《可靠性及维修性工程手册 下》
作者 | 曾天翔主编 编者 |
---|---|
出版 | 北京:国防工业出版社 |
参考页数 | 580 |
出版时间 | 1995(求助前请核对) 目录预览 |
ISBN号 | 7118012491 — 求助条款 |
PDF编号 | 810120638(仅供预览,未存储实际文件) |
求助格式 | 扫描PDF(若分多册发行,每次仅能受理1册) |
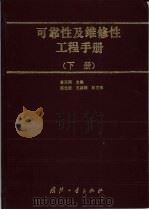
1.1 引言1
1.1.1 可靠性试验的发展史1
第一章 可靠性试验和耐久性试验1
1.1.2 可靠性试验的目的与分类2
1.2.3 可靠性试验与其他试验的关系3
1.2 通用要求4
1.2.1 制订可靠性试验计划5
1.2.2.1 受试产品的说明及数量5
1.2.1.2 确定试验时间和进度5
1.2.1.3 试验场所选取5
1.2.1.4 规定可靠性试验条件5
1.2.1.5 拟定可靠性试验方案5
1.2.1.6 可靠性试验数据的处理要求5
1.2.1.9 振动测定6
1.2.2 试验设备和仪器6
1.2.2.1 试验箱6
1.2.1.7 设置评审点6
1.2.1.8 温度测定6
1.2.2.2 试验仪器7
1.2.2.3 受试产品的检测7
1.2.3 受试产品的预防性维修7
1.2.4 故障的处理7
1.2.5 故障报告、分析和纠正措施系统(FRACAS)7
1.2.6 故障分类7
1.3.1 概述8
1.3.1.1 环境应力筛选(ESS)和可靠性8
1.2.8 可靠性试验记录和报告8
1.3 环境应力筛选8
1.2.7 受试产品修复性维修8
1.3.1.2 ESS的应用效果10
1.3.2 环境应力筛选基本概念12
1.3.2.1 环境应力筛选特性12
1.3.2.2 环境应力筛选与其他工作的关系12
1.3.2.3 环境应力筛选的应用14
1.3.2.4 浴盆曲线和筛选机理15
1.3.2.5 产品中的缺陷及其影响因素16
1.3.2.6 筛选缺陷及其比例17
1.3.3 筛选用典型环境应力及其相应设备19
1.3.3.1 典型应力19
1.3.3.2 各种应力筛选效果的比较24
1.3.4 元器件筛选26
1.3.4.1 元器件筛选的重要性26
1.3.4.2 元器件筛选场所29
1.3.4.3 元器件生产筛选方法30
1.3.4.4 元器件验收筛选通用方法38
1.3.5 组件级以上产品的筛选大纲的设计39
1.3.5.1 ESS大纲的基本内容39
1.3.5.2 ESS大纲设计准则40
1.3.5.3 ESS大纲的设计方法40
1.3.6 组件级以上筛选大纲的实施48
1.3.6.1 一般要求48
1.3.6.2 ESS实施过程50
1.3.6.3 有关事项52
1.3.7.2 温度稳定时间和热点确定方法53
1.3.7 温度、振动响应调查和故障调查53
1.3.7.1 概述53
1.3.7.3 温度软故障调查方法54
1.3.7.4 振动响应调查方法54
1.3.7.5 振动软故障调查方法54
1.4 可靠性研制与增长试验56
1.4.1 可靠性研制试验56
1.4.2 可靠性增长试验56
1.4.2.1 可靠性增长试验的基本概念56
1.4.2.3 可靠性增长试验的适用时机及对试验样品的要求60
1.4.2.2 可靠性增长试验的需求分析60
1.4.2.4 可靠性增长试验的环境条件61
1.4.2.5 可靠性增长试验用的数学模型73
1.4.2.6 可靠性增长潜力分析87
1.4.2.7 可靠性增长试验大纲的编制96
1.4.2.8 可靠性增长试验计划97
1.4.2.9 可靠性增长试验的跟踪101
1.4.2.10 可靠性增长试验中故障的处理104
1.4.2.12 可靠性增长试验的结束105
1.4.2.11 可靠性增长试验评估105
1.5 可靠性鉴定和验收试验106
1.5.1 电子产品的可靠性鉴定试验和验收试验106
1.5.1.1 可靠性特征量的说明106
1.5.1.2 可靠性鉴定和验收试验前工作107
1.5.1.3 可靠性统计试验109
1.5.1.4 可靠性统计试验方案及试验数据处理111
1.5.2 非电子产品可靠性验证试验方案175
1.5.2.1 概述175
1.5.2.2 试验方案说明175
