《板金冲压工艺手册》
作者 | 《板金冲压工艺手册》编委会编著 编者 |
---|---|
出版 | 北京:国防工业出版社 |
参考页数 | 1200 |
出版时间 | 1989(求助前请核对) 目录预览 |
ISBN号 | 7118001031 — 求助条款 |
PDF编号 | 87027078(仅供预览,未存储实际文件) |
求助格式 | 扫描PDF(若分多册发行,每次仅能受理1册) |
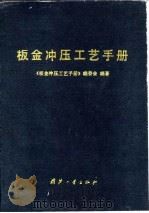
1.1 板金成形基本原理3
1.1.1 内容与范围3
1.1.2 板料塑性变形力学基本知识3
1.1.2.1 应力、应变、实际应力曲线3
1.基本知识3
1.1.2.2应变速度4
1.1.2.3 卸载规律和反载软化现象4
1.1.2.4 简单加载条件5
1.1.2.5 复杂应力状态下,应力与应变之间的关系5
1.1.2.6 各向同性板工程计算的基本公式6
1.1.3 基本成形类型和典型成形方式7
1.1.3.1 成形类型7
1.1.2.8 塑性变形能及其热效应7
1.1.2.7 厚向异性板工程计算的基本公式7
1.1.3.2 典型成形方式8
1.1.3.3 成形方式的复合10
1.1.4 板金成形的限制11
1.2 板金材料的成形性能及其试验方法12
1.2.1 内容与范围12
1.2.2 基本成形性能指数及其试验14
1.2.2.1 单向拉伸试验14
1.2.2.2 液压胀形试验25
1.2.2.3 硬度试验29
1.2.3 模拟成形性能指数及其试验30
1.2.3.1 弯曲成形试验30
1.2.3.2 扩孔成形试验32
1.2.3.3 拉胀成形试验33
4.1.6.2 材料控制 134
1.2.3.4 压延成形试验35
1.2.3.5 复合成形试验37
1.2.4 成形极限曲线及其试验39
1.2.4.1 成形极限曲线的概念39
1.2.3.6 其他模拟成形试验39
1.2.3.7 BCS-30A型通用板材成形性试验机39
1.2.4.2 建立板料FLC的试验方法42
1.2.4.3 一些板料的成形极限曲线46
1.2.4.4 BHB21型坐标网格印制仪49
1.2.4.5 FLC-Ⅰ型板料成形极限曲线试验机50
1.2.5 金属学的成形性能指数及其试验51
1.2.6 特定成形性能指数及其试验51
1.2.6.1 凸耳试验(Earing Test)及其指数51
1.2.6.2 下陷成形试验(Joggle Test)及其指数53
1.2.7 一些常用日本板料的成形性试验值54
1.3.2.1 黑色板金材料62
1.3 常用板金材料的一般知识及有关标准和资料62
1.3.1 内容与范围62
1.3.2 与板金材料有关的国标和冶金部标62
1.3.2.2 有色板金材料63
1.3.3 常用资料64
1.3.3.1 黑色金属品种及常用规格64
1.3.3.2 黑色金属产品名称、用途、特性、工艺方法命名符号66
1.3.3.3 有色金属及合金产品牌号表示方法(GB340-76)68
1.3.3.4 美国板料厚度编级表71
1.3.4 常用金属材料牌号的国内外对照表72
1.3.5 板金成形用钢板的特点82
1.3.5.1 冷轧薄钢板82
1.3.5.2 冲压用热轧钢板85
8.我国新旧国标及OCT公差与配合对照表86
1.3.6.1 轧制薄钢板品种(GB708-65)86
1.3.6 常用黑色板金材料86
1.3.6.2 常用黑色金属的机械性能88
1.3.6.3 优质碳素结构钢薄钢板(GB710-65)90
1.3.6.4 深冲压用冷轧薄钢板(YB215-64)93
1.3.6.5 不锈钢冷轧钢板 (GB3280-84)94
1.3.6.6 合金结构钢薄钢板(YB204-63)100
1.3.6.7 航空用合金结构钢板(YB540-65)101
1.3.6.8 汽车大梁用钢板(GB3273-82)102
1.3.6.9 搪瓷用热轧薄钢板(YB474-64)104
1.3.6.10 变形高温合金钢板105
1.3.6.11 连续热镀锌薄钢板和钢带 (GB2518-81)107
1.3.6.12 电镀锡薄钢板和钢带(GB 2520-81)110
1.3.6.13 一般结构用热连轧钢板和钢带(GB 2517-81)111
1.3.6.14 优质碳素结构钢冷轧钢带(GB3522-83)112
1.3.6.15 冷轧不锈、耐热钢带(GB2598-81)114
1.3.7 常用有色板金材料117
1.3.7.1 常用有色金属的机械性能117
1.3.7.2 铝及铝合金板材的尺寸及允许偏差(GB3194-82)118
1.3.7.3 可热处理强化的铝合金板(GBn167-82)121
1.3.7.4 不可热处理强化的铝及铝合金板(YB606-66)125
1.3.7.5 铝及铝合金薄壁管(YB611-66)126
1.3.7.6 铝及铝合金挤压型材(YB615-66)127
1.3.7.7 工业用纯铝箔 (GB3198-82)129
1.3.7.8 铝合金箔(GB3614-83)131
1.3.7.9 铝及铝合金的其他性能参数132
1.3.7.10 镁合金板金材料(YB628-73)136
1.3.7.11 铜及铜合金板金材料138
1.3.7.12 钛及钛合金板金材料150
1.3.7.13 镍及镍合金板(GB2054-80)155
1.3.8 常用非金属材料的抗剪强度157
1.4.2.1 解析法159
1.4.2 模具的压力中心及其决定方法159
1.4.1 前言159
1.4 模具零件强度计算159
1.4.2.2 图解法161
