《机械加工工艺手册 第1卷》
作者 | 孟少农主编 编者 |
---|---|
出版 | 北京:机械工业出版社 |
参考页数 | 1360 |
出版时间 | 1991(求助前请核对) 目录预览 |
ISBN号 | 7111019547 — 求助条款 |
PDF编号 | 810512908(仅供预览,未存储实际文件) |
求助格式 | 扫描PDF(若分多册发行,每次仅能受理1册) |
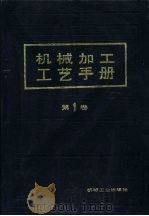
第4章 机械加工质量3
第1章 金属切削原理3
第9章 铣削3
第1节 机械制造工艺基本术语3
第5章 机械加工工艺规程制订3
1·2 原始误差3
1·1 加工精度与加工误差3
1 基本概念3
第1节 机械加工精度3
第6章 机床夹具3
1·1 常用金属轧制件的尺寸与偏差3
1 轧制作3
第1节 毛坯种类和毛坯余量3
第3章 毛坯及余量3
1·2 我国钢号表示方法3
1·1 钢的分类3
1 钢的分类和钢号表示方法3
第1节 钢3
第2章 材料及热处理3
第1节 锯削加工3
1 铣床的型号与技术参数3
1·1 卧式车床及立式车床的型号与技术参数3
1 车床类型与技术参数3
第1节 车床3
第8章 车削3
1·2 锯床类型与技术参数3
1·1 锯床的特点和适用范围3
1 锯床3
第1节 机床夹具的基本概念及分类3
第7章 锯削、刨削、插削3
1·1 设计夹具常用基准的概念及其相互关系3
1 工件在夹具中定位的基本原理3
第2节 工件在夹具中的定位3
4 定位、夹紧和装夹的概念3
3 夹具的组成元件3
2 机床夹具的分类3
1 定义3
第1节 铣床3
1 切削运动、切削用量与切削层参数的基本概念3
1·1切削运动与切削用量3
1·2 切削层参数3
第1节 刀具的几何角度3
2·1 影响尺寸精度的基本因素及消减途径4
2·1 刀具切削部分的组成4
2·2 确定刀具角度的参考系4
2影响加工精度的基本因素及消减途径4
1·2 六点定则4
2 刀具在静止参考系内的切削角度4
1·3 国外钢号表示方法5
第2节 工艺规程的编制5
1 机械加工工艺规程的作用5
2 机械加工工艺规程的制订程序5
3 工艺过程设计5
2·1 锯条齿形型式和几何形状5
2 弓锯床加工5
2·2 影响形状精度的基本因素及消减途径5
3·1 定位基准的选择与定位、夹紧符号5
1·3工件在夹具中加工时的各项误差5
2·3 刀具几何角度的定义5
2·4 刀具几何角度的换算6
2·2 坯料装夹固定方法6
2·3 锯削加工方法6
2 常用定位方法及定位元件6
2·3 影响位置精度的基本因素及消减途径6
2·1 工件以平面为定位基准的定位方法及定位元件6
1·2 轴类零件采用轧制材料时的机械加工余量6
3·3 分析估算加工误差的方法7
3 刀具的工作角度7
3·1 加工误差的分类7
3·2 造成各类加工误差的原始误差7
3 加工误差的综合7
2·5 切削液选用7
2·4 锯削用量及其选用7
2·1 铸造方法8
2·6 弓锯锯削中常见问题与解决方法8
2 铸件8
4 刀具几何角度及刃部参数的选择9
3 圆锯床加工9
3·1 圆锯片9
2·2 工件以外圆柱面为定位基准的定位方法及定位元件10
第2节 刀具材料10
1·2 转塔车床及回轮车床的型号与技术参数10
1 碳素工具钢与合金工具钢11
1·3 仿形车床的型号与技术参数11
2·3 工件以圆孔为定位基准的定位方法及定位元件11
3·4 加工总误差的估算12
3·2 坯料装夹与加工方法12
2·1碳素结构钢12
2 我国钢号的化学成分、机械性能和主要用途12
2 高速钢12
2·2 铸件尺寸公差及选用12
4·1 各种加工方法能达到的尺寸经济精度13
