《可靠性工程与质量管理标准常用术语汇编》
作者 | 顾唯明,张宁生编 编者 |
---|---|
出版 | 北京:国防工业出版社 |
参考页数 | 198 |
出版时间 | 1997(求助前请核对) 目录预览 |
ISBN号 | 7118016802 — 求助条款 |
PDF编号 | 87525058(仅供预览,未存储实际文件) |
求助格式 | 扫描PDF(若分多册发行,每次仅能受理1册) |
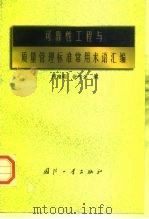
1.基本术语1
1.1实体1
1.2 过程1
1.3 供应链1
1.4 程序1
1.5 产品2
1.6 最终产品3
1.7 硬件3
1.8 软件3
1.11 服务4
1.10 分系统4
1.9 系统4
1.12 服务提供5
1.13 组织5
1.14 组织结构5
1.15 公司6
1.16 顾客6
1.17 供方6
1.25 分供方7
1.24 分承包方7
1.22 承包方7
1.23 商务第一方7
1.20 投标7
1.19 采购方7
1.18 需方7
1.21 商务第二方7
1.26 合同8
1.27 委托方8
1.28 修理的产品8
1.29 不修理的产品8
1.33 时间区间9
1.36 量度9
1.35 累积时间9
1.34 持续时间9
1.32 时刻9
1.31 时间9
1.30 规定功能9
1.37 工作10
1.38 修改(对产品而言)10
1.39 寿命周期10
1.40 阶段10
1.41 论证阶段10
1.42 研制阶段10
1.43 开发10
1.44 生产阶段10
1.50 软件验证11
1.49 验证11
1.48 鉴定11
1.47 评定11
1.46 退役阶段11
1.45 使用阶段11
1.51 确认12
1.52 软件确认12
1.53 剪裁12
1.54 软件产品12
1.55 软件项12
2.1.1 质量13
2.1 质量13
2.质量管理13
2.1.2等级15
2.1.3 产品质量等级品率16
2.1.4 质量要求16
2.1.5 社会要求16
2.1.6 相容性16
2.1.7 互换性17
2.1.8 合格(符合)17
2.1.9 不合格(不符合)17
2.1.14 百分不合格品率18
2.1.13 轻不合格品18
2.1.15 符合性18
2.1.11 致命不合格品18
2.1.10 不合格品18
2.1.12 严重不合格品18
2.1.17 致命缺陷19
2.1.18 严重缺陷19
2.1.19 轻缺陷19
2.1.20 每百单位产品缺陷数19
2.1.21 产品责任19
2.1.22 鉴定过程20
2.1.23 鉴定合格20
2.1.24 检验20
2.1.25 可检验性20
2.1.26 检验合格证书20
2.1.30 质量事故21
2.2.1 质量方针21
2.2 质量体系21
2.1.27 自检21
2.1.29 质量凭证21
2.1.28 客观证据21
2.2.2 质量目标22
2.2.3 质量管理22
2.2.4 质量策划22
2.2.5 质量控制23
2.2.6 质量保证23
2.2.7 质量体系24
2.2.8 厂际质量保证体系25
2.2.9 质量保证体系认证25
2.2.10 全面质量管理25
2.2.12 管理评审26
2.2.11 质量改进26
2.2.13 合同评审27
2.2.14 设计评审27
2.2.15 工艺评审28
2.2.16 质量手册28
2.2.17 质量计划29
2.2.18 规范30
2.2.19 记录30
2.2.20 可追溯性30
2.2.23 基线31
2.2.22 技术状态31
2.2.21 质量工程31
2.2.24 技术状态记实32
2.2.25 技术状态审核32
2.2.26 技术状态控制32
2.2.27 技术状态标识32
2.2.28 技术状态管理32
2.2.29 工程更改32
2.2.30 质量保证文件32
2.2.31 质量保证组织32
2.2.32 质量保证大纲32
2.3.2 质量成本33
2.3.3 质量损失33
2.3 工具与技术33
2.3.1 质量环33
2.3.4 质量保证模式34