1.5.3 可靠性鉴定试验示例186
1.5.3.1 试品概况186
1.5.3.2 试验前的准备工作186
1.5.3.3 试验程序205
1.5.3.4 试验结果206
1.6.1 概述207
1.6 耐久性试验207
1.6.2 耐久性(寿命)试验分类208
1.6.3 耐久性(寿命)参数208
1.6.4 耐久性(寿命)试验大纲的编写211
1.6.4.1 耐久性(寿命)试验目的与作用211
1.6.4.2 耐久性(寿命)试验大纲编写需考虑的因素211
1.6.5 耐久性(寿命)试验的抽样212
1.6.6.3 薄弱环节试验法213
1.6.6.4 截尾寿命试验方法213
1.6.6.1 正常应力试验方法213
1.6.6.2 MTBF控制试验法213
1.6.6 耐久性(寿命)试验方法213
1.6.6.5 加速寿命试验方法214
1.6.7 首翻期初始值及总寿命的计算219
1.6.7.1 首翻期初始值的计算219
1.6.7.2 总寿命的计算224
参考文献225
2.2 维修性验证的主要类型226
2.2.1 维修性核查226
第二章 维修性验证226
2.1 引言226
2.2.2 维修性演示227
2.2.3 维修性评估228
2.3 维修性验证大纲228
2.3.1.2 选择维修作业229
2.3.1.3 维修作业(样本)的分配229
2.3.1.1 选择验证方法229
2.3.1 制定维修性验证方案229
2.3.1.4 故障模拟230
2.3.1.5 故障排除231
2.3.1.6 预防维修231
2.3.2 背景资料232
2.3.3 受试项目的接口232
2.3.4 试验的组织和管理232
2.3.5 物资保障233
2.3.6 维修性验证试验的准备233
2.3.7 维修性验证试验的实施233
2.3.9 维修性验证的基本准则234
2.3.8 试验数据的搜集、分析和信息反馈234
2.3.10 维修性验证试验报告235
2.4 维修性演示实例236
2.4.1 样机维修性演示的组织和管理236
2.4.1.1 样机维修性演示的组织236
2.4.1.2 样机维修性演示监督组的组织和职责236
2.4.1.3 样机维修性演示工作队的组成和职责236
2.4.4 演示的基本准则237
2.4.5.1 样机维修性演示阶段的划分237
2.4.5 样机维修性演示阶段的划分及各阶段的任务237
2.4.3 要求记录的数据内容和性质237
2.4.2 样机维修性演示对设施的要求237
2.4.1.4 样机库检验人员237
2.4.5.2 计划和预演示阶段的任务238
2.4.6 演示阶段的任务238
2.4.7 演示后阶段的任务238
2.4.8 “演示报告表”及其填写指南239
2.4.9 维修性检查表240
2.5.2.3 假设举例244
2.5.2.1 概述244
2.5.2.2 假设244
2.5.1 说明244
2.5 维修性时间指标的验证试验方法244
2.5.2 方法1 均值的试验244
2.5.2.4 样本量245
2.5.2.5 判定过程245
2.5.2.6 讨论245
2.5.2.7 示例245
2.5.3.3 假设举例246
2.5.3.5 判定过程246
2.5.3.4 样本量246
2.5.3 方法2 临界百分位数的试验246
2.5.3.2 假设246
2.5.3.1 概述246
2.5.2.8 OC曲线246
2.5.3.6 讨论247
2.5.3.7 示例248
2.5.3.8 OC曲线248
2.5.4.4 样本量n和接收数C249
2.5.4.3 假设举例249
2.5.4.5 判定过程249
2.5.4.1 概述249
2.5.4.2 假设249
2.5.4 方法3 临界维修时间或工时的试验249
2.5.4.6 讨论250
2.5.4.7 示例250
2.5.4.8 OC曲线250
2.5.5 方法4 中值的试验250
2.5.5.1 概述250
2.5.5.2 假设250
2.5.5.3 样本量250
2.5.5.5 判定过程250
2.5.5.4 任务选择和实施251
2.5.5.6 讨论251
2.5.6 方法5 工时率的试验(采用模拟故障)252
2.5.6.1 概述252
2.5.7.3 定量要求253
