链的基本类型37
2.1 工艺尺寸换算37
2.3 其他工艺尺寸的计算39
2.2 同一表面需要经过多次加工时工序尺寸的计算39
3 计算机辅助求解工序尺寸43
3.1 计算机跟踪寻找尺寸链43
3.2 计算机解算尺寸链的过程46
第4节 典型零件加工工艺过程49
1 主轴的机械加工工艺过程49
2 曲轴的机械加工工艺过程55
3 连杄的机械加工工艺过程57
4 箱体的机械加工工艺过程62
5 套类零件的机械加工工艺过程63
6 齿轮的机械加工工艺过程64
第1节 钢66
1 钢牌号表示方法66
1.1钢的名称及其代号66
第2章 材料及热处理67
1.2常用钢牌号表示方法67
2.1碳素结构钢68
2 常用钢材的牌号力学性能及用途68
2.2优质碳素结构钢70
2.3低合金结构钢72
2.4合金结构钢74
2.5易切削钢80
2.6弹簧钢81
2.7常用轴承钢的特点及用途82
2.8不锈钢的特性及用途84
2.9耐热钢的特性及用途86
2.10 碳素工具钢87
2.11 合金工具钢89
2.12 高速工具钢92
3 型材93
3.1 热轧圆钢和方钢尺寸93
3.2 热轧六角钢和八角钢的尺寸94
3.3 热轧扁钢的尺寸规格94
3.4 热轧角钢的尺寸规格94
3.5 热轧普通工字钢的尺寸规格103
3.6 热轧普通槽钢104
3.7 冷拉圆钢尺寸规格106
3.8 冷拉方钢尺寸规格106
3.9 冷拉六角钢尺寸规格106
3.10 不锈钢冷加工钢棒107
3.11 热轧钢板尺寸规格107
3.12 冷轧钢板和钢带尺寸规格109
3.13 无缝钢管的尺寸110
4 钢材的涂色标记111
3.14 不锈钢无缝钢管111
第2节 铸铁113
1 铸铁牌号表示方法113
2 灰铸铁113
2.1 灰铸铁的力学性能113
2.2 灰铸铁铸件的应用范围114
3 球墨铸铁的力学性能及应用范围115
4 可锻铸铁的力学性能及应用范围115
5 特种铸铁116
5.1 常用耐蚀铸铁的力学性能与应用116
5.2 常用耐热铸铁的力学性能与应用117
5.3 普通白口铸铁的成分、性能与应用117
5.4 合金白口铸铁的性能与应用119
5.5 冷硬铸铁的成分、性能与用途119
5.6 高铬铸铁的成分、性能与用途120
第3节 铸钢120
1 铸钢牌号表示方法120
3 合金铸钢的力学性能及应用121
2 一般工程用铸钢的力学性能及应用121
4 铸造高锰钢力学性能及应用123
5 耐热铸钢的牌号、化学成分及应用123
6 不锈耐酸钢铸件的力学性能及应用124
第4节 有色金属及其合金127
1 有色金属及其合金产品代号表示方法127
2 铜及其合金128
2.1 变形铜及铜合金的主要特点与用途128
2.2 变形铜合金力学性能与物理性能132
2.3 铜及其合金工艺性能与耐蚀性数据134
2.4 铸造铜合金主要特点与用途136
2.5 铸造铜合金力学性能与物理性能138
3 铝及其合金140
3.1 变形铝合金主要特点与用途140
3.2 铝及其合金热处理工艺参数142
3.3 铸造铝合金主要特点和用途142
3.4 铸造铝合金热处理工艺参数143
2 减摩零件用粉末冶金材料145
第5节 粉末冶金材料145
l 粉末冶金材料的应用范围145
3 摩擦零件用粉末冶金材料的性能146
4 粉末冶金铁基结构材料147
5 作过滤用粉末冶金材料的性能与应用148
第6节 非金属材料148
1 常用工程塑料的性能特点及应用148
2 生胶的类型、特性及其用途151
第7节 热处理153
1 一般热处理153
1.1 一般热处理的工艺特点与应用153
1.2 常用结构钢的完全退火与硬度值155
1.3 常用工具钢、轴承钢退火和球化温度与硬度值155
1.4 常用钢材的正火温度与硬度值156
1.5 常用钢材淬火温度与硬度值157
1.6 常用钢材淬火后不同硬度的回火温度158
1.8 球墨铸铁的热处理规范160
1.7 消除焊接与加工应力的低温退火160
2 化学热处理的工艺特点与应用161
3 表面热处理的工艺特点与应用162
4 热处理与前、后工序的相关要求163
5 影响工件热处理变形的主要原因,表现形式和解决方法163
第3章 毛坯及余量165
第1节 毛坯及加工余量的计算165
1 基本术语165
2.2 选择毛坯应考虑的因素166
2 毛坯的类型及选择166
2.1 各类毛坯的特点及应用范围166
3 加工余量的确定167
3.1 影响加工余量的因素167
3.2 最大余量、最小余量及余量公差的计算168
3 用分析计算法确定最小余量169
4 工序尺寸、毛坯尺寸及总余量的计算169
1.1.2 铸件尺寸公差等级170
1.1.1 铸件的尺寸公差170
第2节 毛坯机械加工余量170
1.1 铸件的尺寸公差及公差等级170
1 铸件170
1.2 铸件机械加工余量171
1.3 铸件结构单元的工艺尺寸174
1.3.1 铸造孔的最小尺寸174
1.3.2 铸造壁的最小厚度175
1.3.3 铸造壁(或肋)间的最小距离175
1.3.4 起模斜度175
1.3.5 圆角半径177
1.4 铸造工艺余量177
2 锻件178
2.1 自由锻件机械加工余量及公差178
2.1.1 台阶轴类178
2.1.2 圆盘类179
2.1.3 带孔圆盘类179
2.1.6 光轴类182
2.1.5 圆环类182
2.1.4 套筒类182
2.1.7 黑皮锻件187
2.2 胎模锻件机械加工余量及公差188
2.2.1 型摔成形类188
2.2.2 套模、垫模成形类188
2.2.3 合模成形类188
2.3.2 确定锻件公差及机械加工余量的主要因素190
2.3.3 公差191
2.3.l 公差及机械加工余量等级196