2·3 铸件机械加工余量13
1·4 多刀车床的类型与技术参数13
4 经济加工精度13
2·2 优质碳素结构钢14
3·5 锯削中常见问题与解决方法15
3·4 切削液选用15
3·3 锯削用量及其选用15
4·2 各种加工方法能达到的形状经济精度16
4·3 各种加工方法能达到的位置经济精度16
3 硬质合金16
3·1 常用硬质合金的分类、性能及应用范围16
3·1 定位误差产生的原因16
3·2 定位误差的计算16
3·2 零件表面加工方法的选择16
4·1 锯带16
4 带锯床加工16
1·5 自动车床的类型与技术参数16
3 常用定位方法的定位误差分析与计算16
2·3 低合金结构钢17
2·4 铸件浇注位置及分型面选择17
4·2 立式带锯床加工18
3·3 加工顺序的安排18
4·3 卧式带锯床加工18
2·5 铸件上几种结构单元的工艺尺寸18
2·4 合金结构钢19
4·3 时间定额的组成及缩减单件时间的措施19
4·2 工艺装备的选择19
4·5 锯削用量及其选用19
4·4 万能带锯床简介19
1 已加工表面粗糙度19
第2节 机械加工表面质量19
4·1 机床的选择19
2 铣床主轴联系尺寸与工作台T形槽尺寸19
4 工序设计19
2 各种车床与工夹具的联系尺寸19
2·1 卧式车床主轴的联系尺寸19
2·2 立式车床卡盘的联系尺寸19
2·3 转塔车床的联系尺寸20
1·1 切削加工表面粗糙度形成原因及降低措施20
3 铣床附件21
2·6 铸造工艺余量21
2·7 铸造毛坯图21
4·6 切削液选用21
4·7 带锯床锯削中常见问题与解决方法21
3·2 新牌号的硬质合金21
第2节 刨削加工22
1·1 各类刨床的型号与技术参数22
1 刨床的型号、技术参数及加工精度22
4·8 带锯床的操作安全22
4 铣床的附加装置23
1·1 夹紧力计算的假设条件23
1 确定夹紧力的基本原则23
第3节 工件在夹具中的夹紧23
2·7 自动车床的联系尺寸23
2·6 多刀车床的联系尺寸23
2·5 仿形车床的联系尺寸23
2·4 回轮车床的联系尺寸23
1·2 磨削表面粗糙度形成原因及降低措施24
1·2 夹紧装置设计的内容和步骤24
3·1 锻造方法24
3 锻件24
3·2 自由锻件机械加工余量25
第2节 铣刀及其辅具25
1 铣刀类型、几何参数与规格25
4 涂层刀具材料25
1·2 刨床的工作精度25
1·1 铣刀的类型与用途25
1·2 铣刀的几何参数25
1·3 铣刀的规格25
2·5 冷拉钢26
2·1 刨刀的种类与用途26
2 刨刀26
1·4 龙门刨床在不同条件下的允许载荷26
5 其他刀具材料26
5·1 陶瓷26
2·1 斜楔夹紧机构26
2 各种夹紧机构的设计及其典型结构26
1·3 加工方案与经济精度26
1·3 各种加工方法能达到的表面粗糙度27
5·2 金刚石27
2·6 冷镦钢28
2 加工硬化28
2·1 加工硬化产生的原因28
3·3 钢质模锻件公差及机械加工余量28
5·3 立方氮化硼29
2·2 加工硬化对零件使用性能的影响29
2·2 刨刀合理几何参数29
1·1 切屑形成过程的典型模型29
1 切屑的形成过程29
第3节 切削过程中金属的变形与切削力、切削功率29
2·3 加工硬化的测定方法29
2·3 先进刨刀30
1·2 剪切区内的变形过程30
2·4 影响加工硬化的因素30
2·8 弹簧钢30
2·7 易切削结构钢30
2·1 用相对滑移表示31
2 切屑变形程度的表示方法31
2·2 螺旋夹紧机构31
2·2 用变形系数表示31
3·1 积屑瘤产生的原因32
3 积屑瘤32
