《材料表面技术及其应用手册》求取 ⇩
作者 | 钱苗根主编 编者 |
---|---|
出版 | 北京:机械工业出版社 |
参考页数 | 977 ✅ 真实服务 非骗流量 ❤️ |
出版时间 | 1998(求助前请核对) 目录预览 |
ISBN号 | 711106478X — 违规投诉 / 求助条款 |
PDF编号 | 87394298(学习资料 勿作它用) |
求助格式 | 扫描PDF(若分多册发行,每次仅能受理1册) |
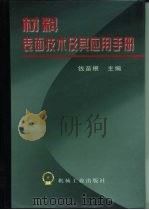
1 固体材料及其表面1
1.1 固体材料1
1.2 固体材料的表面1
第1章 概论1
1.3 表面分析5
1.4 表面科学10
2 表面技术及检测11
2.1 表面技术11
第1篇 腐蚀与防护15
2.2 表面检测17
3 表面技术的应用22
3.1 表面技术应用的广泛性和重要性22
3.2 表面技术的应用概况23
参考文献29
第2章 金属腐蚀原理与腐蚀形态31
1 腐蚀电池31
1.1 异金属电池31
1.2 浓差电池33
2 影响腐蚀速度的因素34
2.1 腐蚀速度的表示方法34
2.2 冶金因素的影响34
2.3 环境因素的影响35
3.1 均匀腐蚀及防护36
3 腐蚀的主要形态及金属的防护36
2.4 力学因素的影响36
3.2 点蚀及防护37
3.3 缝隙腐蚀及防护39
3.4 晶间腐蚀及控制40
3.5 应力腐蚀开裂及控制42
3.6 腐蚀疲劳及防止44
3.7 磨损腐蚀及防止46
参考文献47
1.1 缓蚀剂的定义、发展历史与特点48
1.3 缓蚀剂的作用特征及其分类48
1.2 缓蚀效率48
1 缓蚀剂保护原理48
第3章 缓蚀剂保护48
2 水溶性缓蚀剂及防锈水49
2.1 国内外常用的水溶性缓蚀剂49
2.2 防锈水50
3 油溶性缓蚀剂及防锈油脂51
3.1 油溶性缓蚀剂分类52
3.2 常用的油溶性缓蚀剂53
3.3 防锈油脂54
4 工业冷却水系统缓蚀剂60
4.1 工业冷却水系统与冷却水缓蚀剂60
4.2 工业冷却水系统缓蚀剂简介61
5.1 酸洗缓蚀剂62
5 酸洗与酸化缓蚀剂62
5.2 石油油(气)井酸化缓蚀剂63
参考文献65
第4章 电化学保护65
1 电化学保护原理65
1.1 阴极保护原理65
1.2 阳极保护原理67
2 阴极保护技术与应用69
2.1 牺牲阳极阴极保护69
2.2 外加电流阴极保护78
2.3 阴极保护系统的测量与监控84
2.4 阴极保护的应用85
3.2 阳极保护系统的设计、安装、操作及维护89
3 阳极保护技术与应用89
3.1 阳极保护系统89
3.3 阳极保护的应用90
第2篇 金属的清洗92
第5章 金属的脱脂和清洗92
1 金属表面油污的种类92
2 金属的溶剂清洗93
2.1 溶剂冷清洗93
2.2 溶剂的蒸气清洗94
参考文献95
3 乳化液清洗96
2.3 溶剂的回收96
2.4 溶剂清洗的安全操作96
3.1 乳化清洗液的组成和分类97
3.2 乳化清洗的应用97
3.3 乳化清洗工艺97
3.4 乳化清洗的安全操作98
4 碱清洗98
4.1 碱清洗的机理98
4.2 碱清洗液的组成98
4.3 碱清洗的操作方法99
4.4 碱清洗的工艺条件99
5.1 电解清洗的机理100
5 电解清洗100
5.2 电解清洗剂的组成101
5.3 清洁程度的测定101
5.4 电解清洗的安全操作102
参考文献102
第6章 金属的除锈和酸洗103
1 喷射磨料除锈103
1.1 喷射磨料除锈工艺103
1.2 钢材表面除锈等级104
2 酸洗104
2.1 钢铁材料的酸洗104
6 热喷涂涂层后处理和涂层性能的检验113
2.2 有色金属的酸洗115
参考文献118
第3篇 电镀和化学镀119
1 镀铜119
1.1 用途、分类及不同类型镀铜溶液的比较119
第7章 普通电镀119
1.2 氰化镀铜120
1.3 酸性镀铜121
1.4 焦磷酸盐镀铜123
2 镀镍125
2.1 用途、分类及不同类型镀镍溶液的比较125
2.2 防护装饰性镀镍126
2.3 功能性镀镍128
2.4 镀镍的质量控制129
3.1 用途、分类及不同类型镀铬溶液的比较131
3 镀铬131
3.2 六价铬镀铬132
3.3 六价铬镀液的维护和工艺上的注意点135
3.4 特殊的镀铬工艺137
4 镀锌139
4.1 用途、分类及不同类型镀锌工艺的比较139
4.2 各类镀锌工艺139
4.3 各类镀锌溶液中杂质的影响与去除方法142
4.4 镀锌层的钝化144
5.2 各类镀镉工艺144
5 镀镉144
5.1 镉镀层的性能及用途144
6.2 硫酸盐镀锡145
6 镀锡145
6.1 用途、分类及不同类型镀锡溶液的比较145
6.3 氟硼酸盐镀锡146
6.4 碱性镀锡147
8 镀铁148
8.2 各类镀铁工艺148
8.1 镀铁的用途及分类148
7.2 镀铅工艺148
7.1 铅的性质与用途148
7 镀铅148
参考文献149
第8章 合金电镀150
1 合金镀层的分类及应用150
2 镀铜合金150
2.1 镀铜锌合金与仿金150
2.2 镀铜锡合金152
3 镀锡合金153
3.1 镀锡铅合金153
3.2 镀锡镍合金154
3.3 镀锡钴合金155
4 镀锌合金156
4.1 镀锌镍合金156
4.2 镀锌钴合金157
4.3 镀锌铁合金157
4.4 镀锡锌合金158
5 镀镍合金158
5.1 镀镍铁合金158