2.3 钢质模锻件的公差及机械加工余量196
2.3.4 机械加工余量201
2.4 径向锻机上钢质轴类锻件公差及机械加工余量203
3 冲压件204
3.1 冲压件的结构要素204
3.2 冷冲压件的公差207
3.2.1 金属冷冲压件的公差207
3.2.2 冲压剪切下料件公差210
4 钢质冷挤压件公差212
5 热切割件213
5.1 气割质量和尺寸偏差213
5.2 等离子弧切割质量和尺寸偏差213
第3节 工序间加工余量215
1 装夹及下料尺寸余量215
2 轴的加工余量226
2.1 外圆柱表面加工余量及偏差226
2.2 轴端面加工余量及偏差229
2.3 槽的加工余量及公差230
3 内孔加工余量及偏差231
4 平面加工余量及偏差238
5 切除渗碳层的加工余量240
6 有色金属及其合金的加工余量241
7 齿轮和花键精加工余量245
1.2 影响形状精度的因素及消除方法247
1.1 影响尺寸精度的因素及消除方法247
1 影响加工精度的因素及消除方法247
第1节 机械加工精度247
第4章 机械加工质量247
1.3 影响位置精度的因素及消除方法249
2 加工误差249
2.2 加工误差的计算250
第2节 机械加工的经济精度257
1 加工路线与所能达到的加工精度和表面粗糙度257
2 各种加工方法能达到的尺寸经济精度259
3 各种加工方法能达到的形状经济精度263
4 各种加工方法能达到的位置经济精度264
第3节 机械加工表面质量与振动266
1 影响加工表面粗糙度的因素及改善措施266
1.1 影响切削加工表面粗糙度的因素及改善措施266
1.2 影响磨削表面粗糙度的因素及改善措施267
2 各种加工方法能达到的表面粗糙度268
3 表面粗糙度与加工精度和配合之间的关系269
5.1 加工硬化271
4 各种联接表面的粗糙度271
5 加工硬化与残余应力271
5.2 残余应力273
6 切削过程中的振动273
第5章 技术测量276
第1节 测量与测量误差276
1 测量常用术语276
2 测量方法的分类276
3 测量误差的分类、产生原因及消除方法276
第2节 常用计量器具277
1 游标类量具277
2 螺旋测微量具277
3 机械式测微仪281
4 角度量具283
5 量块、量规288
1.3 V形槽宽度、角度计算293
1.2 内圆弧与外圆弧计算293
1 常用测量计算举例293
1.1 圆的弓形尺寸系数表293
1.4 燕尾与燕尾槽宽度计算297
1.5 内圆锥与外圆锥计算297
2 形位误差的检测298
2.1 形位误差的检测原则298
2.2 直线度误差的常用测量方法299
2.3 平面度误差的常用测量方法300
2.5 轮廓度误差的常用测量方法301
2.4 圆度误差的常用测量方法301
2.6 定向误差的常用测量方法302
2.7 定位误差的常用测量方法305
2.8 跳动量的常用测量方法307
3 表面粗糙度的检测309
3.1 表面粗糙度的测量方法、特点及应用309
3.2 表面粗糙度标准样块309
3.3 机械加工表面粗糙度样块310
4.1 螺纹量规的名称、代号、功能、特征及使用规则311
4 螺纹的检测311
4.2 螺纹单项测量方法及测量误差312
4.3 用量针法测量螺纹中径313
5 齿轮检测314
5.1 公法线长度的测量314
5.1.1 标准直齿圆柱齿轮公法线长度测量315
5.1.2 斜齿圆柱齿轮公法线长度测量317
5.1.3 公法线平均长度偏差及公差319
5.2 分度圆弦齿厚的测量322
5.3 固定弦齿厚的测量323
5.4 齿厚上偏差及公差324
5.5 内齿轮齿厚测量326
1.1.1 型号表示方法328
1.1.4 机床的组、系代号及主参数328
1.1.3 机床的特性代号328
1.1.2 机床的分类及类代号328
1.1 通用机床型号表示方法328
1 金属切削机床型号编制方法328
第1节 金属切削机床328
第6章 金属切削机床及附件328
1.3 机床自动线的型号329
1.2 专用机床的型号329
1.1.10 金属切削机床统一名称和类、组、系划分329
1.1.9 企业代号及其表示方法329
1.1.8 其他特性代号及其表示方法329
1.1.7 机床的重大改进顺序号329
1.1.6 主轴数和第二主参数的表示方法329
1.1.5 通用机床的设计顺序号329
2 常用通用机床技术参数与联系尺寸336
2.1 车床336
2.1.1 立式车床336
2.1.2 落地及卧式车床337
2.1.3 回轮、转塔车床346
2.1.4 曲轴车床349
2.1.5 仿形车床350
2.1.6 数控车床353
2.2铣床355
2.2.1 龙门铣床355
2.2.2 立式铣床356
2.2.3 卧式铣床359
2.2.4 万能工具铣床362
2.3 钻床363
2.3.1 摇臂钻床363
2.2.5 数控铣床363
2.3.2 台式钻床366
2.3.3 立式钻床366
2.4 镗床368
2.4.1 坐标镗床368
2.4.2 卧式镗床368
2.4.3 金刚镗床370
2.4.4 数控镗床371
2.5.1 刨床372
2.5 刨插床372
2.5.2 插床374
2.6 拉床375
2.7 锯床376
2.8 磨床376
2.8.1 外圆磨床376
2.8.2 内圆磨床379
2.8.3 平面磨床380
2.8.4 万能工具磨床381
2.8.5 曲轴磨床382
2.9 螺纹加工机床382
2.10 齿轮加工机床383
2.10.1 滚齿机383
2.10.2 插齿机385
2.10.3 剃齿机386
2.10.7 弧齿锥齿轮铣齿机387
2.10.6 直齿锥齿轮铣齿机387
2.10.5 齿轮磨床387
2.10.4 珩齿机387