3·2 积屑瘤对切削过程的影响32
2·9 轴承钢33
4 切削力的产生和分解33
3·3 抑制或避免积屑瘤的措施33
5 工艺工作程序及工艺文件34
5 切削功率34
6 各种因素对切削力的影响34
5·1 工艺工作程序34
3·3 影响切削加工表面残余应力的因素35
7·2 用单位切削力计算切削力和功率35
7·1 计算切削力的指数公式35
3 残余应力35
3·1 残余应力对零件性能的影响35
3·2 切削加工残余应力产生的原因35
7 计算切削力的经验公式35
5·2 工艺文件35
2·10 不锈钢35
3·4 影响磨削加工表面残余应力的因素37
第4节 刀具的磨损和耐用度,切削用量的制定37
3·3 确定刨削速度、刨削力及刨削功率的常用表格37
3·2?速度、刨削力、刨削功率的计算公式与修正系数37
3·1??量与刨削深度的选择37
3 刨削用??动时间的计算37
1 刀具的磨损形式38
3·4 锻件分模位置的确定39
2·3 偏心夹紧机构39
3·1 刀具磨损过程曲线39
2 刀具磨损的原因39
3 刀具的磨损过程及磨钝标准39
4·1 刀具耐用度的概念40
1·1 焊接式硬质合金刀片40
3·5 锻造毛坯图40
第2节 车刀及其辅具40
1 刀片40
3·2 刀具的磨钝标准40
4 刀具耐用度40
4·2 刀具耐用度与切削用量的关系式40
3·5 残余应力的测量方法41
4·3 刀具耐用度的确定41
4 冲压件41
1 工件便于装夹和减少装夹次数42
4 磨削加工表面的烧伤与裂纹42
4·1 淬火钢烧伤的几种情况42
4·2 烧伤的评定方法与识别42
2·11 耐热钢42
2·1 可转位铣刀刀片的夹紧形式42
5 切削用量的制订42
2 硬质合金可转位铣刀与刀片42
第3节 零件结构的切削加工工艺性42
5·2 进给量的选择43
4·1 冲压件的特点43
4·2 冲压的基本工序43
5·1 切削深度的选择43
2·2 可转位铣刀的种类与规格44
2·4 铰链夹紧机构44
4·4 消减烧伤与裂纹的工艺途径44
4·3 磨削表面裂纹44
5·4 校验机床功率44
5·3 切削速度的确定44
2 减少刀具的调整与走刀次数45
第5节 工件材料的可切削性45
1 可切削性的概念和衡量指标45
2 工件材料的机械、物理性能对可切削性的影响45
5 机械加工过程中的振动46
5·1 机械加工振动的类型和特点46
5·2 强迫振动的振源、诊断及消减措施46
1·2 切削加工用硬质合金的应用范围46
3 钢的可切削性46
3·2 金相组织对可切削性的影响46
2·3 可转位铣刀刀片46
4·3 冲裁件的结构要素46
3·1 化学成分对可切削性的影响46
3 采用标准刀具,减少刀具种类46
5·3 自激振动产生的原因、诊断及消减措施47
4·4 平冲压件的公差47
4 减少刀具切削空行程47
3·3 常用钢的相对切削性47
4 铸铁的可切削性48
3 几个国家的钢号对照48
3·1 普通碳素结构钢48
5 避免内凹表面及内表面的加工48
1·3 可转位硬质合金刀片的标记法48
5 有色金属及其合金的可切削性49
6 加工时便于进刀、退刀和测量49
2·5 联动夹紧机构49
3·4 机动时间的计算49
4 刨削加工工艺49
3·2 优质碳素结构钢49
4·1 刨削加工方法示例49
4·5 冲压件的合理结构49
1·4 带圆孔的可转位硬质合金刀片50
1·2 润滑作用50
1 切削液的作用50
第6节 切削液50
3·3 合金结构钢50
1·1 冷却作用50
5 焊接件51
5·1 焊接结构的特点及应用51
5·2 采用焊接结构应注意的问题51
3 其他铣刀51
3·1 硬质合金可转位密齿铣刀51