5.2 镀镍钴合金159
参考文献159
1 镀金和金合金160
1.1 碱性氰化物镀金160
第9章 贵金属及其合金电镀160
1.2 中性氰化物镀金162
1.3 酸性氰化物镀金162
1.4 亚硫酸盐镀金163
2 镀银164
2.1 氰化镀银工艺164
2.2 高速选择性镀银165
2.3 镀银后处理166
3 镀钯和钯镍合金166
3.1 电镀钯和钯镍合金工艺166
5 镀铑168
4 镀铂168
3.2 钯和钯镍合金镀液中各成分的作用及工艺条件的控制168
5.1 镀铑工艺169
5.2 镀铑溶液的控制与维护169
6 镀钌170
7 镀铟170
7.1 铟镀层的特点170
7.2 镀铟工艺170
参考文献171
第10章 特殊基材上电镀172
1 塑料电镀172
1.1 塑料电镀前预处理工艺173
1.2 塑料的化学镀和电镀工艺179
2.2 热扩散法180
2 玻璃和陶瓷电镀180
2.1 化学镀法180
3 印刷电路板电镀181
3.1 印刷电路板的孔金属化181
3.2 印刷电路板电镀铜工艺183
3.3 印刷电路板电镀锡铅合金工艺184
3.4 印刷电路板插头镀硬金工艺184
4 铝及铝合金电镀184
4.1 铝及铝合金电镀前特殊预处理184
4.2 铝合金一步法电镀186
6 不锈钢电镀187
5 钛和钛合金电镀187
5.2 钛和钛合金电镀后热处理187
5.1 钛和钛合金电镀前特殊预处理187
6.1 不锈钢镀前化学浸蚀处理188
6.2 不锈钢镀前活化处理188
6.3 不锈钢镀前活化预镀一步法189
7 锌合金压铸件电镀190
7.1 锌合金压铸件电镀工艺过程190
7.2 锌合金压铸件镀前脱脂、浸蚀工艺190
7.3 锌合金压铸件的活化和预镀工艺190
参考文献192
8.3 铁基粉末冶金件电镀和镀后处理192
8.2 铁基粉末冶金件电镀前预处理192
8.1 铁基粉末冶金件电镀工艺过程192
8 铁基粉末冶金件电镀192
第11章 电刷镀193
1 概述193
2 刷镀设备193
2.1 电源193
2.2 刷镀工具193
2.3 辅助设备194
3 刷镀溶液194
4 刷镀的工艺流程195
参考文献196
5 刷镀层的性能196
6 刷镀的有关参数及计算方法196
1.1 化学镀镍层的用途、组成和特性197
第12章 化学镀197
1 化学镀镍197
1.2 化学镀镍溶液的类型及特点198
1.3 化学镀镍磷合金工艺199
1.4 其它类型化学镀镍工艺201
1.5 不同金属基体材料上的化学镀镍202
2.1 复合化学镀镍工艺203
2 复合化学镀镍203
1.7 不合格化学镀镍层的退除203
1.6 化学镀镍层的热处理203
3 化学镀铜204
2.2 复合化学镀镍溶液的控制和维护204
3.1 单络合剂的化学镀铜工艺205
3.2 双络合剂的化学镀铜工艺205
3.3 化学镀铜溶液的配制、使用和维护206
4 化学镀银206
4.1 化学镀银工艺206
4.2 化学镀银溶液的配制程序和维护207
5.2 还原法化学镀金工艺208
5 化学镀金208
5.1 置换法化学镀金工艺208
6 化学镀钯及钯合金209
6.1 以肼或次磷酸钠为还原剂的化学镀钯工艺209
6.2 以次磷酸钠为还原剂的化学镀Pd—Ni合金工艺209
6.3 以次磷酸钠为还原剂的化学镀Pd—Co合金工艺209
7 化学镀钴210
7.1 以次磷酸钠为还原剂的化学镀钴工艺210
7.2 以硼化物为还原剂的化学镀钴工艺210
8 化学镀锡和锡铅合金211
参考文献211
1.1 碱性化学氧化(发蓝)212
1 钢铁的化学氧化212
第13章 金属的化学氧化和磷化212
1.2 酸性化学氧化(常温发黑)213
2 不锈钢的化学氧化215
2.1 不锈钢化学氧化的预处理工艺215
2.2 不锈钢的钝化216
2.3 不锈钢黑色氧化216
2.4 不锈钢的彩色化学氧化(着色)216
2.5 不锈钢彩色化学氧化的后处理工艺217
3 铝及铝合金的化学氧化217
3.1 碱性铬酸盐氧化217
3.2 酸性铬酸盐氧化217
3.3 阿洛丁(Alodine)氧化218
4.1 镁合金化学氧化溶液的配方及工艺219
4 镁合金的化学氧化219
4.2 镁合金化学氧化溶液的维护、调整及适用性220
5 铜和铜合金的化学氧化220
5.1 铜和铜合金的化学氧化溶液的配方及工艺220
5.2 铜和铜合金的化学钝化处理221
5.3 铜和铜合金的化学着色工艺221
6 钢铁磷化222
6.1 磷化膜的组成、性质及用途222
6.2 磷化处理施工方法223
6.3 磷化溶液的组成及工艺条件224
6.4 磷化液的维护和工艺控制225
6.5 磷化后处理工艺226
参考文献226
第14章 铝和铝合金的阳极氧化227
1 铝和铝合金阳极氧化膜性质和用途227
1.1 铝和铝合金阳极氧化膜的性质227
1.2 铝和铝合金阳极氧化膜的用途228
2 铝和铝合金的阳极氧化229
2.1 硫酸阳极氧化229
2.2 铬酸阳极氧化232
2.3 草酸阳极氧化233
3 铝和铝合金的特种阳极氧化235
3.1 硬质阳极氧化235
3.2 瓷质阳极氧化237
4 铝和铝合金阳极氧化后的着色238
3.3 磷酸阳极氧化238
4.1 化学染色238
4.2 电解着色240
5 铝和铝合金阳极氧化后的封闭处理245
5.1 热水、蒸汽封闭法245
5.2 重铬酸盐封闭法246
5.3 水解盐封闭法246
5.4 常温封闭法246
6 铝和铝合金不合格阳极氧化膜的退除247
