《Table 3 Proportion of non-adherent particles under different outgrowth values and atomizing gas pre
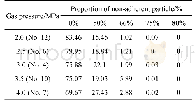
本系列图表出处文件名:随高清版一同展现
《双喷嘴气雾化技术制备球形AlSi10Mg粉末及其表征(英文)》
The influence of atomizing gas pressure on particle size and shape distribution has been studied at five levels(2.0,2.5,3.0,3.5 and 4.0 MPa)with a constant superheat of 250 K and a melt delivery tube diameter of 4.2 mm.The cumulative distribution and median diameter trends are shown in Fig.7.As expected,the cumulative distribution curves move to left with increasing atomization pressure which means a reduction of powder size(Fig.7 (a)) ,median particle diameter D50 decreases with increasing gas to melt ratio(GMR)while fine powder yield rate is just on the opposite,as seen in Fig.7(b).Previous research reported by TING et al[26]also showed that high GMR results in a reduction in medianparticlediameterD50.ACHELISand UHLENWINKEL[3]indicate that a gas mass flow between 100 and 300 kg/h leads to a higher product yield by using a pressure-gas-atomizer.Since the conditions of superheat were identical(250 K)in this part,according to Eqs.(1)-(2),the median particle diameter D50 only relates to gas to metal ratio(GMR).As seen in prior research,an increase in atomization gas supply pressure caused a steady increasing trend in gas mass flow.Meanwhile,the gas velocity would not be increased with pressureincrease[2,27].Data listed in Table 1 show the similar trend.The melt flow rate increases with the rise of gas pressure,which means that the bottom of the melt delivery tube is always in negative pressure state.
图表编号 | XD0064473800 严禁用于非法目的 |
---|---|
绘制时间 | 2019.02.01 |
作者 | 高超峰、肖志瑜、邹海平、柳中强、陈进、李上奎、张大童 |
绘制单位 | 华南理工大学国家金属近净成形工程技术研究中心、华南理工大学广东省金属新材料制备与成形重点实验室、华南理工大学国家金属近净成形工程技术研究中心、华南理工大学广东省金属新材料制备与成形重点实验室、华南理工大学国家金属近净成形工程技术研究中心、江西悦安超细金属有限公司、华南理工大学国家金属近净成形工程技术研究中心、华南理工大学广东省金属新材料制备与成形重点实验室、佛山市岁之博新材料科技有限公司、江西悦安超细金属有限公司、华南理工大学国家金属近净成形工程技术研究中心、华南理工大学广东省金属新材料制备与成形重点实验 |
更多格式 | 高清、无水印(增值服务) |