2.10.8 直齿锥齿轮刨齿机388
2.10.9花键轴铣床389
第2节 机床附件390
1 分度头390
1.1 机械分度头390
1.2 等分分度头390
1.3 数控分度头391
2 卡盘与过渡盘392
2.1 三爪自定心卡盘392
2.2 四爪单动卡盘392
2.3 楔式动力卡盘392
2.4 卡盘用过渡盘398
3 花盘及拨盘400
3.1 花盘400
3.2 拨盘401
4.1 固定顶尖403
4 顶尖及顶尖套403
4.2 回转顶尖405
4.3 拨动顶尖406
4.4 锥孔顶尖407
4.5 顶尖套408
5 夹头409
5.1 扳手式钻夹头409
5.2 自紧式钻夹头410
5.3 攻丝、丝锥夹头411
5.4 快换夹头412
5.5 弹簧夹头413
5.6 铣夹头414
5.7 鸡心夹头415
6 机床用平口虎钳416
7 常用回转工作台418
8 吸盘422
9 铣头、插头与镗头424
1.1 常见各种牌号硬质合金的选用427
1 硬质合金的选用427
第7章 刃具427
第1节 硬质合金刀片427
1.2 几种新牌号硬质合金的性能及应用428
2 硬质合金焊接刀片430
2.l 常用焊接车刀刀片436
2.2 基本型硬质合金焊接刀片436
3 可转位硬质合金刀片436
3.1 可转位硬质合金刀片的标记方法436
3.2 带圆孔的可转位硬质合金刀片439
3.3 无孔可转位硬质合金刀片456
3.4 沉孔可转位硬质台金刀片458
3.5 硬质合金可转位铣刀片465
3.5.1 刀片型号表示方法465
3.5.2 可转位铣刀刀片465
3.6 可转位陶瓷刀片的型号与基本参数469
1 可转位车刀型号表示规则472
第2节 可转位车刀472
2 可转位车刀型式473
第3节 铣刀486
1 立铣刀486
2 键槽铣刀489
3 T形槽铣刀489
4 半圆键槽铣刀489
5 直柄燕尾槽铣刀和直柄反燕尾槽铣刀489
6 槽铣刀496
7 锯片铣刀498
8 三面刃铣刀506
9 圆柱形铣刀513
10 铲背成形铣刀515
11 角度铣刀518
第4节 孔加工刀具522
1 钻头522
2 铰刀548
l 丝锥565
第5节 螺纹刀具565
2 板牙575
3 螺纹滚轮581
4 螺纹模板584
1 盘形齿轮铣刀586
2 盘形锥齿轮铣刀587
3 齿轮滚刀588
4 镶片齿轮滚刀588
5 小模数齿轮滚刀590
6 直齿插齿刀590
7 30度压力角渐开线花键滚刀596
8 45度压力角渐开线花键滚刀596
第7节 拉刀597
1 宽刀体键槽拉刀597
2 平刀体键槽拉刀599
1 普通磨料602
第8节 磨具602
2 硬度等级及其代号604
3 以磨粒率表示的磨具组织及其适用范围604
4 结合剂代号、性能及其适用范围604
5 砂轮的标志方法示例605
6 普通磨具605
7 普通磨具最高工作线速度621
1 夹具常用资料的选择623
1.1 夹具零件常用材料及热处理623
第l节 夹具设计基础资料623
第8章 机床夹具623
1.2 夹具常用公差与配合的选择624
1.3 表面粗糙度在夹具零部件中的应用625
1.4 夹具设计中所用的基本角度和圆锥度627
2 夹具设计常用计算629
2.1 夹具定位尺寸的计算629
2.2 夹具定位精度的计算633
2.3 常见典型夹紧形式所需夹紧力的计算639
1.1 定位件643
第2节 夹具零部件通用标准643
1.2 支承件653
1.3 夹紧件660
1.4 导向件679
1.5 对刀件685
1.6 操作件686
2.1 执行元件687
2.1.1 QGB系列气缸687
2 气动元件687
2.1.2 LCZ系列气缸690
2.1.3 QGv系列膜片气缸693
2.1.4 双活塞回转气缸693
2.2 控制元件694
2.2.1 减压阀694
2.2.2 单向节流阀695
2.2.3 单向阀(A系列)695
2.2.5 二位四通手拉阀696
2.2.4 二位四通转阀(SF24—d)696
2.2.6 脚踏气阀697
2.3 辅助元件697
2.3.1 空气过滤器697
2.3.2 油雾器698
2.3.3 消声器699
第3节 夹具典型机构699
1 可调支承699
2 夹紧机构700
2.1 斜楔夹紧机构700
2.2 螺旋夹紧机构701
2.3 偏心夹紧机构703
2.4 铰链夹紧机构704
2.5 联动夹紧机构706
2.6 定心夹紧机构707
3 分度装置707
1.1 定位要则711
1 机床夹具设计通用要则711
第4节 机床夹具的设计要点及典型结构711
1.2 夹紧要则716
1.3 结构设计要则721
2 车床夹具722
2.1 设计要点722
2.2 车床夹具典型技术要求724
2.3 车床夹具典型结构727
2.3.1 顶尖类727
2.3.2 心轴类727
2.3.3 拨盘类727
2.3.4 卡盘类730
2.3.5 其他车床夹具732
3 钻床夹具733
3.1 设计要点733
3.2 钻(镗)床夹具典型技术要求736
3.3.1 自定心钻夹具740
3.3.2 分度转台740
3.3 钻床夹具典型结构740
3.3.3 钻模742
4 镗床夹具748
4.1 镗床夹具设计要点748
4.2 镗床夹具典型结构752
5 铣床夹具752
5.1 铣床夹具设计要点752
5.2 铣床夹具典型技术要求756
5.3.1 铣床通用夹具760
5.3 铣床夹具典型结构760
5.3.2 铣床专用夹具764
6 磨床夹具764
第5节 可调夹具与组合夹具766
1 可调夹具766
1.1 可调整夹具的特点、适用范围与设计要点766
1.2 可调整夹具结构示例768
2 组合夹具768
2.1 组合夹具的使用范围与经济效果768