参考文献247
第15章 电铸248
1 电铸的特征及电铸制品的应用248
1.1 电铸的优缺点248
1.2 电铸制品的应用248
2 电铸芯模材料及设计原则248
2.1 电铸芯模类型及材料的选择248
2.2 电铸芯模的设计原则249
3.2 非金属芯模的预处理方法249
3 电铸芯模的预处理249
3.1 金属芯模的预处理方法249
4 电铸镍250
4.1 瓦特型电铸镍工艺250
4.2 氨基磺酸盐电铸镍工艺251
4.3 高速电铸镍工艺252
5 电铸铜252
5.1 硫酸盐电铸铜工艺252
5.2 氟硼酸盐电铸铜工艺253
6 电铸铁253
7 电铸镍钴合金254
8 电铸时间、阴极电流密度与电铸镀层厚度的关系254
9 电铸后处理254
9.1 电铸后脱模254
9.2 电铸件的加固254
参考文献255
9.3 电铸件的修饰255
1 电镀液性能的测定256
1.1 pH的测定256
1.2 赫尔槽试验256
第16章 电镀液和电镀层的性能测定256
1.3 电镀液整平性能的测定258
1.4 电镀液分散能力的测定258
1.5 电镀液覆盖能力的测定259
1.6 阴极电流效率的测定260
1.7 极化曲线的测量261
2 电镀层性能的测定262
2.1 镀层厚度的测定(GB 6463)262
2.2 镀层的附着强度测试方法(GB 5270)265
2.3 硬度测试方法(GB 9790)265
2.4 镀层耐蚀性的测定268
2 电镀槽及其辅助装置274
2.1 电镀槽的结构及其选用274
第17章 电镀设备274
1 电镀生产的主要设备和基本要求274
2.2 电镀槽的分类277
2.3 电镀槽材料的选择278
3 电镀挂具282
3.1 挂具的形式和使用的材料282
3.2 挂具材料的截面积计算282
4.1 直流发电机组283
4.2 晶闸管整流器283
4 电镀电源283
3.4 挂具的绝缘283
3.3 挂具的使用要求283
4.3 特殊波形装置285
4.4 直流配电装置和汇流排286
4.5 直流供电方式及线路289
4.6 电镀槽工作电压和电流的调节290
4.7 交流电源292
5 半自动和全自动电镀装置294
5.1 滚镀设备294
5.2 直线式电镀自动线296
5.3 环形电镀自动线297
5.4 线材和带材电镀自动线298
7 通风设备299
7.1 抛磨光机的通风设备299
6 过滤设备299
7.2 电镀槽的通风设备301
参考文献302
第18章 电镀的三废治理303
1 电镀三废治理的有关规定303
1.1 电镀废水303
1.2 电镀废气与粉尘303
2 电镀废水治理的主要方法304
2.1 含六价铬的废水的处理304
2.2 含镍废水的处理305
2.3 含氰废水的处理306
2.5 含铜废水的处理307
2.4 贵金属废水的处理307
2.6 含锌废水的处理308
2.7 酸碱废水的处理308
2.8 沉淀物的去除308
3 电镀废气和粉尘治理的主要方法309
3.1 常用的气体净化设备309
3.2 铬酸废气的净化治理309
3.3 含氰废气的治理310
3.4 氮氧化物废气的治理310
3.5 酸雾及氯化物废气的治理311
3.6 粉尘的治理311
4 重金属污泥的利用312
参考文献313
1.1 涂料的组成314
1.2 涂料的功能314
1 涂料组成、功能、分类和发展趋势314
第19章 涂料和涂装314
第4篇 表面涂敷技术314
1.3 涂料的分类315
1.4 涂料的发展趋势315
2.1 手工涂装316
2 涂装技术316
2.2 浸涂、淋涂涂装318
2.3 非静电喷涂及应用319
2.4 静电涂装320
2.5 电泳320
2.6 粉末涂装322
2.7 辊涂323
2.8 于燥方法、涂层病态、施工安全与防护323
3 各种底材用涂料和涂装技术329
3.1 金属用涂料和涂装技术329
3.2 木材用涂料和涂装技术331
3.4 其它底材用涂料和涂装技术332
3.3 塑料用涂料和涂装技术332
4 典型工业产品使用的涂料及施工方案333
5 几种典型的特种涂料334
参考文献336
第20章 粘接338
1 粘接基本原理338
2 被粘材料的表面处理(预处理)341
2.1 一般处理341
2.2 物理方法处理341
2.3 化学方法处理342
3 胶粘剂344
4 胶粘剂在各行业中的应用349
参考文献351
第21章 堆焊353
1 堆焊材料的分类353
2 常用堆焊材料及堆焊工艺353
2.1 铁基堆焊材料及工艺353
2.2 镍基堆焊材料及工艺365
2.3 钴基堆焊材料及工艺366
2.4 铜基堆焊材料及工艺368
2.5 碳化钨堆焊材料及工艺370
4 堆焊设备与方法的选择371
4.1 堆焊设备371
3 堆焊材料的选择372
4.2 堆焊方法的选择374
参考文献376
第22章 熔结377
1 氧乙炔火焰粉末喷熔377
1.1 基本概念377
1.2 氧乙炔火焰粉末喷熔设备378
1.3 喷熔用合金粉末380
1.4 氧乙炔火焰粉末喷熔工艺383
1.5 喷熔层缺陷产生的原因及预防385
2 真空熔结385
2.1 基本概念385
2.2 涂层合金材料386
2.3 真空熔结合金涂层工艺388
2.4 真空熔结的涂层特性、功能与应用389
参考文献391
第23章 热喷涂392
1 热喷涂原理392
1.1 喷涂涂层形成过程和涂层形成原理392
1.2 涂层结构392