2 切削液中的添加剂51
1·3 清洗作用51
2·6 定心夹紧机构52
3 切削液的分类、配方和选用52
7 减少加工表面数和缩小加工表面面积52
3·2 硬质合金可转位曲轴内铣刀52
5·3 焊接件的合理结构52
3·4 可转位螺旋立铣刀53
3·3 硬质合金螺旋齿玉米铣刀53
8 增强刀具的刚度与耐用度53
3·5 硬质合金可转位阶梯面铣刀54
5·4 焊接件的连接方式54
3·5 弹簧钢54
3·4 易切削结构钢54
9 保证零件加工时必要的刚度54
10 合理地采用组合件和组合表面55
3·6 滚珠轴承钢55
3·7 不锈钢55
4·2 刨床常用装夹方法55
3·6 硬质合金可转位重型面铣刀55
参考文献56
4 铣刀直径和角度的选择56
4·1 铣刀直径的选择56
3·7 组合铣刀56
4·2 铣刀角度的选择57
第2节 工序间加工余量57
第4节 工艺尺寸链的解算57
1 尺寸链的计算参数与计算公式57
1 外圆柱表面加工余量及偏差57
5·5 焊接件图例57
4·3 典型加工举例57
1·1 计算参数57
1·2 计算公式58
3·8 耐热钢58
1 铸钢59
1·3 系数e与k的取值59
1·1 铸造碳钢59
4 切削液的加注方法59
2 工艺尺寸链的特点与基本类型59
2 内孔加工余量及偏差59
第2节 铸钢与铸铁59
2·1 工艺尺寸链的特点59
5 使用切削液的故障分析60
4·4 影响刨削加工质量的因素与解决方法60
2·2 工艺尺寸链的基本类型60
5 铣刀的安装与铣刀辅具60
5·1 铣刀的安装60
1·2 低合金铸钢61
5·2 铣刀辅具61
3·1 气动夹紧62
3夹紧的动力装置62
5·1精刨的类型63
5 精刨63
参考文献63
1·3 特种铸钢64
3 直线工艺尺寸链的跟踪图解法65
3·1 跟踪图的绘制65
5·2 精刨的工作要点65
3·2 用跟踪法列工艺尺寸链的方法66
3·3 工艺尺寸链的解算顺序66
3·4 特殊情况下跟踪图解法的应用66
3·2 气压夹紧67
3·3 气-液增力夹紧机构67
4 平面加工余量及偏差67
3 轴端面加工余量及偏差67
4 计算机辅助求解工序尺寸67
4·1 计算机跟踪寻找尺寸链的原理67
6 扩大刨床加工能力与提高刨削效率68
5·3 精刨表面常见波纹的产生原因与消除措施68
6·1 扩大刨床加工能力68
3·4 真空夹紧69
5 有色金属及其合金的加工余量69
6·1 后刀面的刃磨69
6 铣刀的刃磨69
2 铸铁70
4·2 计算机解算尺寸链的过程70
3·5电动夹紧70
6·2 前刀面的刃磨71
1·5 无孔可转位硬质合金刀片71
3·6 磁力夹紧71
2·1 灰铸铁71
4·3 计算程序的框图72
第5节 工艺设计的技术经济分析72
1 产品工艺方案的技术经济分析72
1·1 表示产品工艺方案技术经济特性的指标72
2 铣床夹具的技术条件73
1 铣床夹具的基本要求73
1·2 工艺成本的构成73
第3节 铣床夹具73
6 切除渗碳层的加工余量73
1 夹具与机床的连接方式和有关元件73
第4节 夹具的对定73
1·3 工艺方案的经济评定74
7 齿轮和花键精加工余量74
1·6 沉孔可转位硬质合金刀片74
2 采用工装、设备的技术经济分析75
2·1 采用夹具的技术经济分析75
2·2 采用自动线的技术经济分析75
3 切削和磨削加工工序成本的计算76
1·2 基本余量76
3·2 磨削工序加工成本的分析计算76
3·1 普通切削工序加工成本的计算76
1·3 单面余量和双面余量76
第3节 加工余量和工序尺寸的计算76
1 基本术语76
1·1 加工总余量和工序余量76
2 对刀、导引元件77
