《AGGLOMERATION OF PHOSPHATE FINES FOR FURNACE USE》
作者 | 编者 |
---|---|
出版 | WILSON DAM |
参考页数 | 124 |
出版时间 | 1950(求助前请核对) 目录预览 |
ISBN号 | 无 — 求助条款 |
PDF编号 | 812109358(仅供预览,未存储实际文件) |
求助格式 | 扫描PDF(若分多册发行,每次仅能受理1册) |
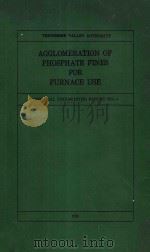
Ⅰ.Introduction1
Ⅱ.Agglomeration by Nodulizing4
Nodulizing Plant Operations4
Nodulizing Tests and Results11
Development of Method for Removal of Kiln Rings14
Refractory Life17
Ⅲ.Agglomeration by Sintering18
Chronological Summary of TVA's Work on Sintering18
Small-Scale Investigations of the Sintering Process20
Equipment and Materials20
Teat Procedure22
Sintering of Unmilled Sand with Sinter Fines and Coke25
Rake Sand25
Bowl Sand26
Bird Sand26
Mixture of Bird and Bowl Sands26
Mixture of Washed Sand and Clayey Binders26
Sintering of Milled Sands,Sinter Fines,and Coke27
Phosphate Sands27
Sand-Matrix Mixtures28
Effects of Bed Depth and Draft29
Development of Pelletizing Equipment30
Effect of Moisture Content of the Feed Mixture31
Use of Sinter Fines and Dry Sand to Control Moisture32
Effects of Type,Proportion,and Particle Size of Fuel33
Application of Results35
Production of Sinter in Large-Scale Plant38
Description of Equipment38
Operation of Equipment42
Production of Sinter from Rake Sand46
Production of Sinter from Bird Sand47
Present Status of Sintering Process49
Ⅳ.Agglomeration by Extrusion50
Ⅴ.Agglomeration by Tumbling54
Equipment and Materials54
Factors Affecting the Formation of Pellets by Tumbling57
Effects of Type of Phosphate and Plasticizing Treatment57
Effect of Moisture Content of Feed61
Effects of Feed Rate to Tumbler and Speed of Tumbler61
Conversion of Tumbled Pellets into Furnace Charge62
Partial Drying of Pellets64
Pelletizing and Partial Drying in Tumbler65
Pelletizing and Partial Drying in Rotary Kiln65
Pelletizing in Tumbler and Partial Drying in Rotary Kiln67
Pelletizing in Tumbler and Partial Drying in Mesh-Belt Drier70
Calcination of Pellets70
Calcination of Tumbled Pellets in Rotary Kiln72
Calcination of Tumbled Pellets in a Shaft Kiln76
Equipment and Procedure76
Pilot-Plant Results80
Evaluation of Shaft-Kiln Calcination83
Ⅵ.Agglomeration by Briquetting84
Pilot-Plant Tests Using a Roll-Type Press84
Equipment,Procedure,and Materials84
Variables Affecting Briquet Production91
Effect of Moisture Content92
Effect of Phosphate Composition92
Effect of Pretreatment94
Effect of Applied Pressure96
Effect of Addition Agents98
Plant Tests Using Raw Briquets99
Use of Briquets in the Calcium Metaphosphate Furnaces99
Use of Briquets in the Fused Tricalcium Phosphate Furnace99
Production of Calcined Briquets101
Calcination in a Rotary Kiln101
Calcination in a Shaft Kiln102
Evaluation of Briquetting Process103
Ⅶ.Choice of Agglomeration Process105
Comparative Studies in TVA Furnaces105
Electric Reduction Furnace105
Fused Tricalcium Phosphate Furnace107
Calcium Metaphosphate Furnace108
Comparative Costs of Agglomerated Products108
Nodulizing Plant109
Sintering Plant109
Calcined Pellet Plant(Rotary Kiln)111
Calcined Pellet Plant(Shaft Kiln)111
Raw Briquet Plant112
Calcined Briquet Plant(Rotary Kiln)113
Plant Investment Costs and Production Capacities114