2.3.5 证实程度34
2.3.6 质量评价34
2.3.7 质量监督35
2.3.8 质量体系评审35
2.3.9 停止点36
2.3.10 质量审核36
2.3.11 过程质量审核37
2.3.12 过程质量评价37
2.3.13 产品质量审核37
2.3.14 产品质量认证37
2.3.21 审核工作管理机构38
2.3.20 受审核方38
2.3.19 质量审核组长38
2.3.22 研制程序38
2.3.15 服务质量审核38
2.3.18 质量审核员38
2.3.17 质量审核观察结果38
2.3.16 观察结果38
2.3.23 定型39
2.3.24 预防措施39
2.3.25 纠正39
2.3.26 纠正措施39
2.3.31 生产许可,偏离许可40
2.3.30 原样使用40
2.3.28 不合格处置40
2.3.27 废品40
2.3.29 不合格品审理委员会40
2.3.32 特许,让步41
2.3.33 返工41
2.3.34 返修41
2.3.38 工序能力42
2.3.40 工序控制点42
2.3.39 工序控制42
2.3.41 关键工序42
2.3.37 工序42
2.3.36 一次交验合格率42
2.3.35 标准返修规程42
2.3.42 特种工艺43
2.3.43 关键件43
2.3.44 重要件43
2.3.45 首件鉴定43
2.3.46 首件三检43
2.3.47 质量会签43
2.3.48 质量损失率43
2.3.49 内部损失成本43
2.4.2 单位产品44
2.4.1 抽样检验44
2.4 抽样技术44
2.3.55 质量责任制44
2.3.54 双岗制44
2.3.52 质量信息44
2.3.51 质量职能44
2.3.50 外部损失成本44
2.3.53 质量标志44
2.4.8 样本单位,样品45
2.4.13 计数检查45
2.4.12 检查45
2.4.11 平均样本量,平均样本大小45
2.4.9 样本45
2.4.10 样本量,样本大小45
2.4.7 随机抽样45
2.4.6 批量45
2.4.5 批次45
2.4.4 连续批45
2.4.3 检查批(简称:批)45
2.4.14 检查水平46
2.4.15 样本量字码,样本大小字码46
2.4.16 逐批检查46
2.4.17 初检查46
2.4.18 过程平均46
2.4.19 可接收质量水平46
2.4.20 抽样方案46
2.5.4 物理性能47
2.5.3 力学性能47
2.5.1 标准物质47
2.5 理化检验47
2.5.2 理化试验47
2.5.9 金相分析48
2.5.13 化学成分分析48
2.5.11 光学金相组织分析48
2.5.10 宏观组织分析48
2.5.12 电子显微组织分析48
2.5.8 电化学腐蚀48
2.5.7 化学腐蚀48
2.5.6 金属的腐蚀48
2.5.5 化学性能48
2.6 计量49
2.6.1 计量确认49
2.6.2 测量设备49
2.6.3 测量49
2.6.4 被测量49
2.6.5 影响量49
2.6.6 测量准确度49
2.6.7 测量不确定度49
2.6.11 调整50
2.6.10 测量器具50
2.6.12 规定的测量范围50
2.6.8 (绝对)测量误差50
2.6.9 修正值50
2.6.13 标准条件51
2.6.14 (指示装置)的分辨力51
2.6.15 稳定性51
2.6.16 漂移51
2.6.17 (测量仪器的)允许误差限51
2.6.18 (测量)标准51
2.6.19 国际(测量)标准52
2.6.20 国家(测量)标准52
2.6.21 溯源性52
2.6.22 校准52
3.3 固有能力53
3.4 特性53
3.产品特性53
3.2系统效能53
3.1 效能53
3.5 特性分类54
3.6 重要特性54
3.7 关键特性54
3.8 一般特性54
3.9 耐久性55
3.10 寿命55
3.11 寿命周期费用55
3.12 寿命剖面55
3.14 可靠性56
3.13 寿命单位56
3.15 基本可靠性57
3.16 任务剖面57
3.17 任务可靠性57
3.18 软件可靠性57