1·4 最大余量、最小余量、余量公差77
2·1 对刀装置与元件77
2 加工余量、工序尺寸及公差的关系78
3 工序尺寸、毛坯尺寸及总余量的计算78
4·2 成组夹具的盈亏平衡分析78
4·1 采用成组技术的决策依据78
3 通用可调铣床夹具78
4 成组技术的经济分析78
2·2 球墨铸铁78
4·3 加工族合理性的经济分析79
4 用分析计算法确定加工余量79
4·1 最小余量的组成79
第6节 典型零件加工工艺过程80
2·2 刀具导引元件80
1 车床主轴加工工艺过程80
6·2 提高刨削效率的途径80
3 分度装置81
4·2 计算回转表面加工余量和工序尺寸的算法流程81
2 汽车连杆加工工艺过程81
1·7 陶瓷刀片82
第5节 专用夹具的设计方法82
1 专用夹具的基本要求和设计步骤82
1·1 专用夹具的基本要求82
1·2 专用夹具的设计步骤82
参考文献82
2·3 可锻铸铁82
1·1 插床型号与技术参数83
1 插床83
1·2 插床的工作精度83
2 插刀与插刀杆83
2·1 插刀83
第3节 插削加工83
1·3 夹具体的设计83
1·4 夹具的材料83
1·5 夹具的结构工艺性83
2 自动化夹具的设计要点84
1·6 夹具的经济性84
1·7 设计实例84
2·4 蠕墨铸铁84
4 铣床夹具的典型结构85
2 车刀85
2·1 车刀刀杆的选用85
4·1 直线进给铣床夹具85
2·5 特种铸铁85
2·2 几何参数的选用86
3 插削用量及其选择86
2·2 插刀杆种类和用途86
3 数控机床夹具的设计要点88
4·1 设计原理89
2·3 刀片及断屑槽型的选用89
4 夹具的计算机辅助设计89
5 常用装夹方法和加工方法示例89
4 切削液的选用89
4·2 设计步骤90
4·4 夹具计算机辅助设计的程序库和数据库91
4·3 信息输入的准备工作91
1 组合夹具93
第6节 组合夹具和可调整夹具93
2·4 车刀类型、结构尺寸93
1·1 有色金属的分类及特点93
1 概述93
第3节 有色金属及其合金93
1·2 有色金属及其合金产品牌号和代号表示法93
6·1 花键孔的插削94
6 插床的扩大使用94
4·2 圆周进给铣床夹具94
6·2 螺旋花键孔的插削95
2 铝及其合金95
2·1 变形铝合金95
2 可调整夹具95
6·4 阿基米德曲线凸轮插削96
6·3 用展成法插削渐开线圆柱齿轮96
4·3 靠模仿形铣床夹具97
参考文献97
参考文献98
1 铣削要素99
第4节 铣削用量及铣削参数计算99
2·1 高速钢铣刀的进给量100
2 铣削进给量的选择100
2·3 铣削难加工材料的进给量102
2·2 硬质合金铣刀的进给量102
2·2 铸造铝合金102
3 铣削速度、铣削刀、铣削功率的计算公式及修正系数104
3·1 铣刀的磨钝标准及耐用度104
3·2 铣削速度计算公式105
1 成组技术的效益105
第7节 成组技术105
2·1 OPITZ分类系统106
2 零件分类编码系统106
2·5 成形车刀107
2·3 国内外主要铝合金牌号对照107
3·3 高速钢及硬质合金铣刀铣削难加工材料时铣削速度的计算107
3 铜及其合金108
3·4 铣削力、扭矩和铣削功率计算109
3·1 变形铜合金109
3·5 铣削条件改变时的修正系数110
2·2 KK-3分类系统113
2·6 专用车刀115
3 车刀辅具117
3·1 专用刀辅具的设计步骤117
3·2 刀辅具设计注意事项118
3·2 铸造铜合金118
4 确定铣削用量及功率的常用表格119
4·1 硬质合金端铣刀的铣削用量119
2·3 JLBM-1分类编码系统120
4·2 刃磨工艺122