1.4.3 冲裁凸模的强度计算及稳定性验算162
1.4.3.1 凸模固定端面抗压强度的计算163
1.4.3.3 凸模纵向弯曲稳定性的验算163
1.4.3.2 凸模最小剖面抗压强度的计算163
1.4.4 冲裁凹模的强度计算164
1.4.4.1 整体凹模的强度计算164
1.4.5.1 模板的强度计算166
1.4.5 模板的强度计算及垫板的选择166
1.4.4.3 凹模承受的劈裂力的计算166
1.4.4.2 分段凹模的固定力的计算166
1.4.5.2 垫板的选择168
1.4.6.1 标准橡皮的选用168
1.4.6 橡皮的选用及计算168
1.4.6.2 非标准橡皮的选用169
1.4.7 弹簧的选用及计算170
1.4.7.1 圆柱形压缩弹簧的计算170
1.4.7.2 碟形弹簧的计算172
1.4.8 提高模具寿命的措施173
1.4.8.1 冲裁凸模末端断裂的解决办法173
1.4.8.3 避免凹模热处理时产生裂纹的办法174
1.4.8.2 改进压延模几何形状,延长寿命174
1.5 板金成形中的摩擦磨损与润滑176
1.5.1 板金成形中的摩擦特点176
1.5.2.1 摩擦起因与减小措施176
1.5.2 摩擦176
1.5.2.2 纯净金属的摩擦系数177
1.5.2.3 常用金属材料间的摩擦系数177
1.5.2.4 各种工程塑料的摩擦系数177
1.5.3 板金成形中的摩擦分析178
1.5.3.1 影响摩擦的因素178
1.5.2.5 常用材料的滚动摩擦系数178
1.5.3.2 各种板金成形中的摩擦179
1.5.4 磨损184
1.5.4.1 磨损的成因184
1.5.4.2 估算磨损的公式184
1.5.4.3 擦伤的成因186
1.5.4.4 耐擦伤的判别方法187
1.5.5.1 常用测试方法188
1.5.5 摩擦、磨损、润滑效果常用试验方法188
1.5.5.2 常用测试板金摩擦的方法189
1.5.6 润滑190
1.5.6.1 润滑的机理190
1.5.6.2 液体润滑的方式190
1.5.6.3 液体润滑剂的成分192
1.5.6.5 固体润滑剂195
1.5.6.4 润滑油脂195
1.5.6.6 高温保护润滑剂196
1.5.6.7 润滑剂的选用原则196
1.5.6.8 润滑剂的涂覆方法196
1.5.6.9 板金成形常用润滑剂配方197
1.6.1 热处理207
1.6.1.1 定义与范围207
1.6.1.2 变形铝合金的热处理207
1.6 板金成形中的热表处理207
1.6.1.3 镁合金的热处理209
1.6.1.4 铜及铜合金的热处理210
1.6.1.5 钛合金的热处理211
1.6.1.6 黑色金属热处理213
1.6.2 表面处理216
1.6.2.1 定义与范围216
1.6.2.2 铝合金的表面处理216
1.6.2.3 镁合金的表面处理218
1.6.2.4 钢的表面处理220
1.6.2.5 铜及铜合金的表面处理222
1.6.3 国外铝合金热处理规范223
1.6.3.1 2024铝合金热处理规范223
1.6.3.2 7075铝合金热处理规范223
1.7.1 定义与范围225
1.7.2 一般冲模的典型结构225
1.7 一般冲模的典型结构和材料选择225
1.7.2.1 冲裁模225
1.7.2.2 弯曲模232
1.7.2.3 压延模232
1.7.3 冷冲模标准模架235
1.7.3.1 冷冲模滑动导向模架235
1.7.3.2 冷冲模滚动导向模架269
1.7.3.3 冷冲模模架技术条件275
1.7.4 一般冲模零件的材料276
1.8 通用机械压力机及冲压机械化与自动化278
1.8.1 内容与范围278
1.8.2 通用锻压设备的型号表示方法及含义278
1.8.3 机械压力机的分类和特点280
1.8.4 机械压力机的主要参数和特性282
1.8.4.1 曲柄压力机的主要参数282
1.8.4.2 曲柄压力机的主要参数与模具的关系283
1.8.4.3 曲轴压力机的许可压力和行程的关系283
1.8.4.4 曲柄压力机的公称压力285
1.8.5 压力机的选择原则286
1.8.6 根据生产批量选择压力机的形式286
1.8.7.1 冲压工艺对压力机的要求287
1.8.7 根据冲压工艺的特点选择压力机的形式287
1.8.7.2 压延压力机的特性288
1.8.7.3 精压机的特性289
1.8.7.4 精密冲裁压力机的特性290
1.8.7.5 金属冷挤压机的特性291
1.8.7.6 高速压力机的特性292
1.8.8.1 根据冲压变形力选择压力机293
1.8.8 选择普通机械压力机的规格293
1.8.8.3 计算加工所需的变形力和变形功294
1.8.8.2 根据冲压变形功选择压力机294
1.8.9 选择压力机的精度和刚度296
1.8.10.1 单柱固定台压力机297
1.8.10 普通机械压力机的技术参数和工作台面尺寸297
1.8.10.2 开式可倾台压力机298
1.8.10.3 闭式单点单动压力机300
1.8.11 冲压生产场地303
1.8.12 冲压生产的方式306
1.8.13 设备数量的计算和冲压工时定额306
1.8.13.1设备数量的计算方法306
1.8.13.2 冲压工时定额308
1.8.14 冲压机械化与自动化317
1.8.14.1 实现冲压机械化与自动化的措施317
1.8.14.2 冲压机械化装置应用示例318
1.8.15 冲压生产线323
1.8.15.1 冲压自动化方式的选择323
1.8.15.2 冲压生产线的特点324