3.19 维修性58
3.20 任务维修性58
3.21 维修保障性58
3.24 可信性59
3.22 保障性59
3.23 可用性59
3.25 可达性60
3.26 测试性60
3.27 安全性60
3.28 战备完好性60
3.29 可生产性61
3.30 适用性61
4.1.4 严重失效62
4.1.3 非致命失效62
4.1.5 轻度失效62
4.1.6 误用失效62
4.1.1 失效62
4.1 失效62
4.失效、故障、失误与产品的状态62
4.1.2致命失效62
4.1.7 误操作失效63
4.1.8 弱质失效63
4.1.9 本质失效63
4.1.10 设计失效63
4.1.11 制造失效63
4.1.12 老化失效,耗损失效63
4.1.13 突然失效63
4.1.16 关联失效64
4.1.17 非关联失效64
4.1.15 灾变失效64
4.1.14 渐变失效,漂移失效64
4.1.18 独立失效65
4.1.19 从属失效65
4.1.20 失效原因65
4.1.21 系统性失效,重复性失效65
4.1.22 完全失效66
4.1.23 退化失效66
4.1.24 早期失效66
4.1.25 偶然失效66
4.1.26 部分失效66
4.1.27 间歇失效66
4.2 故障66
4.2.1 故障66
4.2.8 弱质故障67
4.2.9 设计故障67
4.2.7 误操作故障67
4.2.10 制造故障67
4.2.11 非责任故障67
4.2.4 重要故障67
4.2.5 次要故障67
4.2.3 非致命故障67
4.2.2 致命故障67
4.2.6 误用故障67
4.2.12 偶然故障68
4.2.13 老化故障,耗损故障68
4.2.14 渐变故障68
4.2.15 程序-敏感故障68
4.2.20 隐蔽功能故障69
4.2.22 间歇故障69
4.2.21 持久故障69
4.2.16 数据-敏感故障69
4.2.19 单点故障69
4.2.18 部分故障69
4.2.17 完全故障,功能阻碍故障69
4.2.29 从属故障70
4.2.30 非关联故障70
4.2.28 独立故障70
4.2.32 潜在故障70
4.2.33 系统性故障70
4.2.31 多重故障70
4.2.26 确定性故障70
4.2.25 指令故障70
4.2.24 诱发故障70
4.2.23 原发故障70
4.2.27 非确定性故障70
4.2.34 环境应力筛选故障71
4.2.35 非环境应力筛选故障71
4.2.36 故障原因71
4.2.37 故障产品71
4.3 失误71
4.3.1 失误71
4.3.2 差错71
4.4.7 外因不能工作状态72
4.4.6 不能工作状态72
4.4.5 闲置状态,空闲状态72
4.4.8 不可用状态,内因不能工作状态72
4.4.9 可用状态72
4.4 产品的状态72
4.4.4 待命状态72
4.4.3 不工作状态72
4.4.2 工作状态72
4.4.1 能工作72
4.4.10 忙碌状态73
4.4.11 致命状态73
5.4 维护74
5.3 维修事件74
5.2 软件维修74
5.维修74
5.1维修74
5.8 维修策略75
5.10 维修作业线75
5.9 维修规则75
5.11 维修约定级75
5.7 维修规划75
5.6 维修方针75
5.5 维修准则75
5.12 初始约定层次76
5.13 其他约定层次76
5.14 维修等级76
5.15 维修级别76
5.16 预防性维修76
5.17 修复性维修77
5.18 受控维修77
5.19 计划性维修77
5.24 自动维修78
5.23 遥控维修78
5.25 基本的维修作业78
5.26 逾期维修78
5.22 非现场维修78
5.21 现场维修78
5.20 非计划性维修78
5.27 维修工作79
5.28 修理79
5.29 故障识别79
5.30 故障定位79
5.31 故障诊断79
5.32 故障隔离79
5.33 故障修复79
5.40 减弱功能的维修80
5.39 妨碍功能的维修80
5.38 影响功能的维修80
5.37 维修的实体80
