《HANDBOOK OF PLASTICS》
作者 | HERBERT R。SIMONDS 编者 |
---|---|
出版 | 未查询到或未知 |
参考页数 | 1511 |
出版时间 | 没有确切时间的资料 目录预览 |
ISBN号 | 无 — 求助条款 |
PDF编号 | 811312938(仅供预览,未存储实际文件) |
求助格式 | 扫描PDF(若分多册发行,每次仅能受理1册) |
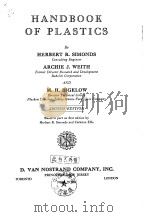
Ⅰ.SURVEY OF THE INDUSTRY1
Ⅱ.PROPERTIES OF PLASTICS51
Ⅲ.COMMERCIAL MATERIALS98
Ⅳ.PRIMARY INGREDIENTS304
Ⅴ.CHARACTERISTICS OF THE VARIOUS PLASTICS378
Ⅵ.TEXTILE FIBERS452
Ⅶ.RUBBERS AND ELASTOMERS500
Ⅷ.NATURAL RESINS525
Ⅸ.FILMS AND SHEETINGS546
Ⅹ.LAMINATES AND PLYWOODS587
Ⅺ.COATINGS648
Ⅻ.ADHESIVES681
ⅩⅢ.MANUFACTURING PROCESSES697
ⅩⅣ.PLANT EQUIPMENT759
ⅩⅤ.PROCESSING AND FABRICATING835
ⅩⅥ.FINISHING OPERATIONS933
ⅩⅦ.MOLDS968
ⅩⅧ.THE CHEMISTRY OF PLASTICS1008
ⅩⅨ.ANALYTICAL METHODS1056
ⅩⅩ.APPLICATIONS1114
ⅩⅪ.DESIGNING MOLDED PARTS1175
ⅩⅫ.OPERATING PRACTICE1198
ⅩⅩⅢ.CHOICE OF PLASTIC1214
ⅩⅩⅣ.COST ACCOUNTING IN THE INDUSTRY1232
ⅩⅩⅤ.PATENTS IN PLASTICS1249
ⅩⅩⅥ.WORLD PLASTICS1292
USEFUL TABLES1319
TRADE-MARKS AND TRADE NAMES1351
GENERAL GLOSSARY1411
CHEMICAL GLOSSARY1437
BIBLIOGRAPHY1455
GENERAL INDEX1465
Ⅰ.SURVEY OF THE INDUSTRY1
What is the Plastics Industry1
What is a Plastic2
History of Plastics3
Progress in Plastics7
Progress in Plastics Processing9
Relation of Rubber and Plastics12
Statistics of the Plastics Industry13
Machin-ery for Plastics17
Allied Chemical and Dye Corporation19
American Cyanamid Company19
American Molding Powder and Chemical Cor-poration20
Bakelite Corporation20
The Barrett Division,Allied Chemical and Dye Corporation20
Carbide and Carbon Chemicals Cor-poration(Plastics Division)21
Casein Company of America21
Catalin Corporation of America21
Celanese Corporation of America22
Celanese Celluloid Corporation23
Chemaco Corporation23
Continental-Diamond Fibre Company23
Dow Chemical Company24
E.I.du Pont de Nemours and Company,Inc.24
Durez PlasticsChemicals,Inc.26
Eastman Kodak Company26
General Electric Company27
Gering Products,Inc.27
B.F.Goodrich Chemical Company28
The Goodyear Tire Rubber Company28
Hercules Powder Company28
Koppers Company,Inc.29
I.F.Laucks,Inc.30
Makalot Corporation30
Manufacturers Chemical Corporation30
Monsanto Chemical Com-pany31
Nixon Nitration Works31
Pittsburgh Plate Glass Company31
Plaskon Division,Llbbey-Owens-Ford Glass Company32
Rohm Haas Company32
Union Carbide and Carbon Corporation33
Westing-house Electric Corporation33
The Future of Plastics34
Technical Employment Possibilities36
Some Typical Laminators39
Molders and Laminators40
Ⅱ.PROPERTIES OF PLASTICS51
Specific Gravity;Tensile Strength;79
Modulus of Elasticity;Compressive Strength;Flexural Strength80
Impact Strength;Hardness,Brinell;Thermal Conductivity81
Specific Heat;Thermal Expansivity;Safe Top Operating Temperature82
Volume Resistivity;Dielectric Strength;Dielectric Constant83
Power Factor84
Moisture Absorption;Refractive Index85
Chemical Resistance of Various Plastics85
Low-Pressure Resins87
Some Properties of Laminac Low Pressure Resins89
Properties of Laminated Materials89
Physical Properties of some Selectron Resins92
Properties of Selectron Laminates95
Ⅲ.COMMERCIAL MATERIALS98
American Cyanamid Company:Products99
American Plastics Corporation: Products106
Athol Manufacturing Company: Products106
Bakelite Corporation:Products107
The Barrett Division,Allied ChemicalDye Corporation:Products115
Burgess Cellulose Company:Products117
Catalin Corporation:Products118
Celanese Corporation of America: Products121
Chemaco Corporation:Products129
Ciba Products Corporation:Products131
Continental-Diamond Fibre Company:Products132
The Dow Chemical Company:Products135
E.I.du Pont de Nemours Company,Inc.:Products154
Durez Plastics Chemicals,Inc.:Products167
Durite Plastics,Inc.:Products173
Fabricon Products,Inc.:Products175
The Firestone Tire Rubber Company:Products183
The Formica Insulation Company:Products187
General Electric Company:Products189
General Mills,Inc.:Products194
B.F.Goodrich Chemical Company:Products195
The Goodyear Tire and Rubber Company,Inc.:Products198
Hercules Powder Company:Products202
Makalot Corporation:Products204
Marathon Corporation:Products207
The Marblette Corporation:Products208
Marbon Corporation:Products209
Marco Chemicals,Inc.:Products210
Minnesota Mining and Manufacturing Company:Products214
Monsanto Chemical Company:Products214
National Vulcanized Fibre Company:Products242
Nixon Nitration Works:Products242
Pennsylvania Coal Products Company:Products245
Pennsylvania Industrial Chemical Corporation:Products247
Pittsburgh Plate Glass Company:Products248
Plaskon Division,Libbey-Owens-Ford Glass Company:Products257
Reilly Tar Chemical Corporation:Products264
The Resinous Products and Chemical Company:Products265
The Richardson Company:Products275
Rohm Haas Company:Products277
Spaulding Fibre Company,Inc.:Products283
Synthane Corporation:Products284
Taylor Fibre Company:Products285
Tennessee East-man Corporation:Products290
The United States Stoneware Company:Products296
Westinghouse Electric Corporation:Products298
Ⅳ.PRIMARY INGREDIENTS304
Fillers304
Catalysts312
Hardeners314
Lubricants315
Solvents and Plasticizers316
Alternate Names for Solvents318
Alternate Names for Plasticizers320
Compatibility Characteristics334
Bibliography-Solvents and Plasticizers352
Preparation of some Raw Materials353
Colorants used in Plastics358
Types of Colorants360
Ⅴ.CHARACTERISTICS OF THE VARIOUS PLASTICS378
Acrylic Resins378
Alkyd Resins381
Allyl Resins383
Benzyl Cellulose383
Bubblfil384
Casein Plastics and Other Proteins384
Cashew Nut Shell Liquid Products386
Cellulose Acetate387
Cellulose Acetate Butyrate389
Cellulose Nitrate390
Chlorinated Rubber392
Cold-Molded Bitumen393
Coumarone-Indene394