4·1 刃磨机床与磨具122
4 车刀刃磨122
4 镁及其合金123
4·2 高速钢和硬质合金圆柱铣刀的铣削用量123
4·3 刃磨注意事项124
1·1 特点125
1·3 车床夹具的技术要求125
1·4 典型车床夹具技术要求示例125
1 特点和要求125
第3节 车床夹具125
4·3 高速钢及硬质合金圆盘铣刀的铣削用量125
1·2 要求125
5 锌及其合金126
6 钛及其合金127
7 镍及其合金128
2·4 几种分类编码示例比较128
2·1 顶尖类128
2 车床夹具典型结构128
8 锡铅焊料、易熔合金与轴承合金129
8·1 锡铅焊料的成分、熔点、性能及用途129
4·4 高速钢和硬质合金立铣刀的铣削用量129
2·2 心轴类129
8·2 易熔(或低熔点)合金130
8·3 各种轴承合金的化学成分、性能与用途130
3·1 生产流程分析法131
3 零件分类成组方法131
2·3 拨盘类131
1·1 减摩材料132
1·2 结构材料132
第4节 粉末冶金材料132
1 主要粉末冶金材料的特点和应用范围132
3·2 编码分类法133
2·4 卡盘类133
1·3 摩擦材料137
4 成组工艺过程的设计137
4·1 成组工艺的设计方法137
1·4 过滤材料138
1·5 磁性材料138
4·2 成组工艺文件格式138
5 成组夹具设计138
5·1 成组夹具的技术经济效果138
2 粉末冶金零件的机械加工139
1 材料的重量计算140
第5节 金属型材140
4·5 涂层硬质合金及金刚石铣刀的铣削用量140
5·3 成组夹具的调整方法141
5·4 成组夹具设计的方法与步骤141
5·5 成组夹具设计任务书格式141
5·2 成组夹具的设计要求141
2 金属型材重量表141
2·5 其他类142
5·1 切削时间计算公式143
5·6 成组夹具设计中的“三图一卡”143
5 铣削切削时间的计算143
5·2 切入行程长度和切出行程长度145
第4节 车削用量与车削参数计算145
1 车床切削用量、车削力与车削功率145
1·1 车削进给量的选择145
6 铣削用量选择举例146
第5节 铣削加工工艺147
1·2 铣削方式147
1·1 铣削特点147
1 铣削特点、铣削方式与铣削加工的应用147
6·2 成组加工车间设计148
6·1 成组生产单元的类型148
6 成组生产组织形式及设备布置设计148
1·3 铣削加工的应用148
1·2 车削速度、车削力、车削功率的计算公式与修正系数150
第8节 计算机辅助工艺过程设计(CAPP)150
1 计算机辅助工艺过程设计的基本原理、类型及优点150
1·1 计算机辅助工艺过程设计的基本原理150
1·2 计算机辅助工艺过程设计的类型151
1·3 计算机辅助工艺过程设计的主要优点151
2 计算机辅助工艺过程设计的基本过程151
2·1 输入原始信息151
2·2 计算机解算工艺课题154
2·3 工艺路线生成的基本过程154
2 分度头的分度计算与分度头的应用155
2·1 分度头的分度方法与计算155
第6节 非金属材料156
1 概述156
2 主要非金属材料(橡胶和塑料)的性能和用途156
2·1 机械工业常用的橡胶材料156
2·2机械工业常用的塑料157
3 常用橡胶与塑料的物理化学性能158
3 国内CAPP系统简介159
3·1 TJICAP系统159
2·2用分度头铣削等导程圆柱螺旋槽的交换齿轮计算159
2·3 用分度头铣削等导程圆锥螺旋槽的交换齿轮计算160
4 橡胶与塑料的机械加工160
3·2 QCCAPP系统161
2·4 用分度头铣削等螺旋角圆锥螺旋槽的交换齿轮计算161