1.8.16 冲压用通用工业机器人324
1.8.16.1 冲压用通用工业机器人的类型324
1.8.16.2 冲压用工业机器人的动作及特点325
1.8.16.3 采用工业机器人的冲压生产线示例330
1.8.16.4 冲压用工业机器人的选择333
2.1.4 材料定额与材料利用率339
2.冲压工艺339
2.1.4.1板材339
2.1 下料339
2.1.3 下料工艺余量339
2.1.2 下料的依据339
2.1.1 定义与范围339
2.1.4.2 型材341
2.1.4.3 管材342
2.1.4.4 材料利用率343
2.1.5 板料排样344
2.1.5.1 板料排样原则344
2.1.5.2 单一条料的排样344
2.1.5.3 两个矩形件合理排样举例345
2.1.5.4 多矩形排样346
2.1.5.5 花边条料下料举例346
2.1.6 常用下料方法347
2.1.6.1 剪切下料347
2.1.6.2 铣切下料352
2.1.6.3 锯切下料360
2.1.6.4 氧气切割下料363
2.1.7 特种切割下料方法364
2.1.7.1 等离子切割下料364
2.1.7.2 激光切割下料366
2.1.7.3 几种热切割方法的选用与比较367
2.1.7.4 电火花线切割下料368
2.1.7.5 高压水切割下料369
2.1.8 非金属材料下料372
2.1.8.1 剪切下料372
2.1.8.3 锯切下料373
2.1.8.4 高压水切割下料373
2.1.8.5 激光切割下料373
2.1.8.2 铣切下料373
2.1.9 下料工艺方案选择与下料工艺规程374
2.1.9.1 下料工艺方案的选择374
2.1.9.2 下料工艺规程374
2.1.10 钛合金、镁合金和LC4材料对下料的特殊要求377
2.1.10.1 钛合金材料的特殊要求377
2.1.10.3 LC4超硬铝材料的特殊要求378
2.1.10.2 镁合金材料的特殊要求378
2.2 冲裁379
2.2.1 定义与范围379
2.2.2 排样379
2.2.2.1 无废料排样379
2.2.2.2 无搭边少废料排样380
2.2.2.3 废料利用的排样381
2.2.3 冲裁模工作部分382
2.2.3.1 间隙382
2.2.3.2 模具384
2.2.4 斜刃模391
2.2.5 冲裁件与冲孔的尺寸偏差392
2.2.6 裁件与冲孔凸、凹模的制造公差394
2.2.7 模具功能参数395
2.2.7.1 零件工艺性397
2.2.7.2 搭边398
2.2.7.3 条料宽度与导轨间宽度401
2.2.7.4 模具其他尺寸401
2.2.8力、功与功率的计算405
2.2.8.1 冲裁(冲孔)力405
2.2.8.2 脱料力407
2.2.8.3 推(顶)件力409
2.2.8.4 凸模力与压力中心409
2.2.8.5 冲裁功与功率410
2.2.8.6 冲裁力与功的图算法412
2.2.9 精密冲裁413
2.2.9.1 用突齿压板的精密冲裁413
2.2.9.2 圆刃精密冲裁416
2.2.10 用橡皮的冲裁417
2.2.11 夹模与板模419
2.2.12 冲切模和钢带模422
2.2.13 刮边整修423
2.2.13.1 外缘的整修423
2.2.13.2 内缘的整修425
2.2.14 冲裁质量,模具磨损与润滑426
2.2.14.1 冲裁质量426
2.2.14.2 模具磨损与润滑427
2.3 弯曲428
2.3.2 弯曲件展开长度428
2.3.1 定义与范围428
2.3.2.1 弯曲中性层位置428
2.3.2.2 卷边429
2.3.2.3 展开长度的确定430
2.3.3 弯曲件工艺性435
2.3.4 最小弯曲半径437
2.3.4.1 外层纤维的变形程度437
2.3.4.2 板材最小弯曲半径438
2.3.4.3 型材与管材最小弯曲半径440
2.3.4.4 避免弯曲破裂的措施440
2.3.5 回弹441
2.3.5.1 钢模压弯回弹角441
2.3.4.5 管材弯曲用低熔点填料441
2.3.5.2 弹性凹模压弯回弹角449
2.3.5.3 最大弯曲半径453
2.3.6 弯曲模453
2.3.6.1 刚性模具453
2.3.6.2 橡胶模具455
2.3.7 弯曲力与弯矩457
2.3.7.1 弯曲力457
2.3.7.3 橡胶凹模弯曲力459
2.3.7.2 弯矩459
2.3.8 型材可能承受的最大弯矩估算式460
2.4.2.1 求旋转体压延件毛料的计算方法462
2.4 压延462
2.4.1 定义与范围462
2.4.2 毛料展开462
2.4.2.2 求旋转体压延件毛料的图算法463
2.4.2.3 由表直接查出压延系数后算出毛料直径466
2.4.2.4 将凸缘件折合为筒形件求m值的方法472
2.4.2.5 盒形件毛料的作图展开法473
2.4.2.6 不规则压延件的展开毛料474
2.4.3 旋转体的压延系数476
2.4.3.1 杯形件压延系数的推荐值476
2.4.3.2 杯形件极限压延系数m?的计算值477
2.4.4.2 压延件高度478
2.4.4.1 压延次数478
2.4.4 旋转体压延件压延次数与高度的估算478
2.4.4.3 压延系数给定后凸缘件的几何关系480
2.4.5 矩形压延件的成形极限与压延次数481
2.4.5.1 一次压延成形的极限481
2.4.5.2 压延次数及各次压延参数482
2.4.6 压边与压延梗483
2.4.6.1 压边圈483
2.4.6.2 压边力484
2.4.6.3 矩形及不规则零件的压边与压延梗485