Ethyl Cellulose396
Methyl Cellulose399
Furfural399
Karbate401
Lignin Plastics402
Melamine-Formaldehyde404
Phenol Aldehyde Resins405
Phenolic Resins in Coatings411
Resorcinol-Formaldehyde Resins414
Polyoamides(Nylon)415
Polyamide Resins417
Unsaturated Polyester Resins418
Polyethylene418
Polystyrene421
Polydichlorostyrene424
Rosin Derivatives424
Shellac424
The Silicones425
Sulfur-Olefin Plastics427
Tetrafluoroethylene Polymer429
Urea-Formaldehyde Resins430
Vinyl Resins436
Polyvinyl Acetate436
Polyvinylcar-bazole438
Polyvinyl Chloride439
Vinyl Chloride-Acetate Copolymers439
Polyvinyl Acetals(Polyvinyl Aldehyde Reaction Products)442
Polyvinyl Acetal,Polyvinyl Butyral,Polyvinyl Formal443
Vinylidene Chloride444
Vulcanized Fiber444
Wood-Base Plastics445
Vibrins449
Zein Plastics451
Ⅵ.TEXTILE FIBERS452
Multifilaments452
Type A Rayons452
Type B Rayons460
Rayon Staple Fiber465
Effect of Variations in Atmospheric Conditions in the Testing of Rayon467
The Rayon Industry470
Protein Fibers(Type C)475
Nylon(Type D)479
Cellulose Propionate Yarns487
Vinyon(Type E)488
Vinylidene Chloride Polymers(Type E);Polyvinyl Chloride(Type E);Polyvinyl Alcohol(Type E);Polyvinyl Acetals(Type E)490
Glass Fibers(Type F)491
Monofilaments493
Nylon494
Vinylidene Resins496
Resin Coated Yarns498
Ⅶ.RUBBERS AND ELASTOMERS500
Kinds of Synthetic Rubber Classified According to their Chemical Structure500
Raw Materials Needed to Make Principal Synthetic Rubbers515
Ⅷ.NATURAL RESINS525
Accroides529
Amber530
Damar532
East Indies:Batu,Black,and Pale533
Kauri534
Manilas535
Ⅸ.FILMS AND SHEETINGS546
Film Materials546
Methods of Film Preparation548
Properties of Unsupported Films552
Films from Cellulose Acetate557
Rubber Hydrochloride Film564
Film from Polyvinyl Chloride and Vinyl Chloride Copolymers570
Film from Polyethylene573
Plastics Films in the Electrical Industry579
Ⅹ.LAMINATES AND PLYWOODS587
Low-pressure Paper-Base Laminates588
Resin Treatment of Wood598
Post Forming613
High-Pressure Laminates619
Laminated Phenolic Materials622
Practical Methods of Machining Laminates629
Suggestions on Design for the Use of Laminates632
A Few Uses for Laminates in Industries they Serve633
Molded Laminates634
Thermoplastic Laminates635
Flexible Pressure Forming637
Bag Molding Technique642
Fiberglas Laminates645
Core Materials646
Ⅺ.COATINGS648
Dispersion Resins649
Silicones649
Cellulose Nitrate650
Wood-Finishing Lacquers651
Ethyl Cellulose657
Cellulose Acetate658
Mixed Esters659
Urea-Formaldehyde Resins660
Melamine Resins663
Vinyl Compounds654
Acrylic Ester Polymers665
Alkyds666
Modified Alkyd Resins668
Phenolics671
The Natural Resins673
Rubber-Base Coatings674
Organic Coating Testing676
Ⅻ.ADHESIVES681
Chemical Classification of Adhesives681
General Characteristics of Adhesives682
Soluble Blood and Synthetic Resin Adhesives686
Starch and Synthetic Resin Adhesives689
Synthetic Resin and Soybean Flour Adhesives691
Furfural Resin Adhesives for Aircraft Use692
ⅩⅢ.MANUFACTURING PROCESSES697
Flow Sheets Accompanying Articles697
Manufacture of Phenol-Formaldehyde Plastics and Molding Compositions698
Manufacture of Cast Phenolic Resins702
Manufacture of Soybean-Phenolic Molding Powder706
Manufacture of Urea Plastics708
Manufacture of Melamine-Formaldenyde Plastics711
Manufacture of Alkyd Resins713
Manufacture of Vinyl Ester Resins716
Manufacture of Vinyl Chloride-Acetate Copolymer718
Manufacture of Polyvinyl-Aldehyde(Acetate)Plastics720
Manufacture of Vinylidene Chloride Plastics722
Manufacture of Polyvinyl-Alcohol Plastics724
Manufacture of Acrylic Resins725
Manufacture of Polystyrene729
Manufacture of Polyethylene732
Manufacture of Coumarone-Indene Resins732
Manufacture of Cellulose Acetate Plastics736
Manufacture of Cellulose Nitrate Plastics738
Manufacture of Cellulose Ether Plastics741
Manufacture of Lignin Plastics743
Manufacture of Furfural Resins744
Manufacture of Casein Plastics748
Manufacture of Nylon753
Manufacture of Zein Plastics754
Manufacture of Cold-Molded Products756
ⅩⅣ.PLANT EQUIPMENT759
Resin Kettles759
Some General Kettle Considerations762
General Processing Equipment767
Equipment for Molding Plants779
Weighing and Measuring779
Preforming781
Compression Molding Equipment784
Injection Molding Equipment787
Heating Media791
Preforming Equipment796
Commercial Equipment801
Accessory Equipment808
Representative List of Manufacturers822
ⅩⅤ.PROCESSING AND FABRICATING835
Methods of Molding835
Compression Molding835
Injection Molding843
Jet Molding850
Transfer Molding851
Heatronic Molding857
Cold Molding874
Blow Molding875
Plunger Molding882
Radiant Heating883
Induction Heating of Inserts884
Powder Preheating-Continuous Agitation885
Resistance Preheating of Molding Materials887
Laminating887
Extrusion887
Importance of Good Molds898
Operation of Injection Molds901
Practical Use of Compression Molds909
Trimming and Assembling918
Casting Plastics920
Fluid Pressure Molding926
Application of Plastics to Fabrics by Calendering930
ⅩⅥ.FINISHING OPERATIONS933
Finishing Molded Parts933
Machining Plastics947
Grinding,Sanding and Tumbling950
Finishing and Assembling Cast Phenolics952
Metal Coatings on Plastics957
Forming Cellulose Acetate Sheets963
ⅩⅦ.MOLDS968
Design of Molds971
Mold Construction975
Materials of Mold Construction981
Types of Steel Used for Molds996
Hard Chromium Plating997
Stainless Steels for Plastic Molds1005
What Type of Stainless is Most Desirable1006
ⅩⅧ.THE CHEMISTRY OF PLASTICS1008
Raw Materials1008
Coal1011
Petroleum1013
Natural Gas Case1015
Agricultural Material1015
Carbohydrates1015
Methylene;Formaldehyde;Acetaldehyde1016
Furfural;Cellulose1017
Protcins1020
Shellac1022
Lignin1023