2.2 组合夹具的系列、元件类别及作用769
2.3 组合夹具结构示例770
第9章 切削加工771
第1节 车削加工771
1 车床加工范围及装夹方法771
1.1 卧式车床加工771
1.1.1 卧式车床加工范围771
1.1.2 卧式车床常用装夹方法772
1.2 立式车床加工774
1.2.1 立式车床加工范围774
1.2.2 立式车床常用装夹方法775
2 车削圆锥面775
2.1 锥体各部尺寸计算公式775
2.2 车削圆锥面的方法776
2.3 车削标准锥度和常用锥度时小刀架和靠模板转动角度777
3 车削偏心工件的装夹方法777
4 成形面车削方法779
5 滚压加工781
6 车削细长轴783
6.1 车削细长轴的装夹方法783
6.2 车削细长轴常用切削用量784
6.3 车削细长轴车刀几何参数及特点785
6.4 车削细长轴常见工件缺陷和产生原因786
7 车削球面787
9 卧式车床加工常见问题的产生原因及解决方法789
8.2 统制圆柱形螺旋弹簧用心轴直径的计算789
8.l 卧式车床可绕制弹簧的种类789
8 冷绕弹簧789
10 车刀切削部分的几何形状及应用790
10.1 前刀面形状的选择790
1o.2 前角及后角的选择791
10.3 主偏角、副偏角、刃倾角的选挥791
10.4 刀尖圆弧半径、过渡刃尺寸、倒棱前角及倒棱宽度的选择792
10.5 卷屑槽尺寸792
12 车削用量的选择793
12.1 车削速度的计算公式793
11 车刀的磨钝标准及寿命793
12.2 硬质合金及高速钢车刀粗车外圆和端面的进给量795
12.3 硬质合金外圆车刀半精车的进给量796
12.4 硬质合金及高速铜镗刀粗镗孔进给量796
12.5 切断及切槽进给量798
12.6 成形车削时的进给量798
12.7 用YTl5硬质合金车刀车削碳钢、铬钢、镍铬锥及铸钢时的切削速度798
12.8 用YG6硬质合金车刀车削灰铸铁时的切削速度798
12.9 涂层硬质合金车刀的切削用量798
12.10 陶瓷车刀的切削用量800
12.11 立方氮化硼车刀的切削用量802
12.12 金刚石车刀的切削用量802
第2节 铣削加工804
1 铣削方式、铣削范围和基本方法804
1.1 铣削方式804
1.2 铣削范围和基本方法805
2.1 分度头传动系统及分度头定数807
2 分度头807
2.2 分度方法及计算808
2.2.1 单式分度法计算及分度表808
2.2.2 差动分度法计算及分度表809
2.2.3 近似分度法计算及分度表810
2.2.4 角度分度法计算及分度表812
3 铣削离合器812
3.1 齿式离合器的种类及特点812
3.3 分度扳角814
3.2 商合器的铣削及计算814
4 铣削凸轮816
4.l 凸轮传动的三要素816
4.2 等速圆盘凸轮的铣削816
4.3 等速圆柱凸轮的铣削817
5 铣削球面方法818
6 铣刀、铰刀的开齿819
6.1 前角γa=○o的铣刀开齿819
6.2 前角γa>Oo的铣刀开齿820
6.3 圆柱螺旋齿铣刀的开齿821
6.5 锥面齿的铣削822
6.4 端面齿的铣削822
6.6 麻花钻头槽的铣削823
6.7 铰刀的开齿823
7 铣削加工常见问题产生原因及解决方法824
8 铣刀切削部分的几何形状和角度选择826
9 铣刀磨钝标准及耐用度829
10 铣削用量的选择830
10.1 铣削切削速度的计算公式830
10.2 高速钢端铣刀、圆柱铣刀和盘铣刀加工时的进给量832
10.3 高速钢立铣刀、角铣刀、半圆铣刀、切槽铣刀和切断铣刀铣削钢的进给量833
10.4 硬质合金端铣刀、圆柱形铣刀和圆盘铣刀铣削平面和凸台的进给量834
10.5 硬质合金立铣刀铣削平面和凸台的进给量835
10.6 涂层硬质合金铣刀的铣削用量835
第3节 刨削、插削加工835
1 刨削835
1.1 牛头刨床常见加工方法835
1.2 龙门刨床常用加工方法837
1.3 刨削常用装夹方法839
1.4 槽类工件的刨削与切断840
1.5 镶条的刨削842
1.6 精刨843
1.6.l 精刨的类型及特点843
1.6.2 精刨刀常用的研磨方法845
1.7 刨削常见问题产生原因及解决方法845
1.7.1 刨平面常见问题产生原因及解决方法845
1.7.2 刨垂直面和阶台常见问题产生原因及解决方法846
1.7.3 切断、刨直槽及T形槽常见问题产生原因及解决方法847
1.7.4 刨斜面、v形槽及镶条常见问题产原因及解决方法848
1.7.5 精刨表面常见问题产生原因及解决方法848
1.8 常用刨刀种类及用途848
1.9 刨刀切削角度的选择850
1.10 常用刨削用850
2 插削851
2.1 常用装夹和加工方法851
2.2 常用插刀类型及主要几何角度854
2.3 插平面及插槽的进给量855
第4节 钻削、扩削、铰削加工856
1 钻、扩、饺加工方法856
1.1 不同孔距精度所用的加工方法856
1.2 切削液的选择857
1.3 特殊孔的钻削方法857
1.4 深孔的钻削858
1.4.1 深孔钻削的适用范围与加工精度、表面粗糙度858
1.4.2 常用深孔刀具的特点及用途859
2 麻花钻、群钻、铰刀的几何参数861
2.1 通用型麻花钻的主要几何参数861
2.2 常用群钻的几何参数862
2.2.1 标准群钻切削部分几何参数862
2.2.2 铸铁群钻切削部分几何参数863
2.2.3 紫铜群钻切削部分几何参数864
2.2.4 黄铜群钻切削部分几何参数865
2.2.6 毛坯扩孔群钻切削部分几何参数866
2.2.5 薄板群钻切削部分几何参数866
2.3铰刀的主要几何参数867
3 钻头、扩孔钻和铰刀的磨钝标准及耐用度868