2.4.7 模具圆角半径487
2.4.8 间隙与通气孔489
2.4.9 凸、凹模的制造公差、粗糙度490
2.4.10 压延速度491
2.4.11 压延力,功与功率的计算492
2.4.11.1 压延力492
2.4.11.2 压延功493
2.4.11.3 压延功率494
2.4.12 连续压延494
2.4.13 宽凸缘压延499
2.4.14 橡皮与液囊压延499
2.4.14.1 橡皮压延499
2.4.14.2 液囊压延成形502
2.4.15 其他压延方法505
2.4.15.1 凹模加热和凸模冷却的压延方法505
2.4.15.2 无凸模压延506
2.4.16 变薄压延507
2.5翻边510
2.5.1 定义与范围510
2.5.2 圆孔的翻边510
2.5.2.1 圆孔翻边的工艺性511
2.5.2.2 孔的翻边系数511
2.5.2.3 翻边底孔尺寸的确定513
2.5.2.5 翻边力的计算514
2.5.2.4 翻边凸、凹模之间的间隙514
2.5.2.6 翻边模516
2.5.3 非圆形孔的翻边518
2.5.4 螺纹孔和变薄翻边518
2.5.4.1 预制孔直径,翻边孔直径和翻边高度519
2.5.4.2 变薄翻边用模具521
2.5.5.1 埋头窝524
2.5.5 埋头窝和减重孔524
2.5.5.2 减重孔526
2.5.6 曲线外形的凹弯边528
2.6.1 定义与范围533
2.6.2 零件的胀形系数533
2.6 胀形533
2.6.3 刚性模胀形法534
2.6.3.1 刚性分瓣凸模的胀形534
2.6.3.2 刚性整体凸模胀形535
2.6.3.3 平头凸模和圆头凸模胀形高度的估算式536
2.6.4 橡皮模胀形法537
2.6.5.1 橡皮囊液压胀形538
2.6.5 液压胀形538
2.6.5.2 液压胀形539
2.6.5.3 橡皮和液压胀形高度的估算式541
2.6.5.4 波纹管零件液压胀形541
2.6.6 胀形最大应变与胀形力计算542
2.7扩口544
2.7.1 护口部分的基本要求544
2.7.2.1 单扩口管545
2.7.2 最小直段长度545
2.7.3 管端壁厚的计算546
2.7.2.2 双扩口管546
2.7.4 扩口力547
2.7.5 扩口用的工具和模具547
2.7.5.1 扩口棒扩口547
2.7.5.2 扩口模549
2.7.6 对毛料的要求549
2.8 缩口550
2.8.1 定义和分类550
2.8.2 缩口方法550
2.8.2.1 模压缩口550
2.8.2.2 旋压缩口551
2.8.2.4 热缩口551
2.8.2.3 冲击缩口551
2.8.3.1 缩口变形程度553
2.8.3 缩口工艺参数553
2.8.3.2 缩口毛料高度的计算555
2.8.3.3 缩口力的计算555
2.8.3.4 缩口参数556
2.9 冷挤压558
2.9.1 冷挤压方法及分类558
2.9.2 冷挤压用材料559
2.9.3 冷挤压件的工艺性560
2.9.3.1 冷挤压件的一般工艺要求560
2.9.3.2 冷挤压件的尺寸精度及表面粗糙度563
2.9.3.3 冷挤压件图的内容567
2.9.4 冷挤压毛坯568
2.9.4.1 毛坯的形状和尺寸568
2.9.4.2 毛坯的制备570
2.9.4.4 毛坯的表面处理与润滑572
2.9.4.3 毛坯的软化处理572
2.9.5 冷挤压变形程度与挤压力578
2.9.5.1 变形程度的计算和许用变形程度578
2.9.5.2 挤压力581
2.9.6 冷挤压模具设计592
2.9.6.1 模具的基本设计要求与典型形式592
2.9.6.2 工作部分的设计595
2.9.6.3 冷挤压模主要零部件结构612
2.9.7 冷挤压模具材料及热处理614
2.9.8 冷挤压件质量分析615
2.10 压印623
2.10.1 定义与范围623
2.10.2 压印的工艺设计626
2.10.2.1 一般工艺步骤626
2.10.2.2 压印件的尺寸、精度和表面粗糙度626
2.10.2.3 压印压力626
2.10.3 压印中的润滑628
2.10.5 设备选择628
2.10.4 压印模设计628
2.10.6 压印件质量问题629
2.11 局部成形631
2.11.2 板材的压窝631
2.11.1 定义与范围631
2.11.2.1 最大压窝高度633
2.11.2.2 压窝所需的力636
2.11.3 板材的压埂(加强槽)636
2.11.4 型材的下陷639
2.11.4.1 直线零件简单下陷的成形640
2.11.4.2 成形极限641
2.11.4.3 通用下陷模645
2.11.4.4 压制下陷中的常见故障649
2.11.4.5 其它下陷的成形649
2.11.4.6 压下陷所需的力650
2.11.4.7 工艺上应注意的几个问题650
2.12 校形652
2.12.1 定义与范围652
2.12.2 常用的校形方法652
2.12.2.1 机械校形652
2.12.2.3 手工校形660
2.12.2.2 热校形660
2.12.3 板金零件校形的基本要求663
2.12.4 辅助设备与工具664
2.12.4.1 辅助设备664
2.12.4.2 校形工具673
3.1 旋压677
3.1.1 定义与范围677
3.1.2 普遍旋压677
3.1.2.1 分类与应用677
3.板金工艺677
3.1.2.2毛料材料要求与尺寸679
3.1.2.3 工艺条件679
3.1.2.4 工艺装备683
3.1.2.5 旋压力686