Inorganic1024
Monomers and Polymers1027
Condensing Type Polymers1033
Addition Type Polymers1042
Cellulose Plastics1049
ⅩⅨ.ANALYTICAL METHODS1056
Differentiation into Groups1058
FluoreScence Analysis of Plastics1081
Composition1087
Ring and Ball Method1093
Apparatus1093
Preparation of Sample1094
Procedure1094
Viscosity Determination1096
Phenolic Plastics1097
Urea Plastics1098
Alkyd Plastics1100
Polystyrene1102
Polyacrylate Plastics1104
Cellulose Ethers1104
Cellulose Esters1105
ⅩⅩ.APPLICATIONS1114
Abrasives1114
Plastics in Architecture,Building,and Furnishings1115
Prefabricated Housing1117
Plastics in the Arts1119
Plastics and Phonograph Records1123
Plastics in Sculpture1125
Plastics in Handicrafts1125
Plastics in the Automotive Industry1126
Application of Chemigum N Synthetic Rubber1129
Synthetic Resins in Airplane Construction1130
Plastics for Displays1137
Plastics in the Electrical Industry1139
Plastics in Household Appliances and Gadgets1140
Industrial Applications1147
Plastics in Packaging1159
Athletic and Sport Equipment1167
Plastics in Dentistry1167
Plastics in Surgery1174
ⅩⅪ.DESIGNING MOLDED PARTS1175
Correct Detailed Design Reduces Mold Expense1176
Principles of Design1176
Allowances and Tolerances1179
Inserts1179
Lettering and Engraving1186
Assembly Accessories1188
Color and Plastics1189
Design of Inserts for Molded Plastics Parts1191
ⅩⅫ.OPERATING PRACTICE1198
Routine Plant Inspection and Physical Testing of Plastics1198
Production Control1198
Price and Production1202
Workers’ Welfare1207
ⅩⅧ.CHOICE OF PLASTIC1214
Selection Based on Characteristics1218
Stress and Strain1226
Effect of Temperature on Tensile Strength1227
Tensile Properties1229
Flexural Properties1230
Impact Properties1230
Reliability of Data1230
ⅩⅩⅣ.COST ACCOUNTING IN THE INDUSTRY1232
The Balance Sheet;The Operating Statement;The Cost System;Cost Application;Cost Control;Estimating1232
Price Formula1233
Shop Control1233
Office Control;Sales1234
Accounting;Forms1235
The First Year’s Comparative Cost Accounting by One Company1235
Establishing the Basis for Costing1236
Compiling the Standard Costs1243
ⅩⅩⅤ.PATENTS IN PLASTICS1249
Alkyd(Glyptal)Resins1249
Aminoplasts1251
Lignin Plastics1258
Organo-Silicon Resins1259
Phenolic Resins1260
Vinyl,Styrene and Acrylic Resins1269
Miscellaneous Resins1278
ⅩⅩⅥ.WORLD PLASTICS1292
Argentina;Brazil;Chile1292
Colombia;Peru;Uruguay;Venezuela;Australia;Canada;Mexico;Russia1293
Plastics in Germany1294
Polyvinyl Chloride1295
Polyvinylidene Chloride;Polyethylene1296
Polystyrene1297
Polyamides1298
Polyurethanes1299
Polyvinyl Ethers1301
Polyacrylates1302
Polyvinyl Cabarzole;Polyester Elastomers;Polyvinyl Acetate1305
Polyvinyl Alcohol;Polyvinyl Acetals;Polyisobutylene1306
Polyethyleneimine;Phenolic Resins1307
Urea Resins1309
Cellulose Plastics1310
Plastics in England1311
Export Trade1313
1.1General Plastics Statistics16
1.2Production of Five Resins17
1.3Production in the United States,July,1946 and 194718
1.4Technical Personnel and Volume of Production in the Synthetic Resins and and Plastic Industry37
1.5Members of the American Chemical Society Reporting Specialization in Synthetic Resins and Plastics,with Corresponding Percentages of Total for all Fields of Specialization37
1.6Research Laboratories Engaged in work on Synthetic Resins and Plastics38
2.1Properties of Phenol-Formaldehyde,Phenol-Furfural and Silicone Resin Compounds52
2.2Properties of Urea and Melamine Molding Compounds63
2.3Properties of Vinyl Resins and Polystyrenes64
2.4Properties of Methyl Methacrylate68
2.5Properties of Nylon70
2.6Properties of Cellulose Derivative Plastics72
2.7Miscellaneous Compounds74
2.8Properties of Plastics Compared79
Properties of Low-Pressure Binders88
Some Properties of Laminac Low Pressure Resins89
Properties of Laminated Materials89
Physical Properties of some Selectron Resins92
3.1Properties of Injection Grades of Ethocel Plastic136
3.2Properties of Extrusion Grades of Ethocel Plastic137
3.3Properties of LT Ethocel Plastic140
3.4Strength of Tubing141
3.5Silicone and Petroleum Greases151
3.6Specifications for Dow Corning Silicone Greases153
3.7General Properties of Lucite155
3.8Comparison of Specific Gravities of Some Materials158
3.9General Properties of Plastacele158
3.10Cellulose Nitrate Compared with Wood160
3.11General Properties of Pyralin161
3.12General Properties of Polythene163
3.13Typical Properties of Durez General-Purpose,Heat-Resistant and Non-Bleed Materials168
3.14Typical Properties of Durez High-Impact Electrical and Special Materials170
3.15Properties of Durite Molding Materials174
3.16Weight of Phenopreg Grades175
3.17Physical Values of Various Grades of Phenopreg after Lamination176
3.18Bootleg Duck Grades177
3.19Enameling Duck Grades178
3.20Phenopreg Sheeting178
3.21Phenopreg Paper Grades179
3.22Phenopreg Tube Winding Paper Grades179
3.23High-Tensile Plastic Paper,Grade No.34180
3.24Phenopreg Bonding Material180
3.25Phenopreg Specialty Grades181
3.26Properties of Makalot Phenolic Compounds205
3.27Typical Makalot Phenolic Molding Compounds206
3.28Effect of Various Chemicals on Some Resins212
3.29Marco-Board-Properties and Specifications213
3.30Comparative Properties of Monsanto Plastics218
3.31Monsanto Potting Compound,Physical and Electrical Properties228
3.32Resin Resistance to Solvents and Oils232
3.33Physical Properties of Typical Thermosetting Vinyl Butyral Compound241
3.34Average Values of Phenolite Tubing241
3.35Average Values of Phenolite Sheet243
3.36General Properties Chart of Nixon Plastics244
3.37Fabrication Characteristics of Allymer C.R.39252
3.38Physical Properties of Allymer C.R.39,when Polymerized into clear Castings,and of two Typical Laminates252
