《航空制造工程手册 框架壳体工艺》求取 ⇩
作者 | 《航空制造工程手册》总编委会主编 编者 |
---|---|
出版 | 北京:航空工业出版社 |
参考页数 | 392 ✅ 真实服务 非骗流量 ❤️ |
出版时间 | 1997(求助前请核对) 目录预览 |
ISBN号 | 780134233X — 违规投诉 / 求助条款 |
PDF编号 | 84978148(学习资料 勿作它用) |
求助格式 | 扫描PDF(若分多册发行,每次仅能受理1册) |
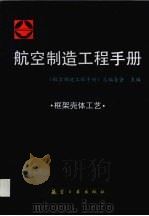
第1章 概论1
1.1 概述1
1.2 航空机载设备壳体分类1
1.2.1 按系统功能分类1
1.2.2 按壳体材料分类2
1.3 航空机载设备壳体特点2
1.3.1 结构特点2
1.3.2 工艺特点2
1.4 壳体加工工艺技术发展趋向3
第2章 框架壳体制造的工艺基础5
2.1 框架壳体毛坯5
2.1.1 毛坯材料5
2.1.2 毛坯种类7
2.1.3 毛坯制造及精度12
2.1.3.1 典型锻件工艺简介12
2.1.3.2 典型铸件工艺简介14
2.1.4 毛坯热处理19
2.1.5 毛坯检验20
2.2 壳体加工工艺基础28
2.2.1 复杂壳体设计图的布局28
2.2.2 复杂壳体设计图的工艺分析29
2.2.2.1 壳体精加工阶段的加工表面29
2.2.2.2 壳体结构特殊部位对加工的影响32
2.2.2.3 壳体其它特殊要求35
2.2.2.4 油路系统分析及油路系统图35
2.2.3 复杂壳体工艺路线和工序安排36
2.2.3.1 壳体加工工艺路线36
2.2.3.2 半精加工阶段工序安排37
2.2.3.3 壳体加工辅助工序安排39
2.2.3.4 壳体加工各工种的编排39
2.2.4 粗、精定位基准的选择43
2.2.4.1 粗基准的选择43
2.2.4.2 精基准的选择47
2.2.4.3 壳体基准的要求48
2.2.4.4 壳体夹具的夹紧点49
2.3 各种加工工艺在框架壳体加工中的应用50
2.3.1 钻削工艺50
2.3.1.1 概述50
2.3.1.2 空间油路孔的加工50
2.3.1.3 铰孔55
2.3.1.4 挤孔56
2.3.1.5 钻床反向锪圆面工艺59
2.3.1.6 钻床切槽工艺61
2.3.2 车削工艺62
2.3.2.1 概述62
2.3.2.2 影响车床加工孔位置精度的因素及总误差分析62
2.3.2.3 车床夹具的平衡68
2.3.2.4 组合钻及组合扩孔钻在车床上的应用68
2.3.2.5 螺纹对孔同轴度和对端面垂直度的控制方法72
2.3.2.6 位置精度小于±0.05mm的控制方法72
2.3.3 金刚镗床加工工艺75
2.3.2.1 概述75
2.3.3.2 床头调整和调整工具75
2.3.3.3 镗床夹具的调整79
2.3.3.4 镗刀头的调整82
2.3.3.5 金刚镗床的定位形式82
2.3.3.6 金刚镗床控制同轴度的工艺方法83
2.3.3.7 金刚镗床加工细长孔的方法83
2.3.3.8 金刚镗床加工易产生问题的原因及其解决措施84
2.3.4 铣削工艺85
2.3.4.1 普通铣床加工85
2.3.4.2 仿型铣床加工87
2.3.4.3 镜面铣削加工92
2.3.5 坐标镗床镗孔与切槽94
2.3.5.1 平行孔系加工94
2.3.5.2 双斜孔加工96
2.3.5.3 孔端面及孔内槽加工98
2.3.5.4 小孔镗削98
2.3.5.5 坐标镗床加工前的准备工作98
2.3.5.6 提高镗孔质量的常用方法101
2.3.6 钳工加工工艺101
2.3.6.1 铰锥孔101
2.3.6.2 手工攻丝102
2.4 壳体空间角度和尺寸的计算与检测102
2.4.1 空间角度(复合角)计算公式102
2.4.2 壳体空间角度和尺寸计算示例105
2.4.3 计算空间角度合成偏差的方法107
2.4.4 壳体斜孔角度和尺寸的通用检测方法110
2.4.5 壳体斜孔空间角度和交点尺寸检测示例112
第3章 框架壳体加工技术114
3.1 数控加工技术在壳体加工中的应用114
3.1.1 概述114
3.1.2 数控加工工艺应用基础114
3.1.3 数控机床上夹具的选用119
3.1.4 加工中心的某些加工方法121
3.1.5 工艺编制中应注意的问题123
3.2 组合机床在框架壳体加工中的应用124