1.3 涂层结合机理392
1.4 涂层残余应力392
2 热喷涂的种类和特点392
3 热喷涂前的预处理393
3.1 基体表面的清洗、脱脂393
3.2 基体表面氧化膜的处理393
3.3 基体表面的粗化处理394
3.4 基体表面的预热处理394
3.5 非喷涂表面的保护394
4 热喷涂材料395
4.1 热喷涂线材395
4.2 热喷涂粉末398
5 热喷涂工艺及设备406
5.1 氧乙炔火焰喷涂与喷熔406
5.2 电弧线材喷涂409
5.3 等离子弧喷涂410
5.4 爆炸喷涂411
5.5 其它热喷涂方法412
6.1 热喷涂涂层后处理413
6.2 热喷涂涂层性能的检验项目413
6.3 涂层与基体表面的结合强度试验413
6.4 涂层自身粘结强度试验414
6.5 涂层孔隙率的测定415
6.6 涂层耐蚀性能试验416
参考文献416
1.1 电火花涂敷工作原理417
1.2 电火花涂敷过程的分析417
第24章 电火花涂敷417
1 电火花涂敷原理和特点417
1.3 电火花表面涂敷的特点418
2 电火花涂敷工艺及应用范围418
2.1 电火花涂敷应用范围418
2.2 电火花涂敷工艺方法418
3 电火花涂敷层的特性421
3.1 电火花涂敷层的形貌421
3.4 电火花涂敷层的结构422
3.5 电火花涂敷层的厚度422
3.3 电火花涂敷层的化学元素分布422
3.2 电火花涂敷层的金相组织422
3.6 电火花涂敷层的残余应力425
3.7 电火花涂敷层的性能425
4 包火花涂敷应用实例428
4.1 电火花模具涂敷428
4.2 电火花刀具涂敷429
4.3 电火花涂敷零部件429
参考文献430
4.4 磨损表面电火花修复430
第25章 热浸镀431
1 概述431
1.1 金属镀层的种类431
1.2 热浸镀工艺431
1.3 热镀的发展432
2 热镀锌433
2.1 锌对钢铁的保护作用433
2.2 锌和铁之间的反应433
2.3 热镀锌生产工艺436
2.4 带钢热镀锌生产技术的发展441
2.5 热镀锌钢板的应用448
3 热镀铝450
3.1 热镀铝镀层的形成450
3.2 影响铁铝合金层附着力的因素450
3.3 热镀铝工艺451
4 热镀铅452
3.4 镀铝钢板的性能和用途452
4.1 热镀铅镀层的形成453
4.2 热镀铅钢板生产工艺453
4.3 热镀铅-锡合金钢板产品454
参考文献455
1.1 搪瓷工艺457
1.2 搪瓷的分类457
1 搪瓷的工艺和分类457
第26章 搪瓷涂敷457
2 建筑搪瓷458
2.1 建筑用内外装饰钢板搪瓷墙面板458
2.2 镀铝薄钢板搪瓷墙面板459
3 医用搪瓷460
3.1 搪瓷牙冠460
3.2 植人人体的搪瓷材料462
5.1 红外辐射搪瓷的制备463
5 红外辐射搪瓷463
4.3 电子搪瓷基板的应用463
4.1 电子搪瓷基板的制备工艺463
4 电子搪瓷基板463
4.2 电子搪瓷基板的性能463
5.2 红外辐射搪瓷的应用464
6 耐酸搪瓷(搪玻璃)464
6.1 耐酸搪瓷制品的基材及坯体的质量要求464
6.2 耐酸搪瓷制品对搪瓷的质量要求465
6.3 搪玻璃的制造工艺465
6.4 搪玻璃制品的耐腐蚀性能466
6.5 搪玻璃层表面局部破损时的修补467
7 微晶搪瓷468
7.1 Li_2-Al_2O_3-SiO_2系微晶搪瓷468
7.2 磨加微晶体的微晶搪瓷468
8.1 低碳钢用高温搪瓷469
8.2 不锈钢用高温搪瓷469
8.3 高温合金用高温搪瓷469
7.3 微晶搪瓷的应用469
8 高温搪瓷469
9 搪瓷工艺设备471
9.1 铁坯制作工艺设备471
9.2 瓷釉熔制及淬冷设备471
9.3 涂搪工艺设备472
9.4 搪瓷烧成工艺设备473
参考文献474
1.2 选用涂层应考虑的因素475
2.1 熔烧涂层工艺475
2 陶瓷涂层的工艺及特点475
1 陶瓷涂层的分类和选用涂层应考虑的因素475
1.1 陶瓷涂层的分类475
第27章 陶瓷涂敷475
2.2 高温喷涂陶瓷涂层工艺476
2.3 热扩散涂层工艺477
2.4 低温烘烤陶瓷涂层工艺477
2.5 热解沉积涂层工艺477
3.1 高温喷涂陶瓷涂层的性能和用途478
3 陶瓷涂层的性能和用途478
3.2 热扩散涂层的性能和用途480
3.3 低温烘烤陶瓷涂层的用途486
参考文献492
第28章 塑料涂敷493
1 概述493
2 塑料粉末涂料及涂敷方法的分类494
3 塑料涂敷方法介绍494
3.1 静电喷涂法494
3.2 流动浸塑法495
3.3 静电流浸法496
3.4 挤压涂敷法496
3.5 分散液喷涂法497
3.6 粉末火焰喷涂法498
3.7 金属塑料复合膜粘贴法499
3.8 其它涂敷方法500
4 塑料涂敷层质量检验501
参考文献502
第29章 表面涂敷设备503
1 表面涂敷(装)的作用和应用范围503
2 涂敷前的清理设备503
2.1 喷射式清理设备503
2.2 干法清理设备504
2.3 湿法清理设备507
3 喷敷设备509
3.1 涂敷工具及设备509
3.2 静电喷涂设备510
3.3 静电喷粉涂装设备511
4 电泳涂装及其设备513
4.1 电泳涂装种类513
4.2 电泳涂装特点514
4.3 电泳涂装工艺及设备514
参考文献516
1.1 喷丸在生产中的应用517
1 概述517
第30章 喷丸强化517
第5篇 表面改性技术517
1.2 喷丸强化518
