《MARINE GEARS》
作者 | 编者 |
---|---|
出版 | 未查询到或未知 |
参考页数 | 439 |
出版时间 | 没有确切时间的资料 目录预览 |
ISBN号 | 无 — 求助条款 |
PDF编号 | 811385028(仅供预览,未存储实际文件) |
求助格式 | 扫描PDF(若分多册发行,每次仅能受理1册) |
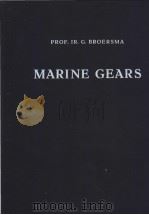
INTRODUCTION13
Chapter Ⅰ:DESIGN A. DESCRIPTIONS19
1Introduction19
2 Actual designs21
3 A.E.G.marine gears24
4 Ansaldo marine gears24
5 British Thomson-Houston marine gears31
6 Wm.Denny & Bros.,Ltd.marine gears33
7 Howaldt-werke marine gears35
8 De Laval Marine Gears37
9 M.A.A.G.marine gears39
10 Parsons marine gears46
11 De Schelde marine gears46
12 Westinghouse Electric Corp.marine gears46
13 (Zrodowski’s) General Electric marine gears46
References49
Chapter Ⅱ:DESIGN CLASSIFICATION RULES50
A.COMPARISON OF SOME PRIMARY DESIGN RULES FOR MARINE GEARS50
14Introduction50
15 Germanischer Lloyd50
16 Lloyd’s Register of Shipping52
17 Bureau V?ritas54
18 Zrodowski’s unit load57
19 Blok’s permissible flash temperature59
20 Bending stresses59
21 Application to and further investigations of specific designs60
22 Double helical,hobbed design60
23 Hardened and ground gear64
References65
B.ADDITIONAL CONSIDERATIONS WITH RESPECT TO PRIMARY DESIGN RULES66
24Pinion deformation66
25 Pinion deformation with regard to bearing clearance70
26 Maximum tooth opening with regard to oil-film thickness in meshing zone71
27 Pinion deformation with regard to local tooth overloading73
28 Natural (or free) torsional vibrations of pinions73
References74
C.ACTUAL RULES OF THE VARIOUS SOCIETIES74
29American Bureau of Shipping74
30 Bureau Véritas74
31 Germanischer Lloyd83
32 Lloyd’s Register of Shipping93
Appendix99
Chapter Ⅲ:DESIGN-CALCULATIONS101
33Introduction101
A.DEFORMATIONS AND STRESS SYSTEMS IN WHEEL TYRES AND WHEEL RIMS101
34Introduction101
35 Deformations and stresses in the wheel tyre and wheel rim of a wheel with shrunk-on wheel tyre - same modulus of elasticity throughout the wheel101
36 First primary stress system103
37 Second primary stress system103
38 Transitional stress systems103
39 Division made in the investigation of tran-sitional stresses105
40 Transitional stress systems for a design consisting of two infinitely (very) long wheel tyres and wheel rims on either side of a wheel center disc105
41 Investigation into the nature of the con-tact between wheel tyre and wheel rim109
42 Transitional stress systems for a structure with infinitely (very) long wheel tyre and wheel rim on one side of the wheel center disc only111
43 Verifying the moment of wheel center disc to wheel rim113
44 Stability of wheel center disc and wheel rim114
45 Angular rotation in the K1 system; tran-sition moment to wheel center disc114
46 Investigation into the behaviour of the wheel tyre and the wheel rim in the K1-and K2-systems115
47 Transition stress systems in the case of a short wheel tyre and wheel rim on one side of the wheel center disc (with finite overhang)and infinitely (very long) ones on the other side116
48 Transition stress systems for a design with- out overhang or with a short overhang on one side of the wheel center disc, and with a finite (short) wheel tyre and wheel rim on the other side respectively118
49 Summary120
50 Deformations and stress systems in the wheel tyre and wheel rim of a wheel with shrunk-on wheel tyre,when the moduli of elasticity of wheel tyre and wheel rim are essentially different121
51 Secondary stress systems121
52 Summary123
B.POSSIBLE LOADS ON A SPLIT MAIN WHEEL OF A MARINE GEAR123
C.WHEEL DESIGN123
53General discussion123
54 Some actual designs125
References129
D.ANALYSIS OF THE DESIGN OF CARBURIZED, HARDENED AND GROUND PINIONS IN RELATION TO THE HEAT TREATMENT129