1·3 车削用量、车削力与车削功率常用表格162
2·5 用分度头铣削内外球形163
1·1 热处理的工艺特点和处理目的164
1 概述164
第7节 热处理164
3 平面的精铣165
3·2 精铣平面对铣刀的要求和采取的措施165
3·1 精铣平面对铣床主要的精度要求165
3·3 GYCAPP系统166
3·4 武工CAPP系统166
3·3 精铣平面的铣削用量167
3·7 TSCAPP系统167
3·6 HNGCAPP-1系统167
3·5 CTUCAPP-1系统167
3·4 提高工艺系统的刚度和精度168
3·5 铝合金的精铣168
3·10 STCAPP系统169
3·9 LKCAPP-1系统169
3·8 S4MCAPP系统169
4 型面铣削169
4·1 成形面的铣削169
4·2 凸轮的铣削170
3·11 J2CAP系统171
1·2 热处理对钢铁材料切削加工性能的影响172
4·3 端面齿离合器的铣削174
3·13 WIHCAP系统175
2·2 影响工件热处理变形的主要因素、表现形式和解决措施175
3·12 CTCAPP系统175
2 热处理变形175
2·1 变形的类别175
3·2 制定热处理工艺时应注意的事项176
3·1 热处理在整个工艺路线中的次序176
3 热处理与其前后工序间的关系176
1·4 车削切削时间的计算176
3·3 热处理和机加工之间的工艺尺寸公差分配177
1·5 车削用量选用举例178
3·4 热处理变形的尺寸修正和补偿178
3·5 热处理后工件的加工余量179
4 淬火硬化件磨削裂纹的预防措施179
第8节 金属表面处理179
2 自动车床的车削用量179
2·1 单轴和多轴自动车床进给量179
1 电镀180
4·4 曲面铣削180
参考文献181
2 化学镀181
7·1 油漆的命名和型号182
6 刷镀182
5 喷镀182
4 阳极氧化处理182
3 化学处理182
7 油漆涂装182
7·2 油漆材料与涂装方法的选择184
参考文献185
5·2 铣刀安装与调整188
5·1 多刀铣削188
5 多刀铣削及铣刀的安装调整188
2·2 自动车床加工外圆的车削速度188
6·1 圆锥螺旋(槽)铰刀的开齿190
6 铣削加工举例190
2·3 自动车床加工孔的钻削速度192
6·2 曲轴的铣削192
2·4 自动车床加工螺纹的切削速度及切削功率195
6·3 气缸体顶面的精铣197
6·5 支架平面的铣削199
6·4 圆工作台铣床上铣削平面199
第5节 卧式车床与立式车床加工200
1 卧式车床加工200
1·1 概述200
6·6 锁块平面的铣削202
6·7 分离叉圆弧面的铣削202
7 铣削质量问题与解决措施203
1·2 加工中心孔203
8 铣床加工的扩大应用205
8·1 多轴铣削205
1·3 车削细长轴206
8·2 箱体内端面铣削207
1·4 车削内孔208
8·3 套车209
1·5 车削圆锥面211
参考文献211
1·6 车削偏心工件214
1·7 卧式车床加工质量问题与解决措施217
1·8 车削特殊型面218
1·9 在卧式车床上绕制弹簧225
1·10 在卧式车床上进行滚压加工228
2 立式车床加工234
2·1 加工范围235
2·2 工件的装夹、定位和测量235
2·3 立式车床加工中应注意的三种关系238
2·4 几种难加工工件的加工241
第6节 转塔车床和回轮车床加工244
1 转塔车床加工244
1·1 加工范围244
1·2 工艺编制245
1·3 孔和螺纹加工246
1·4 刀辅具选用246
1·5 加工举例248
2 回轮车床加工253