1.3 喷丸的其它方面的应用519
2 喷九工艺参数519
2.1 喷丸强度测定519
2.2 表面覆盖率521
3.1 喷丸过程522
3 喷丸介质522
3.2 铸铁弹丸523
3.3 铸钢弹丸523
3.4 钢丝切割丸524
3.5 玻璃弹丸524
3.6 其它喷丸介质527
3.7 弹丸的选用528
4 喷丸设备529
4.1 叶轮式喷九机529
4.2 气动式喷丸机530
4.4 喷丸机辅助装置533
4.3 其它喷丸设备533
5 受控喷丸基础535
5.1 喷九表层的形貌和组织结构535
5.2 受控喷丸对材料力学性能的影响539
5.3 喷丸表层残余应力场539
5.4 喷射特性对残余应力的影响541
参考文献543
1.3 残余应力的极限544
2.1 不均匀塑性变形引起的残余应力544
2 残余应力的形成544
1.4 残余应力的分类544
第31章 机械零件的表层残余应力544
1.2 残余应力的性质544
1.1 残余应力的平衡条件544
1 残余应力544
2.2 温度差异引起的残余应力545
2.3 金属的相变应力548
2.4 化学成分差异引起的应力549
3.1 残余应力对疲劳强度的影响550
3.2 残余应力对应力腐蚀的影响550
3 残余应力对机械零件性能的影响550
3.3 残余应力对加工精度的影响552
3.4 残余应力对尺寸稳定性的影响552
4 合理调整残余应力的表面处理553
4.1 表面热处理553
4.2 薄壳淬火554
4.3 应力淬火555
4.4 表面形变强化555
5 残余应力的测定557
5.1 应力松弛法测定残余应力557
5.2 X射线衍射法测定残余应力559
5.3 应力敏感性测残余应力560
参考文献561
1 感应加热表面热处理562
1.1 感应加热基本原理562
第32章 钢的表面热处理562
1.2 感应加热淬火的特点及基本技术要求563
1.3 中、高频感应加热表面淬火工艺566
1.4 感应器572
1.5 感应加热淬火件的回火574
1.6 工频感应加热表面淬火575
1.7 超高频冲击淬火及大功率脉冲感应淬火575
1.8 感应加热淬火件的质量检验575
1.9 感应加热淬火件常见缺陷及防止方法577
2 火焰加热表面淬火579
2.1 火焰加热的火焰特性579
2.2 火焰加热的供气装置580
2.3 火焰加热表面淬火方法580
2.4 火焰淬火喷嘴581
2.5 淬火工艺参数选择581
2.6 火焰淬火的质量检验582
2.7 火焰淬火的安全技术要求582
4 接触电阻加热淬火583
3 电解液淬火583
5 常见高、中频感应器的结构与实际应用举例584
参考文献590
第33章 钢的化学热处理591
1 钢的渗碳591
1.1 渗碳用钢591
1.2 渗碳质量的技术要求592
1.3 常用渗碳钢的预备热处理、非渗碳表面的防渗593
1.4 固体渗碳594
1.5 盐浴渗碳596
1.6 气体渗碳598
1.7 其它渗碳方法604
1.8 渗碳后的热处理604
1.9 渗碳件的质量检验604
1.10 渗碳常见缺陷及防止方法605
2 钢的渗氮606
2.1 常用渗氮钢种、氮化物及合金元素的作用606
2.2 钢的气体渗氮608
2.3 其它渗氮方法615
2.4 渗氮件的质量检查616
2.5 渗氮常见缺陷及防止措施617
3 钢的碳氮共渗619
3.1 碳氮共渗件的技术条件619
3.2 气体碳氮共渗619
3.3 液体碳氮共渗621
3.4 碳氮共渗用钢及共渗后的热处理622
3.5 碳氮共渗件的质量检验623
3.6 碳氮共渗件常见缺陷及防止措施624
4 钢的氮碳共渗624
4.1 氮碳共渗分类、生成相及技术条件624
4.2 气体氮碳共渗626
4.3 熔盐氮碳共渗628
4.4 氮碳共渗件的质量检查629
4.5 氮碳共渗常见缺陷及防止措施629
4.7 氮碳共渗复合强化630
4.6 奥氏体氮碳共渗630
5 渗硼631
5.1 渗硼层组织、特性及常用渗硼材料631
5.2 主要渗硼方法632
5.3 渗硼件的热处理637
5.4 渗硼件的质量检验637
5.5 渗硼层的缺陷及防止措施638
6 其它化学热处理638
6.1 渗硫638
6.2 氧氮共渗640
参考文献641
第34章 等离子体扩渗处理642
1 等离子体的物理概念642
1.1 等离子体的性质642
1.2 气体放电的伏安特性曲线642
2.2 离子渗氮的主要特点643
2.1 离子渗氮理论643
1.3 离子轰击阴极表面的物理、化学效应643
2 离子渗氮643
2.3 离子渗氮设备644
2.4 离子渗氮工艺及操作645
2.5 离子渗氮层的质量检验650
2.6 离子渗氮件的常见缺陷及对策650
3.1 离子渗碳原理及优点651
3.2 离子渗碳、离子碳氮共渗工艺及操作651
3 离子渗碳、离子碳氮共渗651
4 离子氮碳共渗652
5 离子渗硫、离子硫氮共渗和离子硫氮碳共渗653
参考文献655
第35章 激光表面改性656
1 激光表面改性设备656
1.1 激光器656
1.2 导光聚焦系统及其元部件660
2 激光表面改性工艺662
2.1 激光表面相变硬化(激光淬火)663
2.2 激光表面熔覆与合金化668
2.3 激光表面非晶化675
2.4 激光冲击硬化677
3 复合表面改性技术680
3.1 黑色金属复合表面改性技术680
3.2 有色金属复合表面改性技术681
3.3 两种以上复合表面改性技术681