55Introduction129
56 Form factor of pinions129
57 Experiments with ECN 35130
58 Elastic tooth stresses and K-factor133
59 Testing of material134
References135
Appendix135
60 Hardenability tests Taken Up in Soviet Paper135
E.TOOTH STRESS CALCULATIONS135
61Introduction135
62 Calculation of nominal bending fatigue stresses in gear teeth136
63 W. John Davies’ fatigue formulae for gears138
64 Jacobson’s photo-elastic research on spur gears139
65 Bending fatigue stress calculations ac-cording to A.V.G.R.A139
66 Braley and Berg’s (US Navy) stress para-meters compilations141
67 Zrodowski’s Unit Load143
References144
F.DYNAMIC LOADS IN MARINE GEARS144
68Introduction144
69 British Thomson Houston investigations on dynamic loads145
70 Dynamic loads on spur gears147
71 Dynamic loads in single, or double, helical marine gears of appreciable helix angle148
References152
G.TEMPERATURE LOADS IN MARI-NE GEARS153
72Introduction153
73 Wydler’s non-dimensional determination of Hertz stress, sliding load and scoring factor154
74 Blok’s flash temperature criterion158
75 Blok’s flash temperature criterion for single or double helical marine gears with ap-preciable helix angle160
76 Applicability of the flash temperature for-mula to full hydrodynamic conditions162
77 Further discussion of flash temperature cri-terion for single or double helical marine gears of appreciable helix angle164
78 Rolling and sliding velocities in gear tooth action167
79 W.John Davies’scuffing criterion169
80 Effect on tooth contact of differential heating between pinion and wheel169
References171
H.WEIGHT OF MARINE GEARS171
81Introduction171
82 Deriving parameters as bases of discussion for marine gear weight173
83 Bending stress-torque-modulus parameter175
84 Other stress parameters175
85 Machining costs176
86 Casing design177
References177
Chapter Ⅳ:COUPLINGS178
87Introduction178
A.FINE TOOTHED COUPLINGS178
88Introduction178
Reference180
B.DESIGN CALCULATION OF A FLEXIBLE COUPLING180
89Introduction180
90 Flexible coupling180
91 Elastic stresses181
92 Light loads181
93 Possible vibrations of the flexible coupling183
94 Normal loads183
95 Loads with racing coupling185
96 Thomassen’s type of coupling185
97 Flexible coupling between propeller and reduction gearing186
C.MALMEDY-BIBBY COUPLINGS187
98Flexible coupling of the Malmédy-Bibby type187
Reference188
D.FALK-BIBBY COUPLINGS188
99Flexible coupling of the Falk,,steelflex” type188
E.RENK COUPLINGS194
100Resilient bush couplings194
Reference195
F.REVERSIBLE FLUID COUPLING FOR GAS-TURBINE-DRIVEN MA-RINE PROPULSION UNIT,IN-CORPORATED IN MARINE GEAR196
FⅠ.Part played by the coupling as a unit of the main propulsion installation196
101Introduction196
102 Parnetrada’s hydraulic reversible coupling196
103 Reversing system with a fluid coupling(and friction coupling for cruising)198
104 Heat to be removed in coupling oil199
105 Losses sustained in manoeuvring with single fluid coupling with intermediate blades199
106 Gas coupling199
107 Dynamic phenomena200
108 Torsional vibrations of the first-reduction pinion200
109 Quill shafts201
110 Torsional vibrations of the system gas tur-bine-reduction gear-propeller, with or without turbine201
111 Hardened and ground gears201
112 Hobbed gears201
113 Retardations (and accelerations) during manoeuvring202
114 Dynamic phenomena due to pitch errors204
References204
FⅡ.Dimensioning, damping, control205
115Introduction205
116 Dimensional analysis of a fluid coupling205
117 Transmission efficiency as a function of the weight of the fluid206
118 Investigation into the regulation of the quantity206