5.36 监测80
5.35 恢复80
5.34 功能核查80
5.41 不影响功能的维修81
6.时间82
6.1维修的有关时间82
6.1.1 维修时间82
6.1.2 维修人时82
6.1.3 实际维修时间82
6.1.4 预防性维修时间82
6.1.5 修复性维修时间82
6.1.11 未检出故障时间83
6.1.10 维护时间83
6.1.9 维修事件的平均直接维修工时83
6.1.7 实际的修复性维修时间83
6.1.6 实际的预防性维修时间83
6.1.8 维修活动的平均直接维修工时83
6.1.12 管理延迟(对于修复性维修)85
6.1.13 后勤延迟85
6.1.14 故障修复时间85
6.1.15 技术延迟85
6.1.16 检测85
6.1.17 检查时间85
6.1.18 故障诊断时间85
6.1.24 自动恢复时间86
6.2.2 工作时间86
6.2.1 在编时间86
6.2 产品状态的有关时间86
6.1.21 修理实施时间86
6.1.23 修理准备时间86
6.1.22 维护准备时间86
6.1.20 修理时间86
6.1.19 故障定位时间86
6.2.3 可工作时间87
6.2.4 不工作时间87
6.2.5 需求时间87
6.2.6 无需求时间87
6.2.7 待命时间87
6.2.12 不可工作时间88
6.2.11 不可用时间88
6.2.13 故障停机时间88
6.2.8 延误时间88
6.2.9 闲置时间88
6.2.10 不能工作时间88
6.2.14 累积不可用时间89
6.2.15 外因不能工作时间89
6.2.16 可用时间89
6.2.17 杂项时间89
6.2.18 平均需求间隔时间89
6.2.24 再次使用准备时间90
6.2.28 重复运行时间90
6.2.27 程序测试时间90
6.2.26 程序生产时间90
6.2.25 环境损失时间90
6.2.22 系统生产时间90
6.2.23 系统测试时间90
6.2.21 改进时间90
6.2.20 反应时间90
6.2.19 任务时间90
6.3.8 恒定失效率期91
6.3.7 恒定失效密度期91
6.3.6 早期失效期91
6.3.5 恢复前时间91
6.3.4 失效间工作时间91
6.3.2 失效前时间91
6.3.1 首次失效前时间91
6.3 可靠性特征量的有关时间91
6.3.3 失效间隔时间91
6.3.9 耗损失效期92
7.1.2 瞬时不可用度93
7.1.3 平均可用度93
7.1.4 平均不可用度93
7.1.1 瞬时可用度93
7.1 可用性特征量93
7.可用性、可靠性、维修性、维修保障性特征量93
7.1.5渐近可用度94
7.1.6 极限有效度94
7.1.7 稳态可用度94
7.1.8 渐近不可用度94
7.1.9 稳态不可用度95
7.1.10 渐近平均可用度95
7.1.11 渐近平均不可用度95
7.1.12 平均可用时间95
7.1.13 平均累积不可用时间95
7.2.1 可靠度96
7.1.17 有效度的观测值96
7.2 可靠性特征量96
7.1.16 使用可用性96
7.1.15 可达可用性96
7.1.14 固有可用性96
7.2.2 可靠度的观测值97
7.2.3 累积失效概率97
7.2.4 累积失效概率的观测值97
7.2.5 固有可靠性和维修性值97
7.2.6 使用可靠性和维修性值98
7.2.7 系统可靠性和维修性参数98
7.2.8 外推可靠性量度98
7.2.9 瞬时失效率98
7.2.13 瞬时失效密度99
7.2.12 平均失效率的观测值99
7.2.11 失效率的观测值99
7.2.10 平均失效率99
7.2.14 平均失效密度100
7.2.15 平均首次失效前时间100
7.2.16 平均失效前时间100
7.2.17 平均失效间隔时间100
7.2.18 平均失效间工作时间101
7.2.19 平均故障间隔时间(MTBF)的验证区间101
7.2.20 MTBF的观测值(点估计)101
7.2.21 MTBF的检验下限θ1101
7.2.22 MTBF的检验上限θ0101
7.2.23 MTBF的预计值θp101