3.39Effects of Modifying Agents,Added to Allymer C.R.39 before Polymerization upon the Properties of the Polymer253
3.40Properties of Allymer C.R.149254
3.41Fabrication Characteristics of Allymer C.R.149254
3.42Physical Properties of Allymer C.R.149,when Polymerized into clear Castings,and of two Typical Crossed Laminates255
3.43Effects of Modifying Agents,added to Allymer C.R.149 before Polymerization,upon the Properties of the Polymer256
3.44Properties of Allymer 170256
3.45Fabrication Characteristics of Allymer 170257
3.46Physical Properties of Allymer 170 when Polymerized into clear Castings,and of two Typical Crossed Laminates257
3.47Lighting Efficiency of Plaskon258
3.48Plaskon Molding Conditions260
3.49Physical Properties of Plaskon 911-11 Resin Laminates264
3.50Paraplex Characteristics267
3.51Physical Properties of the Uformites269
3.52Physical Properties of Acryloid270
3.53Characteristics of Acryloid Films270
3.54Electrical Resistance of Acryloid Films270
3.55Properties of Plexiglas280
3.56Plexene M Molding Powder282
3.57Taylor Vulcanized Fibre Data286
3.58Dielectric Strength of Sheets289
3.59Summary of Range of Properties-Tenite Ⅰ293
3.60Summary of Range of Properties-Tenite Ⅱ294
3.61Comparison of Physical Properties of Micarta to Various Metals299
3.62Properties of Molded Micarta302
4.1Properties of Some Common Fillers305
4.2Flexural and Impact Strength of Wood-Flour Filled Resins306
4.3Base Materials which may be Used in Plastics308
4.4Additional Materials Used in Plastics311
4.6Some Catalytic Reactions Important to the Plastics Industry,with the Catalysts Usually Employed312
4.7Table of Solvents322
4.8Table of Plasticizers336
4.9Factors Influencing the Selection of Coloring Materials364
4.10Compatibility of Coloring Materials with Various Plastic Binders365
4.11General Properties of Coloring Materials Used in Plastics366
4.12Major Test and Fastness Requirements for Coloring Matters in Plastics367
4.13Plastic Binders as Solid Solvents for Dyes368
4.14Properties Chart of Coloring Materials for Plastics369
4.15Colors for Plastics374
5.1Heating Time and Temperature for Bending Acrylic Rods379
5.2Physical Properties of Karbate401
5.3Designation of Different Types of Karbate401
5.4Phenolic Resins-Laminates Tubes410
5.5Typical Properties of Tetrafluoroethylene Polymer429
5.6Properties of Polectron Polymer438
5.7Properties of Extruded Vinyl Chloride-Acetate441
5.8Properties of Vibrin-103450
6.1Viscose Process454
6.2Ethoxy Content of Ethyl Cellulose464
6.3Physical Properties of Cellulose Ether and Cellulose Ester464
6.4Physical Properties-Representative Textile Type Rayon Yarns466
6.5Physical Properties-High Tenacity Viscose Rayon Yarns467
6.6Types of Rayons Sold in United States470
6.7Rayon Staple Fiber Production in the United States471
6.8Selected Textile Fiber and Yarn Prices472
6.9U.S.Rayon Production and Distribution473
6.10Physical Properties of Protein Fibers479
6.11Diamine-Dicarboxylic Acid Salts480
6.12Physical Properties of Nylon484
6.13Some Important Characteristics of Nylon484
6.14Types of Nylon Yarn485
6.15Physical Properties of Vinyon488
6.16Chemical and Physical Characteristics of Vinyon489
6.17Types and Costs of"Vinyon"Yarn489
6.18Sizes of the Common Monofils495
6.19The More Important Properties of Saran497
6.20Approximate Tensile Strength and Elongation of Certain Textile Fibers499
7.1Physical Properties of Silastic Stocks501
7.2Electrical Properties of Silastic Stocks501
7.3Chemical Resistance of Silastic Stocks for Molding and Extruding ASTM D-543-43502
7.4Physical Properties of Silastic 120 and 125 for Coating and Laminating504
7.5Electrical Properties of Silastic 120 and 125504
7.6Chemical Resistance of Silastic 120 and 125 for Coating and Laminating ASTM D-543-43504
7.7Some Characteristics of Hercules"Ethyl Rubber"Compositions514
7.8Production of Synthetic Rubber515
7.9Chemical Structure of Varieties of Synthetic Rubber and Elastomers517
7.10Properties of Various Substances of Rubbery Characteristic521
8.1Classification of Natural Resins527
8.2Origin and Commercial Packages of Natural Resins528
8.3Properties of Natural Resins537
8.4Compatibility of Natural Resins with Other Resins539
8.5Compatibility of Natural Resins with Nitrocellulose540
8.6Compatibility of Natural Resins with Ethyl Cellulose541
8.7Compatibility of Natural Resins with Waxes542
8.8Compatibility of Natural Resins with Asphalts and Pitches543
8.9Compatibility of Natural Resins with Chlorinated Rubber544
9.1Properties of Regenerated Films555
9.2Gas Permeability of Regenerated Cellulose556
9.3Thickness in Weight of Films559
9.4Transparency of some Films559
9.5Weights for Rubber Hydrochloride Film566
9.6Moisture Vapor Transmission of Representative Types of Pliofilm566
9.7Diffusion Rates of Air,Oxygen and Carbon Dioxide through Pliofilm566
9.8Physical Test Data on Pliofilm566
9.9Properties of Vinyl Film572
9.10Properties of Saran Film-Type M574
9.11Gas Permeability of Polyethylene Film576
9.12Moisture absorption of Cellulose Films580
9.13Permeability Standards(Values of D)581
9.14Dielectric Strength of Some Plastics Films582
9.15Power Factor and Dielectric Constant of some Materials582
10.1Standard Nema Specifications for Resin-Impregnated Paper Laminates for Use in Electrical Insulation589
10.2Physical Characteristics of Type X Insulation and Impregnated Mitscherlich Spruce Sulfite590
10.3Difference in Physical Characteristics of Laminates Molded at 100 and 1000 PSI594
10.3A Characteristics of Typical Low Pressure Laminating Resins594
10.4Variations in Strengths Characteristics of High-Strength Paper Laminates595