2.5.7.4 任务选择和实施253
2.5.7.2 使用条件253
2.5.7.5 接收/拒收准则253
2.5.6.3 判定过程253
2.5.7 方法6 平均修复时间Mc1和最大修复时间Mm41c1的验证试验253
2.5.6.2 讨论253
2.5.7.1 概述253
2.5.7.6 讨论256
2.5.8.2 使用条件257
2.5.8.3 定量要求257
2.5.8.4 任务选择和实施257
2.5.8.1 概述257
2.5.8 方法7 ?和Maxct的验证试验257
2.5.8.5 接收/拒收准则258
2.5.8.6 符号说明259
2.5.9 方法8 ?、Mmaxc1、和Mmaxp1的验证试验259
2.5.9.1 概述259
2.5.10.3 定量要求260
2.5.10.2 使用条件260
2.5.10.1 概述260
2.5.10 方法9 ?和(或)Mmaxpt的验证试验260
2.5.9.5 接收/拒收准则260
2.5.9.4 任务选择和实施260
2.5.9.3 定量要求260
2.5.9.2 使用条件260
2.5.10.4 任务选择和实施261
2.5.10.5 接收/拒收准则261
2.6 备选试验方案261
2.6.1 概述261
2.6.2 抽样方案假设261
2.6.3 对数正态分布261
2.6.4 符号说明262
2.6.5 固定样本试验(对数正态分布)262
2.6.5.1 介绍262
2.6.5.2 方法1 验证对数正态分布的中值262
2.6.5.3 方法2 验证临界维修时间263
2.6.5.4 方法3 对数正态参数的组合试验264
2.6.6.1 介绍268
2.6.6.2 方法4 验证对数正态分布的均值、中值或百分位数的序贯试验,a2已知268
2.6.6 序贯试验(对数正态分布)268
2.6.6.3 方法5 验证对数正态分布的中值的序贯试验,a2未知270
2.6.6.4 方法6 验证临界维修时间的序贯试验,a2未知271
2.6.7 非参数试验272
2.6.7.1 介绍272
2.6.7.2 方法7 验证中值或百分位数272
2.6.7.3 方法8 验证两个临界维修时间274
2.6.7.4 方法9 验证对数正态分布278
2.6.7.5 方法10 一项临界维修时间的序贯试验281
2.6.8 试验方法选择指导282
2.6.8.1 介绍282
2.6.8.2 10种方法的概况282
2.6.8.3 选择试验方法决策树简介282
参考文献284
第三章 测试性285
3.1 概述285
3.2 名词术语285
3.3.1.1 任务C1:测试性要求286
3.3.1 战术技术指标论证阶段286
3.3 研制与产生阶段的测试性工作286
3.3.1.2 任务C2:测试权衡287
3.3.1.3 任务C3:初步系统规范288
3.3.2 方案论证及确认阶段288
3.3.2.1 任务V1:测试性工作计划288
3.3.2.2 任务V2:把测试性结合到初步设计中289
3.3.2.3 任务V3A:权衡BIT、ETE和人工测试三者组合的备选设计方案291
3.3.2.4 任务V4:初步设计的固有测试性分析291
3.3.2.5 任务V5A:编写测试性分析报告292
3.3.2.7 任务V7A: 支持初步设计评审(PDR)293
3.3.2.6 任务V6:准备规范293
3.3.3 工程研制阶段294
3.3.3.1 任务F1:进行测试要求分析294
3.3.3.2 任务F2A:预测系统、分系统和每个UUT的故障检测和隔离水平294
3.3.3.3 任务F3A:测试性费用效益分析295
3.3.3.4 任务F4A:对每个C1,评审测试性特性和预计的测试性参数295
3.3.3.5 任务F5:测试性验证296
3.3.4.1 任务P1:监控生产过程趋向,审查更改测试性建议297
3.3.4 生产阶段297
3.3.3.8 任务F8A:提供现场测试性数据297
3.3.3.7 任务F7A:监控、评价和建议纠正措施297
3.3.3.6 任务F6A:编写测试性分析最终报告297
3.3.5 使用阶段298
3.3.5.1 任务D1A:监控使用和保障活动298
3.3.5.2 任务D1B:评审测试性更改计划298
3.4 测试性的规定及分配298
3.4.1 测试性的规定298