3.1.2.6 工件质量687
3.1.3 剪切旋压688
3.1.3.1 分类与应用688
3.1.2.7 特殊旋压方式688
3.1.3.2 毛料材料与尺寸689
3.1.3.3 工艺条件692
3.1.3.4 工艺装备693
3.1.3.5 旋压力695
3.1.3.6 工件质量697
3.1.4 筒形变薄旋压699
3.1.4.1 分类与应用699
3.1.4.2 毛料材料与尺寸699
3.1.4.3 工艺条件700
3.1.4.4 工艺装备701
3.1.4.5 旋压力704
3.1.4.6 工件质量706
3.1.4.7 一些特殊旋压方式及特点707
3.1.5 旋压机床710
3.2 滚弯717
3.2.1 定义与范围717
3.2.2 板料滚弯零件分类及一般性问题717
3.2.3 圆筒形零件的滚弯719
3.2.3.1 上下滚轴中心距的确定719
3.2.3.2 直线段与非圆段的处理方法721
3.2.4 圆锥形零件的滚弯722
3.2.4.1 毛料展开方法722
3.2.4.2 消除扭曲变形724
3.2.4.3 上下滚轴中心距的确定725
3.2.5 切向变曲率零件的滚弯726
3.2.5.1 手工滚弯法726
3.2.5.2 靠模滚弯法728
3.2.6 纵向变厚度一切向变曲率零件的滚弯742
3.2.7 典型型材滚弯零件分类743
3.2.8 等曲率型材零件的滚弯744
3.2.9 板弯型材的滚弯745
3.2.9.1 手工调整滚弯法746
3.2.9.2 靠模滚弯法746
3.2.10 型材滚弯过程的一般性问题754
3.2.11 型材滚形756
3.2.12 板料滚弯机762
3.2.13 型材滚弯机763
3.3 绕弯764
3.3.1 型材绕弯764
3.3.1.1 型材绕弯的方式与选择764
3.3.1.2 绕弯力矩及回弹量的计算765
3.3.1.3 绕弯过程常见缺陷767
3.3.1.4 绕弯模与侧压装置768
3.3.2 管子绕弯769
3.3.2.1 管子绕弯方法和分类769
3.3.2.2 各类管子绕弯法的使用范围771
3.3.2.3 管子绕弯工艺参数780
3.3.2.4 弯管工具783
3.3.2.5 心棒选用和弯曲前机床调整要点793
3.3.2.6 弯管主要设备794
3.3.2.7 弯管润滑剂797
3.3.2.8 弯管常遇故障分析及排除方法797
3.4拉弯800
3.4.1 定义与机理800
3.4.2 型材拉弯过程及有关参数801
3.4.2.1 一次拉弯法801
3.4.2.2 二次拉弯法802
3.4.2.3 预拉力、补拉力、延伸率的计算803
3.4.2.5 毛料长度的确定806
3.4.2.4 剖面尺寸收缩的核算806
3.4.3 几种特殊形状零件的拉弯法807
3.4.3.1 曲率方向变化零件的拉弯807
3.4.3.2 变斜角零件的拉弯808
3.4.3.3 变切面型材的拉弯809
3.4.3.4 具有下陷零件的拉弯809
3.4.3.5 环形件、空间弯曲件的拉弯810
3.4.4.1 塌肩现象811
3.4.4 拉弯零件的缺陷及解决方法811
3.4.4.2 剖面收缩812
3.4.4.3 剖面挠曲及畸变813
3.4.5 拉弯模与拉伸夹头814
3.4.5.1 拉弯模的典型结构814
3.4.5.2 ПΓР-6、ПΓР-7、XL-2、ПΓР-8拉弯模典型结构814
3.4.5.3 拉弯夹头典型图818
3.4.5.4 转台拉弯机侧压滚轮设计821
3.4.6 回弹样板的制造822
3.4.7 加热拉弯822
3.4.7.1 加热拉弯工艺规范及润滑剂822
3.4.7.2 加热拉弯模及附属设备824
3.4.8 拉弯机825
3.5.2.2 摩擦对拉形的影响827
3.5.1 定义与范围827
3.5.2.1 拉形的成形过程827
3.5.2 拉形的成形过程与影响因素827
3.5 拉形827
3.5.2.3 典型拉形零件各点的变形量829
3.5.2.4 板材塑性指数n、r值对拉形的影响830
3.5.3 拉形件和拉形方法分类830
3.5.3.1 按几何外形分类830
3.5.3.2 按拉形原理分类831
3.5.3.3 双曲度整体壁板的成形831
3.5.3.4 钛合金板材拉形832
3.5.5.1 板材热处理状态的选择834
3.5.5 拉形参数834
3.5.4 拉形工艺方法834
3.5.5.2 毛料尺寸确定835
3.5.5.3 拉形力836
3.5.5.4 拉形系数836
3.5.5.5 极限拉形系数和拉形次数的确定837
3.5.6 拉形质量838
3.5.7 拉形模设计技术要求839
3.5.7.1 制造依据839
3.5.7.2 拉形模数量839
3.5.7.3 拉形模材料839
3.5.7.4 拉形模结构840
3.5.7.5 拉形模重量840
3.5.7.6 拉形模吊环840
3.5.8 拉形设备841
3.6 加热成形与校形842
3.6.1 定义与范围842
3.6.2 加热成形工艺参数的选择842
3.6.3 加热校形工艺参数的选择844
3.6.4 加热方法844
3.6.5 成形设备845
3.6.5.1 专用成形设备845
3.6.5.2 加热电炉849
3.6.6 成形模(或校形模)850
3.6.6.1 模具种类850
3.6.6.2 模具材料850
3.6.6.3 模具设计851
3.6.7 毛料的制备857
3.6.8 润滑剂和防氧化涂料858
3.6.9 热处理859
3.6.9.1 钛与钛合金859
3.6.9.2 镁合金859
3.6.10 去氧化膜860
3.7 超塑性成形862