2·1 加工范围253
2·2 工艺编制253
2·3 加工举例259
3 加工质量问题与解决措施259
第7节 仿形车床加工264
1 仿形加工264
1·1 加工范围264
1·2 仿形装置264
1·3 工艺编制中的若干问题264
1·4 细长轴和盘状工件的加工268
1·5 仿形靠模设计要点269
1·6 加工举例275
2 加工质量问题与解决措施275
1 卡盘多刀车床加工276
第8节多刀车床加工276
1·1 加工的型面和适用范围277
1·2 工艺编制278
1·3 加工举例278
2 立式多刀车床加工280
2·1 加工范围与工艺特点280
2·2 工艺编制281
2·3 加工举例281
3 立式多轴车床加工283
3·1 加工范围283
3·2 工艺编制283
3·3 加工举例296
4 加工质量问题与解决措施305
1 单轴纵切自动车床加工307
1·1 加工范围307
第9节 自动车床加工307
1·2 刀具径向位置图与加工过程图308
1·3 工艺编制308
1·4 凸轮设计315
1·5 单轴纵切自动车床的单件工序工时计算316
1·6 加工举例317
2 单轴转塔自动车床加工322
2·1 加工范围322
2·2 辅具种类与装夹尺寸324
2·3 工艺编制327
2·4 凸轮设计335
2·5 生产率的计算343
2·6 加工举例343
3·1 加工范围348
3 多轴棒料自动车床加工348
3·2 通用辅具和专用附件351
3·3 工艺编制369
3·4 工作凸轮的布置与选用371
3·5 生产率计算373
3·6 加工举例374
4·2 材料消耗定额计算378
4·1 对材料的要求378
4 自动车床加工用材料378
5·2 单轴转塔自动车床379
5·1 单轴纵切自动车床379
5 加工质量问题与解决措施379
5·3 多轴自动车床380
参考文献381
1991《机械加工工艺手册 第1卷》由于是年代较久的资料都绝版了,几乎不可能购买到实物。如果大家为了学习确实需要,可向博主求助其电子版PDF文件(由孟少农主编 1991 北京:机械工业出版社 出版的版本) 。对合法合规的求助,我会当即受理并将下载地址发送给你。
高度相关资料
-
- 机械加工工艺手册 第2卷 第16章 螺纹加工
- 1991 北京:机械工业出版社
-
- 金属机械加工工艺人员手册
- 1965年06月第1版 上海科学技术出版社
-
- 金属机械加工工艺人员手册
- 1965年06月第1版 上海科学技术出版社
-
- 机械加工工艺手册
- 1990 北京:北京出版社
-
- 实用机械加工工艺手册
- 1997 北京:机械工业出版社
-
- 机械加工工艺装备设计手册
- 1998 北京:机械工业出版社
-
- 机械加工工艺手册 第3卷
- 1992 北京:机械工业出版社
-
- 机械加工工艺手册 第3卷 第25章 机械加工车间设计
- 1992 北京:机械工业出版社
-
- 机械加工工艺手册 第3卷 第24章 机械加工的质量管理
- 1992 北京:机械工业出版社
-
- 机械加工工艺手册 第3卷 第23章 装配
- 1992 北京:机械工业出版社
-
- 机械加工工艺手册 第3卷 第20章 检测
- 1992 北京:机械工业出版社
-
- 机械加工工艺手册 第3卷 第19章 难加工材料的切削加工
- 1992 北京:机械工业出版社
-
- 机械加工工艺手册 第2卷 第17章 齿轮加工
- 1991 北京:机械工业出版社
-
- 机械加工工艺手册 第2卷
- 1991 北京:机械工业出版社
提示:百度云已更名为百度网盘(百度盘),天翼云盘、微盘下载地址……暂未提供。➥ PDF文字可复制化或转WORD