3.2.1 组合机床加工特点124
3.2.2 框架壳体常用组合机床的配置方式124
3.2.3 框架壳体组合机床的要求和发展127
3.2.4 组合机床工艺方案制订原则127
3.2.5 组合机床加工铝合金材料的一般切削用量129
3.2.6 组合机床加工框架壳体的一般精度129
3.2.7 组合机床加工中常出现的问题及解决办法130
3.3 壳体组件加工技术131
3.3.1 壳体压套工艺技术131
3.3.1.1 压套工艺过程和关键技术131
3.3.1.2 压套易产生的问题和采取的措施132
3.3.1.3 压套工装及辅助设备132
3.3.1.4 压套后壳体衬套孔的精加工和关键技术133
3.3.2 堵塞孔的工艺技术138
3.3.2.1 可拆卸式堵塞138
3.3.2.2 不可拆卸式堵塞141
3.3.3 光孔上螺桩的工艺技术145
3.3.3.1 概述145
3.3.3.2 光孔上螺桩的金相分析与强度145
3.3.3.3 光孔上螺桩的优越性146
3.3.3.4 铸造铝合金基体孔和螺桩结构146
3.3.3.5 光孔上螺桩加工技术149
3.3.3.6 螺桩装配151
3.3.4 壳体密封和强度试验152
3.3.4.1 壳体密封试验152
3.3.4.2 高压试验153
3.3.4.3 气密试验和高压试验的密封形式154
3.4 钢丝螺套工艺技术154
3.4.1 钢丝螺套简介154
3.4.2 钢丝螺套连接结构的设计156
3.4.2.1 钢丝螺套型面结构设计156
3.4.2.2 装钢丝螺套用内螺纹的设计157
3.4.3 钢丝螺套型面标准159
3.4.3.1 钢丝螺套型面结构及尺寸159
3.4.3.2 钢丝螺套型面主要技术要求159
3.4.3.3 钢丝螺套型面测量160
3.4.3.4 国外钢丝螺套型面标准介绍161
3.4.4 钢丝螺套163
3.4.4.1 普通型钢丝螺套163
3.4.4.2 锁紧型钢丝螺套165
3.4.4.3 普通型镀层钢丝螺套170
3.4.4.4 国外钢丝螺套标准介绍170
3.4.4.5 钢丝螺套绕制工艺177
3.4.4.6 钢丝螺套的检验177
3.4.5 装钢丝螺套用内螺纹178
3.4.5.1 装钢丝螺套用内螺纹结构及尺寸178
3.4.5.2 国外装钢丝螺套用内螺纹标准178
3.4.6 基体螺孔181
3.4.6.1 基体材料181
3.4.6.2 基体螺孔结构181
3.4.6.3 基体螺孔的加工182
3.4.6.4 基体螺孔的检验186
3.4.7 钢丝螺套的装配186
3.4.7.1 装配前的准备工作186
3.4.7.2 钢丝螺套的装配过程187
3.4.7.3 钢丝螺套的拆除190
3.4.7.4 基体螺孔的修复190
3.4.7.5 钢丝螺套装配后的检验190
3.4.8 螺栓(螺钉)装配要求191
3.5 壳体加工过程中产生的毛刺和杂质的清除191
3.5.1 清除毛刺和杂质的重要性191
3.5.2 壳体内不易清除毛刺及杂物的部位192
3.5.3 清除毛刺及杂物的综合工艺方法192
3.5.4 壳体冲洗和涮洗工艺技术193
3.5.4.1 大块切屑的冲洗193
3.5.4.2 油气交替冲洗和涮洗196
3.5.4.3 内孔腔清理后的质量检查197
3.6 镁合金加工技术197
3.6.1 防止切削热引起的切屑燃烧198
3.6.2 防止切削热引起的工件变形198
3.6.3 温差引起的尺寸精度变化199
3.6.4 工艺装备设计时材料线膨胀问题199
3.6.4.1 使用钢制定位元件时的最大容许尺寸[A]200
3.6.4.2 一种新型量具的设计原理201
3.6.5 镁合金氧化防锈问题203
3.6.5.1 镁合金加工过程中的防锈要求203
3.6.5.2 验收和存放的防锈要求203
3.6.5.3 镁合金锈蚀的排除方法203
第4章 典型框架壳体的加工工艺204
4.1 燃油调节器壳体加工工艺204
4.1.1 功用和特点204
4.1.2 主要技术要求及工艺方法209
4.1.3 壳体毛坯210
4.1.3.1 毛坯图说明210
4.1.3.2 铸件必检项目210
4.1.4 壳体定位基准210
4.1.5 定位基准的加工215
4.1.6 壳体工艺流程216
4.1.7 典型加工方法217
4.1.8 辅助工序的编制230
4.1.9 油路冲洗230
4.2 带齿轮泵的燃油调节器壳体加工工艺230