3.4.1.1 测试性定量要求的规定299
3.4.1.2 测试性分配301
3.5 测试性分析302
3.5.1 固有测试性分析302
3.5.2 系统测试性分析306
3.5.3 LRU测试性分析309
3.5.4 SRU测试性分析309
3.5.5 BIT分析310
3.5.5.1 BIT初步分析310
3.5.5.2 BIT性能分析311
3.6.2 方法1:GB 5080.5 的方法312
3.6.1 概述312
3.6 测试性验证312
3.6.3 方法2:RADC的方法314
3.6.4 MIL-STD-471A的方法321
3.7 测试性预计324
3.7.1 概述324
3.7.2 预计方程324
3.7.2.1 CND事件的分类324
3.7.2.2 预计方程的最终形式326
3.7.3 应用指南326
3.8.2.1 人工测试与自动测试的权衡328
3.8.2.2 BIT和ATE的权衡328
3.8 测试性设计328
3.8.2 测试性设计的权衡328
3.8.1 测试性设计的范围328
3.8.2.3 BIT和脱机测试的配合329
3.8.3 测试性设计的一般指南329
3.8.3.1 对BIT的设计的要求329
3.8.3.2 对BIT软件的要求329
3.8.3.3 为减少虚警的设计指南330
3.8.3.4 对划分的要求331
3.8.3.5 对测试点的要求332
3.8.3.6 对容差的要求333
3.8.3.7 对传感器的要求333
3.8.3.8 对指示器的要求334
3.8.3.9 关键测试参数的确定334
3.8.3.10 UUT与ETE的兼容性核对表335
3.8.3.11. 对初始化的要求335
3.8.3.12 对可控性的要求336
参考文献337
3.8.3.13 对可观性的要求337
第四章 软件可靠性338
4.1 引言338
4.2 软件可靠性的基本概念338
4.2.1 术语定义338
4.2.2 软件可靠性与硬件可靠性的区别和联系339
4.2.3 软件可靠性常用的度量参数343
4.3.2.1 语法错误344
4.3.2 软件错误分类344
4.3.1 软件错误及其根源344
4.3 软件错误及其分类344
4.3.2.2 语义错误345
4.3.2.3 运行期错误345
4.3.2.4 规范错误345
4.3.2.5 性能错误345
4.4 软件可靠性建模346
4.4.1 模型中使用符号说明346
4.4.2 分析模型346
4.4.2.1 失效间隔时间模型347
4.4.2.2 失效计数模型348
4.4.2.3 故障植入模型和以输入域为基础的模型348
4.4.2.4 软件可靠性模型假设及其限制349
4.4.2.5 软件可靠性模型在软件开发各阶段的应用351
4.4.2.6 建模的一般程序352
4.4.3 经验模型352
4.4.3.1 莫兰达模型352
4.5 软件可靠性预计及估计353
4.5.1 软件可靠性预计及估计的一般程序353
4.4.3.3 施奈德模型353
4.4.3.2 霍尔思特德模型353
4.5.2 软件可靠性预计及估计方法354
4.5.2.1 数学模型法354
4.5.2.2 经验公式法364
4.6 提高软件可靠性的方法366
4.6.1 规范编写368
4.6.2 设计368
4.6.2.1 逐步检查法368
4.6.2.3 避错技术369
4.6.2.2 故障抑制369
4.6.3 程序测试375
4.6.4 容错技术376
4.6.4.1 N版本编程法376
4.6.4.2 恢复程序块法377
4.6.4.3 N版本编程法和恢复块法的比较380
4.7 软件的验证与确认381
4.8 软件可靠性管理383
4.8.1 概述383
4.8.2 软件可靠性的管理活动及技术384
4.8.2.2 系统分析385
4.8.2.1 要求定义385
4.8.2.4 单元设计、代码及调试386
4.8.2.5 程序包综合及测试386
4.8.2.6 系统综合及测试386
4.8.2.7 验收测试386
4.8.2.8 大纲计划386
4.8.2.9 规范386
4.8.2.3 程序包设计386
4.8.2.10 数据系统387
4.8.2.11 型号项目大纲评审387
参考文献388
