《表3 TC6合金在不同介质中的磨痕参数》
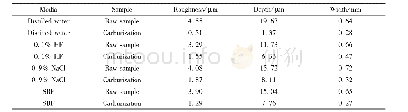
本系列图表出处文件名:随高清版一同展现
《TC6钛合金渗碳层在不同介质环境中的腐蚀磨损性能》
图8为TC6合金原样和渗碳样在4种介质中磨损后的三维形貌图及轮廓曲线。从图可以看到,渗碳处理后合金的表层粗糙度增大,但由于硬度的提高,磨损过程中只有凸起部分发生接触和轻微磨损,因而磨损量较小,摩擦因数总体也比原样低。在不同介质中,未经渗碳处理的TC6合金磨损后表面形成了较深的犁沟且犁沟内附着磨削,而渗碳后的TC6合金磨损后表面相对原样而言比较光滑仅有少量较浅的犁沟。这是由于TC6合金基体本身较软,增加了磨面间的咬合度,使得磨损过程中产生大量的磨削并附着在对磨球及合金表面,其磨损机制以粘着磨损为主[25];而经渗碳处理后试样表层的Ti C陶瓷相具有较高的硬度,能有效减缓Al2O3球对表面的切割作用,在磨损过程中磨削的产生将减小磨面间的接触面面积,其磨损机制主要为磨粒磨损[26]。在蒸馏水中,渗碳处理后的TC6合金磨痕最浅,约为1.37μm;而原样的达到19.63μm,是渗碳样的14倍(表3)。在0.1%HF溶液中,腐蚀是造成材料损失的主要因素。从图8(c)可以看出,原样的整个表面的磨痕比较均匀,这是由于犁沟中的凸起和凹陷部分在腐蚀液中形成腐蚀电池,在F-作用下,凸起区域迅速被腐蚀。同时未磨损区域因发生较快的全面腐蚀,因而在0.1%HF溶液中原样与渗碳样的相对磨痕最浅,粗糙度最低。在0.9%NaCl溶液中原样在摩擦过程中产生较深、较宽且均匀有序的犁沟,相对磨痕深度达15.72μm;渗碳样在0.9%NaCl溶液中的磨痕形貌如图8(f)所示,其表面受损情况较轻,相对磨痕深度为8.11μm。结合对应的开路电位,渗碳层的不完整性导致电位降低,但是与原样相比,耐蚀性能仍较优。在SBF溶液中,原样表面由于受SBF溶液中Cl-、HPO42-、及H2PO4-等离子的影响,相对磨痕深度为15.04μm,且磨痕的局部位置产生塑性变形。由图8(h)可知,渗碳后的TC6合金表面受磨损程度小于原样,相对磨痕深度为7.76μm,说明渗碳层的存在能较好地抑制SBF溶液中各类离子对内部基体的破坏。
图表编号 | XD00182748700 严禁用于非法目的 |
---|---|
绘制时间 | 2020.04.23 |
作者 | 代燕、吴旋、杨峰、李坤茂、刘静、欧梅桂 |
绘制单位 | 贵州师范大学材料与建筑工程学院、贵州师范大学材料与建筑工程学院、贵州师范大学材料与建筑工程学院、贵州大学材料与冶金学院、贵州师范大学材料与建筑工程学院、贵州大学材料与冶金学院 |
更多格式 | 高清、无水印(增值服务) |