参考文献682
2 电子束表面改性设备683
2.1 电子枪系统683
1 电子束表面改性基本原理683
第36章 电子束表面改性683
2.2 真空系统684
2.3 控制系统684
2.4 电源系统685
3 电子束表面改性工艺及其特点686
3.1 电子束加热区的温度场686
3.2 电子束加热区能量与时间的关系686
3.3 电子束表面改性束流的控制687
4 应用实例与效果688
3.4 电子束表面改性工艺的特点688
参考文献689
第37章 离子注入表面改性690
1 历史的简略回顾690
2 荷能离子在固体中的力学运动及其诱发的固体内部变化690
2.1 荷能离子在固体中的力学运动690
2.2 荷能离子诱发的固体内部变化692
4.1 半导体材料的离子注入693
3 离子注入的基本设备693
4 各种材料的离子注入改性693
4.2 金属、陶瓷等材料的离子注入694
4.3 有机高分子材料的离子注入697
4.4 离子注入的其它应用697
5 离子注入装备的新发展697
参考文献699
2 材料的真空蒸发特性700
1 真空蒸镀的定义和特点700
第6篇 气相沉积技术700
第38章 真空蒸镀700
3 各种加热方式和蒸发源703
4 薄膜的沉积速率与基板上的膜厚分布705
5 真空蒸镀设备708
6 真空蒸镀工艺711
参考文献715
第39章 溅射镀膜716
1 溅射镀膜的定义和特点716
2 溅射的基本规律716
2.1 影响溅射率的各种因素716
2.2 溅射粒子的状态、能量分布与角分布718
3 各种溅射方法720
3.1 直流二极、三极和四极溅射720
3.2 射频溅射721
3.3 磁控溅射722
3.4 离子束溅射724
4 溅射镀膜设备726
5 溅射镀膜工艺727
6 薄膜制作举例728
6.1 合金薄膜的制作728
6.2 化合物薄膜的制作729
6.3 非晶薄膜的制作729
6.4 单晶薄膜的制作730
6.5 有机薄膜的制作730
参考文献730
第40章 离子镀731
1 气体放电等离子体离子镀731
2 空心阴极放电离子镀731
2.1 概述731
2.2 工作原理及装置732
2.3 空心阴极枪工艺参数732
3.1 概述735
3 多弧离子镀735
2.5 空心阴极离子镀产品一览735
2.4 空心阴极离子镀工艺实例735
3.2 工作原理和装置736
3.3 阴极斑点737
3.4 多弧离子镀蒸发源的型式737
3.5 多弧离子镀的阴极靶738
3.6 多弧离子镀的工艺参数739
3.7 多弧离子镀设备工艺实例739
4 离化团束沉积技术741
参考文献743
第41章 普通化学气相沉积(CVD)744
1 化学气相沉积的一般原理744
1.1 热分解反应沉积744
1.2 氢还原反应沉积745
1.3 化学合成反应沉积745
1.4 化学输运反应沉积745
2.1 开管气流法747
2 化学气相沉积的装置与技术747
2.2 封管法748
2.3 近间距沉积法748
3 影响沉积质量的因素749
3.1 沉积参数的影响749
4 低压化学气相沉积技术及其工艺模拟理论750
4.1 低压化学气相沉积的特点750
3.3 反应系统装置的影响750
3.2 衬底的影响750
4.2 LPCVD工艺模拟理论的研究概况751
4.3 LPCVD多晶硅工艺的理论模拟751
4.4 LPCVD氮化硅工艺的理论模拟753
参考文献756
第42章 等离子体化学气相沉积(PCVD)757
1 等离子体的基本特征757
1.1 等离子体的形成757
1.2 等离子体的温度757
2.1 射频放电的一般现象758
2 射频辉光放电758
1.3 浮置极板上鞘层的形成758
2.2 射频放电的其它优点759
3 等离子体用于化学气相沉积759
3.1 等离子体增强化学反应、降低沉积温度759
3.2 PCVD系统中的等离子体性质759
4 等离子体化学气相沉积的工艺设备760
4.1 平行圆板形沉积工艺设备760
4.2 扩散炉型等离子体化学气相沉积设备761
5 工艺参数对沉积速率和薄膜质量的影响763
5.1 等离子体化学气相沉积氮化硅薄膜763
5.2 等离子体化学气相沉积氧化硅薄膜767
5.3 等离子体化学气相沉积非晶硅768
6 PCVD薄膜的性质及应用769
6.1 氮化硅膜的性质769
6.3 非晶硅膜的性质770
6.2 二氧化硅膜的性质770
6.4 PCVD技术的应用771
7 PCVD领域的新进展773
7.1 激活低压金刚石气相生长的非平衡热力学理论773
7.2 用PCVD技术制备功能梯度材料774
参考文献775
第43章 金属有机化学气相沉积(MOCVD)776
1 引言776
2 原理776
3 设备和工艺776
3.1 设备776
3.2 工艺777
4 MO源和新MO源778
4.1 沉积金属薄膜用的新MO源779
5.1 涂层780
5 应用780
5.2 细线和各种几何图形780
4.3 沉积化合物半导体材料的新MO源780
4.2 沉积氧化物、氮化物和氟化物薄膜用的新MO源780
5.3 化合物半导体材料781
6 小结781
参考文献781
第44章 激光化学气相沉积(LCVD)782
1 发展概况782
2 激光化学气相沉积设备782
3 激光化学气相沉积工艺及其特点783
4 激光化学气相沉积的应用784
4.1 氮化硅膜784
4.2 正在研究开发的各种膜层特性785
参考文献785
第45章 分子束外延(MBE)786