7.2.24 平均不能工作事件间隔时间101
7.2.29 可靠寿命的观测值102
7.2.28 可靠寿命102
7.2.30 贮存寿命102
7.2.25 致命性故障间的任务时间102
7.2.26 使用寿命102
7.2.27 平均寿命的观测值(平均无故障工作时间的观测值)102
7.3 维修性特征量103
7.3.1 维修度103
7.3.2 瞬时修复率103
7.3.3 平均修复率103
7.3.6 平均不可用时间104
7.3.7 平均修理时间104
7.3.5 平均维修人时104
7.3.4 平均修复率的观测值104
7.3.8 平均修复时间的观测值105
7.3.9 P—分位修理时间105
7.3.10 平均实际修复性维修时间105
7.3.11 平均恢复前时间105
7.3.12 恢复功能用的任务时间105
7.3.13 平均系统恢复时间105
7.3.14 平均维护时间105
7.3.15 平均维修间隔时间105
7.4 维修保障性特征量106
7.3.20 维修工时率106
7.4.1 平均管理延迟106
7.4.2 P—分位管理延迟106
7.3.18 故障识别比106
7.3.19 修复比106
7.3.17 平均拆卸间隔时间106
7.3.16 平均维修活动间隔时间106
7.4.3 平均后勤延迟107
7.4.4 P—分位后勤延迟107
8.1.5 失效安全108
8.1.4 非工作贮备108
8.1.3 备用冗余108
8.1.2 工作冗余108
8.1.1 冗余108
8.1 设计108
8.设计与分析108
8.1.6故障裕度109
8.1.7 故障掩盖109
8.1.8 预计109
8.1.9 可靠性预计109
8.1.10 可靠性模型109
8.1.16 应力模型110
8.1.15 应力分析110
8.1.17 可靠性应力模型110
8.1.18 应力强度模型110
8.1.13 应力110
8.1.12 可靠性框图110
8.1.11 可靠性分配110
8.1.14 强度110
8.1.19 状态转移图111
8.1.20 维修性模型111
8.1.21 维修性预计111
8.1.22 维修性分配111
8.1.23 维修树111
8.1.30 降额112
8.1.34 并联系统112
8.1.33 并联112
8.1.32 串联系统112
8.1.31 串联112
8.1.26 费用效能112
8.1.29 设计规范112
8.1.28 费用效能分析112
8.1.27 效费比112
8.1.25 费用112
8.1.24 以可靠性为中心的维修分析112
8.1.42 结构函数113
8.1.41 结构零件113
8.1.39 结构组件113
8.1.40 结构细节113
8.1.37 旁联系统113
8.1.36 表决系统113
8.1.35 单调关联系统113
8.1.38 潜在通路分析113
8.2.4 体积功率密度114
8.2.7 内热阻114
8.2.6 接触电阻114
8.2.5 热阻114
8.2.8 安装热阻114
8.2.2 热特性114
8.2.1 热环境114
8.2 电子设备热设计114
8.1.43 可靠性和维修性计算114
8.2.3 热流密度114
8.2.16 蒸发冷却115
8.2.21 冷板115
8.2.20 深冷冷却115
8.2.19 性能系数115
8.2.18 热电致冷115
8.2.17 热管115
8.2.13 强迫冷却115
8.2.15 间接液体冷却115
8.2.14 直接液体冷却115
8.2.12 自然冷却115
8.2.11 特征尺寸115
8.2.10 定性温度115
8.2.9 热网络115
8.3 电子设备可靠性预计116
8.2.27 热沉116
8.3.1 基本失效率λb116
8.3.2 工作失效率λP116
8.2.24 温度稳定116
8.2.25 射流冷却116
8.2.23 液冷式模块116
8.2.22 导热模块116
8.2.26 紊流器116
8.3.3 环境类别与环境系数πE117
8.3.4 质量等级与质量系数πQ117