Process Requirements114
Physical Properties of the Agglomerates115
Comparative Ease or Difficulty of Production116
Storage of Agglomerates118
Choice of Processes119
Ⅷ.References121
APPENDIXES122
A.Product Comparison Procedures122
B.Description of Mixers Used for Preliminary Treatment of Raw Sand124
TABLES12
Ⅰ.Nodule Production Data12
Ⅱ.Composition and Screen Analysis of Nodules12
Ⅲ.Effect of Particle Size of Sand on Nodulizing Results13
Ⅳ.Boring Bar Operating Data17
Ⅴ.Chemical Composition of Phosphatic Materials Used in Small-Scale Sintering Tests22
Ⅵ.Rate of Furnaceable Sinter Production from Unmilled Raw Phosphates25
Ⅶ.Effect of Various Charge-Preparation Treatments on Production Rate of Furnaceable Sinter from Phosphate Sands28
Ⅷ.Effect of Milling on Rate of Furnaceable Sinter Production29
Ⅸ.Effect of Moisture Content of Feed Mixture on Rate of Furnace-able Sinter Production31
Ⅹ.Effect of Amount and Particle Size of Sinter Fines Recycled on Sinter Production Rate32
Ⅺ.Effect of Type of Dry Phosphate Used for Moisture Control on Production Rate33
Ⅻ.Effect of Proportion of Coal and Coke on Rate of Furnaceable Sinter Production33
ⅩⅢ.Sintering of Rake Sand in Plant Machine46
ⅩⅣ.Sintering of Bird Sand in Plant Machine47
ⅩⅤ.Average Chemical and Screen Analyses of Bird Sand Sinter49
ⅩⅥ.Chemical and Screen Analyses of Phosphatic Materials Used in Studies of Agglomeration by Tumbling56
ⅩⅦ.Effects of Type of Sand,Matrix Content,and Plasticizing Treat-ment on Production of Pellets by Tumbling59
ⅩⅧ.Effect of Wet-Pan Treatment on Particle Size of Phosphate Sand61
ⅩⅨ.Effect of Matrix Content on Characteristics of Pellets Produced and Partially Dried in Rotary Kiln66
ⅩⅩ.Results of Partial Drying of Pellets in Pilot-Plant Rotary Kiln67
ⅩⅪ.Effect of Feed Mixture,Plasticizing Treatment,and Method of Tumbling on Production of Partially Dried Pellets in Rotary Kiln69
ⅩⅫ.Effect of Size of Calcined Pellets on Their Strength71
ⅩⅩⅢ.Summary of Test Data on Pilot-Plant Pelletization and Rotary Kiln Calcination73
ⅩⅩⅣ.Size of Plus 6-Mesh Calcined Pellets Produced from Various Phosphatic Materials76
ⅩⅩⅤ.Operating Characteristics of Shaft Kiln at Various Production Rates80
ⅩⅩⅥ.Summary of Shaft Kiln Calcination of Pellets of Various Com-positions82
ⅩⅩⅦ.Chemical and Screen Analyses of Phosphatic Materials Used in Briquetting Studies91
ⅩⅩⅧ.Effects of Wet-Pan Treatment and Type of Matrix Used as Binder on Strength of Briquets Produced from Sand-Matrix Mixtures93
ⅩⅩⅨ.Effects of Addition of Tailing and Wet-Pan Treatment on Strength of Briquets Produced from Phosphate Sand94
ⅩⅩⅩ.Effect of Wet-Pan Treatment on Strength of Briquets Produced from Mixed Sand94
ⅩⅩⅪ.Comparison of Size Stability of Briquets Produced from Mixtures Processed in Edge Runner and Wet Pan95
ⅩⅩⅫ.Effect of Length of Edge Runner Treatment and Briquetting Pressure on Strength of Briquets97
ⅩⅩⅩⅢ.Data on Calcination of Briquets in a Rotary Kiln102
ⅩⅩⅩⅣ.Agglomeration Process Requirements115
ⅩⅩⅩⅤ.Physical Tests of Various Agglomerates116
ⅩⅩⅩⅥ.Production Considerations of Agglomeration Processes117