10.5Directional Properties of Paper-Base and Glass-Base Laminates596
10.6Comparison of Various Specific Strengths of Laminated Paper-Base Plastic and Aluminum Alloy 24 ST596
10.7Comparison of Tensile Strength of Plywood,Paper-Base Plastic and Aluminum Alloy 24 ST597
10.8Properties of Cross-Banded,Phenolic Resin Laminates with Different Fiber Bases597
10.9Water-Vapor Transfusion through Resin-Bonded Douglas-Fir Plywood under a Steady-State Relative-Humidity Gradient 100 to 30%602
10.10Normal Approximate Strength Properties of Parallel-Laminated Birch Compreg with a Specific Gravity607
10.11Comparison of High Density Laminated Wood609
10.12Effect of Glue Solids on Moisture Content of Plywood612
10.13Physical Properties of Typical Plywood Tubes613
10.14Mechanical Properties of Typical Plywood Tubes613
10.15Standards of Quality for Laminated Sheets624
10.16Standard Thickness Tolerances of Laminated Sheets627
10.17Approximate Weights of Standard 36 In.x 36 In.Laminated Sheets628
10.18Formula for Computing Horsepower of Laminated Gears628
10.19Comparison of Standard Grade C Sheet Stock with Molded-Laminated and Molded-Macerated Grade C629
10.20Effect of Various Types and Proportions of Fabrics in Thermoplastic Laminations635
10.21Typical Resins Used in Low-Pressure Molding641
10.22Mechanical Properties of Cloth,Paper and Fiber Glass Laminates641
10.23Properties of Glass Cloth Laminates645
10.24Physical Properties-Honeycomb Core646
10.25Some Typical Core Materials Suppliers647
11.1Properties of Some Typical Dispersion Resins649
11.2Properties and Uses of Typical Synthetic Coatings667
11.3Benzyl Cellulose Compared with Other Cellulosic Coatings673
11.4Weathering Characteristics of selected materials679
12.1Industrial Adhesives and Applications685
12.2Strip Shear Tests on 1/16 In.3-Ply Vertical Grain Birch695
13.1Furfural Derivatives747
14.1Corrosion in Alkyd Resins Manufacture764
14.2Corrosion Tests in the Manufacture of Representative Phenolic Resins764
14.3Impact Grinder Data770
14.4Grinders and Sifters770
14.5Wide Range of Capacities Available in Banbury Mixers772
14.6Ranges of Capacities-Stokes Rotary Press796
14.7Preforming Presses797
14.8Some Characteristic Compression Molding Presses799
14.9Some Characteristic Injection Molding Presses805
14.10Specifications for Royle Extruding Machines806
14.11Specifications for Lester Injection Molding Machine for Plastics814
14.12Specifications covering 6 oz.Injection Machine815
15.1Loss Factor of Molding Material Preforms864
15.2Effect of Method of Heating on Flow Characteristics of Molding Materials865
15.3Physical and Electrical Properties of High Impact Resistant Phenolic Material Molded by Standard and Electronic Methods865
15.4Properties of Molded Blocks870
15.5Typical Articles Produced by Heatronic Molding871
16.1Saws for Laminated Plastics947
16.2Laminated Phenolic Plate-Punching Properties of Various Grades949
16.3Tests on Unplated and Plated Plastics961
17.1Tests for Impact and Flexural Strength974
17.2Average Physical Properties of Various Steels985
18.1Sources of Representative Plastics1009
18.2Materials Available from Coal Tar1011
18.3Conversion of Alkanes to Alkenes1013
18.4Plastics Derived from Petroleum1014
18.5Representative Types of Reactions Producing Condensation and Addition Polymers1028
18.6Comparison of Molecular Weight Measurements1032
18.7Average Molecular Weight for Various Polymers1033
19.1Elemental Compositions1057
19.2Separation of Group A1061
19.3Properties of Resins in Group A1062
19.4Separation of Group B1063
19.5Properties of the Resins in Group B1064
19.6Separation of Group C1065
19.7Properties of Resins in Group C1065
19.8Separation of Group D1066
19.9Properties of Resins in Group D1066
19.10Separation of Group E1067
19.11Properties of Resins in Group E1068
19.12Separation of Group F1069
19.13Properties of Resins in Group F1070
19.14Separation of Group G1071
19.15Properties of Resins in Group G1072
19.16Separation of Group H1074
19.17Properties of Resins of Group H1075
19.18Phenol Tests1079
19.19Fluorescence of Plastics and Resins in Filtered Ultraviolet Light1082
19.20Color Test1086
19.21Behavior of Plastics on Strong Heating on Sample in Test Tube1108
20.1Plastics in Architecture,Building,and Furnishings1120
20.2Typical Application of Plastics in Aviation1132
20.3Plastics in the Electrical Industry1141
20.4Suggestions for Use of Plastics in Design of Machine Tools1156
20.5Plastics Plywood Applications1158
20.6Plastics in Clothing and Personal Articles1161
20.7Plastics in Photography1165
20.8Plastics in Railroads and Shipping1166
20.9Use of Plastics in Sports,Games and Toys1168
20.10Plastics in Science1172
22.1Price and Production of molds1203
22.2Additional Production Per Single Cavity1206
22.3Cost Study of Automatic Molding1207
22.4Disabling Injuries,1939,Chemical Industry,by Industrial Groups1212
23.1Selection of Materials for some Typical Products1216
23.2Guide to Selection Based on Characteristics of Materials1218
23.3Manufacturing Procedure Compared for Different Materials1224
23.4Chemicals and Reagents Having no Effect on Cellulose Acetate Butyrate1225
23.5Chemicals and Reagents that Cannot be Used with Cellulose Acetate Butyrate1226
23.6Effect of some Chemicals and Reagents on Cellulose Acetate Butyrate1226
Molding Conditions for Phenolics1228
Tensile Strength of Phenolics at Various Temperatures1229
Flexural Strength of Phenolics at Various Temperatures1230
Impact Strength of Phenolics at Various Temperatures1231
26.1Cost of Vinyl Products1295
26.2Cost of Plastics Compared1297
26.3Production and Cost of German Plastics1298