4 常用钻削、扩削、铰削用量868
4.l 高速钢钻头钻削不同材料的切削用量868
4.2 硬质合金钻头钻削不同材料的切削用量870
4.3 硬质合金可转位钻头钻孔的切削用量871
4.5 群钻加工铸铁时的切削用量872
4.4 群钻加工钢时的切削用量872
4.6 高速钢及硬质合金锪钻加工的切削用量873
4.7 高速钢饺刀加工不同材料的切削用量873
4.8 硬质合金铰刀铰孔的切削用量874
5 钻削、扩削、铰削加工中常见问题产生原因和解决方法875
5.1 麻花钻钻孔中常见问题产生原因和解决方法875
5.2 内排屑深孔钻钻孔中常见问题产生原因和解决方法876
5.3 扩孔钻扩孔中常见问题产生原因和解决方法877
5.4 多刃饺刀铰孔中常见问题产生原因和解决方法878
1 卧式镗床基本工作范围880
第5节 镗削加工880
2 镗刀881
2.1 单刃镗刀的装夹方式及用途881
2.2 双刃镗刀的装夹方式及用途881
2.3 微调镗刀的结构形式与安装882
2.4 组合镗刀头结构形式及刀片安装位置883
2.5 复合镗刀的形式及应用884
2.6 单刃镗刀886
2.7 整体式镗刀块888
2.8 微调镗刀规格系列889
2.9 镗床用攻丝夹头890
3 刀杆、镗杆890
3.1 刀杆890
3.2 镗杆891
4 卧式镗床定位方式及特点893
5 工艺基准面校正方法895
6 卧式镗床常用测量方法及精度896
8.2 找正工具与找正方法897
8.1 坐标换算与加工调整897
8.3 坐标测量897
7.1 金刚镗床的加工精度897
8 坐标镗床加工897
7.2 硬质合金金刚镗镗刀几何参数的选择897
7 金刚镗床加工897
9 镗削用量903
9.1 卧式镗床的镗削用量与加工精度903
9.2 金刚镗床的镗削用量904
9.3 坐标镗床的镗削用量与加工精度904
10 影响镗削加工质量的因素与解决方法905
10.1 卧式镗床加工中常见的质量问题与解决方法905
10.2 影响孔距加工精度的因素与解决方法905
第6节 拉削加工908
1 拉削方式及加工特点908
2 拉削装置及辅具908
2.2.2 外拉刀用拉削辅具912
2.2.1 内拉刀用拉削辅具912
2.2 拉削辅具912
2.1 拉削装置912
3 拉削余量的选择918
4 拉刀几何角度的选择918
5 常用拉削切削液919
6 拉削速度的选用919
7 拉削中常见缺陷产生原因与解决方法919
第10章 磨削加工923
第1节磨削加工基础923
1 常见的磨削方式923
2 砂轮平衡与修整924
2.1 砂轮安装与静平衡924
2.2 砂轮修整的方法925
3 常用磨削液的名称及性能925
第2节 普通磨削929
1 外圆磨削929
1.1 外圆磨削常用方法929
1.2 外圆磨削余量的合理选择931
1.3 外圆磨削切削用理的选择932
1.3.1 外圆磨削砂轮速度932
1.3.2 纵进给粗磨外圆磨削用量932
1.3.3 纵进给精磨外圆磨削用量933
1.4 外圆磨削常见的工件缺陷、产生原因及解决方法934
2 内圆磨削935
2.1 内圆磨削常用方法935
2.2 内圆磨削余量的合理选择937
2.3 内圆磨削切削用量的选择938
2.3.1 内圆磨削砂轮速度选择938
2.3.2 粗磨内圆磨削用量938
2.3.3 精磨内圆磨削用量940
2.4 内圆磨削常见的工件缺陷、产生原因及解决方法942
3 平面磨削942
3.1 平面磨削常用方法942
3.3 平面磨削切削用量的选择946
3.3.1 平面磨削砂轮速度选择946
3.2 平面磨削余量的合理选择946
3.3.2 往复式平面磨粗磨平面磨削用量947
3.3.3 往复式平面磨精磨平面磨削用量947
3.3.4 回转式平面磨粗磨平面磨削用量948
3.3.5 回转式平面磨精磨平面磨削用量949
3.4 平面磨削常见的工件缺陷、产生原因及解决方法950
4 无心磨削950
4.1 无心外圆磨削常用方法950
4.2 无心外圆磨削切削用量的选择952
4.2.1 无心外圆磨粗磨磨削用量952
4.2.2 无心外圆磨精磨磨削用量952
4.3 无心外圆磨削常见的工件缺陷、产生原因及解决方法953
4.3.l 无心外圆磨削常见的工件表面形状缺陷、产生原因及解决方法953
4.3.2 无心外圆磨削常见工件表面外观缺陷、产生原因954
1.1 高速磨削的特点956
1.2 高速磨削对机床的要求956
第3节 高效与低粗糙度磨削956
1 高速磨削956
1.3 高速磨削对砂轮的要求957
1.4 高速外圆磨削钢材的磨削用量957
2 宽砂轮磨削957
2.1 宽砂轮磨削的特点957
2.2 宽砂轮磨削对机床的要求957
2.3 宽砂轮磨削砂轮的选择957
2.4 宽砂轮磨削工艺参数的选择957
3.1 低粗糙度磨削分类958
3 低粗糙度磨削958
3.2 低粗糙度磨削砂轮的选择959
3.3 低粗糙度磨削对机床的要求959
3.4 各种磨削方式低粗糙度磨削工艺参数959
3.4.1 外圆低粗糙度磨削工艺参数959
3.4.2 内圆低粗糙度磨削工艺参数960
3.4.3 平面低粗糙度磨削工艺参数960
1.1.1 常用珩磨头结构形式961
1.1 珩磨头961
1 珩磨961
第4节 光整加工961
1.1.2 常用珩磨头的联接杆962
1.2.1 珩磨加工常用夹具结构形式963
1.2.2 珩磨加工中的“对中”965
1.3 珩磨油石的选择965
1.4 珩磨工艺参数的选择967
1.5 珩磨加工常见缺陷产生原因及解决方法967
2 研磨972
2.1 研磨的分类和适用范围972
2.2 研具972
2.3 研磨剂975
2.4 研磨膏976
2.5 研磨工艺参数选择977