ⅩⅩⅩⅦ.Effect of Immersion in Water for 1 Hour on the Strength of Fired Agglomerates119
FIGURES5
1.Flow Diagram of Phosphate Nodulizing Process5
2.Layout of Nodulizing Plant6
3.Plant Nodulizing Kilns7
4.CO-Coal Burner10
5.Detail of Boring Bar for Removal of Kiln Rings16
6.Experimental Sintering Unit21
7.Typical Sintering Test Data24
8.Effects of Bed Depth and Draft on Rate of Furnaceable Sinter Production29
9.Effect of Fuel Particle Size on Rate of Sinter Production from Bird Sand35
10.Flow Diagram of Phosphate Sintering Process36
11.Layout of Sintering Plant37
12.General Arrangement of Feed End of Sintering Machine38
13.Equipment for Preparation of Sinter Feed39
14.Sintering Machine;View from Feed End41
15.Slotted-Type Sinter-Machine Grate46
16.Bird Sand Sinter;(a)View Showing Porous Structure,(b)View Showing Structure on Bottom of Sinter Bed48
17.Flow Diagram for Agglomeration by Tumbling54
18.Effect of Wet-Pan Treatment Time on Pellet Formation58
19.Effect of Proportion of Matrix in Feed on Pellet Formation59
20.Effect of Type of Wet Pan Used on Pellet Formation60
21.Effect of Moisture Content of Feed on Pellet Formation62
22.Effect of Feed Rate to Tumbler on Pellet Formation63
23.Effect of Moisture Content of Partially Dried Pellets on Resistance to Shattering and Abrasion64
24.Effect of Calcination Temperature and Tim on Strength of Pellets71
25.Calcined Pellets Discharging from Pilot-Plant Rotary Kiln77
26.Detail of Shaft Kiln Construction78
27.Flow of Materials and Gases Through Shaft Kiln Pilot Plant79
28.Methods of Feed Distribution for Shaft Kiln80
29.Experimental Briquetting Equipment85
30.Experimental Briquetting Machine87
31.Modified Wet Pan88
32.Modified Patterson Mixer89
33.Effect of Pressure and of Matrix on Strength of Briquets Made from Bird Sand—Matrix Mixtures97
34.Flow Diagram of Nodulizing Process110
35.Flow Diagram of Sintering Process110
36.Flow Diagram of Tumbling Process(Calcination in Rotary Kiln)111
37.Flow Diagram of Tumbling Process(Calcination in Shaft Kiln)112
38.Flow Diagram of Briquetting Process(Raw Product)113
39.Flow Diagram of Briquetting Process(Calcination in Rotary Kiln)114
1950《AGGLOMERATION OF PHOSPHATE FINES FOR FURNACE USE》由于是年代较久的资料都绝版了,几乎不可能购买到实物。如果大家为了学习确实需要,可向博主求助其电子版PDF文件(由 1950 WILSON DAM 出版的版本) 。对合法合规的求助,我会当即受理并将下载地址发送给你。
高度相关资料
-
- PHOSPHATE MINERALS
- 1984
-
- MIGRATIONS OF FINES IN POROUS MEDIA
- 1998 KLUWER ACADEMIC PUBLISHERS
-
- USE OF SHOTCRETE FOR UNDERGROUND STRUCTURAL SUPPORT
- 1973 AMERICAN SOCIETY OF CIVIL ENGINEERS
-
- PHOSPHATE DEPOSITS OF THE WORLD VOLUME 2
- 1989 GAMBRIDGE UNIVERSITY PRESS
-
- REGULATION OF PHOSPHATE AND MINERAL METABOLISM
- 1981 PLENUM PRESS
-
- APPROPRIATE USE OF FLUORIDES FOR HUMAN HEALTH
- 1986 WORLD HEALTH ORGANIZATION GENEVA
-
- a manual of palaeontology for the use of students
- 1879 William blackwood and sons edinburgh and london
-
- FINES IN SENTENCING:A STUDY OF THE USE OF THE FINE AS A CRIMINAL SANCTION
- 1984 U.S.DEPARTMENT OF JUSTICE
-
- Managing Microcomputers in Large Organizations
- 1985 NATIONAL ACADEMY PRESS
-
- Size Enlargement by Agglomeration
- 1991 JOHN WILEY & SONS
提示:百度云已更名为百度网盘(百度盘),天翼云盘、微盘下载地址……暂未提供。➥ PDF文字可复制化或转WORD