26.4Cost of Certain Vinyl Ethers1301
26.5Production and Cost of Selected Plastics1303
26.6U.S.Exports of Cellulose Plastic Molding Compositions and Powders,January Through May,19461314
Ⅰ.Modulus of Elasticity in Tension of some Materials1319
Ⅱ.Thermal Conductivity of Materials1319
Ⅲ.Densities and Refractive Indices of Synthetic Resins1319
ⅢA.Specific Gravity to Pounds Per Gallon1321
Ⅳ.Densities and Refractive Indices of Natural Resins and their Glycerol Esters1322
Ⅴ.Constants of Oils Used in Paint,Varnish,and Lacquer Industry1322
Ⅵ.Physical and Chemical Properties of the Common Waxes1323
Ⅶ.Specifications for Coke Oven Light Oil Distillates and Other Coal Tar Solvents1324
Ⅷ.Properties of Certain Flammable Materials1326
Ⅸ.Capacities of Hydraulic Rams in Tons1328
Ⅹ.Steam Table1331
Ⅺ.Tap and Drill Sizes1332
Ⅻ.Button Measurements1333
ⅩⅢ.Table of Brinell Hardness Numbers1334
ⅩⅣ.Screen Scale Sieves for Closer Sizing1334
ⅩⅤ.Wire and Sheet Metal Gauges1335
ⅩⅥ.Temperature Conversion Tables1336
ⅩⅦ.Plastics Production Conversion Table1337
ⅩⅧ.Areas,Volumes and Conversion of Fractions into Decimals1338
ⅩⅨ.Weight of 1000 Pieces in Pounds Based on Weight of One Piece in Gram1341
ⅩⅩ.Specific Gravity into Ounces and Grams1342
ⅩⅪ.Hardness of Materials by Moh Scale1343
ⅩⅫ.Weight of Rods of Specific Gravity 1.361343
ⅩⅩⅢ.Number of Feet of Tube of Specific Gravity 1.36 in One Pound1344
ⅩⅩⅣ.Hardness Conversion Tables1345
ⅩⅩⅤ.Conversion of Volumes or Cubic Measure1346
ⅩⅩⅥ.Summary of Inflammability and Explosibility of Powders Used in the Plastics Industry1347
ⅩⅩⅦ.Table Showing Feet Per Pound in Cellulose Nitrate Rods and Tubes1348
3.1Effect of Temperature on Impact Strength of Ethocel Plastics138
3.2Effect of Temperature on Dimensional Change of Injectional Molded LT Ethocel Plastic139
3.3Bursting Strength of Extruded Ethocel Plastic Tubing141
3.4Relative Reactivity Phenol and Resorcinol245
3.5Gel Time of Resin at Various pH Values246
6.1Types of Synthetic Fibers452
6.2Conversion of Wood Pulp and Cotton Linters453
6.3Rayon Viscose Process455
6.4Rayon Viscose455
6.5Rayon Viscose,Ripening456
6.6Regeneration in Rayon Production457
6.7Bucket Rayon Spinning Machine458
6.8Cellulose Acetate Rayon461
6.9Flow of Cellulose Materials through Various Manufacturing Processes to the Finished Articles462
6.10Rayon463
6.11Per cent of Relative Humidity468
6.12Relative Humidity468
6.13Relative Humidity of 1% Viscose Rayon469
6.14Relative Humidity of 0.4% Viscose Rayon469
6.15U.S.Rayon Production475
6.16Flow Chart for Casein Filaments477
6.17Flow Chart for Soybean Filaments478
6.18Flow Diagram for Nylon Filament481
6.19Tenacity of Several Fibers486
6.20Water Absorption of Certain Fibers486
6.21Elastic Recovery of Selected Fibers486
6.22Manufacturing Processes,Glass Fibers492
6.23Plastic Flow vs.Temperature of Several Thermoplastics493
7.1Outline Flow Diagram for Manufacture of Buna-S505
7.2Flow Diagram for Manufacture of Buna-N506
7.3Flow Diagram for Manufacture of Butyl Rubber508
7.4Flow Diagram for Manufacture of Neoprene509
7.5Flow Diagram for the Manufacture of Thiokol"A"510
7.6Manufacturing Flow Diagram for Koroseal511
9.1Section of Hopper Used for Casting Viscose548
9.2Film Forming Machines549
9.3Schematic Diagram of Cellophane Casting Machine554
10.1Assemblies of Low- and High-Density Plywood601
10.2Variable Density Before and After Pressing602
10.3Continuous Lumber Core Edge-Gluer608
10.4Conventional Hot Platen Plywood Press610
10.5Conventional Plywood Press610
10.6Wood Assemblies Heated Between High Frequency Electrodes611
10.7Methods of Applying Electric Heat to Wood Assemblies611
10.8Continuous Veneer Splicer613
10.9Preparation of Strip for Making Tubes614
10.10Rolling Plywood Tubes615
10.11Post Forming616
10.12Types of Post Forming Molds617
10.13Flow Diagram for the Production of High-Pressure Cloth-Phenolic Lami-nated Sheets623
10.14Design of Punched Holes631
10.15Design of Drilled and Broached Recesses632
10.16Design of Threaded Holes632
10.17Use of Fillets632
10.18Flexible Bag Molding with Inflatable Interior Bag637
10.19Methods of Applying Omni-Directional Pressure638
10.20Process of Forming Clips with Tubular Pressure638
10.21Molded or Formed Shapes or Clips639
10.22Tabular Pressure in Assembly-Gluing639
10.23Use of Bag or Flexible Tube for Flat or Arched Laminates640
10.24End View of Autoclave642
10.25Arrangement of Plies at Start of Forming642
10.26Small Bag-Molding Shop Layout644
10.27Impregnated Paper Honeycomb Core Material646
13.1Flow Sheet for Manufacturing of Finished Plastics Parts699
13.2Manufacture of Phenol-Formaldehyde Molding Compositions700
13.3Manufacturing of Thermosetting and Thermoplastic Casting Resins702
13.4Manufacture of Cast Phenolic Resins703
13.5Manufacture of Soybean Phenolic Molding Powder707
13.6Manufacture of Urea Plastics709
13.7Manufacturing of Melamine Formaldehyde Plastics712
13.8Manufacture of Two Polybasic Acids and Two Polyhydric Alcohols,Most Used in the Production of Alkyd Resins714
13.9Manufacture of Alkyd Resins715
13.10Manufacture of Vinyl Ester Resins717
13.11Manufacturing of Vinyl Chloride-Acetate Copolymers719
13.12Manufacture of a Typical Vinyl Aldehyde Resin Plastic721
13.13One Method of Manufacture of Vinylidene Chloride Plastics722
13.14Orientation Process for Vinylidene Chloride723
13.15Dow Method of Manufacturing Vinylidene Chloride724
13.16Manufacture of Polyvinyl Alcohol Plastics725
13.17Manufacture of Acrylic Resins726
13.18Manufacture of Acrylic Molding Powders728
13.19One Method of Manufacture of Polystyrene729
13.20Polystyrene Flow Sheet,Similar to Dow Method731
13.21Manufacture of Polyethylene732