3 抛光979
3.2 磨料和抛光剂980
1 刀具刃磨的砂轮选择981
第5节 刀具刃磨981
2 砂轮和支片安装位置的确定982
3 刀具刃磨实例983
1.2 普通螺纹代号与标记988
1.5 普通螺纹公差988
1.3 普通螺纹直径与螺距系列988
1.4 普通螺纹基本尺寸988
1.1 普通螺纹基本牙型及尺寸计算988
1 普通螺纹988
第1节 螺纹基本尺寸及公差988
2 英制螺纹1023
2.1 英制螺纹基本牙型及尺寸计算1023
2.2 英制螺纹基本尺寸1023
2.3 英制螺纹公差1024
3 梯形螺纹1024
3.1 梯形螺纹牙型1024
3.2 梯形螺纹代号和标记1025
3.3 梯形螺纹直径与螺距系列1025
3.4 梯形螺纹的基本尺寸1026
3.5 梯形螺纹公差1030
4 锯齿形螺纹1036
4.1 基本牙型1036
4.2 锯齿形(3°、30°)螺纹直径与基本尺寸1037
4.3 锯齿形(3°、30°)螺纹公差1038
4.4 锯齿形螺纹标记1041
5 管螺纹1041
5.1 用螺纹密封的管螺纹1041
5.1.1 圆锥外螺纹基本牙型及尺寸计算1041
5.1.2 圆柱内螺纹基本牙型及尺寸计算1041
5.1.3 螺纹基本尺寸1042
5.1.4 螺纹公差1042
5.2 非螺纹密封的管螺纹1043
5.2.1 基本牙型与尺寸计算1043
5.2.2 基本尺寸及公差1043
5.4 米制锥螺纹1045
5.3 60度圆锥管螺纹1045
6 螺纹新、旧国标对照1046
6.1 新、旧国标螺纹名称及代号时照1046
6.2 新、旧国标螺纹公差等级对照1046
6.3 新、旧国标螺纹公差带位置的比较1047
第2节 螺纹加工1047
1 车螺纹1047
1.1 车螺纹的刀尖宽度尺寸1047
1.2.1 用无进给箱车床车螺纹1048
1.2 车螺纹时的交换齿轮计算1048
1.2.2 有进给箱车床的交换齿轮计算1050
1.3 螺纹车削方法1051
1.4 螺纹车刀、切削用量及切削液1052
1.4.1 常用螺纹车刀的特点与应用1052
1.4.2 高速钢及硬质合金车刀车削不同材料的切削用量1056
1.4.3 高速钢车刀车削螺纹时常用切削液1057
1.5 车削螺纹常见问题产生原因与解决方法1058
2.3 旋风铣削螺纹常用切削用量1059
2.2 旋风铣削螺纹的刀具材料和几何角度1059
2 旋风铣削螺纹1059
2.1 旋风铣削螺纹方式及适用范围1059
3 攻螺纹1061
3.1 普通螺纹丝锥的选择1061
3.2 攻螺纹常用辅具1061
3.3 攻螺纹前底孔直径的确定1062
3.3.1 普通螺纹攻螺纹前底孔的钻头直径1062
3.3.2 非螺纹密封的管螺纹攻螺纹前钻底孔的钻头直径1062
3.3.3 英制锥管螺纹和英制锥螺纹攻螺纹前钻底孔的钻头直径1062
3.4 攻螺纹切削液选择1063
3.5 机用丝锥攻螺纹中常见问题产生原因与解决方法1063
4 挤压丝锥挤压螺纹1064
4.1 挤压丝锥的种类及使用范围1064
4.2 挤压螺纹前螺纹底孔尺寸1064
5.1 板牙种类和使用范围1065
5.2 圆板牙的几何参数1065
4.3 挤压螺纹切削速度的选择1065
5 板牙套螺纹1065
5.3 板牙架型式和尺寸1066
5.4 套螺纹切削液的选择1066
5.5 板牙套螺纹前螺杆直径的确定1066
第3节 渐开线齿轮基本尺寸及精度1067
1 齿轮基本齿廓1067
2 齿轮模数系列1067
3.2 内齿轮几何计算1068
3.3 斜齿圆柱齿轮几何计算1068
3.l 直齿圆柱齿轮几何计算1068
3 圆柱齿轮1068
3.4 齿条几何计算1070
3.5 变位直齿圆柱齿轮1070
3.5.1 高变位直齿圆柱齿轮几何计算1070
3.5.2 角变位直齿圆柱齿轮几何计算1070
3.6 齿轮精度1071
3.6.l 齿轮和齿轮副误差及侧隙的定义和代号1071
3.6.2 齿轮的公差组1077
3.6.4 齿轮公差值1078
3.6.3 新旧标准的误差及偏差名称和代号对照1078
4 锥齿轮1081
4.1 直齿锥齿轮几何尺寸计算1081
4.2 锥齿轮精度1083
4.2.l 锥齿轮、锥齿轮副的误差与侧隙1083
4.2.2 锥齿轮及锥齿轮副公差1088
5 蜗杆和蜗轮1100
5.1 圆柱蜗杆和蜗轮常用计算1100
5.2.1 蜗杆、蜗轮及其传动的误差和侧隙1102
5.2 圆柱蜗杆、蜗轮精度1102
5.2.2 蜗杆、蜗轮及传动的公差1106
第4节 齿轮加工1113
1 成形法铣削齿轮1113
1.1 铣直齿圆柱齿轮1117
1.2 铣直齿条的移距方法1117
1.3 铣斜齿圆柱齿轮1118
1.4 铣直齿锥齿轮1119
3.1 滚齿机传动系统1120
3 滚齿1120
3.2 常用滚齿机联接尺寸1120
2.1 交换齿轮计算及配置1120
2.3 铣削方法1120
2.2 飞刀各部尺寸计算1120
2 飞刀展成铣削蜗轮方法1120
3.3 常用滚齿夹具及齿轮坯安装1123
3.4 滚刀心轴和滚刀的安装要求1123
3.5 滚刀安装角度和工作台转动方向及中间轮装置1125
3.6 交换齿轮计算及滚齿机定数1129
3.7 滚铣大质数齿轮1129
3.7.1 滚铣大质数直齿圆柱齿轮时各组交换齿轮计算1130
3.7.2 滚铣大质数斜齿圆柱齿轮时各组交换齿轮计算1130
3.7.3 Y38滚齿机加工大质数直齿圆柱齿轮时,分度、差动交换齿轮表1131
3.8 滚齿加工常见缺陷及解决方法1132
4 插齿1132
4.1 插齿机传动系统及工作精度1134
4.3 插齿用夹具及调整1137
4.2 插齿刀具的调整1137
4.4 常用插齿机交换齿轮计算1139