3.7.1 定义与功用862
3.7.2 超塑性机理862
3.7.3 金属超塑性材料863
3.7.4 影响超塑性成形的因素864
3.7.4.1 变形温度的影响864
3.7.4.2 应变速度的影响864
3.7.4.3 晶粒的影响865
3.7.5.1 超塑性成形规范866
3.7.5 超塑性成形方法866
3.7.5.2 超塑性成形的基本方法867
3.7.5.3 气压成形的一般工艺步骤869
3.7.5.4 零件壁厚不均匀的控制方法870
3.7.6 超塑性成形模具873
3.7.6.1 模具材料873
3.7.6.2 模具设计问题874
3.7.7 超塑性成形设备877
3.7.7.2 基本组成部分877
3.7.7.1 基本要求877
3.7.8 超塑性成形与扩散连接组合工艺879
3.7.8.1 组合工艺特点879
3.7.8.2 组合工艺结构的基本形式879
3.7.8.3 隔离剂(止焊剂)881
3.8.1 定义与范围882
3.8.2 橡皮成形机882
3.8.2.1 基本形式882
3.8 橡皮成形882
3.8.2.2 大台面液压橡皮囊成形机的技术参数883
3.8.3 橡皮成形工艺883
3.8.3.1 直弯边成形883
3.8.3.2 凸弯边成形884
3.8.3.3 凹弯边成形888
3.8.3.4 其它结构要素的橡皮成形893
3.8.4 减少橡皮成形零件手工修整量895
3.8.5 橡皮成形模896
3.8.6 橡皮垫容框897
3.8.6.1 容框材料和结构897
3.8.6.2 橡皮容框的壁厚898
3.8.7 橡皮成形零件设计的工艺性899
3.8.8.1 工艺参数899
3.8.8 钛合金橡皮热成形899
3.8.8.2 钛合金橡皮热成形工艺900
3.8.8.3 橡皮热成形的计算902
3.9.1 定义与范围904
3.9 喷丸成形与校形904
3.9.2 典型零件与工艺方法的选择904
3.9.2.1 工艺方法904
3.9.2.2 典型零件907
3.9.3 工艺参数的选择909
3.9.3.1 喷丸成形工艺参数选择的原则909
3.9.3.2 主要参数对极限成形半径的影响909
3.9.3.3 极限成形半径的限制913
3.9.3.4 喷丸送进方向和零件尺寸因素的影响913
3.9.4 马鞍形零件的数控喷丸成形914
3.9.5 喷丸校形916
3.9.6 零件的质量控制920
3.9.6.1 表面粗糙度的变化920
3.9.6.2 外形精度与尺寸的变化921
3.9.6.3 残余应力与组织结构的变化922
3.9.6.4 机械性能的变化923
3.9.7 喷前要求和喷后处理926
3.9.7.1 喷前要求926
3.9.8.1 横向施加预弯的夹具927
3.9.8 预应力夹具927
3.9.7.2 喷后处理927
3.9.8.2 纵向施加预弯的夹具928
3.9.8.3 局部施加预弯的夹子929
3.9.9 喷丸成形机929
3.9.9.1 气动式喷丸成形机929
3.9.9.2 离心式喷丸成形机932
3.9.9.3 真空喷丸装置933
3.9.9.4 旋片喷丸工具934
3.9.10 弹丸936
3.10 高能率成形940
3.10.1 定义与范围940
3.10.2.1 爆炸成形的原理941
3.10.2 爆炸成形941
3.10.2.2 进行爆炸成形的条件942
3.10.2.3 炸药944
3.10.2.4 安全同题945
3.10.2.5 工艺参数选择945
3.10.2.6 爆炸成形件的质量946
3.10.2.7 模具材料949
3.10.2.8 爆炸成形设备949
3.10.2.9 爆炸胀形955
3.10.2.10 爆炸成形工艺参数实例958
3.10.3 液电成形976
3.10.3.1 电极形式和放电法977
3.10.3.2 液电成形设备978
3.10.4 电磁成形978
3.10.4.1 线圈与集磁器979
3.10.4.2 成形方法980
3.10.4.3 电磁成形设备983
3.11 落压成形985
3.11.1 定义与特点985
3.11.2 气动落锤985
3.11.3 典型的落压零件986
3.11.4 落压零件展开毛料形状和尺寸的确定987
3.11.4.1 铺铅皮法确定展开样板987
3.11.5.1 落压成形的方法988
3.11.4.2 几何作图法988
3.11.5 落压工艺988
3.11.6 落压模990
3.11.6.1 落压模种类和结构990
3.11.5.2 中间退火的确定990
3.11.6.2 落压模的制造992
3.11.7 钛和镁合金板的落压成形1000
3.11.7.1 钛合金板零件落压成形的基本要求1000
3.11.7.2 自阻加热工作电压V的确定1001
3.11.7.3 加热夹具1001
3.11.7.4 保温和测温装置1002
4.4.9 金属材料各种硬度值的相互换算1002
3.11.7.5 钛合金落压成形用保护涂料及润滑涂料1003
3.11.7.6 镁合金落压成形1003
3.12 辅助加工1004
3.12.2.1 板材零件的修边1004
3.12.2 板金零件的修边、钻孔及其工具设备1004
3.12.1 定义与范围1004
4.5.12.8 槽形型材桁条的缺口(HB0-31-83)1008
3.12.2.2 型材零件的修边1009
3.12.2.3 板金零件的钻孔1012
3.12.3 板金冲压零件去毛刺1013
3.12.3.1 板金件去毛刺1013
3.12.3.2 冲压件和小板金件去毛刺1013
4.2.6.7 型材下陷允许偏差1015