8.3.5 工作失效率模型中的其它调整系数(π系数)117
8.3.6 通用工作环境温度118
8.3.7 通用失效率λG118
8.4.4 危害度119
8.4.6 故障模式与影响分析119
8.4.5 失效模式、效应及后果分析119
8.4.1 故障模式119
8.4.3 故障影响119
8.4.2 失效模式119
8.4 故障模式、影响及危害性分析119
8.4.7 故障模式、影响与危害度分析120
8.4.8 严酷度120
8.5 故障树分析120
8.5.1 故障树120
8.5.2 故障树分析120
8.5.5 底事件121
8.5.6 基本事件121
8.5.3 失效树分析121
8.5.4 事件121
8.5.7 未探明事件122
8.5.8 结果事件122
8.5.9 顶事件122
8.5.10 中间事件123
8.5.11 特殊事件123
8.5.12 开关事件123
8.5.13 条件事件123
8.5.14 逻辑门123
8.5.16 或门124
8.5.17 非门124
8.5.15 与门124
8.5.18 顺序与门125
8.5.19 表决门125
8.5.20 异或门126
8.5.21 禁门126
8.5.22 转移符号126
8.5.23 相同转移符号126
8.5.24 相似转移符号127
8.5.25 二状态故障树127
8.5.26 多状态故障树127
8.5.35 最小割集128
8.5.34 割集128
8.5.33 最大模块128
8.5.32 模块128
8.5.31 成功树128
8.5.29 非正规故障树128
8.5.28 正规故障树128
8.5.27 规范化故障树128
8.5.30 对偶故障树128
8.5.36 底事件结构重要度129
8.5.37 底事件概率重要度129
8.5.38 底事件的相对概率重要度129
8.6.3 人员数量与技术等级130
8.6.6 技术资料130
8.6.5 保障设备130
8.6.4 供应保障130
8.6.2 综合保障要素130
8.6.1 综合保障130
8.6 保障性分析130
8.6.7 训练与训练保障131
8.6.8 计算机资源保障131
8.6.9 保障设施131
8.6.10 设计接口131
8.6.11 包装、装卸、储存和运输131
8.6.12 保障资源131
8.6.13 保障系统131
8.6.20 共用性132
8.6.19 基准比较系统132
8.6.18 使用方案132
8.6.17 运输性132
8.6.15 保障计划132
8.6.14 保障方案132
8.6.16 保障性分析132
8.7.5 鉴别比d133
8.7.9 事故133
8.7.7 危险严重性133
8.7.6 危险133
8.7.8 危险可能性133
8.7.4 判决(决策)风险133
8.7.3 生产方风险α133
8.7.2 使用方风险β133
8.7.1 风险133
8.7 安全性分析133
9.试验、数据、失效分析与纠正、改进与增长134
9.1试验134
9.1.1 试验134
9.1.2 试验规范134
9.1.3 验证试验134
9.1.4 测定试验134
9.1.5 可靠性测定试验134
9.1.6 可靠性验证试验134
9.1.7 验收试验134
9.1.8 鉴定试验134
9.1.13 耐久性试验135
9.1.12 现场可靠性试验135
9.1.9 实验室试验135
9.1.10 实验室可靠性试验135
9.1.11 现场试验135
9.1.14 寿命试验136
9.1.15 加速试验136
9.1.16 加速系数136
9.1.17 时间加速系数136
9.1.18 失效率加速系数136
9.1.22 恒定应力试验137
9.1.25 优势频率137
9.1.23 筛选试验137
9.1.24 环境应力筛选试验137
9.1.21 序进应力试验137
9.1.20 步进应力试验137
9.1.19 失效密度加速系数137
9.1.26 瞬态故障138
9.1.27 增长试验138
9.1.28 试验周期138
9.1.29 活动状态138
9.1.30 工作参数或环境参数138