4.5 插齿加上中常出现的缺陷及解决方法1140
5 挂轮表1141
6 剃齿1145
6.1 剃齿机及其精度1145
6.2 常用剃齿方法1148
6.3 剃齿用心轴1149
6.4 剃齿加工余量1151
6.5 剃齿误差产生原因及解决方法1151
第5节 花键1153
1 矩形花键1153
1.1 矩形花键基本尺寸系列1153
1.2 矩形花键键槽的截面尺寸1154
1.3 矩形花键公差1155
2.1 标准压力角及模数1156
2.2 渐开线花键的基准齿形及主要参数1156
2 圆柱直齿渐开线花键1156
2.3 渐开线花键尺寸1158
2.4 渐开线花键公差1160
第6节 花键加工1171
1 花键的定心方式及加工精度1171
2 成形铣削方法1171
2.1 用三面刃和锯片铣刀加工花键轴铣削过程1171
2.2 用成形铣刀铣削花键1174
3 铣削花健轴时产生的误差及解决方法1175
第12章 难加工材料加工及特种加工1176
第l节 难加工材料的切削加工1176
1 常用的难切削材料及应用1176
2 难切削金属材料的切削加工性比较1176
3 高锰钢的切削加工1177
3.1 常用切削高锰钢的刀具材料1177
3.2 切削高锰钢车刀与铣刀的主要角度1177
3.3 常用硬质合金刀具车削、铣削高锰钢的切削用量1177
4.4 车削加工高强度钢切削用量1178
4.3 切削高强度钢的车刀与铣刀的主要角度1178
4.5 按高强度钢工件硬度选择铣削用量1178
4 高强度钢的切削加工1178
4.2 常用切削高强度钢用硬质合金1178
4.1 常用切削高强度钢用高速钢刀具材料1178
5 高温合金的切削加工1179
5.l 常用切削高温合金的刀具材料1179
5.2 车削高温合金常用刀具的前角与后角1179
5.3 车削高温合金切削用量举例1179
5.4 铣削高温合金切削用量举例1180
6 钛合金的切削加工1181
6.1 常用切削钛合金的刀具材料1181
6.2 车削钛合金的车刀与铣刀主要角度1182
6.3 车削钛合金切削用量1182
6.4 铣削钛合金切削用量1182
7 不锈钢的切削加工1183
7.1 常用切削不锈钢的刀具材料1183
7.2 切削不锈钢车刀与铣刀的主要角度1183
7.4 高速钢铣刀铣削不锈钢切削用量1184
7.3 车削不锈钢切削用量1184
第2节 特种加工1185
1 电火花线切割1185
1.1 常用国产电火花线切割机床1185
1.2 导轮1186
1.3 电极丝保持器形式及特点1187
1.4 典型夹具及附件形式1188
1.5 不同工作液对工艺参数的影响1189
2.2 常用国产电解加工机床1190
2 电解加工1190
2.1 电解加工应用举例1190
2.3 各种间隙的计算公式1191
2.4 电解液1192
3 电喷涂1196
3.1 电喷涂修复方法的优缺点1196
3.2 电喷涂修复工艺1196
4.2 灰铸铁件刷镀工艺1197
4.1 刷镀的一般工艺过程1197
4 电刷镀1197
5 浇铸巴氏合金及补焊巴氏合金1198
5.1 清理轴瓦1198
5.2 挂锡处理1198
5.3 浇铸1198
5.4 巴氏合金浇铸后的冷却1198
5.5 补焊巴氏合金1199
第13章 数控加工程序编制1200
第l节 零件加工工艺分析1200
1 零件结构设计与加工艺性1200
1.1 改进零件结构工艺性的方法1200
1.2 使用数控机床加工零件应避免的特殊表面1204
2 零件加工工艺分析的基本原则和方法1204
第2节 零件编程通用标准1206
1 数控机床的坐标轴和运动方向1206
1.1 坐标和运动方向命名原则1206
1.2 机床坐标系简图1208
2 数控机床的编码字符1211
3 数控机床的程序段格式1211
3.1 字符的意义1211
3.2 穿孔带程序段格式中符号含义1212
3.3 键盘中所用符号的含义1212
4 准备功能G代码及其功能1212
5 辅助功能M代码及其功能1213
6 常用数控标准1215
6.1 我国的数控标准1215
6.2 ISO制订的数控标准1216
第3节 程序编制及举例1216
1 数值计算1216
1.1 直线圆弧的基点和节点计算方法1216
1.2 非圆曲线节点计算方法1216
2 程序编制1216
2.1 基本移动指令构成的程序段1216
2.2 补偿指令的应用1220
2.3 螺纹切削程序段1221
2.4 固定功能循环1222
2.5 尖角过渡处理方法1224
2.6 切入程序的编制1225
3 编程举例1225
3.1 数控车床程序编制举例1225
3.2 数控铣床程序编制举例1227
第4节 数控常用术语1228
第14章 装配工艺1232
第1节 装配工艺基础1232
1 工艺方法的选择1232
1.1 装配的工艺配合方法1232
1.2 装配尺寸链的基本计算公式1232
1.3 各种装配的组织形式1233
1 清洗1234
1.1 常用清洗方法1234
第2节 一般装配的工作方法1234
2 装配工艺规程制订的基本原则1234
1.2 清洗液的选用1235
1.2.1 防锈汽油配方1235
1.2.2 常用碱液清洗液1235
1.2.3 水剂清洗液1236
2 平衡1237
2.1 静平衡方法及平衡装置1237
2.2.1 动平衡精度等级1238
2.2 动平衡1238
2.2.2 动平衡机类型及用途1239
3 校准1240
3.1 常见校准方法1240
3.2 校准实例1241
4 刮削1242
4.1 常见刮削的应用及刮削面种类1242
4.2 刮削工具1243
4.2.1 刮刀的种类及用途1243
4.2.2 通用刮研工具1244
4.3 各种显示剂1245
4.5 刮削余量1246