4.8.2.12 测试计划388
4.8.2.13 技术手册388
第五章 非工作状态的可靠性、维修性和测试性390
5.1 引言390
5.2 非工作环境391
5.2.1 系统寿命周期剖面391
5.2.2 环境考虑因素394
5.3 储存、运输和装卸397
5.3.2.1 运输设备、能力及限制401
5.3.2 运输401
5.3.2.2 运输环境及其影响401
5.3.3 装卸402
5.4 非工作状态对产品可靠性的影响403
5.4.1 非工作故障率通用模型403
5.4.2 温度影响404
5.4.3 设备通-断循环的影响405
5.4.4 环境因子406
5.4.5 可靠性综合模型407
5.5 非工作状态的可靠性设计408
5.5.1 元器件选择及控制408
5.5.1.1 概述408
5.5.1.2 元器件选择及控制的通用指南410
5.5.1.3 具体元器件的选择及控制指南412
5.6 非工作状态的维修性及维修414
5.6.1 非工作产品的维修方案414
5.6.1.1 “简捷”维修方案415
5.6.1.2 定期监控和(或)修理的维修方案416
5.6.2 非工作产品的维修性设计416
5.6.2.1 无维修设计考虑416
5.6.2.2 定期监控和(或)修理设计考虑417
5.7.1 测试方案422
5.7 非工作状态的测试性422
5.7.2 非工作系统的测试性设计考虑423
5.7.2.1 维修方案对测试性的影响423
5.7.2.2 测试效能对非工作系统的影响423
5.7.2.3 “通过-不通过”与“参数”测试424
5.7.2.4 非工作系统的测试性设计指南424
5.8 劣化的保护425
5.8.1 保护方法425
5.8.2 包装及其他保护技术427
5.8.2.1 组件包装428
5.8.2.2 防湿气428
5.8.2.3 电磁辐射保护技术429
5.8.2.4 其他的环境保护431
5.8.3 容器设计432
5.8.4 储存中的定期检验433
5.9 试验与评估437
5.9.1 内场试验和评估437
5.9.1.1 最坏情况电路容差分析437
5.9.1.2 寿命周期可靠性评估438
5.9.1.3 加速寿命试验440
5.9.1.4 环境应力筛选442
5.9.2 外场试验和评估442
5.9.2.1 战备完好性评估模型442
5.9.2.2 定期试验及再验证443
5.9.3 专门的试验和评估444
5.9.3.1 储存品实验室试验444
5.9.3.2 储存品飞行试验445
5.9.3.3 实时元器件老化试验445
参考文献446
第六章 以可靠性为中心的维修分析与装备预防性维修大纲447
6.1 引言447
6.1.1 RCMA的发展与应用447
6.2.1 维修对象449
6.2.2 按故障类型和后果确定维修工作449
6.2 RCM的基本理论449
6.2.3 维修方式与预定维修工作类型450
6.2.4 逻辑决断分析450
6.2.4.2 结构逻辑决断分析451
6.2.5 维修间隔期与工龄探索451
6.2.6 RCMA与保障性分析(LSA)451
6.2.4.1 系统/动力装置的逻辑决断分布451
6.3 装备预防性维修大纲451
6.3.1 维修大纲主要内容451
6.3.2 制订维修大纲的组织与过程454
6.3.2.1 组织形式454
6.3.2.2 编制过程455
6.4 系统/设备的RCMA方法和程序456
6.4.1 概述456
6.4.2 确定重要功能产品的详细步骤456
6.4.3 进行FMECA/FMEA458
6.4.4 逻辑决断458
6.4.4.1 逻辑决断图458
6.4.4.2 划分故障后果459
6.4.4.3 按各故障影响分支确定维修工作类型460
6.4.4.4 确定预防性维修工作类型462
6.4.6 确定维修级别470
6.4.5 确定预防性维修工作间隔期470
6.4.9 RCMA记录471
6.4.8 维修间隔期探索(工龄探索)471
6.4.7 非重要功能产品的维修工作471
6.4.10 波音757飞机液压刹车系统RCMA示例471
6.5 结构维修大纲的制订475
6.5.1 概述475
6.5.1.1 适用范围475
6.5.1.2 结构项目的特性475
6.5.1.3 结构维修工作分析的特点475