4.2.1 壳体结构特点230
4.2.2 壳体主要技术要求234
4.2.3 工艺分析234
4.2.3.1 毛坯的确定234
4.2.3.2 基准的确定和加工236
4.2.3.3 辅助工序的分析与安排241
4.2.4 调节器壳体加工工艺过程241
4.2.5 主要加工工艺242
4.2.5.1 用加工中心机床加工壳体242
4.2.5.2 活塞孔的加工251
4.2.5.3 密封孔的加工252
4.2.5.4 齿轮孔的加工253
4.2.6 主要加工部位的检测方法258
4.2.6.1 活塞孔的检测258
4.2.6.2 两齿轮孔底平面深度差的检测258
4.2.6.3 密封孔的检测258
4.2.7 加工易产生的问题及解决方法258
4.3 液压助力器壳体加工工艺259
4.3.1 壳体的功用和特点259
4.3.2 主要技术要求和工艺方法260
4.3.3 壳体毛坯特点和技术要求261
4.3.4 壳体主要加工工艺261
4.3.5 壳体加工的典型工艺装备264
4.3.5.1 环氧树脂浇注夹具的特点、制作和使用264
4.3.5.2 弯板式车床夹具和使用264
4.3.5.3 内直角孔钻具266
4.3.5.4 带导向的研磨具266
4.3.6 壳体数控加工的准备与工艺266
4.4 恒速装置壳体加工工艺270
4.4.1 壳体的作用270
4.4.2 壳体技术要求与工艺难点及采取的措施270
4.4.3 上壳体工艺流程及工序示例273
4.4.3.1 上壳体工艺流程273
4.4.3.2 上壳体工序示例274
4.4.4 下壳体工艺流程及工序示例277
4.4.4.1 下壳体工艺流程277
4.4.4.2 下壳体工序示例278
4.4.5 粗基准的选择280
4.4.6 精基准的选择281
4.4.6.1 定位面积与孔间距要求281
4.4.6.2 统一基准的应用281
4.4.7 相交孔钻削及引偏标准281
4.4.7.1 相交孔加工防引偏的导向方法281
4.4.7.2 钻头钻相交孔防偏斜方法281
4.4.7.3 深孔位置度引偏标准282
4.4.8 提高孔加工位置精度的措施282
4.4.8.1 用较大的定心孔直径282
4.4.8.2 纠正铸造油路孔偏斜的方法282
4.4.8.3 合理选择孔加工余量282
4.4.9 卧式镗床加工空间相交孔示例283
4.4.9.1 上壳体相交孔在镗床上的定位关系283
4.4.9.2 零件位置调整至加工状态的空间点坐标旋转及计算284
4.4.10 液压试验287
4.4.10.1 液压试验的作用287
4.4.10.2 试验工序安排287
4.4.10.3 工序安排实例288
4.4.10.4 液压试验操作要求289
4.4.11 计量基准的过渡应用289
4.4.11.1 坐标尺寸转轴换算289
4.4.11.2 计量基准的过渡290
4.4.11.3 位置度相位图291
4.4.12 配套表的应用292
4.4.12.1 配套表的作用292
4.4.12.2 上壳体配套表应用实例292
4.5 陀螺框架加工工艺293
4.5.1 概述293
4.5.1.1 功用和特点293
4.5.1.2 陀螺框架类型293
4.5.1.3 陀螺框架的主要精度297
4.5.1.4 陀螺框架材料、热处理和表面处理298
4.5.2 陀螺框架工艺分析299
4.5.2.1 陀螺内框架工艺分析299
4.5.2.2 陀螺外框架工艺分析301
4.5.3 陀螺框架主要表面的加工309
4.5.3.1 陀螺框架主要表面在组合镗床上的加工309
4.5.3.2 陀螺框架主要表面在坐标镗床上的加工324
4.5.3.3 陀螺框架主要表面在车床上的加工326
4.5.3.4 陀螺框架在加工中心机床上的加工328
4.5.4 陀螺框架精度检测328
4.5.4.1 陀螺框架径向尺寸检测328
4.5.4.2 陀螺框架同轴度检测328
4.5.4.3 陀螺框架位置度检测330
4.5.4.4 陀螺框架垂直度检测332
4.6 机载雷达框架加工工艺332
4.6.1 机载雷达框架功用及特点332
4.6.2 主要技术要求336
4.6.3 毛坯的确定337
4.6.4 工艺基准选择337
4.6.4.1 设计基准分析337
4.6.4.2 定位基准选择337
4.6.5 定位基准面加工338
4.6.5.1 底座定位基准面加工338
4.6.5.2 方位框架定位基准面加工339