9.1.31 工作参数或环境参数的严酷度138
9.1.32 严酷度等级138
9.1.33 环境条件138
9.1.34 工作条件138
9.2.1 观测数据139
9.2.2 试验数据139
9.2 数据139
9.2.3 现场数据139
9.1.36 代表性严酷度139
9.1.38 维修性验证139
9.1.37 维修性检验139
9.1.35 试验严酷度139
9.1.39 边缘测试,边缘检测139
9.3.2 失效分析140
9.3.4 失效物理140
9.3.3 失效机理140
9.3.5 纠正措施140
9.3.1 故障报告140
9.3 失效分析与纠正140
9.2.4 基准数据140
9.3.6 偶然损伤141
9.3.7 损坏模式141
9.3.8 损坏影响141
9.3.9 环境损伤141
9.3.10 耗损141
9.3.11 退化141
9.4 改进与增长141
9.4.1 老练141
9.4.5 残余性薄弱环节142
9.4.4 系统性薄弱环节142
9.4.3 可靠性增长142
9.4.2 可靠性改进142
9.4.6 残余性失效143
9.4.7 A类失效143
9.4.8 B类失效143
9.4.9 计划的可靠性量度143
9.4.10 反应速率模型143
10.可靠性与维修性管理144
10.1可靠性和维修性管理144
10.2 可靠性和维修性保证144
10.3 可靠性和维修性保证大纲144
10.7 可靠性计划145
10.9 可靠性和维修性监察145
10.8 可靠性和维修性审计145
10.5 可靠性和维修性控制145
10.6 可靠性和维修性计划145
10.4 可靠性和维修性大纲145
10.10 可靠性和维修性工程146
10.11 可靠性保证大纲146
10.12 可靠性认证146
10.13 预防性维修大纲146
10.14 可靠性程序146
11.6 使用的148
11.5 固有的148
11.4 估计的148
11.2 预计的148
11.1 真实的148
11.修饰词148
11.3外推的148
11.7 平均的149
11.8 P—分位149
11.9 瞬时的149
11.10 稳态的149
11.11 验证过的149
11.12 确认过的149
12.3 工业行业或经济部门150
12.4 ISO 9000族150
12.1 调准150
12.2 调试150
12.其他150
12.5接口设备151
12.6 流程性材料151
12.7 受益者151
12.8 成套技术资料151
12.9 工业总产值152
汉语拼音索引153
英文索引167
附表 可靠性、质量管理国家标准和国家军用标准一览表196
1997《可靠性工程与质量管理标准常用术语汇编》由于是年代较久的资料都绝版了,几乎不可能购买到实物。如果大家为了学习确实需要,可向博主求助其电子版PDF文件(由顾唯明,张宁生编 1997 北京:国防工业出版社 出版的版本) 。对合法合规的求助,我会当即受理并将下载地址发送给你。
高度相关资料
-
- 可靠性工程与管理实践 怎样提高产品可靠性
- 1993 上海:上海科学技术出版社
-
- 质量管理和质量保证标准汇编 (一)
- 1997年05月第1版
-
- 可靠性技术标准手册
- 1994年3月第1版
-
- 可靠性技术标准手册
- 1994
-
- 可靠性管理
- 成都电讯工程学院管理工程系
-
- 电子工业:可靠性与质量管理
- 1981
-
- 计算机软件可靠性与质量管理
- 1992 北京:中国经济出版社
-
- 质量与可靠性管理
- 1993 北京:宇航出版社
-
- 可靠性标准及应用
- 1988 北京:国防工业出版社
-
- 土木工程质量管理标准
- 1987 北京:中国铁道出版社
-
- 可靠性技术与管理
- 1989 北京:人民交通出版社
-
- 质量管理与可靠性
- 1995 北京:机械工业出版社
-
- 可靠性工程
- 1990 北京:清华大学出版社
-
- 系统质量与可靠性工程
- 1988 北京:解放军出版社
提示:百度云已更名为百度网盘(百度盘),天翼云盘、微盘下载地址……暂未提供。➥ PDF文字可复制化或转WORD