13.22Manufacture of Coumarone-Indene Resin Used as Binder733
13.23Manufacturing of Cellulose Acetate Plastics735
13.24Manufacture of Cellulose Nitrate for Plastics738
13.25Manufacture of Plastics from Cellulose Nitrate739
13.26Manufacture of Ethyl Cellulose Plastics741
13.27Ethyl Cellulose Flow Sheet742
13.28Manufacture of Lignin Plastics743
13.29Manufacture of Furfural745
13.30Manufacture of Casein Plastics by the Dry Process749
13.31Manufacturing of Nylon753
13.32Production of Zein Plastics754
13.33Manufacture of Cold-Molded Bituminous Plastics757
14.1Views of Banbury Mixers771
14.2Cross Section of Molding Powder Dryer778
14.3Diagram of Loading Tray780
14.4Steam Platen Showing Channeling,Space Bars,Plugs and Bolster Plate793
14.5Temperature Control of Platens794
14.6Mold Perspective Showing Water Connections795
14.7Bench Fastened to Press Provides Space for Preforms798
14.8Standard Semi-Automatic Molding Press798
14.9100 to 150-ton Molding Press800
14.10Section and Elevation of an Automatic Injection Press802
14.11Outline Assembly of Injection Molding Machine803
14.12Diagram of Typical Hydraulic Circuit for an Injection Molding Machine804
14.13Diagram of Typical Hydraulic Circuits for Simple Hydraulic Clamp or Press Installation807
14.14One In.Four-Way Hydraulic Control Valve,Lever Operated809
14.15Schematic Flow Diagrams Showing Automatic Volume Control for Vickers Double Pump and Combination Valve Unit810
14.16"Hy-Speed" Plunger Molding Press816
14.17Turbojector817
14.18The H-P-M Hydraulic Operating System818
14.19Pump and Piping in Press Operation819
14.20Closure Presses820
14.21Layout of Small Extrusion Plant820
14.22Equipment for Extruding Tenite Sheeting821
15.1Piping and Valve Arrangement for Up-Stroke Press840
15.2Location of Two-Way Valve on Down-Stroke Press841
15.3Angle Press842
15.4Good and Bad Design of Semi-Positive Mold843
15.5Automatic Press844
15.6Section View Illustrating General Method of Injection Molding845
15.7Jet Molding Nozzle Principle850
15.8Injection Molding Machine.Correct Design852
15.9Injection Molding Machine.Incorrect Design853
15.10One Ram Transfer Mold854
15.11Plunger Transfer Mold855
15.12Side Ram Transfer Mold856
15.13Schematic Transfer Mold856
15.14Good and Bad Design of Electrodes859
15.15Size of Electrodes860
15.16Preheating Time Curves862
15.17Temperature Rise Related to Moisture Content863
15.18Comparison Cup Closing Time for Heatronic and Standard Molding Methods866
15.19Relationship of Specimen Thickness(Small) and Minimum Curing Time867
15.20Operation Sequence Chart868
15.21Long Core Sequence Chart869
15.22Equipment Cost872
15.23Operating Cost873
15.24Design of Molds for Sheet Forming877
15.25Compressible Diaphragm878
15.26Pressure Blowing of Plastic Sheet Stock879
15.27Split Pressure Blow Mold for Blowing Tubes880
15.28Blow Molding on Modified Injection Molding Machine881
15.29A Press with a Two-Cavity Mold882
15.30Radiation Heating of Woodfilled Phenolic Preforms884
15.31Layout of Equipment for Resin Insulating888
15.32Schematic Cross Section Through an Extrusion Machine890
15.33TyPe of Extrusion Machine Used for Extruding Acetate Tubing891
15.34 15.35 15.36 15.37Some Typical Extruded Sections for Use in Connection with Wallboard892
15.38Some Typical Extruded Sections for Use in Connection with Wallboard892
15.39Interlox Tee Section892
15.40Successive Steps in Applying Interlox on Table Edging892
15.41Typical Extruded Plastic Sections Which Are Now Available in Almost Any Thermoplastic Material894
15.42Dryer for Drying Thermoplastics before Extruding895
15.43Extruded Forms for Architectural Uses897
15.44Standard Gate904
15.45Fan Gate905
15.46Ring Gate906
15.47Disk Gate906
15.48Air-Cooling Small Core Pin909
15.49Organ-Stop Mold910
15.50Battery-Seal Mold911
15.51Oil-Cup Mold912
15.52Spectacle-Case Mold913
15.53a,b,c,d,-Operating Diagram for Pencil-Barrel Mold914
15.53Pencil-Barrel Mold915
15.54Cigarette-Holder Mouthpiece Mold916
15.55aBowl-Base Mold917
15.55bInkwell Mold917
15.56Vertical Pressure Diagram;Hemi-Spherical926
15.57Pressure Applied by Canvass Bands926
15.58Pressure Applied by Vacuum Bag927
15.59Pressure Applied by Flexible Tubes927
15.60Flexible Bag Outside Molded Shape928
15.61Flexible Membrane or Bag Surrounds Shape928
15.62Flexible Bag Inside Molded Shape929
15.63Fluid Pressure and Flexible Heating Element929
16.1Shoe Pegs938
16.2Design of Drills for Plastics951
16.3aDesign of Drills for Deep Holes951
16.3bDesign of Drills for Small Holes951
16.4Typical Mountings for Transparent Plastic Sheets966
17.1Positive Mold969
17.2"Landed" Positive Mold969
17.3Simple Flash Mold969
17.4Semi-Positive Mold969
17.5Semi-Positive Type Mold with Horizontal Flash970
17.6Semi-Positive Type Mold with Vertical Flash971
17.7Full Flash Type Mold971
17.8True Semi-Positive Mold Vertical Flash Appears at Cutoff972
17.9Flash Type Mold973
17.10Location of Guide Pins in Semi-Positive Mold973
17.11Positive Type Mold with Stop Blocks and Sprue Grooves974
17.12Proper Method of Steam Plate Heating975
17.13Improper Method of Steam Plate Heating975
17.14Proper Steam Channeling975
17.15Improper Steam Channeling975
17.16Schematic Diagram Showing Hobbing Press with the Blank and Necessary Accessories in Position for Sinking977
17.17Flow of Metal during Hobbing979
17.18Maximum Hardness vs.Carbon Content982
17.19Tensile Strength,Brinell Hardness and Ductility of Hot Rolled Plain Car-bon S.A.E.Steels as Received991
17.20Depth of Case vs.Carburizing Time in Furnace for S.A.E.1020 Steel992
17.21Percent Carbon vs.Depth Beneath Surface for S.A.E.3112 Steel Car-burized for 16 Hr.at 1700° F993