3.12.4 零件打标记1015
4.1.2.1 一般术语1019
4.产品检验与协调1019
4.1表面质量控制1019
4.1.1 定义与范围1019
4.1.2 术语1019
4.1.2.2 表面缺陷术语1020
4.1.3 表面质量标准1022
4.1.3.1 一般标准1022
4.1.3.2 特殊标准1024
4.1.3.3 板金零件边缘要求1025
4.1.4.1 铝合金优质表面板金零件的表面保护1026
4.1.4 板金零件的表面保护1026
4.1.4.2 中等质量表面铝合金板金零件的表面保护1027
4.1.4.3 镁合金板金零件的表面保护1027
4.1.4.4 管制零件的表面保护1028
4.1.4.5 不锈钢板金零件加工过程中的表面保护1029
4.1.5 铝合金板金零件外表面的修复1030
4.1.5.1 铝合金板金零件表面缺陷的检测方法1030
4.1.5.2 铝合金蒙皮的修复方法1031
4.1.5.3 修复表面的保护1033
4.1.6.1 工、量具控制1034
4.1.6.3 工艺控制1034
4.1.6.4 操作人员的控制1034
4.1.6 控制1034
4.2.2 平板件和毛料的加工偏差1035
4.2 板金工艺通用技术检验条件1035
4.2.1 定义与范围1035
4.2.3.1 板件凸弯边与凹弯边的外形偏差1037
4.2.3 板弯零件的允许偏差1037
4.2.3.2 加强窝与减轻孔类零件的偏差1038
4.2.3.3 翻边孔1039
4.2.3.4 弯边端头的弯曲半径1039
4.2.3.5 板弯型材拉弯后截面变化1039
4.2.3.6 弯曲半径偏差1039
4.2.3.7 配合板件的弯曲半径偏差1040
4.2.3.8 带有缺口的弯边弯曲半径偏差1040
4.2.3.9 弯边斜角偏差1040
4.2.3.10 下陷偏差1040
4.2.3.12 搭边间隙1041
4.2.3.11 加强弯边的内外隆起1041
4.2.4.1 单曲和双曲度蒙皮与切面样板或模胎的允许间隙1042
4.2.4.2 前缘蒙皮和模胎与样板的允许间隙1042
4.2.4.3 大蒙皮与模胎的允许间隙1042
4.2.4 蒙皮零件允许偏差1042
4.2.3.14 零件平面的不平度1042
4.2.3.13 板弯铰链和卡箍的允许开口尺寸1042
4.2.5.2 油箱零件的加强槽和翻边孔1043
4.2.5.3 立体件的弯曲半径和下陷偏差1043
4.2.4.6 蒙皮倒角、弯曲半径和下陷的偏差1043
4.2.5 立体零件允许偏差1043
4.2.5.1 立体零件与模胎或检验模的允许间隙1043
4.2.4.4 蒙皮翻边圆角与模胎的允许间隙1043
4.2.4.5 鼓形件的收边1043
4.2.6 挤压型材零件的偏差1044
4.2.6.1 型材长度、端头、缺口和切边的偏差1044
4.2.6.2 型材零件的外形偏差1044
4.2.6.3 型材不平度偏差1044
4.2.6.4 型材斜角偏差1044
4.2.6.5 型材零件压制斜角1044
4.2.6.6 挤压型衬的滚弯1044
4 2.6.8 型材弯曲部分的偏差1046
4.2.6.9 型材拉弯允许的尺寸变化1046
4.2.6.10 铰链零件的偏差1047
4.2.8 边缘切割允许偏差1047
4.2.7 焊接半管零件的允许偏差1047
4.2.10 零件材料的允许变薄量1048
4.2.9 制孔的允许偏差1048
4.2.11 铝合金板制零件表面状态要求1049
4.2.11.1 包铝层零件允许划伤和擦伤的范围1049
4.2.11.2 无包铝层零件的划伤和擦伤1049
4.2.12 板金零件牛加压检验1049
4.3.2.2 磁力探伤对零件表面的要求1051
4.3.3 超声波探伤1051
4.3.2 磁力探伤1051
4.3 板金零件无损检验方法1051
4.3.2.1 磁力探伤法可以发现的缺陷1051
4.3.1 定义与范围1051
4.3.3.1 应用范围1052
4.3.3.2 超声波探伤注意事项1052
4.3.4 X光探伤1052
4.3.4.1 应用范围1052
4.3.4.2 工序安排1052
4.3.4.3 灵敏度1052
4.3.6 着色探伤1053
4.3.5 荧光探伤1053
4.3.5.4 对被检查零件的要求1053
4.3.5.2 荧光液的配制和功能1053
4.3.5.3 荧光探伤设备和材料1053
4.3.5.1 应用范围1053
4.3.6.2 灵敏度1054
4.3.7 各种无损探伤方法的性能比较1054
4.3.6.1 应用范围1054
4.3.8 铝合金分光检验1055
4.3.8.1 应用范围1055
4.3.8.2 分光检验位置和表面要求1055
4.4 硬度检验1056
4.4.1 定义与范围1056
4.4.2 常用的各类硬度及其测定方法1056
4.4.2.1 布氏硬度(HB)1056
4.4.2.2 洛氏硬度(HR)1057
4.4.2.5 邵尔硬度(A)1058
4.4.3 硬度检验方法的选择原则和适用范围1058
4.4.2.4 克氏硬度(HK)1058
4.4.2.3 维氏硬度(HV)1058
4.4.4 显微硬度检验1059
4.4.5 热处理零件的硬度检验类别1060
4.4.5.1 航空、航天工业最终热处理零件的硬度检验1060
4.4.5.2 航空、航天工业化学热处理零件的硬度检验1060
4.4.6 硬度检验的安排1060
4.4.7 硬度检验的抽样和判定1060
4.4.8 变形铝合金硬度检验的有关规定1061
4.4.8.2 用硬料加工的零件的硬度检验1061