119 Oil drain from the coupling208
120 Restricting manoeuvring time208
121 Hydrodynamic accelerations and retar-dations in the coupling209
122 Regulation with baffles209
References209
G.BARCLAY-CURLE HYDRAULIC COUPLINGS210
123Barclay-Curle hydraulic couplings210
Reference210
H.VULKAN COMPRESSED AIR COUPLINGS211
124Vulkan compressed air coupling211
I.TORSIONAL FREQUENCIES IN SINGLE GAS-TURBINE-DRIVEN, LOCKED TRAIN MARINE GEAR-MARINE PROPELLER, PROPULSION UNIT213
125Introduction213
126 Main part?culars213
127 Distribution of mass moments of inertia214
128 Reduced shaft lengths214
129 Mass moments of inertia,resp.shaft lengths reduced on propeltershaft214
130 System reduced on propeller speed214
131 Critical frequency of the first order214
132 Critical frequency of the second order215
133 Critical frequency of the third order216
134 Critical frequencies of the first order for different turbine rotor mass moments of inertia216
135 Hardened and ground gear216
References216
J.TORSIONAL FREQUENCY CALCU-LATION OF AN ACTUAL DESIGN216
136Torsional frequency calculation of R & W.Hawthorn Leslie & Co.,Ltd.’s 7.500/8,250 hp at 100/103 r.p.m. design216
Appendix218
Chapter Ⅴ: BEARINGS219
A.BALL AND ROLLER BEARINGS219
137Introduction219
138 Ball and roller bearings220
B.SLEEVE BEARINGS222
139Description222
140 Design calculation223
141 Oil whirl in bearings229
C.THRUST BEARINGS231
142Thrust bearings231
D.FLEXIBLE COUPLINGS231
143Lubrication of flexible couplings231
E.OIL FILM THICKNESS IN SPUR GEAR TEETH232
144Oil film thickness in the contact area of loaded and running straight spur gear teeth232
F.LUBRICATING OIL234
145Lubricating oil for turbine marine propul-sion units234
146 Extreme pressure lubricants for marine gears236
147 Gas-lubricated bearings241
AppendixⅠ242
AppendixⅡ243
References247
Chapter Ⅵ: MATERIALS248
148Introduction248
A.MATERIAL SPECIFICATIONS248
149Material specifications248
B.MATERIAL FAILURES250
150Material failures250
151 New reagent for microscopic strain analysis in steel254
C.SPHERICAL INCLUSIONS IN STEEL255
152The identification of microscopic spherical inclusions in electric-furnace steel255
153 Conclusion257
D.STRESS SYSTEMS CAUSED THROUGH DIFFUSION IN MATERIALS257
154Summary257
155 Diffusion257
156 Crystalline boundary diffusion258
157 Spherical diffusion258
158 Stress system259
159 Differential equation for the geometricai displacerhent parameter259
160 Study of stresses260
161 Rupture conditions-critical hole radius260
162 Time elapsed at rupture - characteristic time261
163 Fatigue stresses262
164 Actual failures263
165 Rupture not adjacent to the load263
166 Conclusions263
Appendix263
167 Dislocations263
168 Crystal forming during casting264
References264
Chapter Ⅶ:MANUFACTURE265
169Introduction265
A.GENERAL DESCRIPTIONS OF REDUCTION GEAR FACTORIES265
170Stabilimente Meccanico Ansaldo, Genoa265
171 Royal Shipbuilding and Engineering Co.De Schelde,Flushing266
172 Schiess AG,Duesseldorf271
References275
B.TOOTH GENERATING MACHINES275
173Introduction275
174 Development of hobbing machines281
175 Developing, and measuring, accuracy of bobbing machines and gears286
176 The application of hydrostatic high pre-cision bearings to gear bobbing machines,resp.marine reduction gears293
177 Horizontal hobbing297
178 Hobbing by a diagonal generating process299
179 Gear cutting and gear grinding machines299
References301
C.MACHINING PROCESSES301
180Introduction301
181 Hobbing303
182 ,,R?umwalzfr?ser”;hobsforroughhobbing309
183 Hob tooth profiles315
184 Hobbing energy317
185 New developments in hobbing317