1 引言——发展简史和原理786
1.1 发展简史786
1.2 分子束外延原理787
2.1 MBE系统结构788
2 分子束外延系统788
2.2 MBE系统分类789
3 MBE生长工艺792
3.1 化学清洁处理792
3.2 热处理脱附792
3.3 外延生长793
3.4 掺杂794
4 MBE材料及器件应用794
4.1 超晶格量子阱材料794
参考文献797
4.2 器件应用797
第46章 离子束合成薄膜技术798
1 薄膜合成中的离于束应用概述798
1.1 薄膜合成中的离子束工艺与其它离子工艺的关系798
1.2 离子束辅助沉积798
1.3 低能离子束沉积798
1.4 离子簇束沉积799
2.1 离子束辅助沉积装置实例800
2.2 离子束辅助沉积装置实例二800
2 离子束辅助沉积的基本工艺及装置800
2.3 离子束辅助沉积的基本工艺及特点801
3 离子束辅助沉积的机理801
3.1 离子束辅助沉积的基本过程801
3.2 离子束轰击对薄膜组分及其分布的影响802
3.3 离子束辅助轰击对薄膜织构的影响803
3.4 离子束辅助轰击对薄膜颗粒度与致密度的影响805
4.1 离子束辅助沉积应用实例一806
4.2 离子束辅助沉积应用实例二806
4 离子束辅助沉积的应用和发展806
3.5 离子束辅助轰击对薄膜相结构的影响806
4.3 离子束辅助沉积应用实例三807
4.4 离子束辅助沉积应用实例四807
4.5 离子束辅助沉积的其它应用实例808
4.6 浸没式离子束辅助沉积装置809
4.7 磁过滤冷极弧源离子束辅助沉积装置809
参考文献810
4.8 离子束辅助沉积的其它新动向810
第7篇 玻璃的表面处理811
第47章 玻璃的表面装饰811
1 玻璃表面装饰的分类811
1.1 按装饰的效果分类811
1.2 按装饰的方法分类811
2 玻璃表面装饰色釉811
2.1 玻璃釉的要求和种类812
2.2 玻璃釉的化学成分及配制812
2.3 玻璃釉调合剂813
2.4 玻璃表面施釉和焙烧(烤花)814
3 玻璃表面化学蚀刻815
3.1 化学蚀刻原理815
3.2 表面蚀刻工艺815
4 玻璃表面蒙砂816
4.1 化学腐蚀法(化学蒙砂)816
5 玻璃表面喷砂和砂雕817
5.1 喷砂设备与工艺817
4.2 蒙砂釉817
5.2 砂雕818
6 玻璃表面冰花818
7 玻璃表面装饰涂层819
7.1 涂层的特点和分类819
7.2 无机发光涂层819
7.3 树脂印花涂层820
8 玻璃表面上金(描金)821
9.2 堆花粉的制造823
9 玻璃表面堆花(堆釉)823
9.1 堆花工艺流程823
参考文献824
第48章 玻璃的表面强化825
1 玻璃表面对强度的影响825
2 玻璃的热处理增强827
2.1 淬冷法增强(钢化玻璃)827
3.1 低温型离子交换831
3 玻璃的离子交换增强831
2.2 加热拉伸增强831
3.2 高温型离子交换835
3.3 高温型和低温型结合离子交换836
4 玻璃表面酸处理增强837
4.1 酸洗法所用酸液组成837
4.2 酸洗法工艺制度837
5.2 玻璃表面热端涂层838
5.1 表面涂层的分类838
5 玻璃表面涂层增强838
4.3 酸洗法和其它增强方法的结合838
5.3 玻璃表面冷端涂层840
参考文献841
第49章 玻璃表面脱碱842
1 用脱碱法提高玻璃强度842
2 用脱碱法增加玻璃的化学稳定性845
2.1 酸性气体脱碱处理845
2.2 盐类溶液喷涂脱碱846
2.3 固体气化分解脱碱846
参考文献847
第50章 玻璃的表面着色848
1 玻璃表面膜着色848
1.1 气相沉积虹彩848
1.2 热喷涂着色849
1.3 溶胶凝胶浸涂着色851
2 玻璃表面扩散着色852
2.1 扩散着色机理853
2.2 影响扩散着色的因素854
2.3 扩散着色工艺856
3 玻璃表面辐照着色857
3.1 紫外线辐照着色858
3.2 丁射线辐照着色858
参考文献859
2.1 化学还原法镀膜860
2 玻璃表面镀膜的方法860
1.4 按膜和玻璃结合情况分类860
1.3 按膜的结构分类860
1.2 按膜的成分分类860
1.1 根据性质和用途分类860
1 玻璃表面镀膜的分类860
第51章 玻璃的表面镀膜860
2.2 高温分解法镀膜861
2.3 化学气相沉积法镀膜861
2.4 溶胶——凝胶法镀膜862
2.6 真空沉积(蒸发)法镀膜863
2.5 电浮法镀膜863
2.7 阴极溅射法镀膜864
2.8 离子镀(离子渗镀)法镀膜864
2.9 静电粉末喷涂法镀膜865
3 玻璃表面光学膜865
3.1 玻璃表面增透膜865
3.2 玻璃表面反射膜867
3.3 玻璃表面分光膜868
3.4 玻璃表面吸光膜和滤光膜868
4.1 热反射膜870
4 玻璃表面热反射膜、吸热膜和低辐射膜870
4.2 吸热膜871
4.3 低辐射膜872
5 玻璃表面导电膜873
5.1 LTO导电膜873
5.2 SnO_2导电膜873
5.3 多层导电膜874
6 玻璃表面电致变色膜(EC)874
6.1 电致变色原理874
6.2 电致变色膜层材料与镀膜工艺875
7 玻璃表面憎水和防雾膜875
7.1 憎水膜875
7.2 防雾膜876
参考文献876
1 表面技术在修复中的应用877
1.1 电刷镀在修复中的应用877
第52章 表面技术在结构材料上的应用877
第8篇 材料表面技术应用指南877