4.6.5.3 俯仰框架定位基准面加工339
4.6.6 工艺路线安排340
4.6.7 主要表面加工340
4.6.7.1 底座主要表面加工340
4.6.7.2 方位框架主要表面加工341
4.6.7.3 俯仰框架主要表面加工342
4.6.8 零件工艺凸台的设置343
4.6.9 热处理工序的安排344
4.6.10 铸镁合金零件的防锈344
4.6.10.1 一般规定344
4.6.10.2 工序间防锈345
4.6.10.3 成品件防锈345
4.7 齿轮减速器壳体加工工艺345
4.7.1 齿轮减速器壳体功用及特点345
4.7.2 壳体组件零件图分析与技术要求346
4.7.3 减速器壳体材料与毛坯346
4.7.4 减速器壳体组件加工工艺过程350
4.7.4.1 壳体加工工艺流程及工序示例350
4.7.4.2 壳体组件加工工艺流程及工序示例352
4.7.5 减速器壳体组件加工工艺特点355
4.7.5.1 加工阶段的划分355
4.7.5.2 壳体热处理与氧化355
4.7.6 工艺基准的确定356
4.7.7 定位销孔加工356
4.7.8 壳体组件轴承孔加工357
4.7.8.1 壳体轴承孔加工357
4.7.8.2 上盖轴承孔加工360
4.7.8.3 壳体盖轴承孔加工360
4.8 弹射止动器加工工艺362
4.8.1 概述362
4.8.2 结构特点及技术要求362
4.8.2.1 结构特点362
4.8.2.2 技术要求362
4.8.3 工艺分析363
4.8.3.1 毛坯的确定363
4.8.3.2 基准的确定364
4.8.4 弹射止动器加工工艺过程368
4.8.5 主要表面加工工艺368
4.8.5.1 安装弹射杆孔的加工工艺368
4.8.5.2 铣圆台面369
4.8.5.3 钻孔、扩孔和攻螺纹370
4.8.5.4 内孔镀铬372
4.9 挂梁骨架加工工艺373
4.9.1 概述373
4.9.2 结构特点及技术要求375
4.9.2.1 结构特点375
4.9.2.2 技术要求375
4.9.3 工艺分析375
4.9.3.1 毛坯的确定375
4.9.3.2 基准的确定377
4.9.4 挂梁骨架加工工艺过程381
4.9.4.1 制定工艺路线需考虑的问题381
4.9.4.2 加工工艺过程381
4.9.5 主要表面加工工艺382
4.9.5.1 孔加工工艺382
4.9.5.2 翼形面加工工艺384
4.9.5.3 翼形槽加工工艺386
4.9.5.4 前接头安装孔加工工艺388
4.9.5.5 前、后接头安装部位长孔加工工艺389
参考文献391
1997《航空制造工程手册 框架壳体工艺》由于是年代较久的资料都绝版了,几乎不可能购买到实物。如果大家为了学习确实需要,可向博主求助其电子版PDF文件(由《航空制造工程手册》总编委会主编 1997 北京:航空工业出版社 出版的版本) 。对合法合规的求助,我会当即受理并将下载地址发送给你。
高度相关资料
-
- 航空制造工程手册 飞机钣金工艺
- 1992 北京:航空工业出版社
-
- 航空蜂窝结构制造工艺
- 1980
-
- 航空航天机械制造工艺学
- 1990 北京:北京航空航天大学出版社
-
- 航空制造工程手册 非金属结构件工艺
- 1996 北京:航空工业出版社
-
- 航空制造工程手册 通用基础
- 1993 北京:航空工业出版社
-
- 航空制造工程手册 电连接器工艺
- 1996 北京:航空工业出版社
-
- 航空制造工程手册 发动机叶片工艺
- 1998 北京:航空工业出版社
-
- 航空制造工程手册 飞机结构工艺性指南
- 1998 北京:航空工业出版社
-
- 航空制造工程手册:特种加工
- 1993 北京:航空工业出版社
-
- 航空制造工程手册:飞机机械加工
- 1995 北京:航空工业出版社
-
- 航空制造工程手册:电子设备装配
- 1995 北京:航空工业出版社
-
- 航空制造工程手册 救生装备工艺
- 1995 北京:航空工业出版社
-
- 航空制造工程手册 飞机模线样板
- 1993 北京:航空工业出版社
-
- 航空制造工程手册 飞机装配
- 1993 北京:航空工业出版社
-
- 航空制造工程手册 飞机工艺装备
- 1994 北京:航空工业出版社
提示:百度云已更名为百度网盘(百度盘),天翼云盘、微盘下载地址……暂未提供。➥ PDF文字可复制化或转WORD