6.5.1.4 制定结构维修大纲所需的信息475
6.5.1.5 结构维修大纲的制定步骤476
6.5.2 重要结构项目的选择476
6.5.2.1 重要结构项目的定义476
6.5.2.2 重要结构项目选择方法476
6.5.2.3 典型的重要结构项目类型477
6.5.3 结构的逻辑决断分析477
6.5.3.1 决断时应考虑的因素477
6.5.3.2 决断过程477
6.5.4 重要结构项目的评级479
6.5.4.1 疲劳损伤的评级479
6.5.4.2 环境损伤的评级479
6.5.4.3 偶然损伤的评级480
6.5.5 重要结构项目检查要求的确定480
6.5.5.1 疲劳损伤检查要求480
6.5.5.2 环境损伤检查要求481
6.5.5.3 偶然损伤检查要求481
6.5.5.4 维修间隔期探索481
6.5.5.5 维修级别的确定481
6.5.5.6 检查工作的组合481
6.6 区域检查大纲和日常工作482
6.6.1 区域检查大纲482
6.6.1.1 概述482
6.6.1.2 区域检查大纲的制订步骤482
6.6.1.3 区域检查大纲制订法的示例483
7.3.2.2 编制计划的程序和要点483
6.6.1.4 区域检查大纲的形式484
6.6.2 润滑保养工作485
6.6.3 日常一般目视检查486
参考文献486
7.3.3 可靠性和维修性指标管理486
第七章 可靠性和维修性管理487
7.1 引言487
7.2 可靠性和维修性管理的特点488
7.2.1 参数应用的针对性要求进行正确的参数选择488
7.2.2 指标实现的阶段性决定了必须全过程跟踪489
7.2.3 可靠性和维修性评估对信息的依赖性要求加强信息管理489
7.2.4 可靠性和维修性保证的协同性需要跨部门合作489
7.3 产品寿命周期中的可靠性和维修性管理490
7.3.1 产品寿命周期内的可靠性和维修性管理活动490
7.3.2 可靠性和维修性工作计划492
7.3.2.1 计划制定的依据和原则493
7.3.2.3 可靠性和维修性工作项目的剪裁493
5.3.1 储存498
5.3.1.1 储存的类型、能力及限制498
5.3.1.2 爆炸物的储存498
5.3.1.3 储存期间引起质量及可靠性下降的因素499
7.3.4 可靠性和维修性工作过程控制500
7.3.4.1 对设计依据的控制500
7.3.4.2 对研制过程的监督与控制501
7.3.4.3 技术状态管理504
7.3.5 可靠性和维修性管理保证506
7.3.6 飞控系统研制阶段可靠性和维修性管理示例508
7.3.6.1 概述508
7.3.6.2 系统概况508
7.3.6.5 飞控系统研制阶段可靠性和维修性工作的计划流程509
7.3.6.4 系统及各分系统和LRU的可靠性和维修性工作项目509
7.3.6.3 适用的系统可靠性和维修性指标509
7.4 接口管理514
7.4.1 可靠性和维修性工作接口514
7.4.2 综合保障与可靠性和维修性工程的关系516
7.4.2.1 综合保障的定义、目标及工作516
7.4.2.2 对可靠性和维修性的影响516
7.4.2.3 综合保障将可靠性和维修性设计与保障要求相结合517
7.4.2.4 保障性分析是在设计中实现与保障结合的重要手段517
7.4.2.5 寿命周期各阶段综合保障考虑要点518
7.4.3 生产性与可靠性和维修性工程的关系519
7.4.3.1 生产性及生产要素520
7.4.3.2 对可靠性和维修性的影响520
7.4.3.3 对安全性的影响520
7.4.4 接口管理的实施520
7.4.4.1 实施接口管理的重要手段是建立信息渠道520
7.4.4.2 接口控制文件521
7.4.4.3 接口管理机构及职责521
7.5.1 概述522
7.5 可靠性及维修性数据522
7.5.2 数据收集与反馈523
7.5.3 故障报告及分析525
7.5.3.1 故障报告525
7.5.3.2 故障分析527
7.6 可靠性增长管理534
7.6.1 概述534
7.6.2 可靠性增长管理的准备工作535
7.6.2.1 用于可靠性增长的信息源535
7.6.2.4 可靠性增长预算536
7.6.2.2 可靠性增长潜力分析536