1.2 热喷涂(喷焊)在修复中的应用879
1.3 堆焊在修复中的应用881
1.4 粘接在修复中的应用883
2 表面技术在提高材料耐蚀性方面的应用885
2.1 表面涂镀技术在提高材料耐蚀性方面的应用885
2.2 利用离子注入提高材料耐蚀性887
2.3 利用化学热处理提高材料的耐蚀性888
3 利用表面技术提高材料的耐磨性889
3.1 利用表面涂镀技术提高材料耐磨性889
3.2 利用离子注入技术提高材料的耐磨性890
3.3 利用化学热处理提高材料耐磨性891
3.4 利用复合表面技术提高材料的耐磨性892
4 利用表面技术提高材料的疲劳强度893
5 激光热处理在于程材料中的应用894
5.1 激光热处理在铸铁中的应用894
5.2 利用激光热处理改善金属材料的耐蚀性895
5.4 激光热处理在模具钢中的应用896
5.3 激光热处理在汽车零件上的应用896
5.5 激光热处理在工具钢中的应用897
5.6 激光热处理在有色金属中的应用898
5.7 激光热处理与其它工艺成本的比较899
6 几种表面技术的比较900
6.1 离子渗氮与其它表面技术的比较900
6.2 离子镀TiN与气体碳氮共渗的比较901
6.3 不同镀铬技术的对比及其与真空镀膜(PVD)技术的竞争901
6.4 热喷涂方法、工艺特点及与其它技术的比较902
6.5 渗碳技术的发展及其比较904
6.6 粘接、电刷镀、离子注入的特点与应用范围比较904
参考文献905
第53章 表面技术在光学材料及器件上的应用906
1 光学薄膜分类906
2 薄膜光学907
3 增透膜908
4.2 电介质反射膜912
4.1 金属反射膜912
4 反射膜912
5 干涉滤光膜915
5.1 截止滤光片915
5.2 带通滤光片917
6 分光膜918
参考文献920
第54章 表面技术在光电子器件及材料上的应用921
1 光电子器件和材料921
2.1 电光源和激光器922
2 表面技术在光源器件及材料上的应用922
2.2 激光薄膜923
2.3 半导体激光器与表面技术923
3 表面技术在光电探测器件及材料上的应用926
3.1 光电探测器及与其有关的特性参数926
3.2 光电子发射器件928
3.3 光电导探测器930
3.4 光伏型探测器932
3.5 红外探测器935
3.6 像管936
3.7 真空摄像器件938
3.8 固体摄像器件940
4 表面技术在能量转换器件和材料上的应用943
4.1 太阳电池转换效率的极限和损失944
4.2 各种势垒的太阳电池944
4.3 薄膜太阳电池946
5 表面技术在光电存储材料和器件上的应用947
5.1 表面技术在光盘方面的应用947
5.2 表面技术在光学全息存储方面的应用949
6 表面技术在光电显示器件及材料上的应用951
6.1 显示器件的分类和主要特性指标951
6.2 阴极射线管(CRT)与表面技术953
6.3 液晶显示器件与表面技术953
6.4 电致发光显示器件与表面技术953
7 表面技术在光电信息传输材料和器件上的应用956
7.2 光纤的传输特性957
7.1 光纤的类型与应用957
7.3 特种光纤及应用958
7.4 光纤的制造技术958
7.5 表面技术在光电传输器件上的应用961
8 表面技术在集成光学材料和器件上的应用964
8.1 集成光学简介964
8.2 光波导材料964
8.3 导波光学器件965
参考文献966
第55章 表面技术在微电子器件和材料上的应用967
1 表面技术对微电子技术发展的重大影响967
2 薄膜元件及其电学性能967
2.1 无源薄膜元件968
2.2 有源薄膜元件970
3 微电子微细加工技术971
3.1 集成电路的制作971
3.2 微细加工技术972
参考文献977
1998《材料表面技术及其应用手册》由于是年代较久的资料都绝版了,几乎不可能购买到实物。如果大家为了学习确实需要,可向博主求助其电子版PDF文件(由钱苗根主编 1998 北京:机械工业出版社 出版的版本) 。对合法合规的求助,我会当即受理并将下载地址发送给你。
高度相关资料
-
- Java技术及其应用
- 1999 北京:高等教育出版社
-
- 航空材料及其应用工艺手册
- 1981
-
- Intranet技术及其应用
- 1998 西安:西安电子科技大学出版社
-
- 表面裂纹理论及其应用
- 1987 西安:西北工业大学出版社
-
- 粗糙表面 测量、表征及其应用
- 1987 杭州:浙江大学出版社
-
- 电气材料及其应用
- 1983 西安:陕西科学技术出版社
-
- 油料应用技术手册
- 1989 沈阳:辽宁科学技术出版社
-
- 半导体表面钝化技术及其应用
- 1981 北京:国防工业出版社
-
- 新材料技术及其应用
- 1989 北京:中国建筑工业出版社
-
- 新型材料及其应用
- 1990 武汉:华中理工大学出版社
-
- 固体材料及其应用
- 1994 广州:华南理工大学出版社
-
- 工程材料及其应用
- 1986 北京:机械工业出版社
-
- 声表面波器件及其应用
- 1983 北京:人民邮电出版社
-
- 声表面波器件及其应用
- 1984 北京:科学出版社
-
- 世界最新集成运算放大器及其互换手册 续集 日、美、德、荷兰、法和韩国型号及其互换
- 1993 长沙:中南工业大学出版社
提示:百度云已更名为百度网盘(百度盘),天翼云盘、微盘下载地址……暂未提供。➥ PDF文字可复制化或转WORD