17.22Toughness vs.Drawing Temperature for a 1.05% Carbon Tool Steel994
17.23Mold for Producing Clipper Housing998
17.24Yoke or Mounting Plate for Four-Cavity Top and Bottom Halves of Clipper Housing999
17.25Mold for Producing Clipper Housing1000
17.26Two-Cavity Hand Mold for Producing a Handle1001
17.27Four-Cavity Injection Mold for Producing a Bushing1002
18.1Conversion of Vinyl Acetylene into Chloroprene1012
18.2Formation of Butadiene1014
18.3Furfural1017
18.4Cellulose Sugar1017
18.5Cellulose Nitrate Unit1018
18.6Cellulose Acetate Unit1018
18.7Ethyl Cellulose1019
18.8Benzyl Cellulose Unit1019
18.9Preparation of Cellulose Xanthate and Ethyl Cellulose1020
18.10Suggested Reaction in Production of Casein Plastics1021
18.11Formaldehyde and Casein1022
18.12Shellac1023
18.13Lignin1023
18.14Vinyl Compounds1027
18.15Formation of Orthohydroxybenzyl Alcohol1034
18.16Formation of Phenol Dialcohol1034
18.17Polymerizing Unit1036
18.18Steps in Phenol Formaldehyde Polymer Formation1036
18.19Formation of Monomethylol Urea and Dimethylol Urea1037
18.20Formation of Methylene Urea1038
18.21One Molecular Structure of Ureas1038
18.22Anhydroformaldehydeaniline1039
18.23Anhydroformaldehyde Polymerizing Unit1040
18.24Phthalic Anhydride1040
18.25Alkyd Resin Structure1041
18.26Polyvinyl Chloride1042
18.27Polyvinyl Acetate1042
18.28Copolymer of Vinyl Chloride and Vinyl Acetate1042
18.29Nylon Structure1043
18.30Polyvinyl Alcohol1043
18.31Dehydration of Polyvinyl Alcohol1043
18.32Polyvinylidene Chloride1045
18.33Vinylidene Chloride Polymerized with Vinyl Chloride1045
18.34Polymerized Acrylic and Methacrylic Acids1046
18.35Methyl Methacrylate1046
18.36Ethyl Acrylate1047
18.37Polystyrene1047
18.38Divinyl Benzene1048
18.39Polystyrene1048
18.40Polystyrene End Valences1048
18.41Modified Form1048
18.42Coumarone-Indene1049
18.43Coumarone-Indene Resin1049
18.44Preparation of Polyamides1051
18.45Reaction of a Diamine with Free Hydrogen Atoms1051
18.46The Nylon Reaction1052
18.47Reaction Used by Germans for Polyurethanes1053
18.48Structure of Koresin1053
19.1Viscosity Pipette1096
20.1Methods of Recessing Plywood Backs1118
20.2Plastics Parts on an Automobile1128
20.3Plastics Parts of an Airplane1131
20.4Comparative Brightness:500-Watt,18-In.,Semi-Direct Plastics Diffusers1142
20.5Plastics on an Electric Refrigerator1143
20.6Beading on Rigid Transparent Containers1144
20.7Chemical Cost of Deionizatiou1154
20.8The Dorreo D.I.System1155
21.1Wall Thickness Design1176
21.2Cross-Section Design1177
21.3Correct or Incorrect Wall Design1178
21.4Bottle and Jar Cap Wall Section1178
21.5Correct Sidewall Taper1178
21.6Embedded Metal Inserts1179
21.7Supporting Long Inserts in Mold1180
21.8Extrusion or Transfer Molding Process1180
21.9Sufficient Wall Thickness Around Inserts Prevents Cracking1181
21.10Air Gaps at Point of Flashing or Arcing on Electrical Parts1181
21.11Rathbun Spring Hinge1183
21.12Pin Hinge1183
21.13Piano Hinge1183
21.14Standard Bottle or Jar Cap Thread with Round Profile1183
21.15Correct and Incorrect Design for Threads1184
21.16Design of Tapped Holes1184
21.17Radii or Fillets Overcome Structural Weaknesses in Sharp Corners1185
21.18Design for Hexagonal Handles1185
21.19Bas-Relief Lettering or Engraving1186
21.20Speed-Nut and Speed-Clip Fastenings1188
21.21Inserting Cold-Set Plastics Inlay in Molded Part1188
21.22Primary and Secondary Colors1190
21.23Location and Design of Various Inserts1191
21.24Use of Knurled and Upset Inserts1192
21.25Typical Tapped Inserts1192
21.26Inserts in Through Holes1193
21.27Various Types of Inserts in Electrical Work1193
21.28Design for Threaded Inserts1194
21.29Design of Threaded Parts1194
21.30Design of Recesses1194
21.31Location of Core Pins1195
21.32Design of Hinges1195
21.33Design of Molded Knobs1196
21.34Use of Uniform Sections1196
21.35Good and Bad Design for Lugs1196
21.36Location of Inserts1196
21.37Proper Location of Holes1196
21.38Use of Shrink Fits1197
21.39Design for a Handle Made of Two Molded Halves1197
21.40Use of Beads to Cover Parting Lines1197
21.41Use of Bosses in Design1197
22.1Importance of Saving Seconds in Molding Cycle Time1205
22.2Set-Up Showing Mold for Automatic Production of Threaded Caps1206
22.3Mechanical Type of Brake1210
22.4Outline of Activities for a Typical Safety and Fire Prevention Department1211
24.1Burden Statement1237
24.2Cost Record Sheet1240
24.3Monthly Plastic Cost Record1241
24.4Cost Estimate Sheet for Plastics1242
24.5Plastic Cost Record1244
24.6Comparatiye Profit Loss Statement for Hardware1245
24.7Typical Manufacturing Specifications1248
App.1Conversion Table:Specific Gravity to Grams per Cubic Inch1320
App.2Chart for Determining Weight from Volume1320
Melting and Flash Points for Some Chemicals1327
App.4Hydraulic Pressure Relations1330
Glos.1Compression Molding1416
Glos.2Hob Sinking1422
《HANDBOOK OF PLASTICS》由于是年代较久的资料都绝版了,几乎不可能购买到实物。如果大家为了学习确实需要,可向博主求助其电子版PDF文件。对合法合规的求助,我会当即受理并将下载地址发送给你。
高度相关资料
-
- HANDBOOK OF PLASTICS TEST METHODS
- 1971 PUBLISHED FOR THE PLASTICS INSTITUTE
-
- PLASTICS MATERIALS HANDBOOK SECOND EDITION
- 1964 THE MACHINERY PUBLISHING
-
- HANDBOOK OF REINFORCED PLASTICS OF THE SOCIETY OF THE PLASTICS INDUSTRY
- 1964 REINHOLD PUBLISHING CORPORATION
-
- HANDBOOK OF FIBERGLASS AND ADVANCED PLASTICS COMPOSITES
- 1969 VAN NOSTRAND REINHOLD COMPANY
-
- INTERNATIONAL PLASTICS HANDBOOK SAECHTLING
- 1973 HANSER PUBLISHERS
-
- Plastics Extrusion Technology Handbook
- 1981 INDUSTRIAL PRESS INC
-
- Technician's Handbook of Plastics
- 1981 VAN NOSTRAND REINHOLD COMPANY
-
- Plastics Engineering Handbook fourth edition
- 1976 VAN NOSTRAND REINHOLD COMPANY
提示:百度云已更名为百度网盘(百度盘),天翼云盘、微盘下载地址……暂未提供。➥ PDF文字可复制化或转WORD