186 Post-hobbing processes321
187 Shaping and grinding323
188 Machining operations, not connected with gear generation324
189 Assembly325
References325
D.HEAT TREATMENT325
190Introduction325
191 De Schelde gas carburizing and hardening plant326
192 AVGRA gas carburizing and hardening plant328
193 Induction hardening331
194 Case thickness and hardness gradients331
References332
E.MEASUREMENTS332
195Introduction332
196 Roughness measurements on marine gear teeth335
197 Tooth surface roughness, measured on large gear wheels335
198Comparison of the Talysurf apparatus with the interference microscope for the mea-surement of surface roughness339
Summary343
199 Other roughness records of hobbed (and shaved) gear teeth343
200 Gear tooth undulations343
201 Checking the heat treatment of hardened and ground gears352
202 Checking macroscopic tooth geometry353
203 Dynamic loads, and pitch errors357
204 Checking geometry of the gearing359
205 The alignment of gear cases in manufacture and on board360
References361
Chapter Ⅷ:RESEARCH AND TES-TING OF MARINE GEARS362
A.STATISTICAL ANALYSIS362
206Introduction362
207 Statistical analysis of marine gear failures362
208 Pitting363
209 Scuffing of teeth373
210 Tooth fracture375
211 Wheel failures375
B.RESEARCH ON ULTIMATE LOADS378
212Introduction378
213 Measurement of the machining stresses in gear teeth378
214 Gear and casing deformation under load379
215 Actual tests of gears and casing under load381
216 Wheel deformation383
217 Possible surface and bending fatigue stresses383
References389
C.VIBRATION AND NOISE RESEARCH390
218Vibration and sound research in relation to the cutting machine390
Reference395
D.CRITICAL TORSIONAL SPEEDS OF PINIONS396
219Introduction396
220 Natural torsional vibrations of a cylindrical bar,as derived by the “eigenvalues” method396
221 Critical torsional speeds of pinions in ma-rine gears400
Reference401
E.VIBRATIONS OF NESTED TYPES OF GEARS401
222Introduction401
223 Propeller torque401
224 Differences in magnitude and character of cyclic pitch error on both helices of wheel, resp. pinion403
225 Displacement of the intermeshing teeth on main wheel due to elastic behaviour of parts of the gear403
226 Natural torsional vibrations of wheel helices405
227 Forced torsional vibrations of wheel helices405
228 Absorbing pitch errors on the meshing teeth only405
229 Natural and forced bending vibrations in main wheel406
230 Integral first reduction design406
231 Summary406
References406
F.SOUND PRODUCTION AND VI-BRATIONS IN MARINE GEARS-ANALYSIS OF PROPULSION SYS-TEMS406
232Sound production and vibrations in marine gears, analysis of propulsion systems406
References412
G.SHOP AND SHIP TRIALS412
233Introduction412
234 Problems of running-in of marine gears418
235 Shop and ship trials on naval gears426
References427
H.PRESERVATION OF MARINE GEARS428
Appendix Ⅰ430
236Heat and mass transfer on the surfaces of cold liquids430
Reference431
Appendix Ⅱ431
237The alignment of gear cases in manufac-ture and on board431
Concluding appendix433
References439
《MARINE GEARS》由于是年代较久的资料都绝版了,几乎不可能购买到实物。如果大家为了学习确实需要,可向博主求助其电子版PDF文件。对合法合规的求助,我会当即受理并将下载地址发送给你。
高度相关资料
-
- MARINE GRAVITY
- 1978 ELSEVIER SCIENTIFIC PUBLISHING COMPANY
-
- Shifting gears : thriving in the new economy
- 1992 HarperCollins
-
- DESIGN OF GEARS
- 1967 TECHNICAL PUBLICATIONS
-
- ENCYCLOPEDIC DICTIONARY OF GEARS AND GEARING
- 1995 MCGRAW-HILL
-
- MARINE POLLUTION
- 1976 ACADEMIC PRESS INC.(LONDON)LTD
-
- MARINE INSURANCE
- 1922 D. APPLETON AND COMPANY
-
- MARINE GEOLOGY
- 1982 PRENTICE-HALL
提示:百度云已更名为百度网盘(百度盘),天翼云盘、微盘下载地址……暂未提供。➥ PDF文字可复制化或转WORD