4.4.8.1 成形后淬火、时效的零件的硬度检验1061
4.4.8.3 铝合金硬度检验合格值1061
4.4.10 黑色金属硬度、硬度与强度的换算值1065
4.4.11 铝合金硬度、硬度与强度的换算值1070
4.5.1 板材最小弯曲半径(HB0-10-83)1072
4.5 板金零件常用结构要素标准1072
4.5.2 加强槽(HB0-11-83)1073
4.5.3 加强窝(HB0-13-83)1074
4.5.4 弯边减轻孔(HB0-14-33)1075
4.5.5 用橡胶模压制的60°弯边减轻孔(HB0-15-83)1076
4.5.6 直角减轻孔(HB0-16-83)1077
4.5.7.1 开口弯边(HB0-19-83)1079
4.5.7.2 皱纹弯边(HB0-20-83)1079
4.5.7 开口弯边和皱纹弯边1079
4.5.8 板材零件下陷(HB0-21-83)1080
4.5.9 橡胶压制凸凹弯边高度1082
4.5.9.1 橡胶压制凸弯边的高度(HB0-17-83)1082
4.5.9.2 橡胶压制凹弯边的高度(HB0-18-83)1084
4.5.10 挤压型材下陷(HB0-2283)1085
4.5.11 挤压型材倾斜角度极限值(HB0-35-83)1087
4.5.12 长桁缺口1088
4.5.12.1 角形型材桁条的缺口(HB0-24-83)1088
4.5.12.2 角形型材桁条的缺口(HB0-25-83)1088
4.5.12.3 角形型材桁条的缺口(HB0-26-83)1089
4.5.12.4 角形型材桁条的缺口(HB0-27-83)1092
4.5.12.5 角形型材桁条的缺口(HB0-28-83)1093
4.5.12.6 丁字型材桁条的缺口(HB0-29-83)1095
4.5.12.7 槽形型材桁条的缺口(HB0-30-83)1096
4.5.12.9 槽形型材桁条的缺口(HB0-32-83)1100
4.5.12.10 槽形型材桁条的缺口(HB0-33-83)1101
4.5.12.11 Z字型材桁条的缺口(HB0-34-83)1102
4.5.13 板金零件弯角处止裂孔1104
4.5.14 展开长度计算表(HB0-45-83)1104
4.6 模线样板1107
4.6.1 定义与范围1107
4.6.2 样板品种及其标记1107
4.6.2.1 样板的分类、名称、用途和特征1107
4.6.2.2 样板上的工艺孔1110
4.6.2.3 样板标记1112
4.6.3.1 模线绘制公差1132
4.6.3 模线样板公差1132
4.6.3.2 样板制造公差1134
4.7 板金零件的协调1137
4.7.1 板金零件协调的基本概念1137
4.7.1.1 互换与协调1137
4.7.1.2 协调路线1137
4.7.1.3 协调误差的计算1138
4.7.1.4 超差率的计算1142
4.7.2.2 协调路线制定步骤1144
4.7.2 协调方案的制定1144
4.7.2.1 协调方案选择原则1144
4.7.2.3 提高协调路线准确度措施1146
4.7.3.1 协调方法分类1147
4.7.3 板金零件协调方法1147
4.7.3.2 模线样板工作法1148
4.7.3.3 标准样件工作法1149
4.7.3.4 表面样件(总模型)工作法1152
4.7.3.5 CAD/CAM工作法1161
4.8 工艺方案的制定与技术经济分析1165
4.8.1 工艺方案的制定1165
4.8.1.1 制定工艺方案的基本原则1165
4.8.1.2 制定工艺方案的依据1165
4.8.1.3 典型零件的工艺方案1165
4.8.2 工艺方案的技术经济分析1169
4.8.2.1 工艺方案的经济核算1170
4.8.2.2 典型零件工艺方案经济评价1171
4.8.3 工艺方案的选定1176
附录1178
1.力的单位换算1178
2.压力单位换算1179
3.功、能及热量单位换算1182
4.功率单位换算1184
5.各种温度单位换算1185
6.公差等级的应用1186
7.光洁度与表面粗糙度的关系1186
1989《板金冲压工艺手册》由于是年代较久的资料都绝版了,几乎不可能购买到实物。如果大家为了学习确实需要,可向博主求助其电子版PDF文件(由《板金冲压工艺手册》编委会编著 1989 北京:国防工业出版社 出版的版本) 。对合法合规的求助,我会当即受理并将下载地址发送给你。
高度相关资料
-
- 冲压工艺学
- 1982 北京:机械工业出版社
-
- 冲压工艺学
- 1982
-
- 冲压工艺
- 1977
-
- 冲压技术手册
- 1979 新太出版社
-
- 冲压工艺模具学
- 1998 北京:机械工业出版社
-
- 冲压加工技术手册
- 1988 轻工业出版社
-
- 冲压工工艺学
- 1991 沈阳:辽宁科学技术出版社
-
- 板金落压工
- 1975 北京:国防工业出版社
-
- 机械工程手册 第41篇 板料冲压
- 1979 北京:机械工业出版社
-
- 手表零件冲压加工工艺
- 1987 轻工业出版社
-
- 冲压工艺
- 1984 长沙:湖南科学技术出版社
-
- 冲压工工艺学
- 1985 北京:科学普及出版社
-
- 冲压工艺学
- 1987 西安:西北工业大学出版社
-
- 机械工程手册 试用本 第41篇 板料冲压
- 1978 北京:机械工业出版社
-
- 板料冲压加工
- 1982 天津:天津科学技术出版社
提示:百度云已更名为百度网盘(百度盘),天翼云盘、微盘下载地址……暂未提供。➥ PDF文字可复制化或转WORD