《表2 图2a中各点EDS结果》
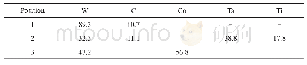
本系列图表出处文件名:随高清版一同展现
《WC-TiC-TaC-Co硬质合金中TaC含量对其显微组织和力学性能的影响》
(mass fraction/%)
图2为样品S4~S7显微组织的SEM-BSE像。WC-TiC-TaC-Co硬质合金主要由3种相组成:灰白色的WC相,灰黑色的(W,Ti,Ta)C相,以及黑色的γ相(以Co为基体元素的Co-W固溶体),如图2a中箭头所示,相的成分如表2所示。在烧结过程中,WC、TiC和TaC通过溶解、再析出和固相固溶形成均匀分散的复合碳化物(W,Ti,Ta)C,如图2a中TaC含量为4.6%的合金(S4)所示。随着TaC含量的升高,复合碳化物(W,Ti,Ta)C增多,会有部分固溶体未溶解于液相,从而溶解、再析出所形成的(W,Ti,Ta)C晶粒会优先在未溶解的固溶体(W,Ti,Ta)C附近析出。且(W,Ti,Ta)C与γ相的润湿性差,当γ相出现在复合碳化物之间时会被挤出,从而(W,Ti,Ta)C晶粒开始聚集,如图2b~d中圆圈所示。图3a为WC晶粒尺寸分布图。随着TaC含量从4.6%~5.5%(S4和S5)增加到6.3%~7.3%(S6和S7),尺寸小于0.5μm的WC晶粒明显增加。S5中WC晶粒尺寸分布不均匀,出现尺寸大于4μm的WC晶粒,这是由于S5中C含量较多,导致液相烧结过程中合金的液相点下降,相应地增加了实际烧结过程中液相量和液相保温时间,WC晶粒发生异常长大。在S7样品中,C含量虽然也较多,但由于Ta含量的增加,使得S7中WC晶粒得以细化,未出现WC晶粒异常长大的现象。图3b为(W,Ti,Ta)C晶粒尺寸分布图。(W,Ti,Ta)C晶粒尺寸集中分布在0.5~1μm,随着TaC含量从4.6%~5.5%(S4和S5)增加到6.3%~7.3%(S6和S7),晶粒尺寸小于1μm的细晶(W,Ti,Ta)C逐渐减少,尺寸大于1μm的粗晶(W,Ti,Ta)C增多。WC-Co硬质合金中,WC晶粒在液相烧结过程中通过溶解-析出机制长大,在合金中加入适量的TaC,Ta元素优先在液相γ相中溶解,降低了W在γ相中的溶解度,从而阻碍细小WC晶粒的溶解,减少烧结冷却阶段WC从液相中的析出,在未被溶解的WC晶粒上结晶的现象,从而抑制WC晶粒的析出长大[18]。随着TaC含量的增加(从S5到S6),尺寸小于0.5μm的WC晶粒明显增多。Ta在γ相中的溶解度很小,约为0.3%,TaC含量的持续增加(从S6到S7),对WC晶粒长大的抑制作用变化不再显著,细晶(<0.5μm)WC含量不再明显增加。
图表编号 | XD00163312300 严禁用于非法目的 |
---|---|
绘制时间 | 2020.07.11 |
作者 | 和淑文、王鸣华、白琴、夏爽、周邦新 |
绘制单位 | 上海大学材料研究所、宝山钢铁股份有限公司、上海大学材料研究所、上海大学材料研究所、上海大学材料研究所 |
更多格式 | 高清、无水印(增值服务) |