7.6.2.3 高层管理部门的职责536
7.6.2.5 可靠性增长管理的一般模式537
7.6.2.6 可靠性增长管理模式的调整537
7.6.3 可靠性增长管理计划538
7.6.3.1 起始点538
7.6.3.2 增长率538
7.6.3.3 确定主要试验阶段538
7.6.3.4 确定试验改进类型538
7.6.3.5 确定可靠性增长途径540
7.6.3.6 理想的可靠性增长曲线541
7.6.3.7 计划的可靠性增长曲线543
7.6.4 可靠性增长过程的跟踪与控制545
7.6.4.1 定性跟踪与控制545
7.6.4.2 定量跟踪与控制545
7.7 生产和使用的可靠性及维修性556
7.7.1 概述556
7.7.2 生产可靠性控制557
7.7.2.1 质量工程和质量控制557
7.7.2.2 生产可靠性的估计和控制559
7.7.2.3 生产可靠性试验和数据的收集分析560
7.7.3 生产维修性控制562
7.7.3.1 维修性工作要点562
7.7.3.2 生产阶段的维修性保证工作562
7.7.4 使用可靠性和维修性的估计和改进563
7.7.4.1 外场使用过程中造成可靠性和维修性下降的因素563
7.7.4.2 大修厂维修劣化控制563
7.7.4.3 维修计划对控制维修劣化的重要性564
7.7.4.5 可靠性和维修性增长565
7.7.4.4 可靠性和维修性评估和分析565
附录567
F7.1 国家(行业)有关可靠性和维修性管理的规定与标准567
F7.1.1 《军工产品质量管理条例》567
F7.1.2 《航空技术装备寿命和可靠性工作暂行规定(试行)》568
F7.1.3 《武器装备可靠性与维修性管理规定》568
F7.1.4 《装备研制与生产的可靠性通用大纲》(GJB 450)568
F7.1.5 《装备维修性通用规范》(GJB 368)569
F7.1.7 《装备可靠性维修性参数选择和指标确定要求 军用飞机》(GJB 1909.5)570
F7.1.6 《航空技术装备维修性管理大纲》(HB 6185)570
F7.1.8 《飞机维修品质规范》(GJB 312)572
F7.1.9 《厂际质量保证体系工作指南》(GJB/Z 2)573
F7.1.10 《设计评审》(GJB 1310)573
F7.1.11 《故障报告、分析和纠正措施系统》(GJB 841)574
F7.1.12 《航空产品可靠性增长 管理》(HB/Z 214.1)574
F7.1.13 《可靠性和维修性工程报告编写一般要求》(GJB/Z 23)574
F7.2 可靠性和维修性文件体系575
F7.2.1 体系构成575
F7.2.2 可靠性和维修性标准项目表576
参考文献580
1995《可靠性及维修性工程手册 下》由于是年代较久的资料都绝版了,几乎不可能购买到实物。如果大家为了学习确实需要,可向博主求助其电子版PDF文件(由曾天翔主编 1995 北京:国防工业出版社 出版的版本) 。对合法合规的求助,我会当即受理并将下载地址发送给你。
高度相关资料
-
- 舰船产品可靠性工程可靠性设计
- 1995 哈尔滨:哈尔滨工程大学出版社
-
- 武器系统可靠性 工程手册
- 1992
-
- 可靠性工程与机械维修
- 1983
-
- 可靠性与维修性
- 1987 北京:机械工业出版社
-
- 可靠性工程学
- 1990 黑龙江科学技术出版社;电子工业出版社
-
- 可靠性与可用性评估手册
- 1986 上海:上海交通大学出版社
-
- 可靠性及维修性工程手册 上
- 1994 北京:国防工业出版社
-
- 可靠性与维修工程
- 1992 石家庄:河北教育出版社
-
- 可靠性工程概论
- 1989 北京:国防工业出版社
-
- 电子机械可靠性与维修性
- 1990 哈尔滨:黑龙江科学技术出版社
-
- 可靠性工程
- 1990 北京:清华大学出版社
-
- 维修、更换和可靠性
- 1985 北京:机械工业出版社
-
- 可靠性工程
- 1988 烃加工出版社
-
- 机器人的可靠性、维修性、安全性
- 1994 北京:科学出版社
-
- 可靠性工程
- 1985 北京:宇航出版社
提示:百度云已更名为百度网盘(百度盘),天翼云盘、微盘下载地址……暂未提供。➥ PDF文字可复制化或转WORD