4.4 刮削精度检验1246
第3节 典型部件装配1247
1 螺纹联接1247
1.1 螺钉(栓)联接的几种形式1247
1.2 螺纹联接的防松方法1247
1.4 有预紧力要求的螺纹联接装配方法1249
1.5 一般螺纹拧紧力矩1249
1.3 螺纹联接的拧紧顺序1249
2 过盈联接装配方法的选择1250
3 铆接1251
3.1 铆钉的几种典型铆接方法1252
3.2 铆钉1252
3.3 铆接常见缺陷产生原因及防止措施1252
4 环氧树脂胶粘接1254
4.1 环氧树脂胶粘接剂1254
4.2 环氧树脂胶粘接工艺1257
3 常用金属材料的弹性模量1258
2 国外部分标准代号1258
第15章 常用技术资料1258
1 国内部分标准代号1258
第1节 常用资料1258
4 常用材料的摩擦系数1259
5 常用材料的密度1259
6 常用金属材料的熔点1260
7 常用材料线膨胀系数1260
8 各种硬度对照表1260
9 主要元素的化学符号、相对原子质量和密度1261
第2节 法定计量单位及其换算1262
1 国际单位制1262
2 常用法定计量单位与非法定计量单位的换算1263
第3节 工厂常用计算1266
1 单位换算1266
2 数的平方、立方、平方根、立方根、圆周长及圆面积1269
4 常用几何图形计算公式1274
3 π的重要函数及π、25.4的近似分数1274
5 圆的几何图形计算1277
5.1 圆周等分系数表1277
5.2 圆弧长度计算表1277
第4节 公差与配合、表面形状和位置公差、表面粗糙度1277
1 公差与配合1277
1.1 术语及定义1277
1.2 基本规定1281
1.3 尺寸至500mm孔、轴公差与配合1291
1.4 未注公差尺寸的极限偏差1325
1.5 新旧国家标准对照1329
2 形状和位置公差1330
2.1 形状和位置公差的分类及符号1330
2.2 形状和位置公差标注与说明1332
2.3 形状和位置公差未注公差的规定1343
2.4 图样上注出公差值的规定1344
3 表面粗糙度1347
1 一般用途圆锥的锥度与圆锥角1350
第5节 锥度、锥角及其公差1350
2 特殊用途圆锥的锥度与圆锥角1351
3 圆锥公差1351
3.1 圆锥角公差1351
3.2 圆锥的形状公差1353
4 未注公差角度的极限偏差1354
第6节 机械制图1354
l 图纸幅面及格式1354
2 比例1355
3 图线1355
4 剖面符号1356
5 简化画法1356
6 尺寸注法1358
7 简化注法1361
8 各种孔的尺寸标注1363
9 尺寸公差的标注1364
10 螺纹和螺纹紧固件画法及标注1366
11 中心孔的符号及标注方法1370
12 滚动轴承的简化画法1371
第7节 零件结构要素1372
1 中心孔1372
1.1 60°中心孔1372
1.2 75°、90°中心孔1372
2 零件倒圆与倒角1373
3 圆形零件自由表面过渡圆角半径和过盈配合联接轴用例角1374
4 球面半径1374
5 润滑槽1375
5.1 滑动轴承上用的润滑槽形式和尺寸1375
5.2 平面上用润滑槽形式和尺寸1376
6 滚花1376
7 普通螺纹收尾、肩距、退刀槽和倒角尺寸1376
7.1 普通外螺纹收尾、肩距、退刀槽和倒角尺寸1376
8 米制锥螺纹的结构要素1379
8.1 米制锥螺纹的螺纹收尾、肩距、退刀槽和倒角尺寸1379
7.2 普通内螺纹的螺纹收尾、肩距、退刀槽和倒角尺寸1379
8.2 米制锥螺纹接头尾端尺寸1380
9 圆柱管螺纹收尾、退刀槽和倒角尺寸1381
10 梯形螺纹收尾、退刀槽和倒角尺寸1382
11 普通螺纹的内、外螺纺余留长度、钻孔余留深度、螺栓突出螺母的未端长度1382
12 紧固件用通孔和沉孔1383
l2.1 螺栓和螺钉用通孔1383
12.4 圆柱头紧固件用沉孔1384
12.3 沉头紧固件用沉孔1384
12.2 铆钉用通孔1384
12.5 六角头螺栓和六角螺母用沉孔1385
13 退刀槽1386
l3.2 公称直径相同具有不同配合的退刀槽1387
14 砂轮越程槽1387
15 刨削、插削、珩磨越程槽及插齿空刀槽1389
16 T形槽1390
17 燕尾槽1392
参考文献1393
1997《实用机械加工工艺手册》由于是年代较久的资料都绝版了,几乎不可能购买到实物。如果大家为了学习确实需要,可向博主求助其电子版PDF文件(由陈宏钧主编 1997 北京:机械工业出版社 出版的版本) 。对合法合规的求助,我会当即受理并将下载地址发送给你。
高度相关资料
-
- 实用机械加工检验手册
- 1989 北京:北京出版社
-
- 金属机械加工工艺人员手册
- 1965年06月第1版 上海科学技术出版社
-
- 金属机械加工工艺人员手册
- 1965年06月第1版 上海科学技术出版社
-
- 机械加工工艺手册
- 1990 北京:北京出版社
-
- 机械加工工艺装备设计手册
- 1998 北京:机械工业出版社
-
- 物质探源
- 1998 武汉:湖北教育出版社
-
- 机械加工工艺手册 第1卷
- 1991 北京:机械工业出版社
-
- 机械加工工艺手册 第3卷
- 1992 北京:机械工业出版社
-
- 机械加工工艺手册 第2卷
- 1991 北京:机械工业出版社
-
- 机械加工工艺设计实用手册
- 1993 北京:航空工业出版社
-
- 板金成形性能
- 1999 北京:机械工业出版社
-
- 机械加工应用手册
- 1983 济南:山东科学技术出版社
-
- 机械加工工艺设计手册
- 1987 北京:航空工业出版社
提示:百度云已更名为百度网盘(百度盘),天翼云盘、微盘下载地址……暂未提供。➥ PDF文字可复制化或转WORD