《表2 不同固溶温度下Mn-N合金化双相不锈钢马氏体相变的开始与结束应变》
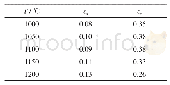
本系列图表出处文件名:随高清版一同展现
《固溶温度对Mn-N型双相不锈钢拉伸变形行为的影响》
Mn-N合金化双相不锈钢样品工程应力-应变曲线上表现出的“S”型形状特征(图3)表明,钢的塑性变形超过一定程度后加工硬化率增加,这主要是钢中亚稳奥氏体相发生了形变诱导马氏体相变引发TRIP效应导致的。形变诱导马氏体的形核与长大,即马氏体转变动力学决定着材料的加工硬化率。Mn-N合金化双相不锈钢真应力(σ)及加工硬化率(θ)随真应变(ε)的变化曲线如图6所示。由图可见,钢在各固溶温度下的加工硬化率均表现出“三阶段”硬化特征,与已报道的TRIP型双相不锈钢加工硬化率曲线(θ-ε)特征相同[8,13,16]。在变形初始阶段,θ迅速降低。室温条件下,双相不锈钢中奥氏体为软相,铁素体为硬相[20],因此,变形初始阶段,钢中软相奥氏体先变形。研究[21,22]表明,在变形初期,具有低层错能的fcc结构金属(本实验用钢对应为奥氏体相)变形主要以位错滑移为主,位错亚结构多表现为位错偶极子、Cottrell气团等,而位错的交滑移不易发生,从而使得螺旋位错的相互湮灭过程(动态回复过程)受限。因此,不锈钢在该阶段主要与奥氏体的位错硬化有关。随着应变的增加,马氏体开始在亚稳奥氏体中形核长大,使得θ上升并逐渐达到最大值。形变诱导马氏体相变进一步发展,使得马氏体含量虽仍在增加,但其转变速率降低,从而使得θ再次下降。随着应变进一步增加,马氏体转变量趋于饱和,达到最大值,相变结束,从而使得变形出现失稳,颈缩发生直至断裂[23]。这也表明,亚稳奥氏体相的形变诱导马氏体相变决定着双相不锈钢整体的加工硬化模式[24]。在θ-ε曲线上,θ开始上升时对应的应变被认为是形变诱导马氏体相变开始点(εs),而塑性失稳点对应的应变为相变终了点(εf)[5]。根据Considére失稳判定准则,求得失稳应变条件[25],即:θ-ε与σ-ε曲线的交点对应的应变,如图6所示。表2列出了不同固溶温度下的εs和εf。可见,随着固溶温度的增加,总体趋势上εs逐渐增大,而εf逐渐减小。说明提高固溶温度会抑制马氏体相变的发生与发展,即抑制TRIP效应而影响加工硬化规律。Herrera等[5]提出,Mn-N型双相不锈钢要获得更高的塑性,亚稳奥氏体相不仅要能形成TRIP效应,还要保证能在较大应变范围内始终存在TRIP效应,即充分延迟颈缩,增加均匀变形。从图6可见,随着固溶温度的升高,加工硬化率降低。通常加工硬化率越低,材料越容易变形失稳[26],可见,固溶温度较高时,由于亚稳奥氏体相中的TRIP效应被抑制,使得材料在拉伸变形时颈缩较早发生。值得注意的是,各固溶温度下应变超过εf后,很快达到断裂应变,不均匀变形区很小,说明试件颈缩失稳后迅速断裂。
图表编号 | XD0035673400 严禁用于非法目的 |
---|---|
绘制时间 | 2019.04.11 |
作者 | 金淼、李文权、郝硕、梅瑞雪、李娜、陈雷 |
绘制单位 | 燕山大学机械工程学院、燕山大学机械工程学院、燕山大学机械工程学院、国家冷轧板带装备及工艺工程技术研究中心、燕山大学机械工程学院、燕山大学机械工程学院、燕山大学机械工程学院、国家冷轧板带装备及工艺工程技术研究中心 |
更多格式 | 高清、无水印(增值服务) |